12 Common Injection Molding Questions — Answered!
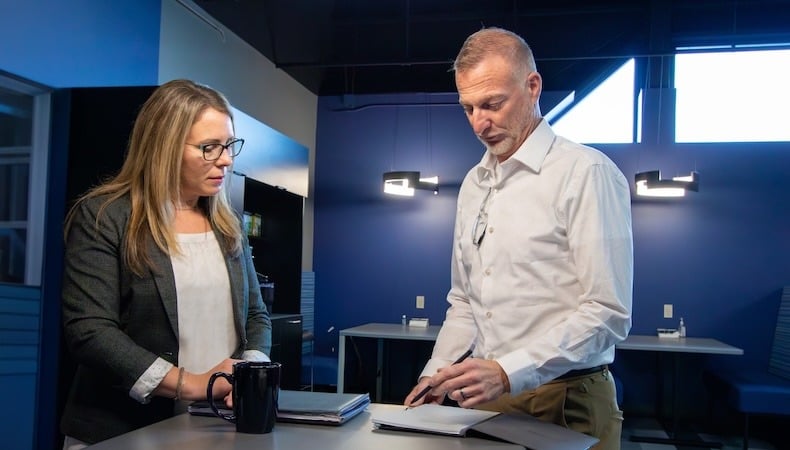
Injection molding is a versatile and precise process, making it ideal for OEMs that rely on complex, highly engineered plastic parts for high-performance applications such as medical devices or automotive engine components.
Given the importance of these injection-molded parts — and the potential far-reaching impact of part defect or failure — selecting a custom injection molding partner must be a carefully considered decision. As a result, OEMs must ask the right questions to gain insights and assurances to help them make the best strategic choice.
Often, these questions revolve around project-related design, materials, process optimization, quality assurance, testing, etc., and the injection molder’s engineers are usually best suited to answer.
As the trusted custom injection molder for OEMs in a range of industries, Kaysun engineering professionals routinely field the frequently asked questions we’ve compiled and answered here.
1. Which plastic should I use for my application?
Material selection is uniquely application-driven since characteristics and factors such as mechanical properties, performance requirements, tooling needs, operating environment, regulatory standards, and price all come into play. Approving a tentative plastic or suggesting a “good fit” based solely on specs and a print would be a disservice to manufacturers and the injection-molded parts. Kaysun is committed to being an injection molding partner that comes alongside OEMs to guide discussions and choices to match design, materials, and goals.
2. Can I substitute plastics?
There are often opportunities to substitute materials for various reasons, but it’s typically not a simple swap-out. Mechanical properties, thermal performance, chemical compatibility, aesthetics, potential tooling changes, processing differences (cycle times, weight, etc.), dimensional stability, secondary operations, compliance considerations, and cost may all be impacted. The expertise of an injection molder is critical in weighing advantages and disadvantages before deciding. Kaysun’s specially trained engineers and our 10 master molders offer analysis on plastics behaviors, mold flow, and potential barriers to success that may not otherwise be readily apparent.
3. Should tooling be made from aluminum or steel?
Steel tooling was once an expensive and time-consuming option that made the comparative speed and cost-effectiveness of creating aluminum tooling an attractive alternative in certain situations. Over the years, manufacturing advancements made cutting steel as efficient as machining aluminum, and steel quickly became the tooling material of choice. Steel provides the closest match to actual production conditions during tooling design and testing, along with better structural integrity and consistent molding repeatability to ensure tight tolerances and complex geometries are maintained to top-quality standards.
The choice really isn’t either/or. Selecting the proper grade of molding tool steel is essential to achieve the desired project outcomes. It influences how plastics behave during molding, which could impact cycle times, part criteria, production volume, and overall cost and maintenance.
4. Can tooling design be modified after the build is complete?
Technically, tooling design can be changed at any point in production. However, where the tooling change falls in the process can be both challenging and costly. Depending on the scope of the changes and status of qualification, Kaysun may be able to offer in-house adjustments to existing tooling to mitigate outsourcing expenses and minimize downtime while accomplishing the goal.
5. Who owns the part design? Tooling?
Ownership typically depends on the arrangement agreed to between the injection molder and customer. Kaysun has non-disclosure agreements in place with all customers to protect intellectual property. Proprietary information and processes, part design, and tooling are and remain the property of the OEM.
6. What experience do your engineers have with scientific molding, DfM, and mold fill analysis?
Kaysun engineers have extensive training and proven experience in scientific molding, Design for Manufacturability (DfM), and mold fill analysis. Expertly applying these predictive principles and processes translate to more efficient injection molding.
DfM focuses on part design optimization and defect prevention through examining part geometry, wall thickness, draft angles, and material flow early in the design process. Should challenges arise they can be corrected at the point of least time and monetary impact. Likewise, affirming that a design is manufacturable early on prevents costly redesigns and delays.
Simulation tools such as mold fill analysis provide valuable insights into the behavior of materials during injection molding. They help engineers visualize how plastic flows through tooling, finding potential defects such as sink marks, and making adjustments to optimize the design before tooling is made. Kaysun engineers depend on mold fill analysis and other advanced simulation software to refine part designs and molding processes — resulting in lower development time and costs without compromising quality outcomes.
7. Do you offer value-added services?
Molders that offer value-added services (aka, secondary operations) play an important role in supply chain management and delivering cost efficiencies for OEMs in need of welding, heat staking, machining, assembly, etc. Kaysun's vertically integrated services are customized to specific project needs, and provide competitive advantages in consistent product quality, timely production, limited risk exposure, and enhanced reliability.
8. How is automation incorporated into your molding process?
Automation is increasingly important in injection molding to improve efficiency, consistency, and safety. At Kaysun, we use a variety of automated systems, and nearly all of our machines include robotics for part removal, insert loading, and secondary operations such as assembly or inspection. Automation allows us to maintain consistent cycle times and cooling times, manage quality, and improve overall throughput, which is especially beneficial for high-volume production runs.
9. How old are your presses? What does maintenance and replacement look like?
Presses are the workhorses of injection molding. How a molder invests in and maintains presses could signal their approach to leaning into challenging projects and innovative solutions. Annually, Kaysun replaces two or three molding machines that are nearing the end of their operational life, and also adds two or three new machines to increase capacity. This regular best practice helps prevent equipment-related downtime and also ensures production is supported by a fleet of state-of-the-art machinery and technologies.
10. What process controls are in place for quality assurance?
The precision and reliability required of complex applications means injection molding quality control held to the same exacting standards. Kaysun is committed to cross-functional, collaborative teamwork and implementation of rigorous quality control. In-process monitoring using RJG technology, dimensional inspections, and in-depth statistical analysis of tight tolerances is supported by our in-house Quality Lab. Quality technicians conduct comprehensive testing on samples at intervals of 3 times per shift to ensure all parts conform to specifications.
11. How do you manage part defects and nonconformities?
Automated inspections using RJG technology continuously scan for defects. Should a suspect cycle arise, robots extract the nonconforming parts for further engineering evaluation and correction. Should dimensional nonconformity occur, engineers backtrack to the last known good inspection to analyze data from that point forward to find and correct errant dimensions that caused departure from specifications.
12. What sustainability initiatives have you implemented to reduce your corporate carbon footprint?
Creating a more sustainable workplace can be challenging for manufacturers, but Kaysun is up to the challenge. With the support of our internal Green Team, we have several initiatives that focus on reducing our carbon footprint.
Since injection molding consumes a lot of energy, finding ways to conserve it is a primary goal. Installing our Central Material Handling System saves 1.5 million kilowatt hours per year. We also committed to plastic-waste-to-energy conversion in partnership with renewable fuel and power producer Convergen Energy, diverting more than 2.7 million pounds of plastic waste from landfills and helping our local utility company reduce greenhouse gas emissions by 40%.
LED lighting, installation of a more efficient tool chiller system, and other facility upgrades also contribute to helping Kaysun be responsible stewards — a goal recently recognized by receiving a Focus on Energy 2024 Energy Efficiency Excellence Award and a grant to fund future conservation efforts.
Understanding the intricacies of injection molding is essential for any manufacturer looking to partner with an injection molder that can consistently produce high-quality plastic parts. By addressing these frequently asked questions, we hope you gained valuable insights into how Kaysun can help you achieve your injection molding goals.
Have more questions? Great! Reach out to the Kaysun team any time. We’re here and happy to help.
If you have more questions or would like to discuss your project in detail, feel free to reach out to our team of experts. We’re here to help you succeed!
Subscribe
TO OUR BLOG
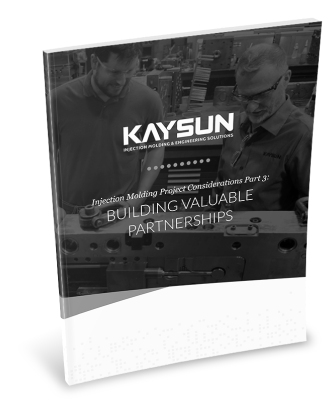
How Do Injection Molder Partnerships Influence Project Costs?
You Might Also Like...
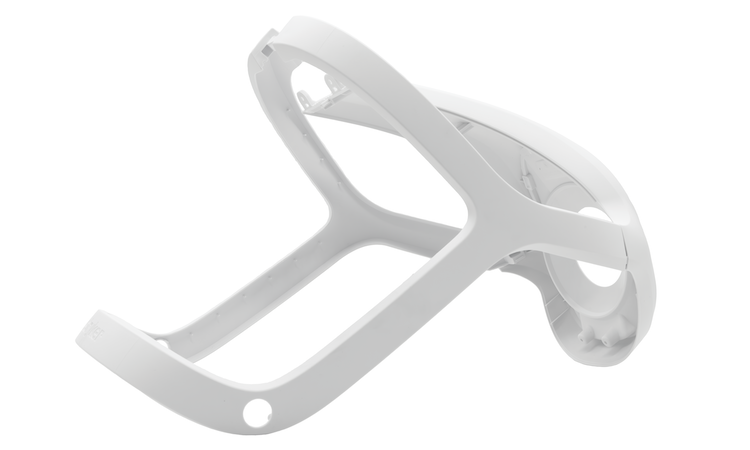
Stryker Turns to Kaysun for Steri-Shield® 8 Helmet Solution
When Stryker set out to develop its next-generation Steri-Shield® 8 Personal Prote…
READ MORE
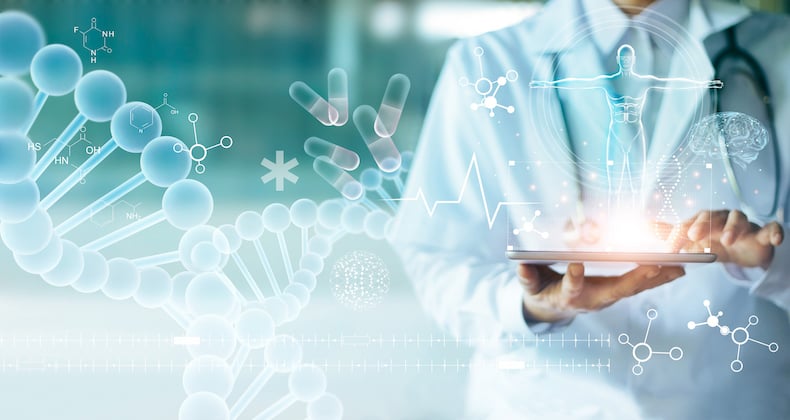
How MD&M West 2024 Keeps MedTech Professionals Ahead of the Curve
MD&M West is one of the largest and most respected medical device trade shows …
READ MORE
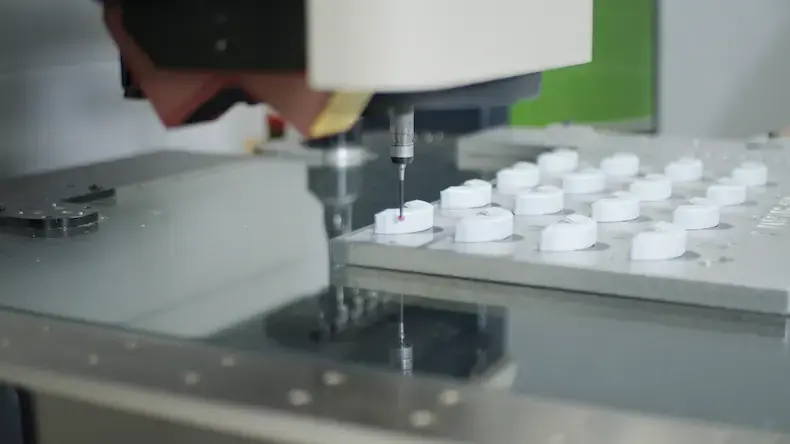
How MedAccred Accreditation Helped Kaysun Enhance Processes & Quality Systems
When you operate at the top of your game, reach higher. Kaysun had already shown i…
READ MORE