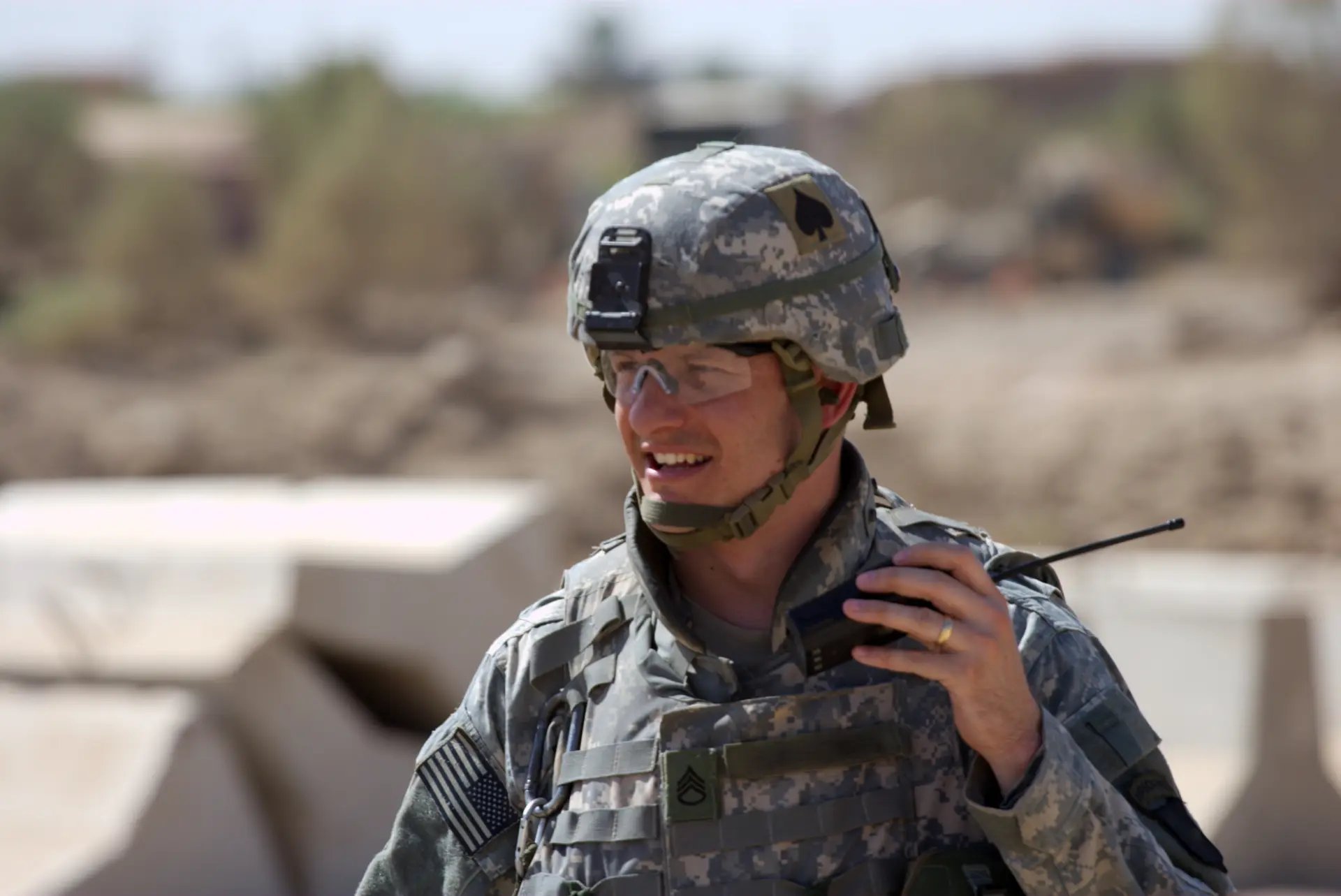
Additional Markets
Kaysun is the trusted custom injection molding partner for OEMs in a range of industries. We are committed to applying our depth of knowledge, engineering expertise, and highly specialized plastics selection insights to help our customers find innovative solutions to their most complex applications, regardless of market.
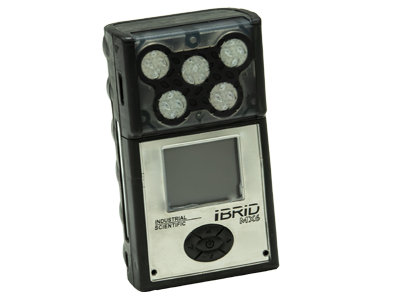
Defense
Police, firefighters, first responders, and the military depend on protective equipment and technologies manufactured using the most advanced materials and processes. Plastics must be lightweight, strong, impact-resistant, and able to withstand chemical exposure and temperature extremes.
It’s a tall order, but one that experienced injection molders can confidently undertake. As an International Traffic in Arms Regulations (ITAR) compliant custom injection molder, Kaysun understands the nuances of defense contracts, protocols, and protective equipment and technologies requirements. Our expertise in metal-to-plastic conversion, comprehensive plastics modeling, and material selection support ensure injection-molded components provide reliable performance, protection, and longevity.

To better understand how a collaborative partnership with an injection molder helps keep defense workers safe in the field, read how we helped solve a portability dilemma:
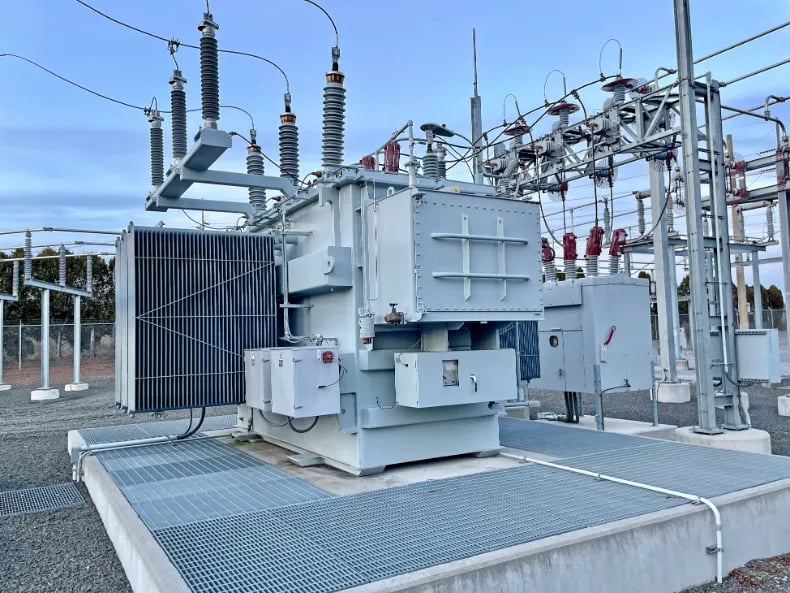
Energy
The United States uses a number of primary and secondary energy sources, making the energy market both dynamic and demanding.
The complex system of substations, transformers, and powerlines — commonly referred to as “the grid” — connects producers and consumers. Kaysun expertise in sophisticated processes such as insert molding allows for strategic integration of multiple materials into contacts, fuses, and other components for reliable power distribution.
Read more about how custom injection molding aligns with energy market needs:
Oil & Natural Gas
Representing roughly 8% of the U.S. GDP (Gross Domestic Product), the oil & natural gas industry is one of the country’s largest employers.1 Keeping more than 10 million workers safe in sometimes dangerous conditions is a top priority — an effort Kaysun has been called upon to support.
Our collaboration with industry partners resulted in finding ways to leverage Design for Manufacturability (DfM), moldfill analysis, material selection, thermoplastic elastomer (TPE) overmolding, and advanced tooling to re-engineer housings for wearable hazardous gas detector units.
The robust processes an injection molder provides speaks to their depth of knowledge and experience.
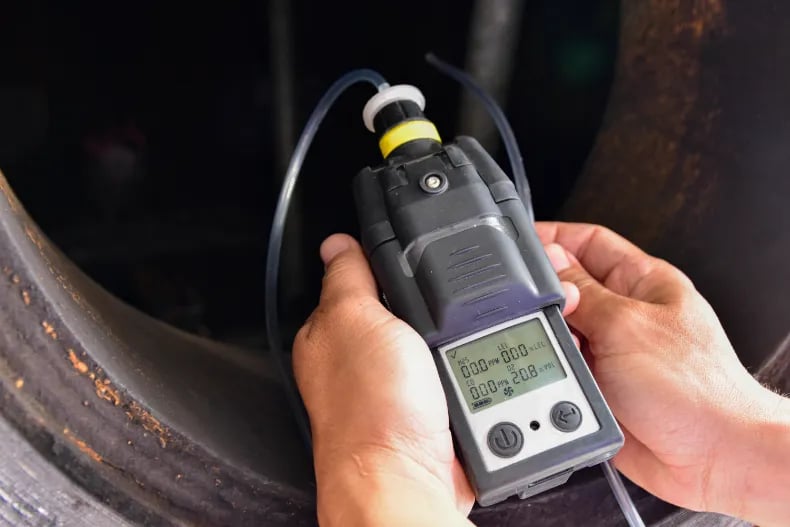
Learn more about how Kaysun arrives at high-performance solutions by leveraging DfM and overmolding:
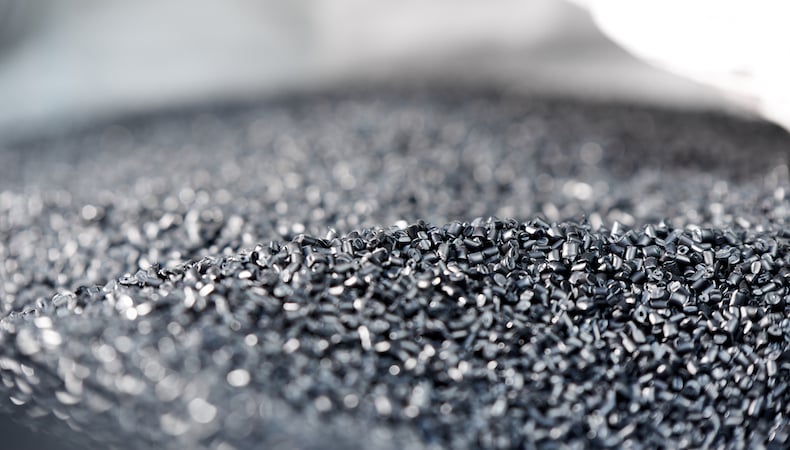
PEEK & PEKEKK
Molding Capabilities
As technologies, components, and applications advance, so does the complexity of injection-molded parts and the plastics used to make them. There are more than 25,000 standard engineered materials available, and high-performance blends and hybrids can be formulated to meet unique project requirements.
Kaysun engineers have highly specialized training in plastics behavior, and access to decades of in-house materials data. As a result, OEMs across industries seek out Kaysun for plastic part design and production requiring high-end materials. We are technically sound molders of polyether ether ketone (PEEK), and our experience extends to polyetherketone ether ketone ketone (PEKEKK) glass-filled resins and other difficult to mold plastics.
Read more about our PEEK & PEKEKK Molding Capabilities
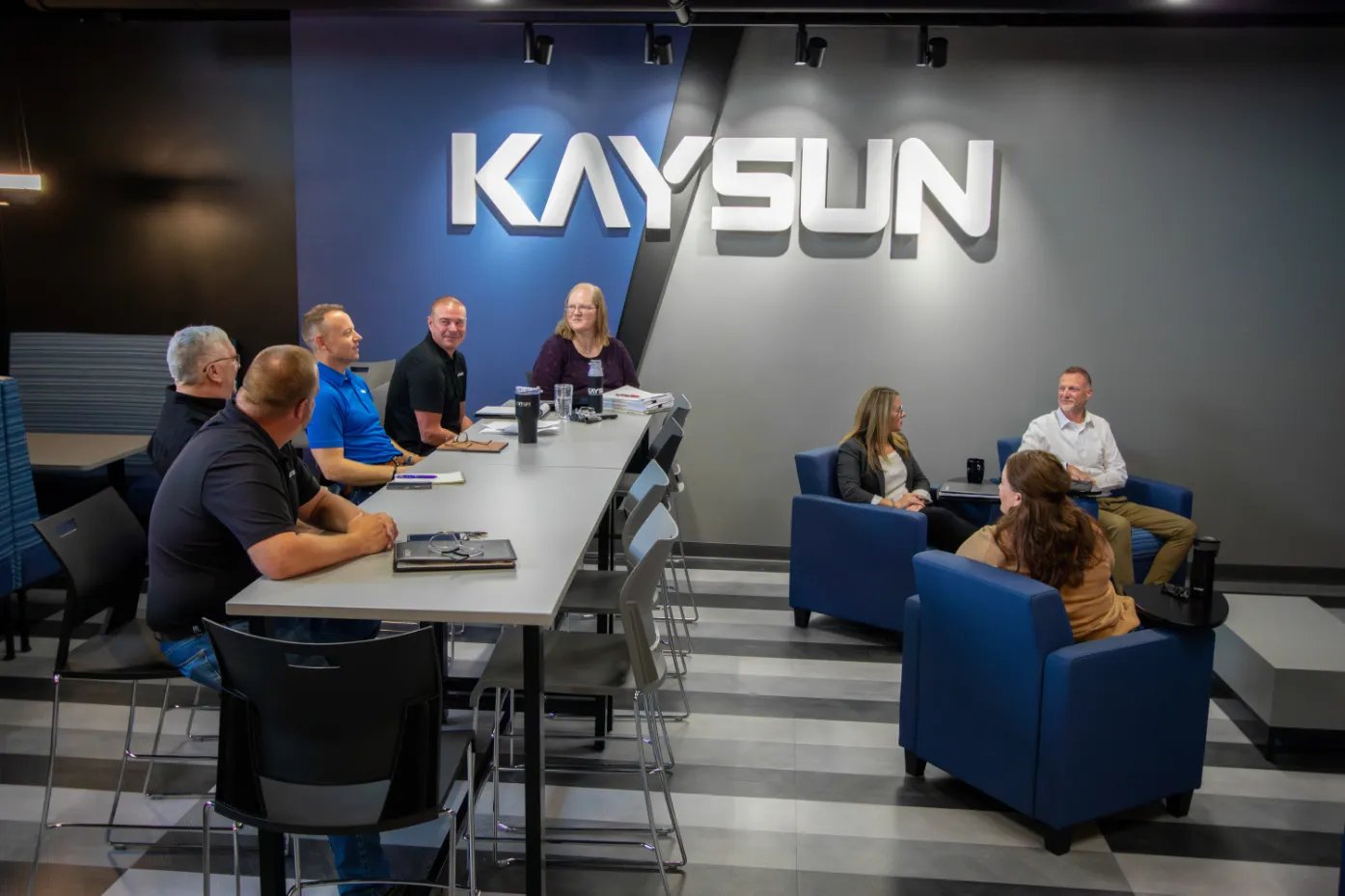
Does your company fit our ideal customer profile?
Complete the form to request a free consultation with our plastic engineering experts.