How to Speed Up Injection Molding Cycle Time
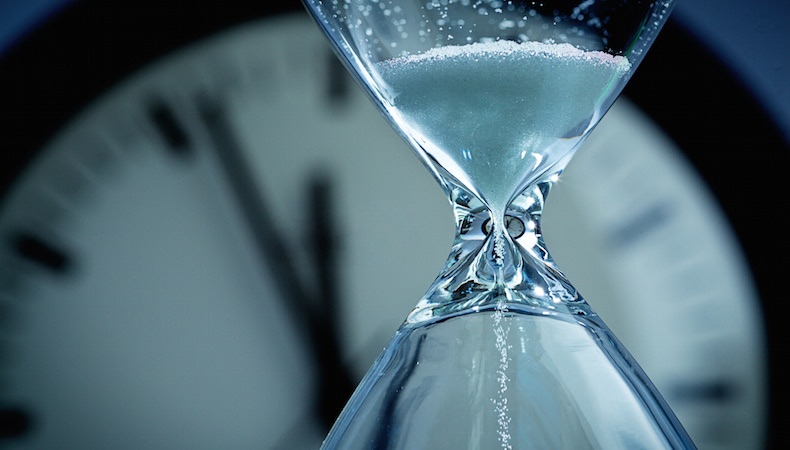
Injection molding cycle time directly influences plastic part cost and capacities, so keeping it as low as possible is the overarching goal of engineers and project managers. When getting quotes from various injection molders for plastic parts, they may be confronted with divergent cycle time estimates, calling accuracy and the molder’s capabilities into question.
The truth is, there is no “magic formula” that an injection molder can simply plug numbers into and pinpoint injection molding cycle time. However, an injection molding partner with wide-ranging expertise and depth of knowledge in scientific molding and moldfill analysis can more realistically quote projects. They have practical experience with a variety of parts and, therefore, can more precisely weigh in on designs and recommend possible cost-cutting measures.
Moreover, an experienced injection molder can anticipate factors that potentially increase cycle time — like thin steel and hot spots — and proactively prevent them by offering design change options. Calculating injection molding cycle time takes many factors into consideration:
Wall thickness
The thickest point of the plastic part requires more filling time and takes the longest to go from a molten state to being rigid enough to eject. Therefore, the thicker the wall the longer the time required. If the thickness of the part or wall can be thinned without affecting its integrity, costs can likely be cut since there is less required machine time per part in addition to possibly producing more parts per run.
Plastic type
The chemistry behind the construction of a plastic also underlies cycle time calculations in important ways. Certain polymers, for example, don’t solidify as quickly as others. If chosen for constructing a certain injection molded part, that extra time translates to longer times in the mold cavity, and thus extended cycle times.
Part design
If an injection molder is looped into the design phase, chances are greatly improved that cycle time missteps will be avoided. Certain design parameters like wrapping plastic entirely around a steel component or another non-flat configuration, designing a mold that cannot accommodate cooling lines, or including unduly thick walls, drives up cooling times. An injection molder that’s previously been through and resolved these kinds of struggles will offer invaluable guidance during the design phase.
Mold material
Like plastics selection and part design, mold material influences outcomes. Steel is the most common mold material used in injection molding machines, but there are occasions when heat must be pulled out of the molded plastic faster than steel allows. In these instances, aluminum or other highly conductive metals may be inserted within the steel tooling so it comes into strategic contact with the plastic to address potential hot spots without interrupting molding or delaying cycle times.
Mold cooling design
Designing the mold to include cooling lines that run through the steel to cool the molded plastic is a typical solution. Injection molders that conduct moldfill analysis to estimate how long it will take that part to reach ejection temperature may encourage the use of cooling lines — or changes to cooling design systems, water temperatures, or flow rates — to optimize the overall molding cycle.
Taken in total, molders that pay attention to how each of these factors are addressed will keep injection molding cycle times low, meaning you can realize increased capacity at decreased costs. What’s more? Accurate estimation of cycle times gives manufacturers the confidence they need in production timelines, from part cost accuracy in planning stages and sales forecasting to part availability for meeting order fulfillment demands.
When it comes to accurately determining production cycle time, an experienced injection molder with deep knowledge of plastic part design, moldfill analysis and ancillary factors impacting production is key. Learn more about the factors contributing to cycle times and how Kaysun contributes to successful outcomes in our eBook 5 Steps to Get New Injection Molded Parts to Market Faster. Click the button below to download your free copy.
Subscribe
TO OUR BLOG
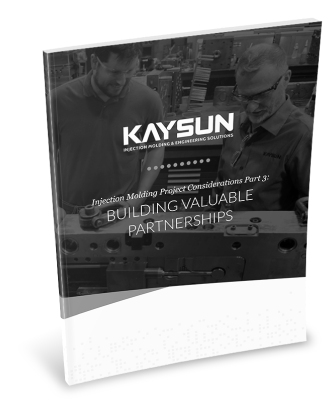
How Do Injection Molder Partnerships Influence Project Costs?
You Might Also Like...
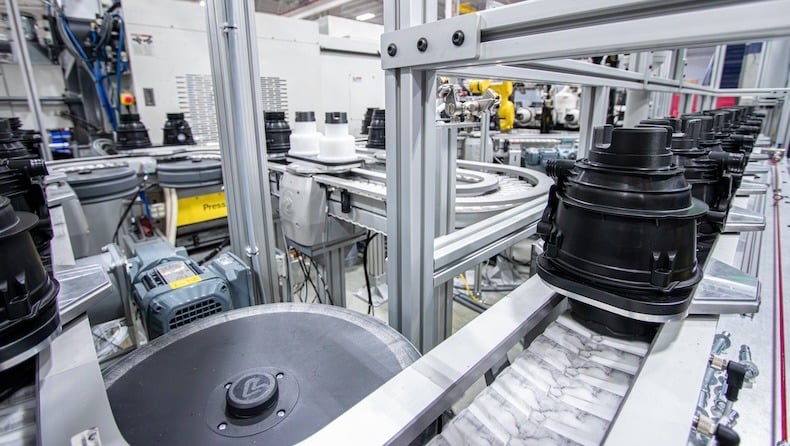
Kaysun Integrates AI on the Production Floor with RJG CoPilot
Industry 4.0 has made manufacturing more dynamic than ever before. Merging IoT, AI…
READ MORE
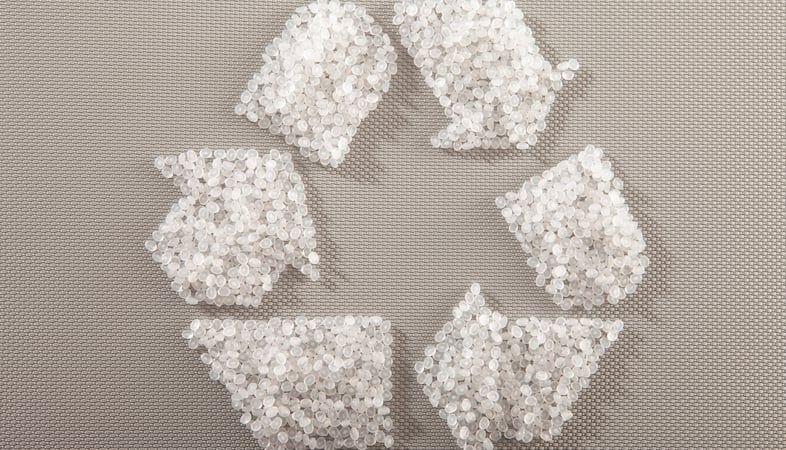
How Kaysun’s Culture of Sustainability Benefits OEMs and The Planet
Injection-molded parts and products are staples for OEMs in industries ranging fro…
READ MORE
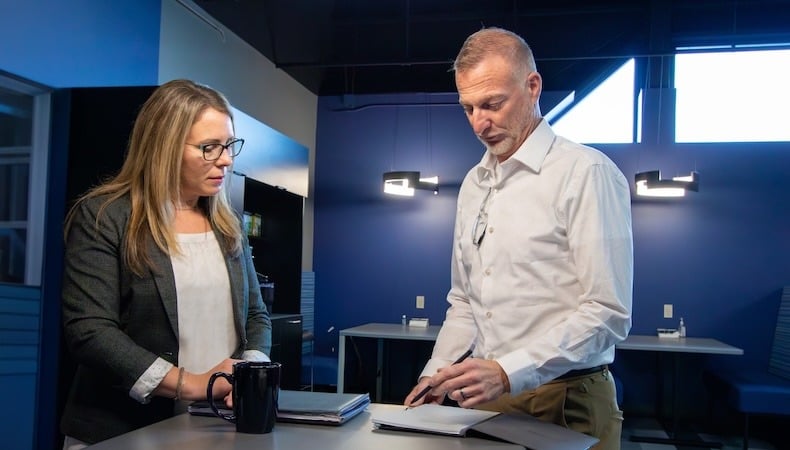
12 Common Injection Molding Questions — Answered!
Injection molding is a versatile and precise process, making it ideal for OEMs tha…
READ MORE