Beyond PEEK: High-Temperature Injection Molding Solutions with PAEK Plastics
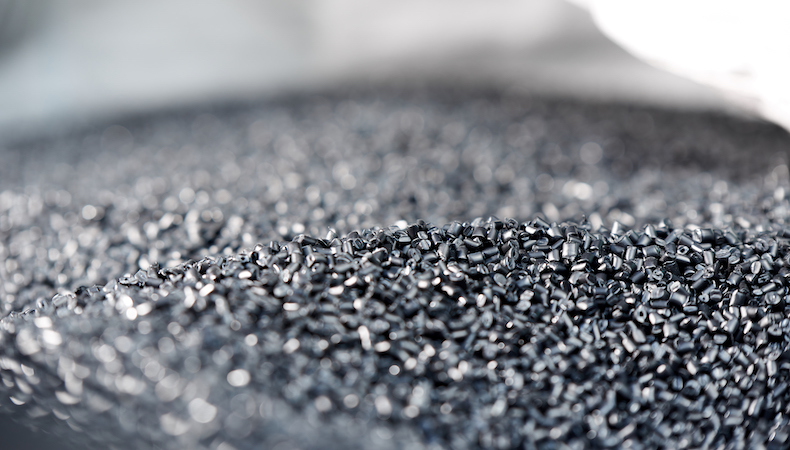
Mention “high-temperature thermoplastic” and chances are that polyether ether ketone (PEEK) comes to mind. Its high heat tolerance, mechanical strength, and chemical resistance make PEEK resin ideal for many demanding applications including those in the automotive, electronics, aerospace, medical, and other markets. But is it the only choice?
PAEK Plastics Provide High Temperature Options
PEEK material falls within the family of semicrystalline thermoplastics known as Polyaryletherketones (PAEK). Polymers within the PAEK plastics classification all have high-temperature stability and excellent mechanical strength. Key differences appear in the temperatures at which the polymers’ textures change — the glass transition temperature (Tg) and melt temperature (Tm).
In short, Tg correlates to the temperature at which a solid, glassy polymer transitions to a viscous, pliable state. Tm refers to the temperature at which the structured molecules of crystalline polymers become random chains of molecules (or, amorphous) — essentially, the thermoplastic begins to melt.
PAEK THERMOPLASTICS
Approximate Tg/Tm (in ℃)
POLYMER TYPE | GLASS TRANSITION TEMPERATURE (Tg/℃) | MELT TEMPERATURE (Tm/℃) |
Polyether ether ketone (PEEK) | 151 | 338 |
Polyether ketone (PEK) | 160 | 372 |
Polyether ketone ketone (PEEKK) | 160 | 360 |
Polyether ketone ether ketone ketone (PEKEKK) | 165 | 384 |
Polyether ketone ketone (PEKK) | 156 | 338 |
The Tg and Tm temperatures of PAEK plastics don’t vary greatly, yet even the seemingly minor differences can impact critical properties of an injection-molded part, including:
- flammability and smoke emission
- mechanical strength
- impact and tensile strength
- dimensional stability
- flexibility
- adhesion
- creep
- chemical resistance
- wear resistance
- fatigue resistance
- moisture absorption
- insulation strength
- radiation resistance
Tooling Considerations
Typically, high-temperature resins can be run on conventional injection molding equipment — with one important caveat. The tooling used with PAEK materials must be able to achieve and withstand high temperatures (at least 165℃) in order to process unreinforced and reinforced PEEK, PEK, PEEKK, and other PAEK materials at processing melt temperatures generally ranging from 370℃ to 410℃.
To ensure consistent, defect-free part production using high-heat resins, tooling design must address several key factors:
- Tool material: Steel is the standard choice for tooling, with H-13, S-7, or P-20 high-strength options being most durable for high-volume production runs with PAEK thermoplastics. Steel tooling is also an investment — if prototyping, aluminum may be most cost effective
- Tool degradation: The processing temperatures of PAEK resins are the highest of all plastics used in injection molding. Tool design needs to take into account the size of the machine and barrel to prevent premature equipment and tool wear
- Heating/cooling: Heat transfer channels and/or thermal pins are essential in tool design to properly heat the tool before injection molding, and cool the molded part prior to ejection
- Maintenance cycles: With PAEK thermoplastics, tooling maintenance is a priority since there is the potential for premature wear and also the need for more scheduled cleanings to help ensure defect-free injection-molded parts and to keep production on track
While not directly related to tool design, it’s important to note injection molding at elevated temperatures is particularly susceptible to moisture. Materials must be completely dry prior to processing or failure could occur even when the most accurate tools are used.
Help From an Experienced Injection Molder
For complex applications, there are rarely any easy solutions — and that includes identifying a high-temperature thermoplastic and maximizing its use during injection molding.
Myriad considerations go into the final decision. It requires input from an experienced injection molding partner such as Kaysun, and guidance like that which you'll find in our white paper, Processing High-Temperature and Engineered-Grade Resins. Click the button below to download your copy of this valuable resource now.
Subscribe
TO OUR BLOG
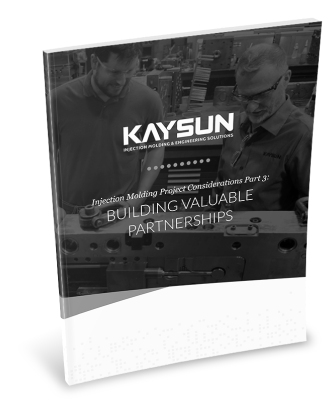
How Do Injection Molder Partnerships Influence Project Costs?
You Might Also Like...
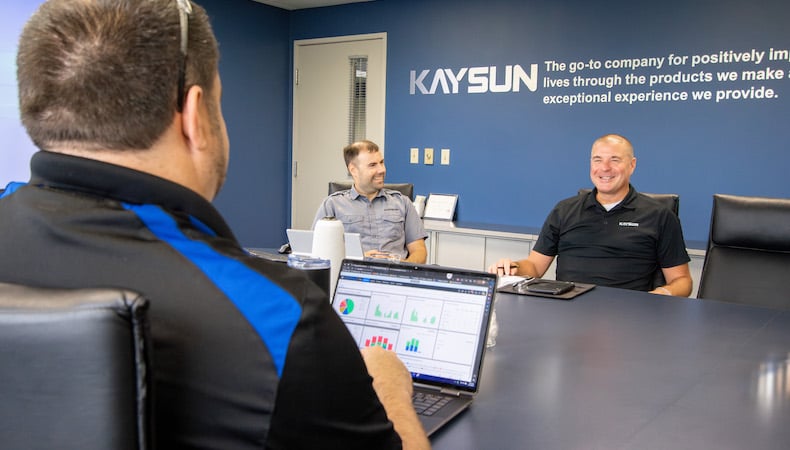
Top 3 Custom Injection Molding Trends to Watch in 2025
Despite being considered more energy efficient and producing less waste than other…
READ MORE
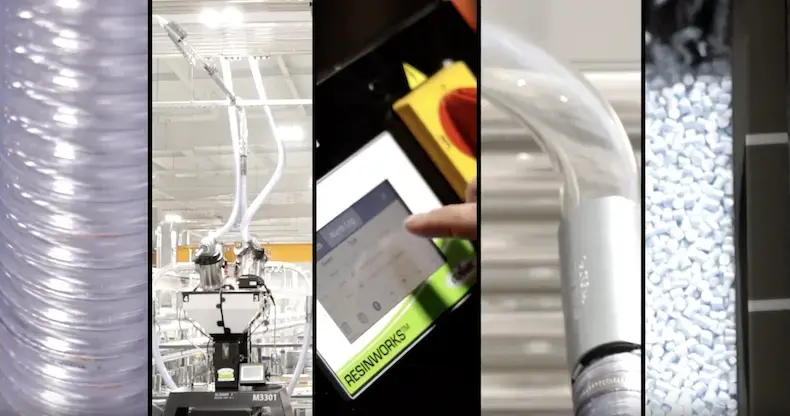
How Centralized Material Handling Streamlines Injection Molding
We consistently look for new ways to deliver timely service and top-quality parts …
READ MORE
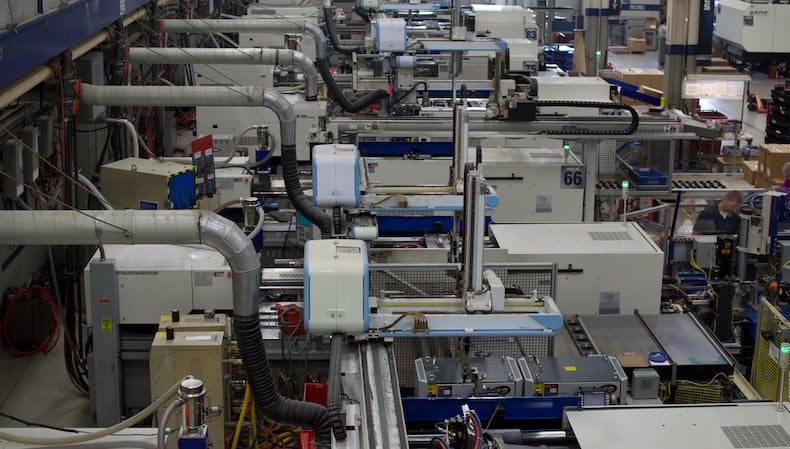
Top 14 Benefits of Injection Molding
OEMs across many industries enjoy the benefits of injection molding. It’s ideal fo…
READ MORE