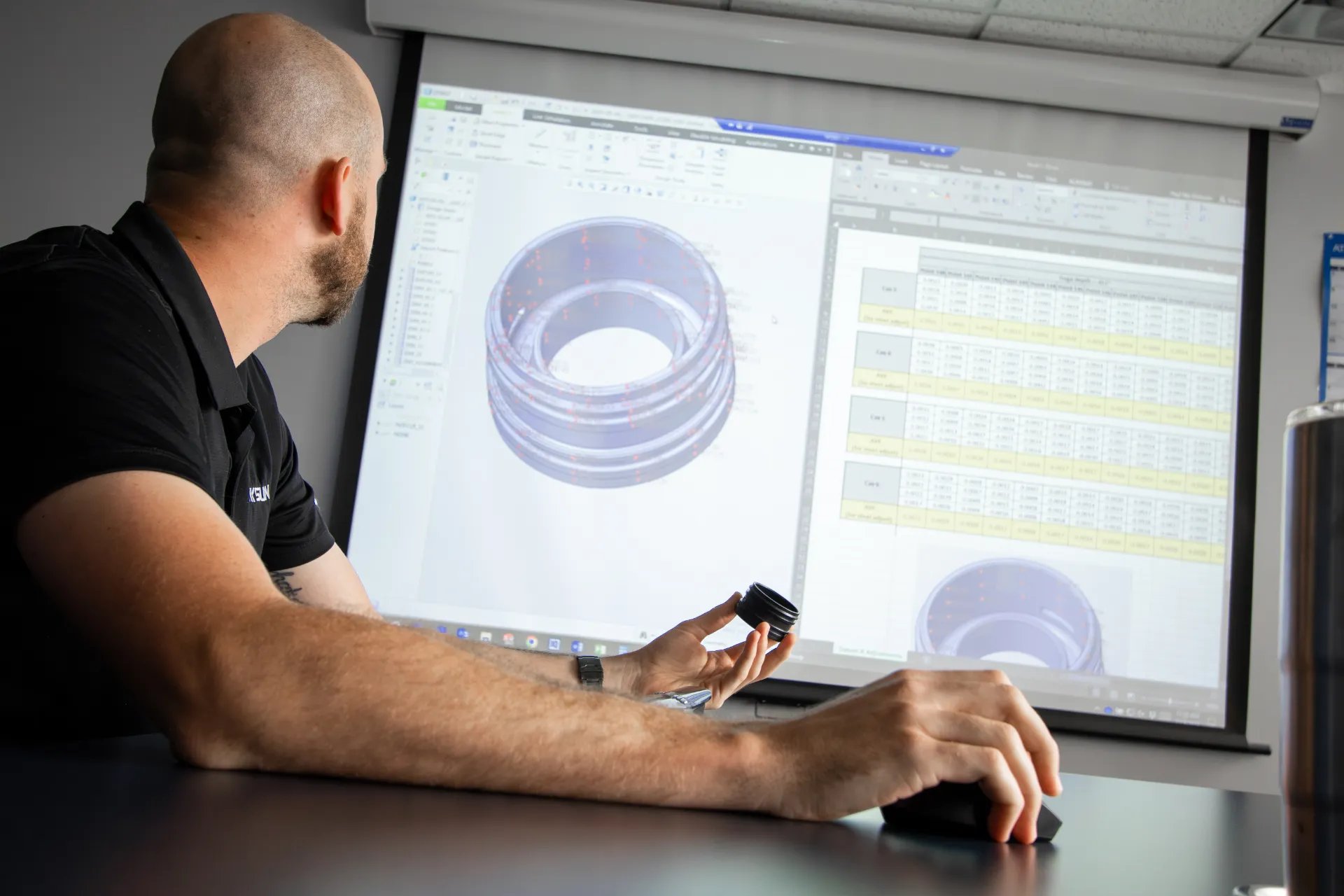
Design for Manufacturability (DfM) Analysis
Involving an injection molder upfront in the design phase provides valuable opportunities for input on standard or custom plastic parts. Kaysun’s engineering and manufacturing teams work with customers to guide design choices that support part innovation, functionality, and performance in combination with the best materials and processes to maximize manufacturability.
Design for Manufacturability (DfM) — also known as Design for Manufacturing — is the process of consciously and proactively designing products to optimize all facets of manufacturing, including injection molding. DfM aligns engineering and production so potential problems can be identified and resolved before they result in costly rework.
Injection molding DfM analysis arms specially trained engineers with project insights that save manufacturers time and money by identifying:
Potential part moldability issues and solutions during the design phase
Part design modifications to simplify tooling
Opportunities to make appropriate materials substitutions to enhance part quality and/or reduce costs while meeting cosmetic specifications
Production efficiencies that improve processes and part quality
Cost efficiencies that lower per-part prices
The Benefits of DfM Analysis
The value of DfM analysis lies in the focus placed on finding practical solutions to project impediments that could jeopardize successful outcomes. DfM analysis defines opportunities for reducing costs, improving manufacturability, and increasing speed to market.
Leveraging DfM Analysis
Key professionals find DfM analysis to be a powerful tool in better understanding their project.
Design Engineers — particularly those less well-versed in manufacturing processes — use it to evaluate new product designs from a plastics manufacturability standpoint. DfM analysis also serves as a touchpoint for further project collaboration with Kaysun engineers.
Conducting DfM Analysis
In conjunction with design review, trained DfM engineers evaluate how the part is intended to interact with the mold. Mold simulation software is used to assess the process and pinpoint potential risk (poor cooling, extended molding cycles, warping). Based on this data, design solutions are developed that include gate locations, parting lines and other factors that influence part functionality and aesthetics.
Implementing DfM Analysis
A finalized part design is not required for DfM analysis. In fact, introducing DfM analysis before a project nears completion is ideal since there’s flexibility to make any necessary changes, either to the design or sourcing.
The only required project information is:
- A 3D CAD file
- Type(s) of part material
- Cosmetic/aesthetic needs
- Preferred gate location(s)
- A general overview of intended part functionality
Kaysun: The Ideal Partner for DfM Analysis
Kaysun is an industry leader in DfM analysis. Our team’s engineering and manufacturing experience allows for the accurate prediction of the processes necessary to achieve a successful new part design. Drawing from that deep knowledge base, we engage professionals from across engineering, tooling and processing disciplines for a full team approach to aligning our expertise with your needs.
Kaysun is fully dedicated to collaborative partnerships with our customers.
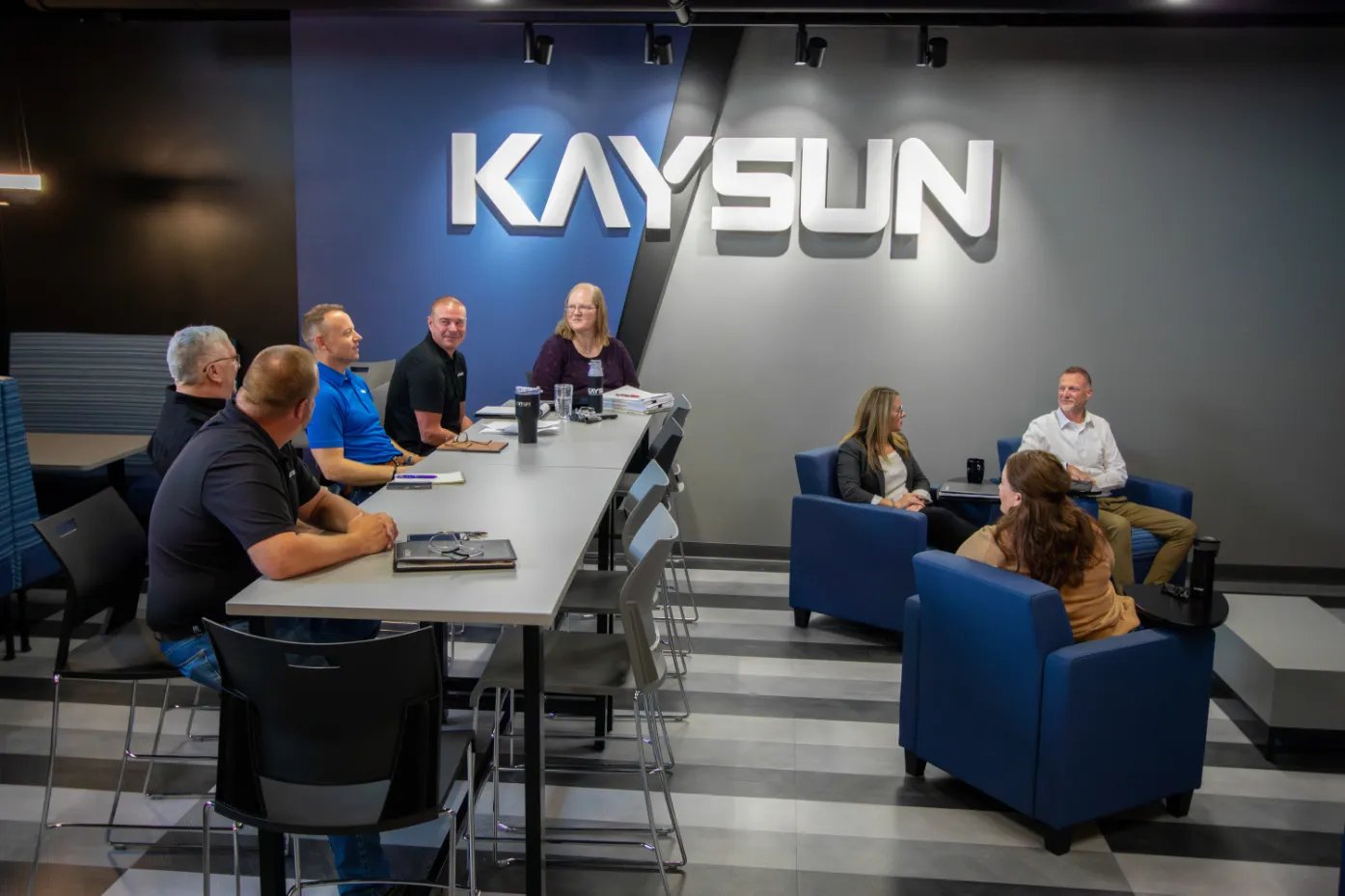
Does your company fit our ideal customer profile?
Complete the form to request a free consultation with our plastic engineering experts.