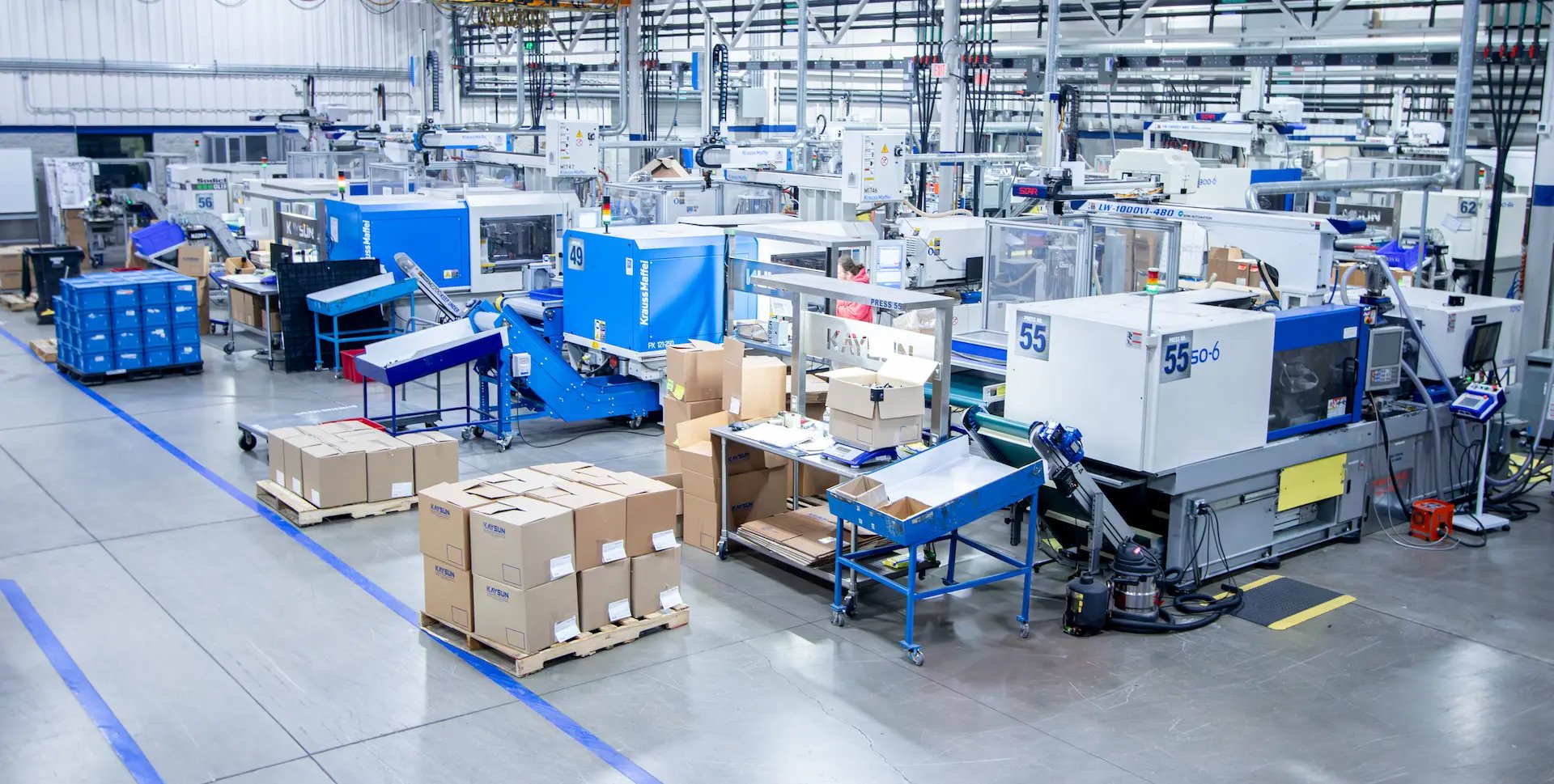
Using High-Temp and Engineered-Grade Resins Advanced Plastics Mean New Opportunities For Injection Molding
Complex applications often require advanced molding solutions. If you’re considering using the custom plastic injection molding process for your next project, our eBook is a must read. It outlines the essentials, including:
- Top benefits of custom plastic injection molding
- Projects best suited for the process
- Common technologies and operations used
- How to select the right molding partner
- And more!
Fill out the form to access your copy of this eBook now!