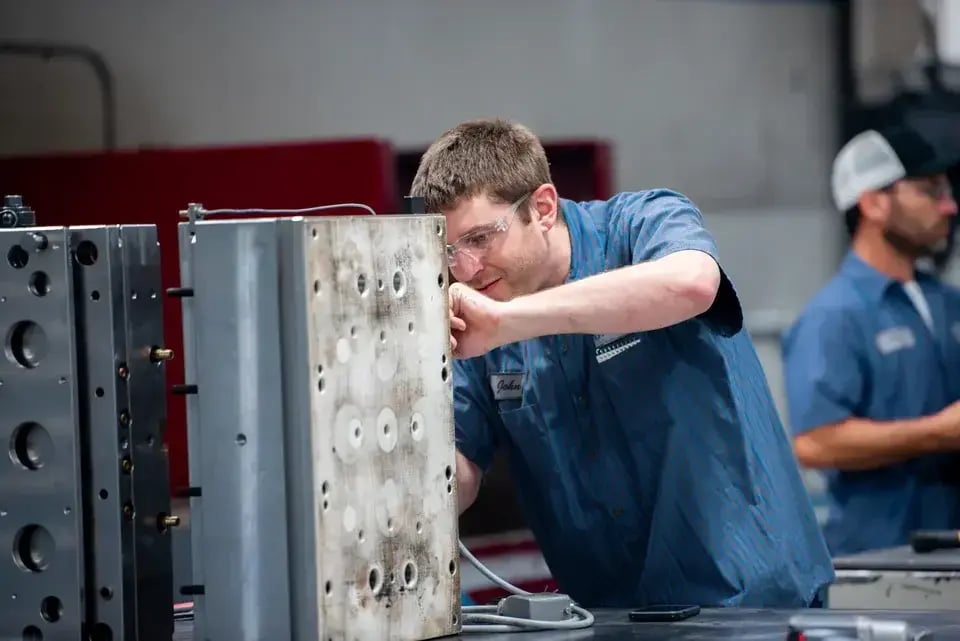
Tool Building
Injection molding tool design and prototyping for complex plastic parts and products is highly technical and invaluable. The right tooling decisions for injection-molded parts with tight tolerances optimize production, reduce costs, and improve quality and customer satisfaction.
In general, injection-molded parts and products with tight tolerances require sophisticated tooling. This is where scientific molding and mastery of materials behavior come into play. Kaysun engineers rely on their in-depth knowledge and training to design and construct the highest-quality tool for the project.
Injection Molding
Tool Materials
The tool is one of the most expensive parts of the injection molding process. The proper grade of steel balances tooling wear and toughness so components don’t wear out prematurely — ensuring the longest possible tool life with minimal maintenance.
To determine the correct steel hardness, several factors must be considered:
- The size of the production run
- The complexity of the part
- The finish quality needed
- The material to be molded (some plastics are corrosive; others contain abrasive glass fibers)
The hardest metals, such as H13 steel, are best for high-volume, highly complex parts. Softer metals, such as aluminum, can be sufficient for smaller runs and simpler part designs. In general, the softer the metal, the easier and less expensive it is to machine.
Injection Molding
Tool Qualification
After considerable preparation regarding product design and process selection, the tool is constructed — a big step toward production.
To ensure consistent and repeatable production of flawless molded parts, though, the tool must be challenged completely before it’s called into action. Injection molding tool qualification is one of the most important jobs of the process engineer.
Kaysun engineers look forward to qualifying tools because it’s a test of how well they designed them. They push the tool relentlessly under realistic conditions (and sometimes beyond) to see where adjustments may be needed. Tool qualifying is a critical step in creating a highly efficient, low-cost production process that ensures top quality and repeatability.
In-House Injection Molding Tool Design and Adjustments
Many injection molders rely on outside tool builders to custom-build the initial tool. Tooling rarely arrives with perfect dimensions. After the tool is qualified, adjustments are typically needed to meet design specifications. For most injection molders, this requires sending the tool out for final adjustments, which can take a month or more to complete.
At Kaysun, we make most of these adjustments in-house and “fine tune” tools after initial sampling to improve the tool core/cavity geometry and achieve the desired dimensions.
The main goal of injection molding tool design is to create a product with highest possible manufacturability. That means a high-quality process that is easy to operate and maintain, and that consistently meets customer specifications — all at the lowest possible cost.
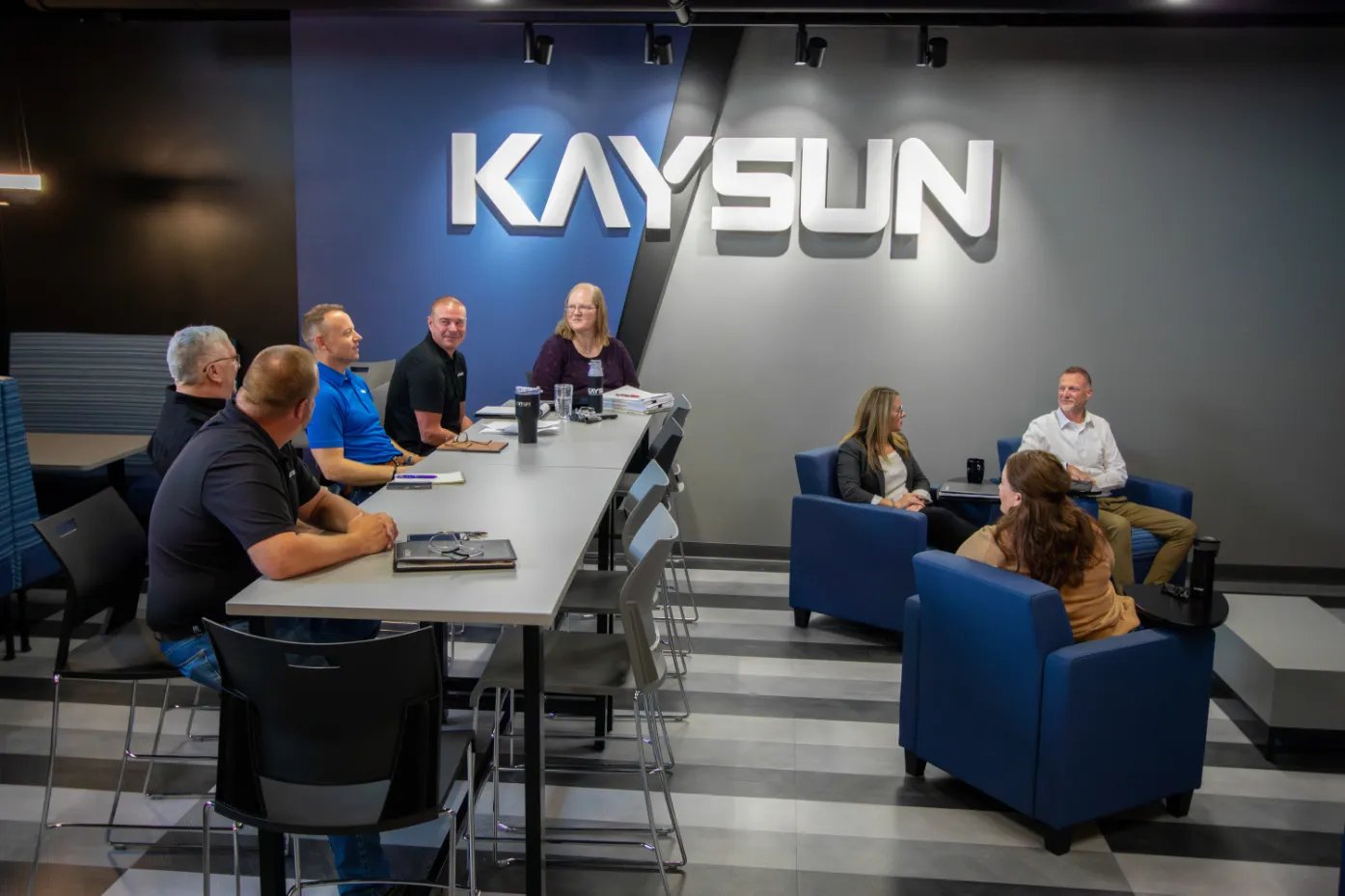
Does your company fit our ideal customer profile?
Complete the form to request a free consultation with our plastic engineering experts.