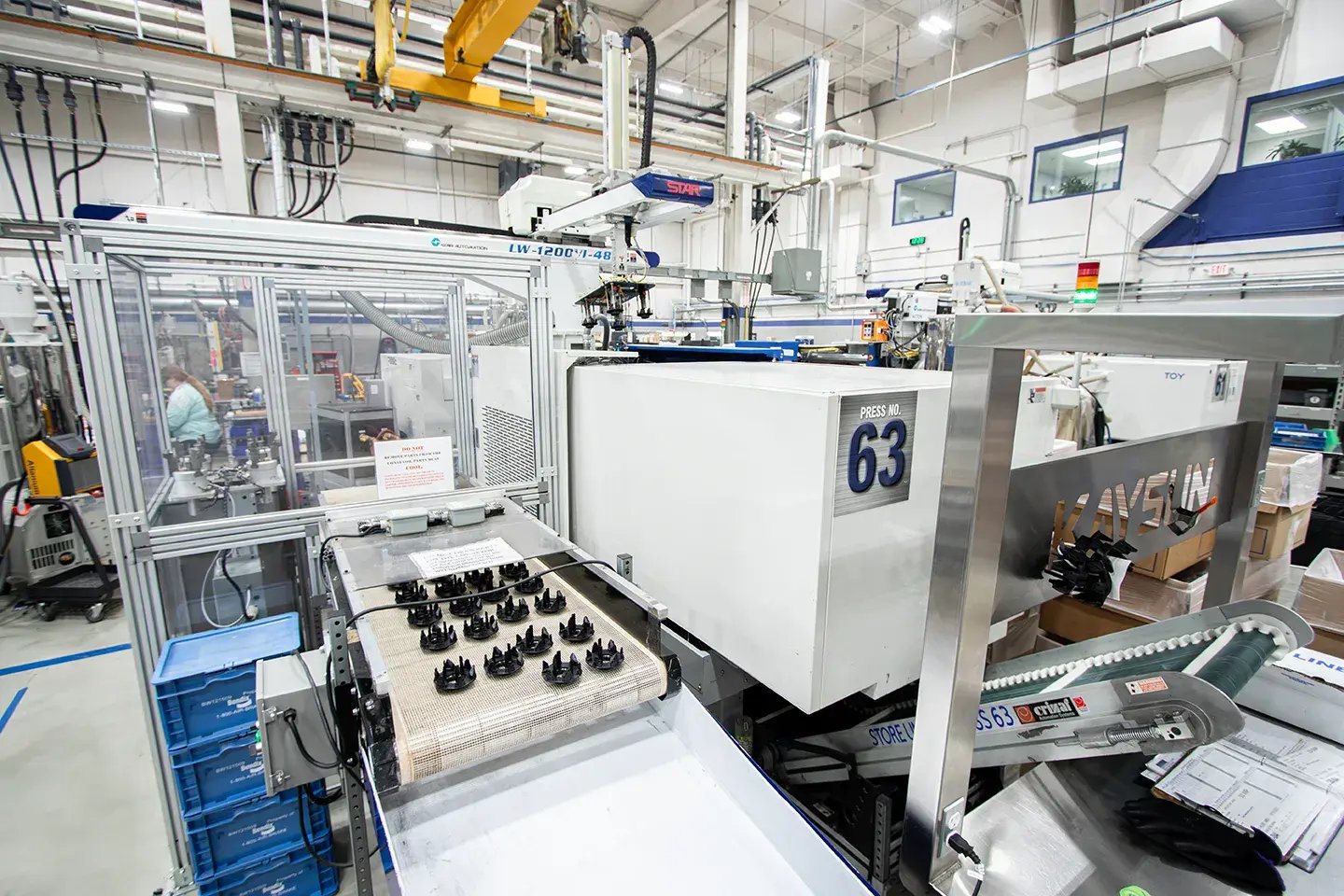
Reshoring
Reshoring — bringing production back to North America from overseas operations —continues to gain momentum as OEMs confront the realities of what lies ahead for manufacturing.
Once seen as the key to cost savings, offshoring has been upended by growing concerns over geopolitical instability, economic volatility, supply chain vulnerabilities, and quality control issues. As these risks intensify, reshoring is emerging as both a more resilient alternative and a strategic imperative for long-term competitiveness.
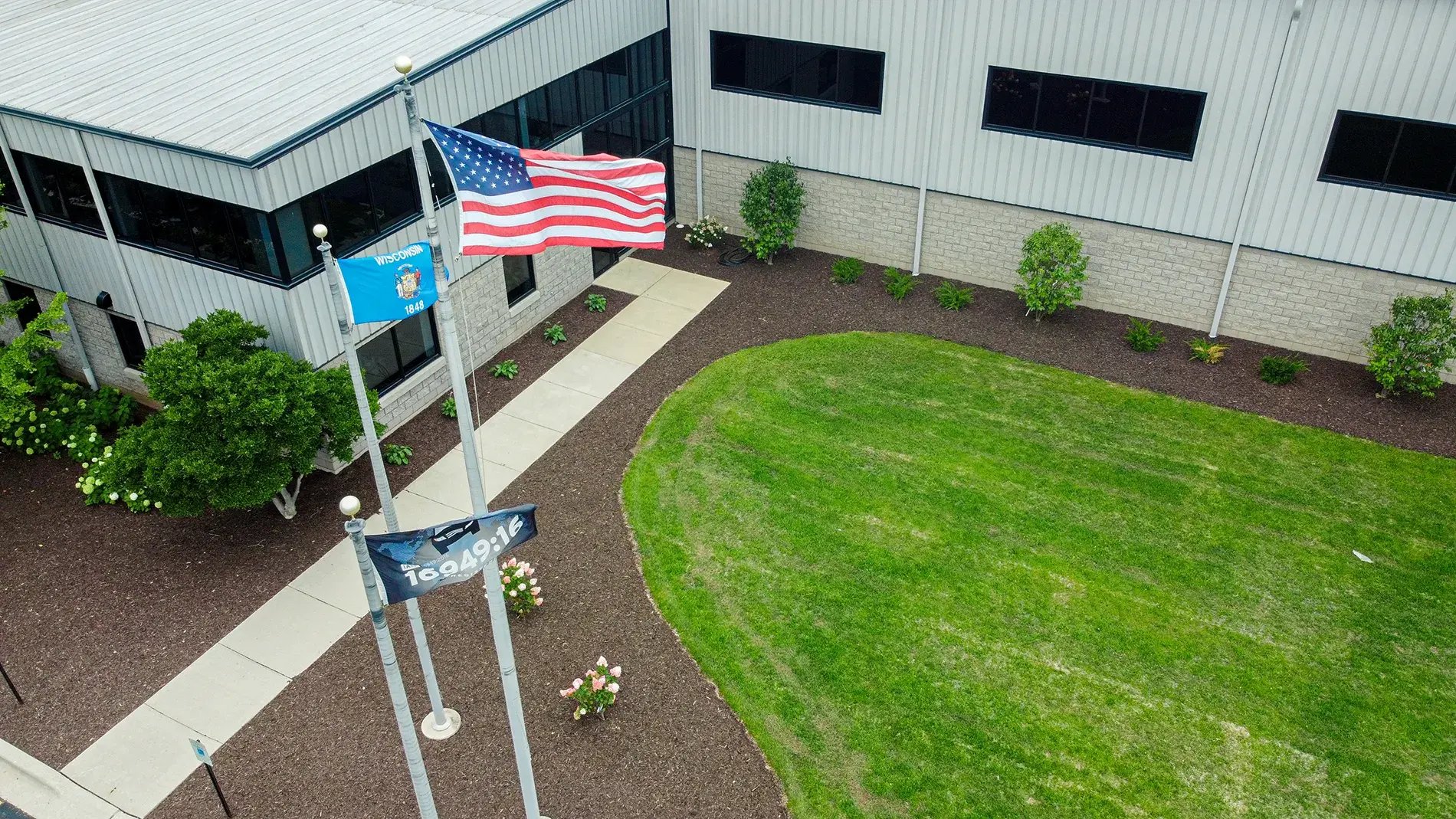
The Strategy
Behind Reshoring
Economics, material availability, and reliability are key drivers behind reshoring, but the decisions aren’t purely reactionary.
Many U.S. companies are taking the opportunity to recalibrate and regain more control of:
- Product quality and innovation
- Supply chain resilience and lead times
- Labor stability and automation (largely using AI-enabled technologies )
- Compliance, ESG goals, and customer expectations
- Intellectual property protection and brand reputation
The “Made in America” Influence
In addition, there’s power in leveraging “Made in America” products. U.S. manufacturers currently make only about 11% of products bought by Americans — a sharp drop from the 80% seen four decades ago. However, trends support a resurgence in preference for domestically sourced items.
65% of Americans routinely look for products Made in the USA
There is a caveat. “Made in America” can’t simply be claimed. The Federal Trade Commission (FTC) has strict compliance standards that need to be met before the label is put on products.
Hidden Costs Of Offshoring
Historically, the correlation between lower labor costs and higher bottom lines was usually enough to convince decision makers to sign off on offshoring as a cost-cutting strategy.
up to 30%
It’s a compelling argument, but somewhat of a false positive. The often overlooked “hidden” operational, financial, and strategic challenges that come with offshoring typically erode the labor savings over time:
- Increased safety stock, warehousing, and expedited shipping inflate carrying and logistics costs tied to long lead times, port and customs delays, and shipping disruptions
- More quality inspections, rework, and scrap material significantly increase cost per unit as standards, expectations, and miscommunication may vary between countries
- Lack of urgency, agility, and responsiveness results in missed opportunities, delayed time-to-market, and poor customer service
- Timezone misalignment translates to higher coordination costs, increased international travel for project management, and geographic project delays
- Limited proprietary control could put product designs and trade secrets at risk of theft, imitation, or counterfeiting
- Reduced liquidity due to more cash allocated to buffer inventory and warehousing
- Sustainability risk as higher global shipping-related emissions and inconsistent environmental standards between countries could trigger regulatory penalties or carbon taxes
- Lack of R&D and production synergies slow innovation feedback and narrow opportunities for cost savings and performance improvements
Why TCO Supports Reshoring
Total Cost of Ownership (TCO) models factor in all indirect, long-term, and ancillary costs to arrive at real numbers and better-informed decisions versus Ex Works (EXW) or Free On Board (FOB) pricing.
- Inventory carrying costs and safety stock
- Expedited shipping and delay penalties
- Travel expenses for supplier oversight
- Currency exchange fluctuation
- Lost revenue from delayed product availability
- Production downtime waiting on components
- Cost of switching or requalifying suppliers
- Warranty claims and field failures
- Additional inspection/testing costs
- Customer dissatisfaction or brand damage
- Higher risk of counterfeiting or IP theft
- Compliance complexity in regulated industries
- Reputational risk due to labor/environmental standards
- Missed sales or innovation windows
- Inflexibility to respond to changing demand
- Slower product development cycles
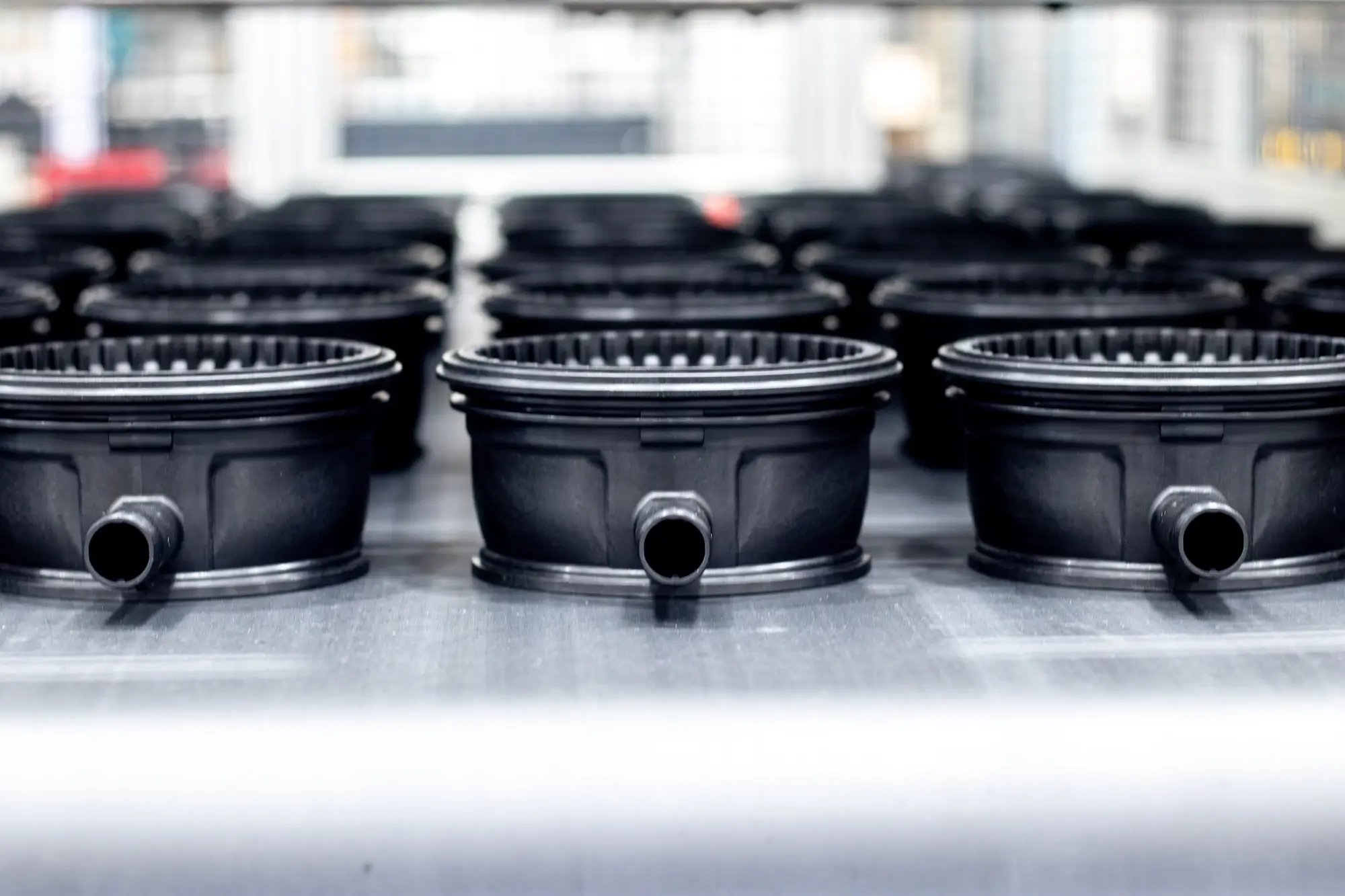
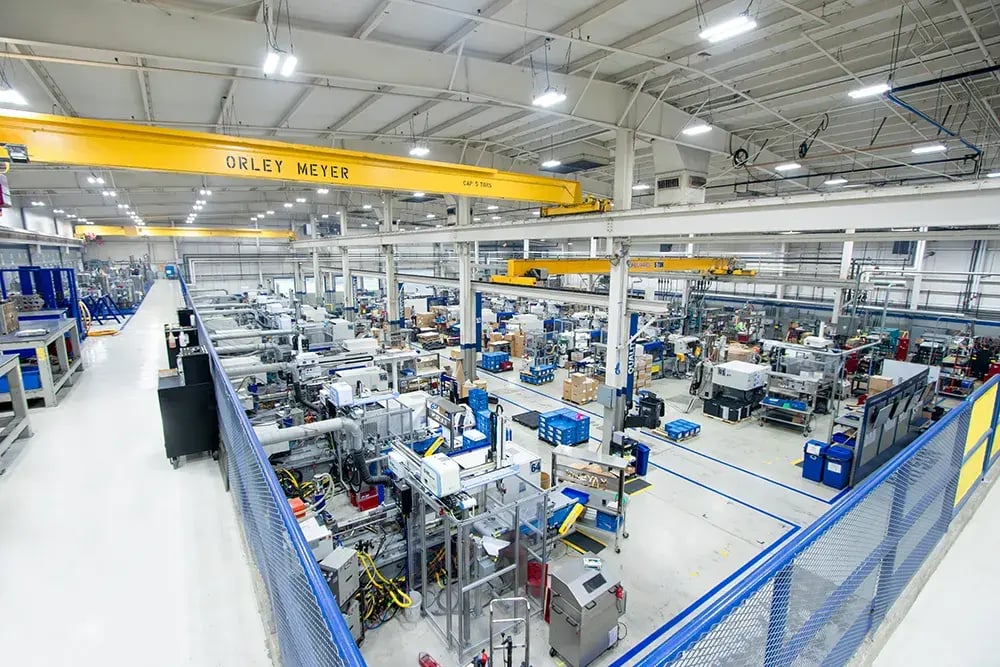
6 Benefits of Reshoring
Reshoring is more than an increasingly global imperative. Strategically, domestic suppliers provide several key operational advantages for OEMs looking to reshore, including:
1. SUPPLY CHAIN STABILITY
Reduced exposure risk and agility in response to disruptions or market changes.
2. FASTER TURNAROUND AND TIME TO MARKET
International shipping delays and/or customs complications are eliminated, shortening development cycles.
3. HIGHER QUALITY, LESS WASTE
Closer collaboration between OEM and supplier teams improves product quality and consistency without iterations of costly rework.
4. STRONGER INTELLECTUAL PROPERTY (IP) PROTECTION
U.S. laws enforcing patents and trademarks reduce counterfeiting and lost market share.
5. MORE SUSTAINABLE MANUFACTURING
Less materials waste, fewer freight emissions, and smaller carbon footprint all support sustainability initiatives.
6. ADVANCED, AI-ENABLED AUTOMATION
Maximizes workforce capabilities and time to support more productive operations overall.
Why Choose Kaysun?
Kaysun is a U.S.-based, engineering-driven injection molding partner with extensive experience in helping OEMs with often complicated reshoring initiatives.
Our dynamic in-house capabilities in engineering, tooling, automation, and quality control give us the flexibility to:
- Seamlessly integrate into your reshored supply chain — eliminating a lot of frustration
- Collaborate closely with your team through every stage of the process, from initial design analysis through production
- Ensure consistent, defect-free quality assurance through rigorous testing using the state-of-the-art equipment in our Quality Lab
- Support your goals with injection molding operations and lean manufacturing practices that are certified and accredited by ISO, IATF, and MedAccred
Sources
SupplyChain Digital, US reshoring is supply chain success - Kearney Report
NetChoice, The Value of “Made in the USA”: What Retailers Need to Know
Reshoring Initiative, Total Cost of Ownership Estimator®
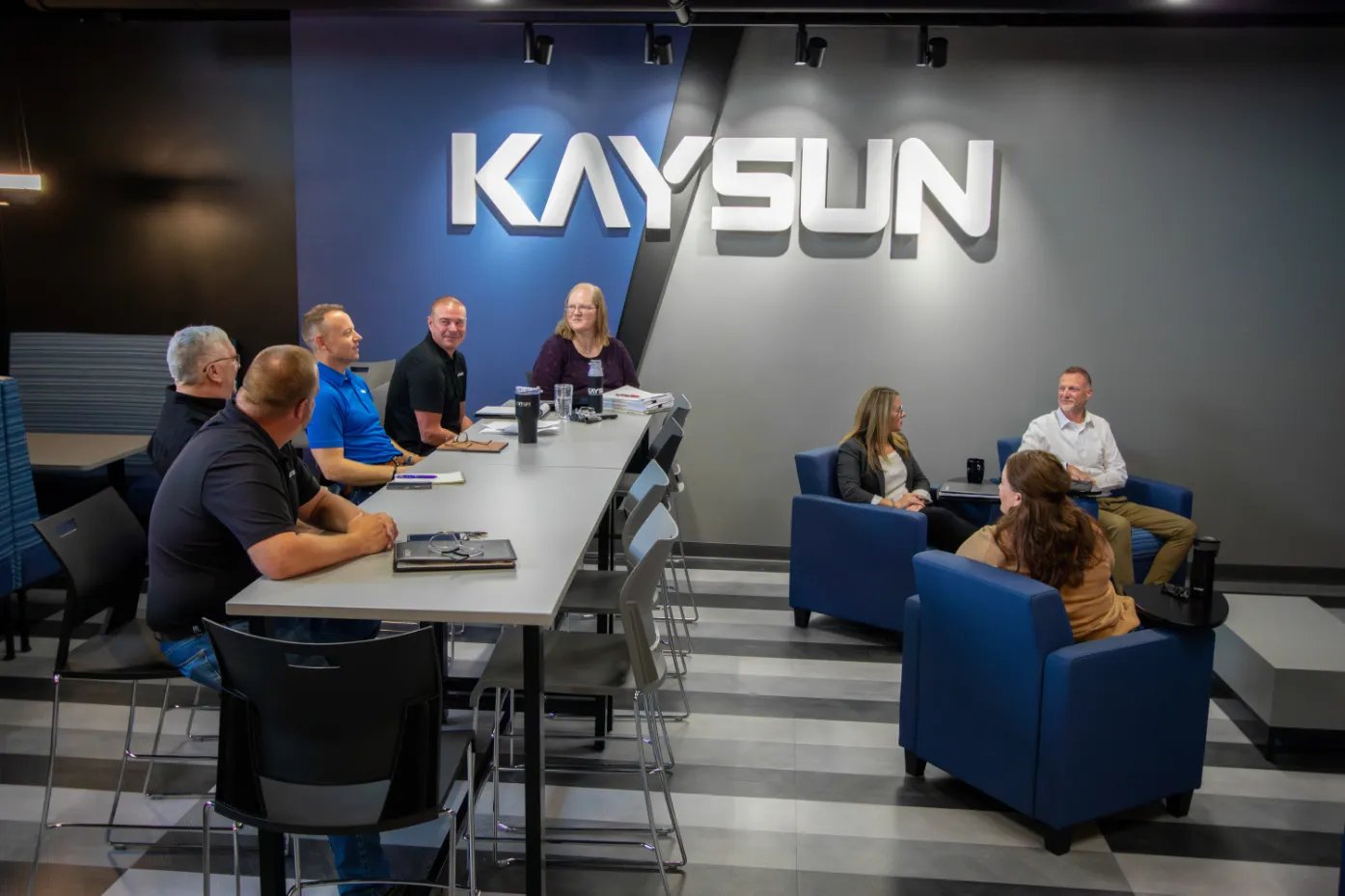
Does your company fit our ideal customer profile?
Complete the form to request a free consultation with our plastic engineering experts.