How Specialty Tool Materials Help Speed Cooling Times
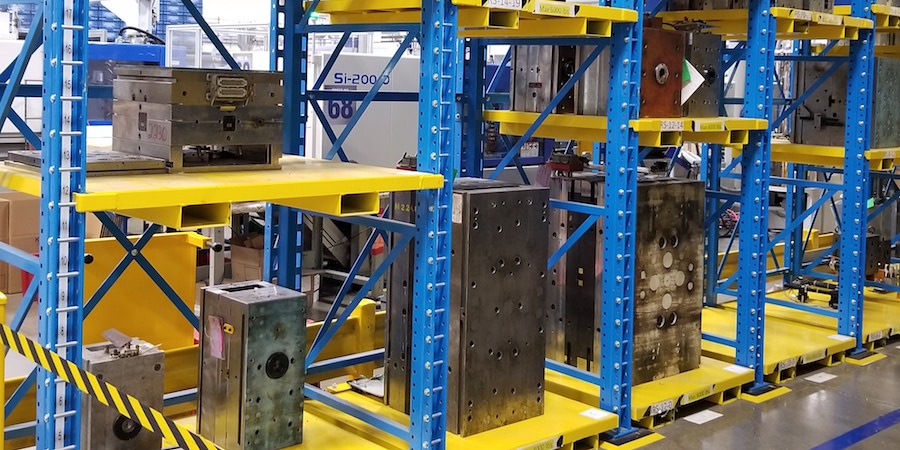
Cooling is one of the most critical parts of the injection molding process. Not only is it the longest part of the process — taking up more than 80 percent of the cycle time — but it's not smart to cut corners when it comes to cooling. In order to achieve precise, tight tolerances, the cooling rate must be carefully controlled — not rushed to completion.
That said, the faster the heat transfer occurs between the part and the tool, the faster the part cools and the sooner it can be ejected. One way to speed up the cooling process without cutting any corners is to make the tool from specialty materials that have higher thermal conductivities compared to standard steel. In the end, the material you choose will depend on the properties of the selected material to be molded (engineered polymers with additives can be more challenging), production and performance expectations, and budget. To help you make the right decision for the best material for your tool, here's an overview of some of the most popular specialty materials in the industry.
Top 3 Specialty Materials for Tooling Design
Although there are many variables at play, tools made from specialty materials with high thermal conductivities can reduce overall production costs by about 25 percent compared to standard steel molds. If you are interested in speeding up the cooling process of your next project, consider using tools made from specialty materials with high thermal conductivity, like MoldMAX®, aluminum, or tungsten carbide.
MoldMAX®
MoldMAX is a family of beryllium-copper alloys that can be easily machined with standard tool-making equipment. The biggest attribute of these materials is their heat-transfer rate — tools made from MoldMAX cool 3-4 times faster than standard mold steels like P20 or H13, which greatly improves cycle times. MoldMAX is ideal for those parts of a tool that can’t accept cooling channels, because they are too narrow or the geometry is too complex.
MoldMAX can be welded and polished, and accept metallic and ceramic coatings. Welding is a big advantage because repairs can be made on the floor. However, drawbacks include higher wear with glass-filled materials and the occasional development of surface corrosion, although that can be easily removed.
Aluminum
When most people think of aluminum, they think of a lightweight, soft metal. What they often don't know is that aluminum also has a thermal conductivity similar to MoldMAX. The softness of an aluminum tool can still lead to premature wear, which has created the widely-held belief that aluminum tools are only good for short runs. That, however, is starting to change. Aluminum alloys continue to get harder (for example, QC-10 and Alumold have a Brinell hardness of 150-180 and Rockwell hardness of B82-B87) and can handle bigger production runs.
Unlike MoldMAX, aluminum is very difficult to weld. Because of this, any tool failures require the tool to be shipped out for repair, which can result in costly delays. Even with the stronger aluminum alloys of today. In general, aluminum tools are much easier to damage than steel tools.
Tungsten Carbide
Tungsten carbide is a very hard, somewhat brittle material with a compressive strength that is greater than almost all other metals and alloys. It is much more rigid than steel, brass, and cast iron. Another key advantage is that tungsten carbide has a high thermal conductivity — about 2-3 times that of P20, and just slightly less than aluminum and MoldMAX.
This great hardness, however, means it can only be machined with diamond tools. The combination of high thermal conductivity and great strength make tungsten carbide an ideal material for core pins, which alone can reduce molding cycle times by 25 percent or more on certain projects.
Depending on your production needs, using a specialty material for your tool with a high heat-transfer rate could be a very cost-effective move. The biggest advantage is that these specialty metals and metal alloys can reduce cycle times by as much as 30-40 percent, which speeds up production and reduces costs significantly.
For more on tool materials and how tooling design impacts cooling time, read our Tooling Design for Injection Molding whitepaper. Click the button below to access your copy.
Subscribe
TO OUR BLOG
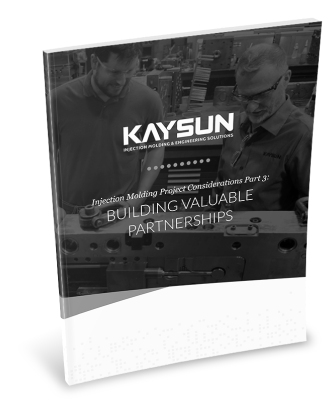
How Do Injection Molder Partnerships Influence Project Costs?
You Might Also Like...
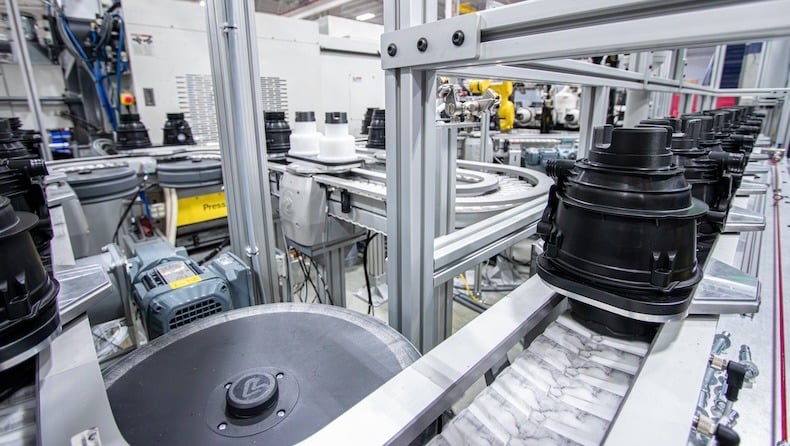
Kaysun Integrates AI on the Production Floor with RJG CoPilot
Industry 4.0 has made manufacturing more dynamic than ever before. Merging IoT, AI…
READ MORE
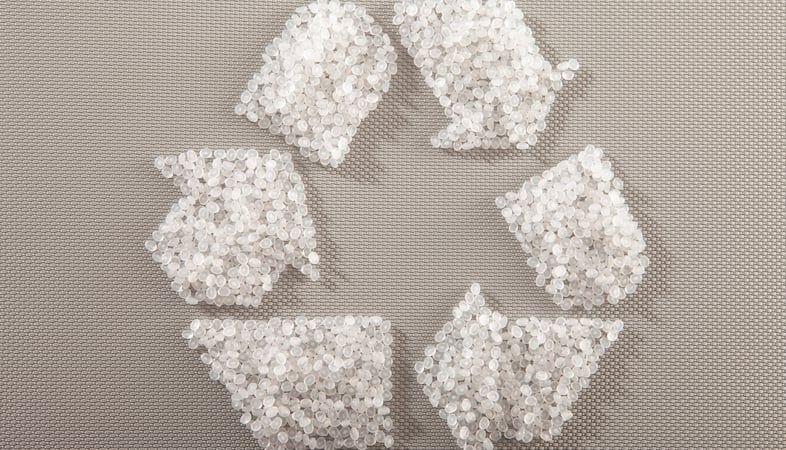
How Kaysun’s Culture of Sustainability Benefits OEMs and The Planet
Injection-molded parts and products are staples for OEMs in industries ranging fro…
READ MORE
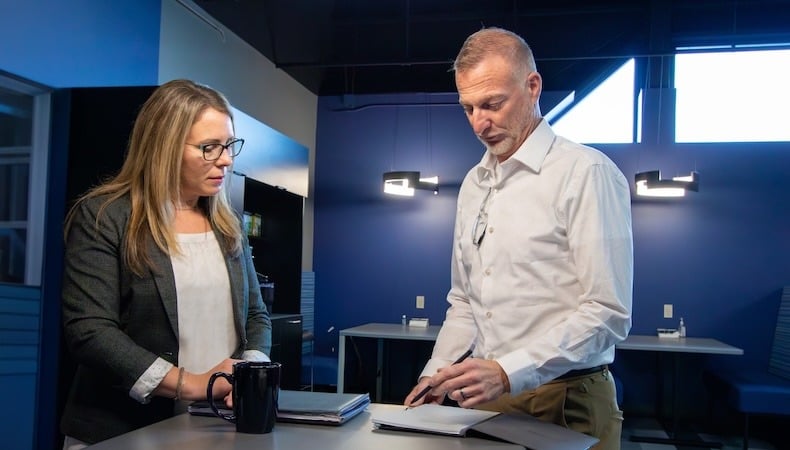
12 Common Injection Molding Questions — Answered!
Injection molding is a versatile and precise process, making it ideal for OEMs tha…
READ MORE