7 Ways to Join Plastic: How Does Plastic Overmolding Compare?
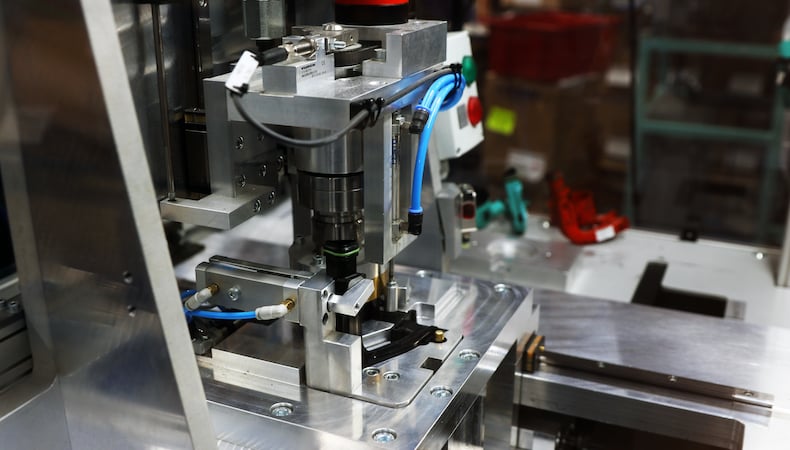
Plastics are extremely versatile, making them sought-after materials across a range of industries. For instance, in the United States the transportation/automotive and construction industries are two of the three major markets that account for the more than $31 billion spent annually on plastic components and products.1
With popularity and common use comes some challenges. For plastics, it’s reliably joining semi-finished plastic products to one another or to other materials. Several proven plastic joining solutions exist — including plastic overmolding — but the process best-suited for a specific project and budget isn’t always readily apparent.
This brief overview of the main plastic joining methods provides fundamentals that will help guide your choices.
4 Plastic Joining Welding Methods
Mechanical fastening with screws, bolts, or rivets and solvent or adhesive bonding were once the only choices in plastic joining. These simple methods are still available and generally effective. However, as secondary processes, they can also be time-consuming and expensive.
The evolution of materials, plastics knowledge, and technologies has expanded plastic joining to include several welding options:
Ultrasonic welding combines vibrational pulses and pressure to join fairly rigid plastics. As the materials vibrate and rub against each other, they heat and ultimately fuse together. Assembly with ultrasonic welding is fast and versatile. Ultrasonics can be used for inserting metal components into plastic, staking metal and plastic parts together, and spot welding plastic.
Spin welding joins plastics using surface friction to create a circular weld joint. One of the two parts to be joined is spun at high speed while force is applied to hold the two parts together. The resulting friction heats and melts the plastics, and more pressure is applied post-spinning to bond the materials together. Spin welds are high strength, hermetically sealed, and the most cost-effective way to achieve round weld joints.
Vibration welding is suited for forming pressure-tight joints in irregularly shaped, typically larger plastic parts or those composed of dissimilar materials with disparate melting points. Vibrational heating causes friction that, when paired with pressure, melt and bond plastics. The strength of the resulting joint weld is comparable to that of the materials used, and cycle times average 5 to 8 seconds for manual or automated operations.
Hot plate welding joins two plastic parts by melting them against a precisely heated platen for a prescribed period of time. The platen is removed and the two parts are forced together. The resulting joint bond is strong, permanent, and often hermetic.
OVERMOLDING FUNDAMENTALS FOR OEMS
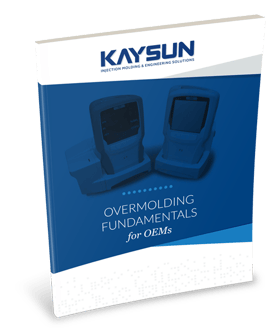
Have you considered how overmolding can further improve product design, performance, and aesthetics?
Advanced Plastic Joining: Infrared, Thermal, and Overmolding
Some advanced plastic joining methods use heat to manipulate melt temperatures, adhesion, and other characteristics of plastics:
Infrared welding is a fast, non-contact method that introduces infrared radiation into the plastic parts, which is transformed into heat and melts the surfaces. The parts are joined by using pressure to hold them together until bonded.
Laser welding leverages the concentrated heat and directionality of a laser beam to join plastics. Laser welding can be used on applications designed with plastics of varying thicknesses, and is ideal for high-volume production of parts requiring narrow, deep welds.
Overmolding is the preferred method for plastics joining as it does more than combine multiple materials. Plastic overmolding improves component or device design and performance because it can be used to dampen sound and vibration impact, insulate delicate electronics, and improve chemical/moisture resistance — all without “value-added” assembly. Plus, an array of colors can be molded into the plastic for easier use (e.g., keyboards, functionality buttons, etc.), durable brand differentiation, and custom aesthetics. Overmolding provides these benefits and more in an all-in-one process that reduces waste, increases efficiencies, and drives down production costs.
The complexities of plastics joining vary from project to project and process to process. Tapping into the expertise of a custom injection molder is beneficial — and essential — to achieve successful outcomes, and to leverage the advantages of advanced methods like plastic overmolding for your application. Learn more in our white paper, Overmolding Fundamentals for OEMs. Click the button below to download your copy now.
1Encyclopedia.com, Industry Profiles: Plastics Products, Undated
Subscribe
TO OUR BLOG
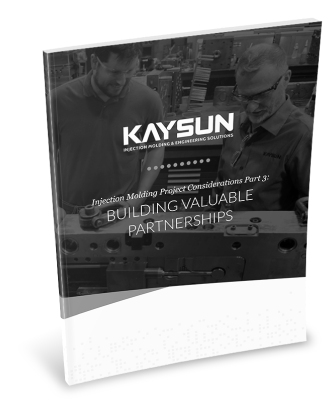
How Do Injection Molder Partnerships Influence Project Costs?
You Might Also Like...
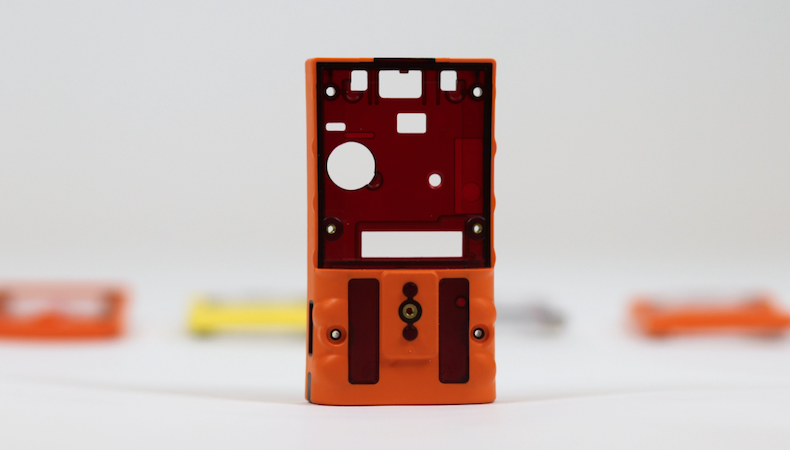
Two-Shot Injection Molding v. Overmolding: 14 Pros & Cons You Need To Know
Injection-molded parts are integral to the performance and aesthetics of a wide ra…
READ MORE
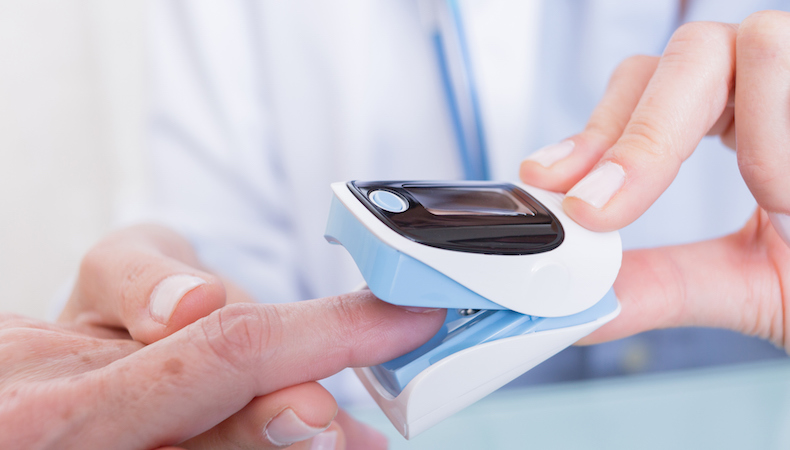
How Overmolding Enhances Handheld Medical Devices
Popular across many industries, overmolding may initially appear to simply enhance…
READ MORE
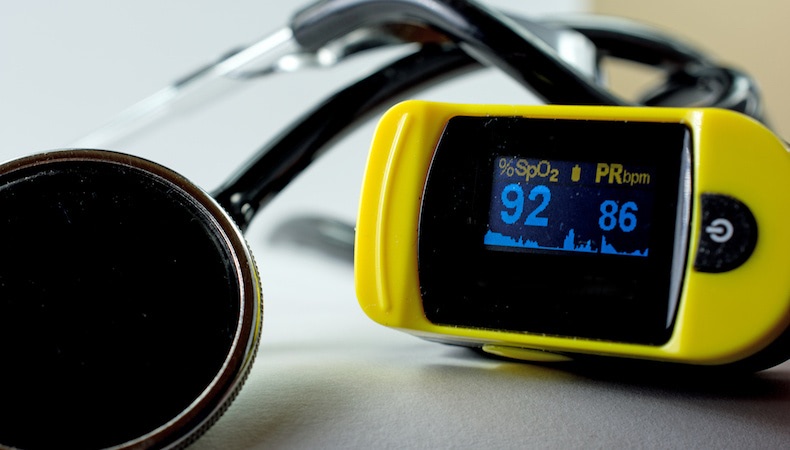
Overmolding: What it is and What it Means for Products and Profits
Increasingly popular with manufacturers of consumer products, medical devices, and…
READ MORE