How In-House Tooling Capabilities Improve Your Projects [VIDEO]
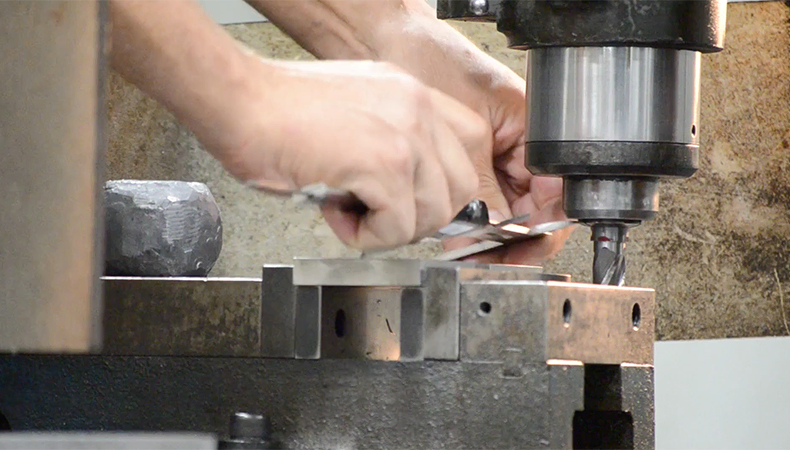
Tooling is arguably the most important part of the entire injection molding process. Not only does the tool need to be perfect to ensure all design specifications are met, but it’s also one of the most expensive, time-consuming fixes if something isn’t right—especially if you’re working with a third-party toolmaker. Working with an outside toolmaker for projects requires a lot of back and forth communication, leaving room for misinterpretations and sometimes delayed responses.
At Kaysun, our experienced in-house toolmakers work side-by-side with our engineers and inspectors to make sure everything is built exactly to specification, and often times our team meets right on the tool room floor to work things out in-person. This eliminates the need for costly rework to the tool, as a single iteration can cost between $1,000 to $10,000 and take anywhere from 3 to 5 weeks to complete.
To better explain just how valuable having in-house tooling capabilities is, watch the short video below.
Video Transcript
Having our own tool room in-house is excellent to help the engineering team through the development phase.
We have all the equipment necessary to build tooling from scratch, but we utilize it for engineering changes and adjustments. So when we have a part that needs to be round, it’s not, we have to go in and reverse engineer that part, develop the programming to reverse engineer it, and then program the electrodes, cut the electrodes, inspect the steel, and then do that burning in-house to make it out of round.
We have EDM equipment available for doing the CNC machining of the electrodes.
What’s even better is that we have the tool room in-house along with our inspection team and our engineering team, so any questions or concerns, we can all sit down together at the CMM machine, review the data, make sure that it is correct, and then go in and make adjustments to the program and adjustments to the steel.
If you don’t have the in-house tool room capabilities and a very good tool-making team, as well as tooling engineers, you’re dependent upon the schedule of your outside tool shop to make these adjustments. And then what happens is we’ve run into this where we have had to go outside.
Sometimes things can get lost in translation. We were going to go positive x and then we ended up going negative x. Or it wasn’t the same orientation that we inspected the part that they applied it in the steel. Those are some of the risks, not only from a timing standpoint, but from a mistake standpoint, that can delay a program, create a situation where now you have to weld or replace inserts rather than getting it right the first time.
So again, that’s an advantage we have having the inspection in-house, the tool room in-house, our project and tooling engineers in-house.
You can really double- and triple-check everything before you go and change steel.
Want to learn more about how you can reduce your upfront tooling costs and improve quality? Download our free whitepaper, Mold Design & Tooling for Injection Molding.
Subscribe
TO OUR BLOG
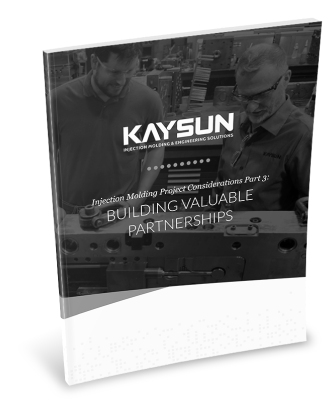
How Do Injection Molder Partnerships Influence Project Costs?
You Might Also Like...
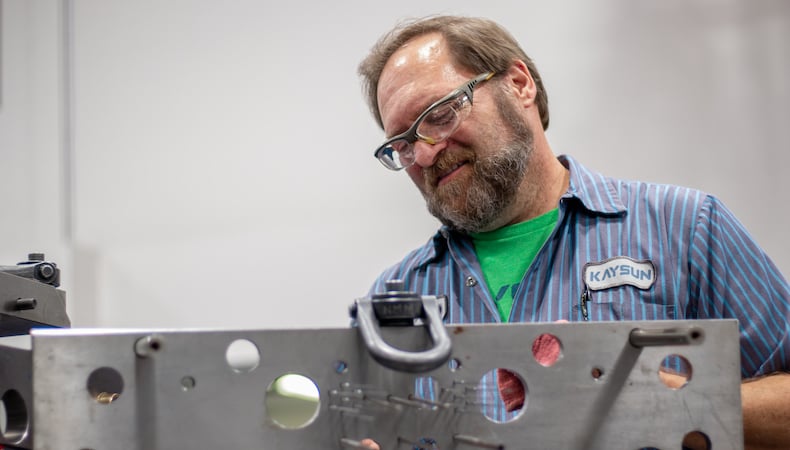
Injection Molding Quotes: 5 Tips to Help Get Tooling Right
Few things impact injection-molded part quality as much as tooling design, materia…
READ MORE
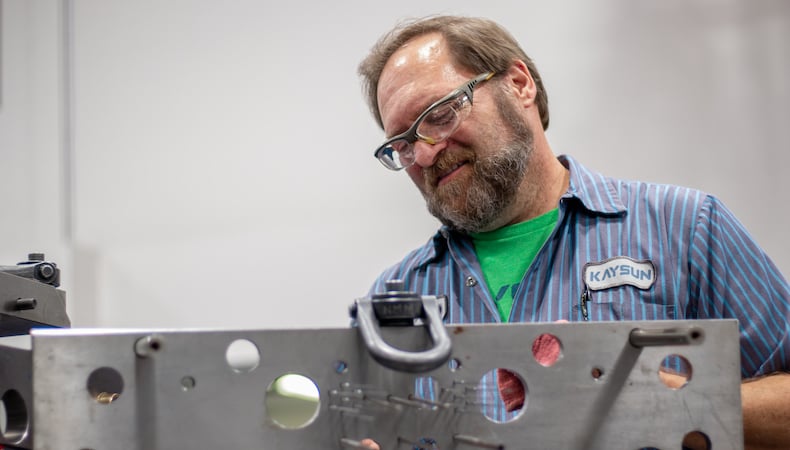
Tooling Audits & Evaluations: How Molders Help OEMs Gauge Health of Assets
When an OEM pursues an injection molding program, tooling is among the most highly…
READ MORE
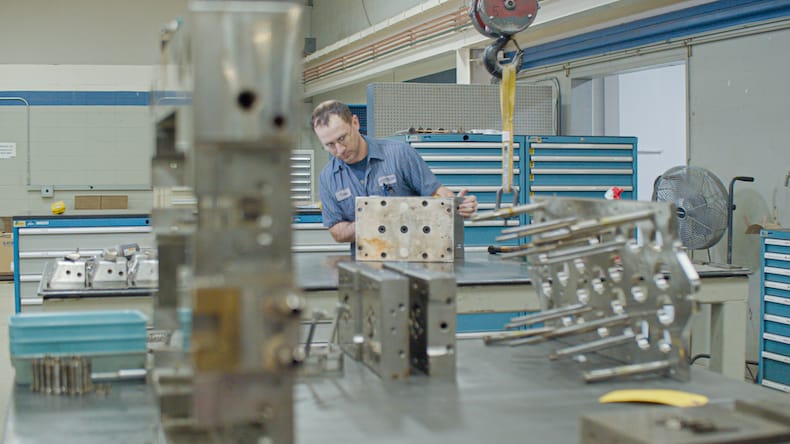
How Concurrent Design Review Aligns Injection Molding Tooling and Parts [VIDEO]
Tool design is an essential and sometimes underestimated part of injection molding…
READ MORE