How Today’s Manufacturers Benefit from Scientific Injection Molding
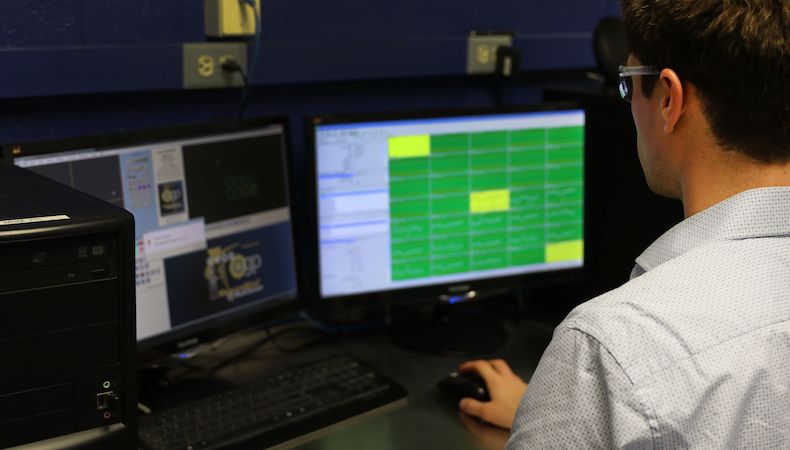
As technologies and demand rapidly increase the competition in many industries, there’s little room for traditional injection molding methods.
The long-established “trial and error” approach to tweaking processes and products into specification through engineering guesswork is time-consuming, outmoded, and inefficient. It can also be costly as there are no reliable ways to successfully capture molding repeatability — meaning subsequent production runs could necessitate their own rounds of rework to meet specs.
Inconsistency spells trouble for complex parts and applications, especially those with tight tolerances and exacting dimensions. Repeatability is the key to precision performance, and scientific injection molding is the systematic approach that delivers it.
What is scientific injection molding?
Defined and methodical, scientific molding uses empirical data gathered by advanced sensors and software to optimize and control the injection molding process. Material-specific information such as pack and hold pressure limits, melt and cooling temperatures, and fill rates give engineers insight into how the process steps need to work together to achieve top quality, defect-free parts.
Ensuring the process is developed with precision and accuracy is vital. Design of Experiments (DOE) is used to continuously test and verify — or strategically change — anticipated process steps to meet specs, maximize the process window, and manage quality. DOE is the rigorous, controlled problem-solving framework that underpins comprehensive scientific molding process development, documentation, maintenance, and troubleshooting.
Ken Glassen, Kaysun VP of Engineering, gives an overview of scientific injection molding:
Additional scientific molding benefits
Scientific molding is a valuable tool for improving injection molding process efficiency and repeatable, high-quality part production. Along with this focus comes ancillary benefits that help OEMs better anticipate and manage costs:
Optimized tooling
Tooling is typically the most expensive part of an injection molding program. Completing a complex part design only to have it not align with the tooling delays production and often means a rework of the tooling — a time-consuming and costly process. Applying scientific molding principles to tooling development concurrent with part design ensures accurate, sophisticated tooling is optimized to consistently produce high-quality parts.
Fewer part variations
Scientific molding gives engineering teams the ability to accurately document the specifications, settings, and steps required for production repeatability over time and across equipment. Identical parts can be reliably produced with tolerances as tight as +/- .001 inches, making scientific molding particularly valuable for complex applications within the automotive, medical, industrial, and consumer markets.
Faster, higher volume production
Since a production process developed using scientific molding is precise and data-driven, engineers are able to better understand materials behavior within the mold. As a result, they can adjust production parameters to these characteristics for improved production efficiencies including faster cycle times, higher production volume, and consistent part quality.
The role of specialized scientific injection molding engineers
In order for scientific molding to be effective, it needs to be performed by molding professionals who have undergone thorough training and hold the proper scientific molding certification.
But it’s more than just using specialized injection molding sensors and software; it’s about knowing exactly what to do to optimize the production process.
Specialized scientific injection molding engineers are adept at problem solving. Addressing issues quickly and accurately provides solutions that will return the process to specification — minimizing production time and costs.
Taking a scientific molding approach to developing an injection molding process is systematic, repeatable, and beneficial to OEMs. When working with an experienced injection molder such as Kaysun, the efficiencies gained translate to precision-molded, top-quality parts along with time and cost savings.
Learn more about the design, engineering, and process steps in our white paper, An OEM’s Guide to Scientific Molding.
Subscribe
TO OUR BLOG
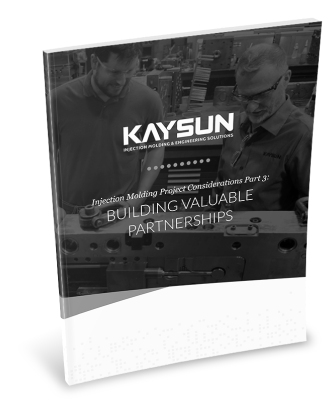
How Do Injection Molder Partnerships Influence Project Costs?
You Might Also Like...
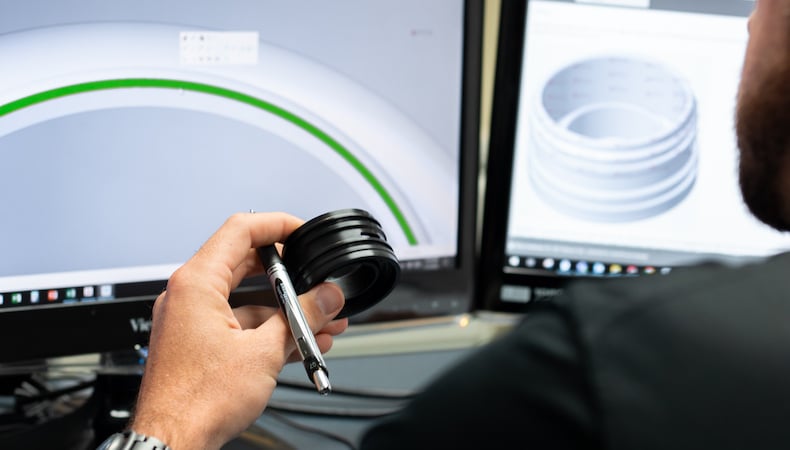
How RJG Master Molder I/II Defines Injection Molding Excellence
In custom injection molding, quality and precision are both an expectation and a g…
READ MORE
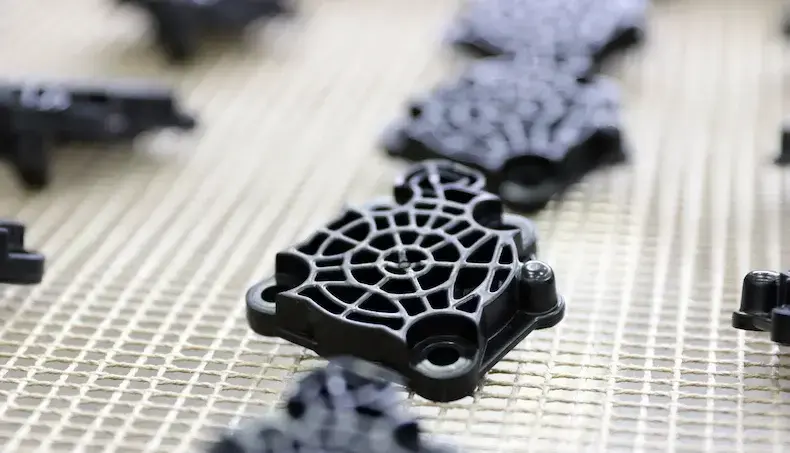
3 Engineering Support Services Your Injection Molder Must Offer
There’s no denying that pandemic-related, weather-influenced, and manmade disrupti…
READ MORE
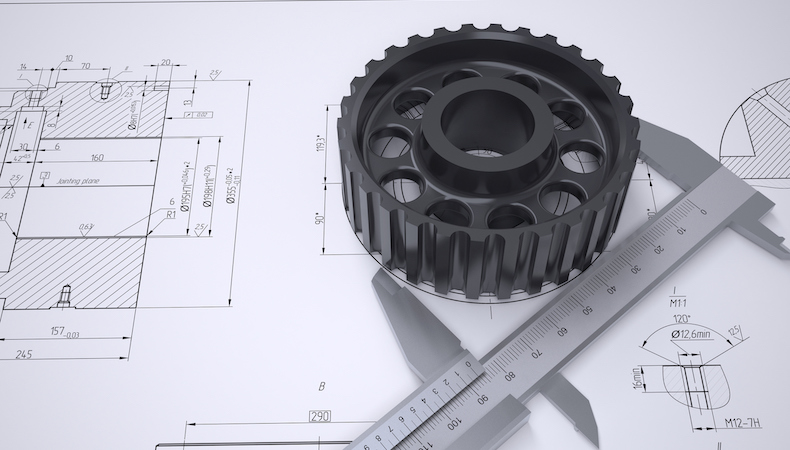
3 Essential Focus Areas for No-Fail Injection Molding Quality Control
Manufacturers across industries continue to rely heavily upon custom injection mol…
READ MORE