How Design for Manufacturability (DfM) Factors Into Project Success
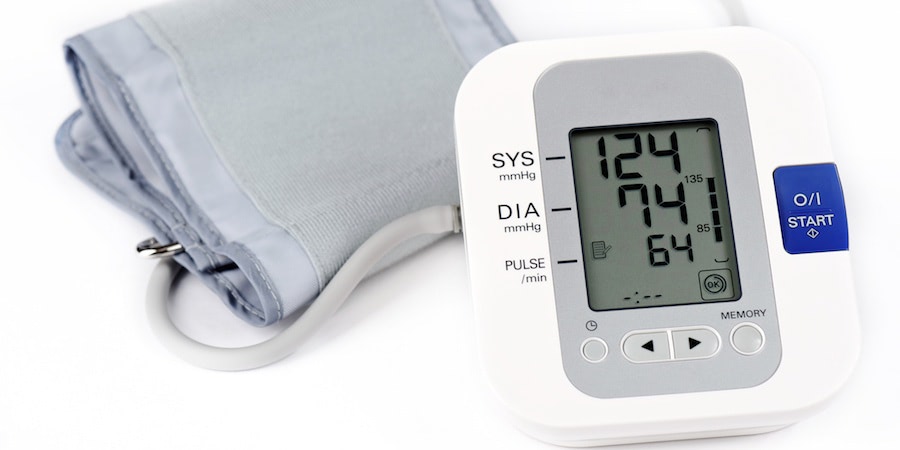
Almost any reasonable design looks good on paper or even as a prototype, but that doesn’t mean it’s a sure thing when it comes to manufacturing it. On the other hand, using Design for Manufacturability (DfM) to improve part design, injection molding processes and material selection ensures a product or component can be manufactured in a streamlined, efficient, validated, and repeatable way — saving time and money.
Quite simply, “part design with manufacturing in mind” will determine the success or failure of an injection molding project. Leveraging every aspect of DfM is key.
Aligning the Teams
First things first. Get the customer design team and the injection-molding engineering team together to discuss the project, including intended end use and lifecycle expectations. Decisions made during these design meetings typically account for about three-quarters of the total final cost of the part or product, so a lot of money is on the line. Having the teams collaboratively focus on the end goal — manufacturability — should always be a top priority when designing parts and tooling, as is knowing which methodologies to employ, and when. For example, feasibility reviews early in development can prevent costly tooling errors and subsequent production delays.
Identifying and Overcoming Design Challenges
Part design and tool design are dependent on each other and thus should be done concurrently, ideally in the earliest design stages. With DfM, the cross-functional engineering team is involved up front to provide a realistic manufacturing perspective on product design, tolerances, mold component functionality, mold materials, tool design, material performance, operational constraints, and associated costs. Of particular importance is:
- Finding any potential problems in part geometry or tolerances that might result in poor steel conditions or require special tooling features such as lifters, slides, and threading/unthreading.
- Evaluating the physical and chemical properties of the selected resin so the proper mold steel is used and appropriate mold cooling is verified.
- Conducting mold flow analysis to determine the best type of gate and gate locations, as well as proper vent locations.
Taking these steps up front is the best way to eliminate wasted effort and rework, which adds significant cost to the tooling budget. Further, confirmation of standard plastic design practices, incorporation of tooling details and running a comprehensive process failure mode effects analysis (PFMEA) creates the most robust design possible.
DfM Outcomes
Designing a product with manufacturability in mind is a cost-effective way to reach desired outcomes by managing these goals at the outset of the injection molding process:
-
Eliminate or replace unusual parts or specifications that add complexity, and/or combine steps to increase manufacturability
- Consider aspects of the tool design when designing the part (such as keeping knit lines and end-of-fill locations in mind when choosing gate locations)
-
Verify material supplier recommendations for selected resins
- Design parts to minimize secondary operations, such as assembly or finishing
-
Design parts with nominal wall thickness whenever possible, and gate into the thickest wall section of the part with a gate designed for minimal to no trimming
-
Design parts with adequate draft for proper release from the mold without the use of mold release agent, and also incorporate generous radii at part geometry intersections to enhance melt flow and reduce stress
-
Once a reasonable design has been created, complete a mold flow analysis, including melt flow, warp cooling pressures, knits, etc., to ensure moldability and manufacturability are streamlined, efficient, validated, and repeatable
Working with an injection molder with expertise in DfM, like Kaysun, allows for design scrutiny and production efficiencies that ultimately help OEMs balance project cost and profitability. Click the button below to learn about key critical-use plastic part design considerations to make to ensure the success of your next project!
Subscribe
TO OUR BLOG
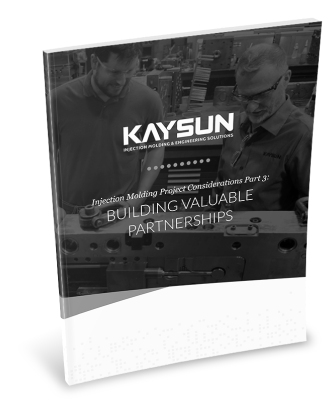
How Do Injection Molder Partnerships Influence Project Costs?
You Might Also Like...
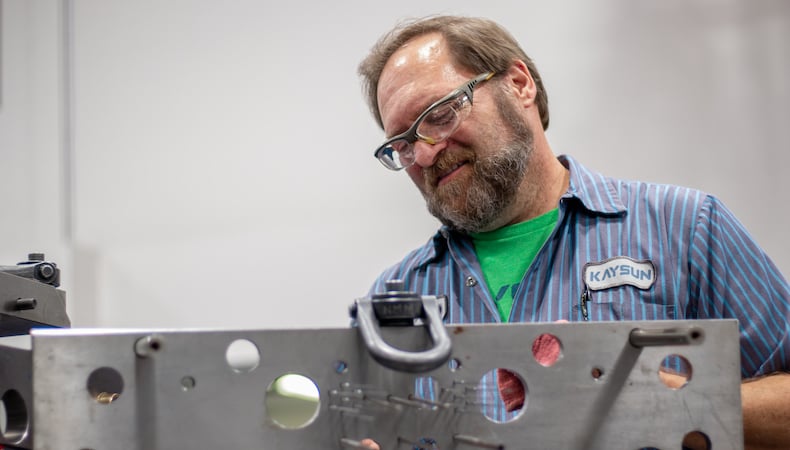
Injection Molding Quotes: 5 Tips to Help Get Tooling Right
Few things impact injection-molded part quality as much as tooling design, materia…
READ MORE
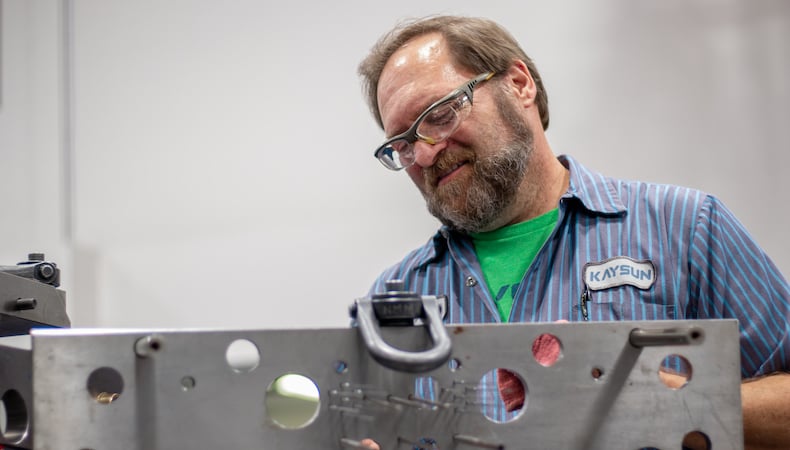
Tooling Audits & Evaluations: How Molders Help OEMs Gauge Health of Assets
When an OEM pursues an injection molding program, tooling is among the most highly…
READ MORE
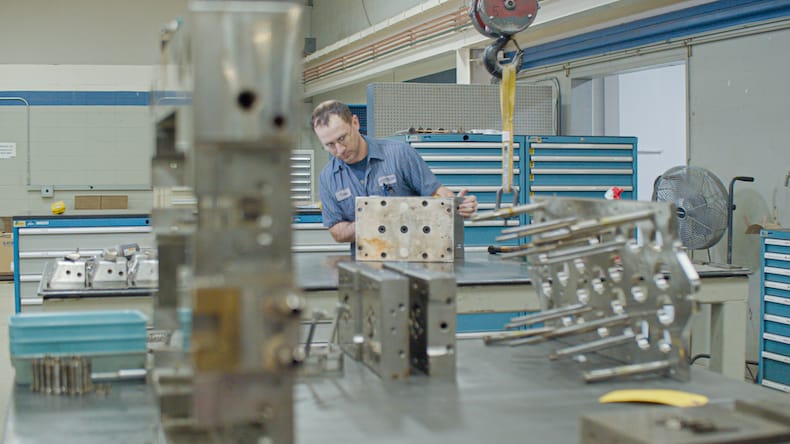
How Concurrent Design Review Aligns Injection Molding Tooling and Parts [VIDEO]
Tool design is an essential and sometimes underestimated part of injection molding…
READ MORE