Injection Molding Process Development: 6 Steps to Streamline & Succeed
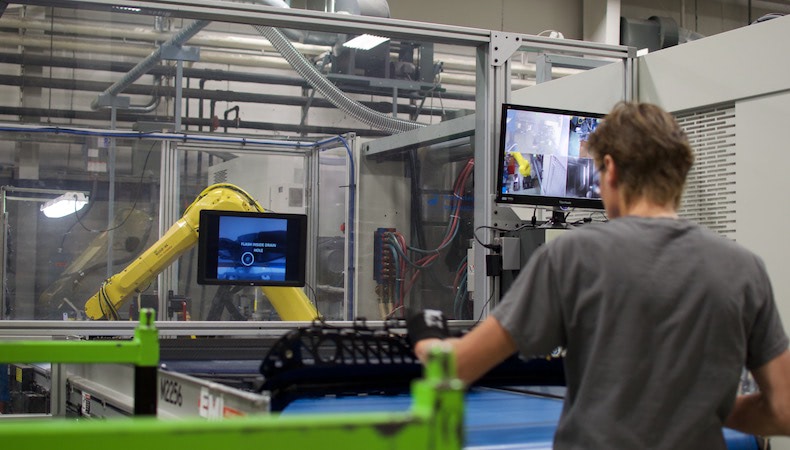
Injection molding is a dynamic, complex process that, simply by the nature of its many variables, requires some testing and adjustments to get it just right before you can start production.
Some manufacturers, however, get their priorities mixed up; they choose to focus on completing the tool first and then build the process around the finalized tool, thinking this saves time and money. This approach typically results in production problems that end up slowing down injection molding process development, and reducing quality and repeatability.
This blog post provides 6 solid, repeatable steps that create the best approach to streamline a plastic part project utilizing custom injection molding:
- Develop a consistent, efficient process
- Maximize your injection molding processing window
- Utilize scientific molding
- Establish a production process prior to tool adjustment
- Pay attention to tool temperatures and venting
- Consider the tool’s functionality during the initial tool sampling
#1: Develop a Consistent, Efficient Process
What came first, the chicken or the egg? Well, in this case, it’s vital to develop a consistent, efficient process first, and then fine-tune the tool to fit that process.
As a guideline, the main steps of the injection molding process are:
- Proper melting of the plastic resin
- Injection at the correct rate
- Packing at the proper pressures
- Cooling with the correct temperature tool surface
- Ejecting the part after the proper amount of cooling
By designing your tool around the injection molding process — rather than trying to figure out how to complete certain steps with your finished tool — your production is much more efficient. Plus, your time to market is reduced.
Streamline these processes, and you avoid running into bigger problems later on in production.
#2: Maximize Your Injection Molding Processing Window
Optimizing the injection molding and tooling process relies on creating the largest possible injection molding processing window. If the team strictly processes for dimensions only, the process may be insufficient to create the molding conditions that yield the most consistent part, because there are subtleties in the process that cannot be fully predicted without testing.
For example, injection speed may need to be adjusted to counteract splay created by shear stress, which can be caused by the shape of the part. Injection speed can also influence dimensional results.
Likewise, the final part has differences in shrink due to direction of material flow. Final shrink is influenced by many molding parameters. Molding within the range of acceptable parameters — cross-checked with final dimensions — allows the final processing “window” to be established.
Of course, you want a high-quality part that meets performance specifications and looks good. The larger the processing window is, the lower the risk for problematic start-ups and inconsistent product quality.
#3: Utilize Scientific Molding
Typically, the best way to factor in the many variables that come into play (and determine the best process) is by following the principles of scientific molding.
Here’s an example. With scientific molding, the proper viscosity of the material is monitored by pressure curves. When lot-to-lot material variations occur, the molding process is adjusted to produce the same pressure curves that were generated during the initial process development — ensuring repeatability and saving time.
There are many different ways scientific molding can benefit your plastic molding development process, however, and this scientific molding whitepaper explains more.
#4: Establish a Production Process Prior to Tool Adjustments
As mentioned earlier, it’s crucial that you establish the production process prior to making any steel adjustments for the tool. Many processing parameters can influence the size of the part and its geometric characteristics, which then impact functionality, longevity, and performance.
Let’s explore an example. O-ring groove dimensions — diameter, roundness, depth, surface finish — can be negatively affected by process variations, resulting in diminished performance (or even failure). Process changes can also have an adverse effect on part assemblies, including how parts fit and work in assembly fixtures, inspection fixtures, and other ancillary equipment.
When the part is “designed with manufacturing in mind,” and the molding process is dialed in before making steel adjustments, you can make accurate steel changes for future part processing. That’s extremely important for consistency — especially when your process calls for work-in-progress parts that are overmolded at a later time.
#5: Pay Attention to Tool Temperatures & Venting
There are three critical processing parameters to thoughtfully consider in the pre-mold design stage of injection molding process development: location of vents, cooling channels, and transducers.
Venting is a critical part of tool function/process development because vents can change flow patterns in the tool. This can easily be added later if needed, after steel changes to a developed process.
Cooling channels are also important to the cooling rate, where infrared cameras or temperature sensors identify the need to change steel or add cooling to these hot spots.
Strategically placed transducers also help develop a robust molding process – one that gives shot-to-shot consistency for making the determination through part measurement, and applying it to steel change.
#6: Consider the Tool’s Functionality During Initial Tool Sampling
Before you set the plastic molding development process and make the necessary changes to your tool, it’s critical that you consider the tool’s functionality during initial tool sampling.
If the part sticks in a certain location in the tool, for example, more polishing or ejection is needed. If the cycle is prolonged or the part comes out deformed, there may be a hot spot in the tool that requires additional cooling.
Likewise, if a part does not have uniform wall thicknesses or has thick areas, there may be a cooling issue that needs to be addressed. This can be evaluated with flow and cooling analysis to pinpoint these spots and make the necessary processing and tooling adjustments. At that point, the actual specific dimensions of the tool is calculated to fit the process, not the other way around.
Want to learn how an experienced injection molder guides all aspects of part production and becomes a complete solution for manufacturers? Our tip sheet, Injection Molding Project Considerations Part 2: Production, explains how to leverage that trusted partnership in production. Click the link below to download your copy.
Subscribe
TO OUR BLOG
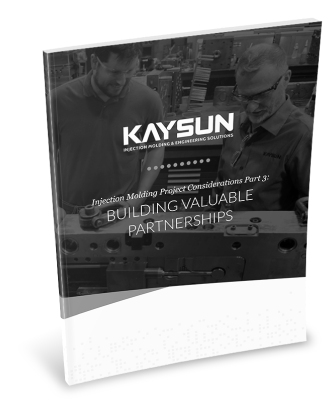
How Do Injection Molder Partnerships Influence Project Costs?
You Might Also Like...
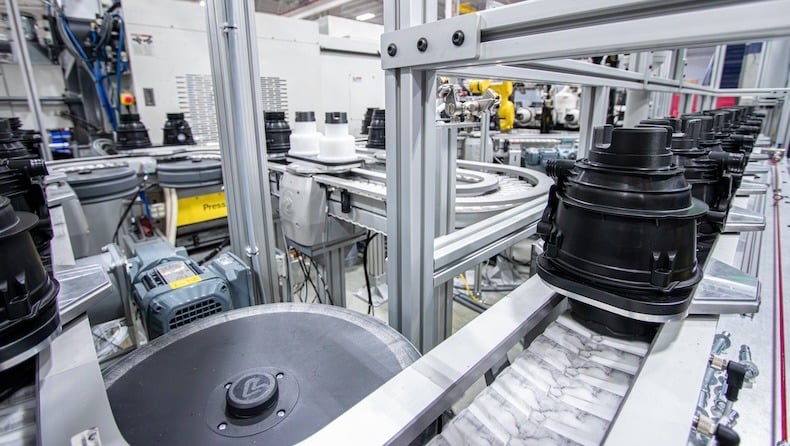
Kaysun Integrates AI on the Production Floor with RJG CoPilot
Industry 4.0 has made manufacturing more dynamic than ever before. Merging IoT, AI…
READ MORE
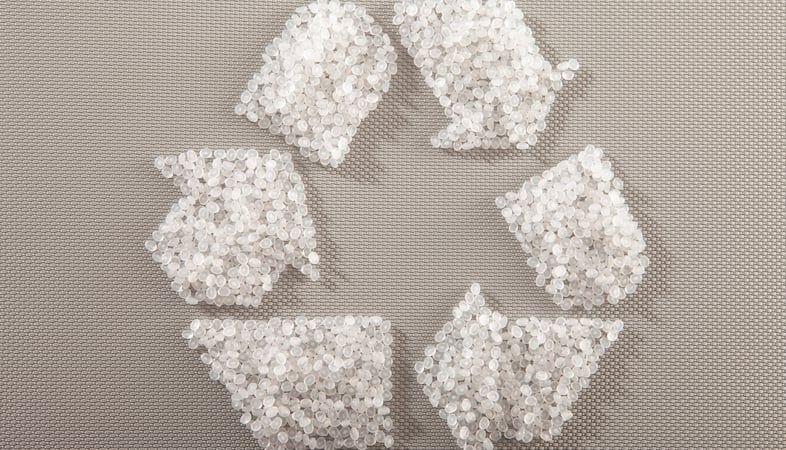
How Kaysun’s Culture of Sustainability Benefits OEMs and The Planet
Injection-molded parts and products are staples for OEMs in industries ranging fro…
READ MORE
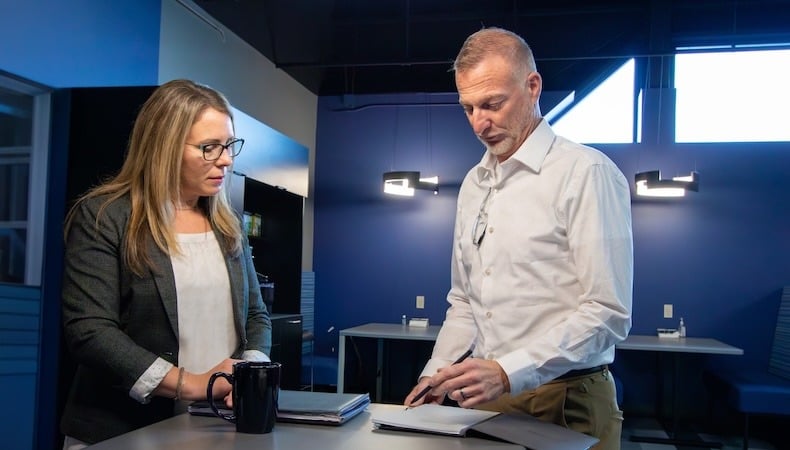
12 Common Injection Molding Questions — Answered!
Injection molding is a versatile and precise process, making it ideal for OEMs tha…
READ MORE