Featured Blogs
Kaysun and Sodick: A Partnership Built on Precision, Proven by Performance
Kaysun and Sodick: A Partnership Built on Precision, Proven by Performance
Precision presses are central to producing injection-molded parts for complex applications in medical, automotive, and other hig…
READ MORE
Stryker Turns to Kaysun for Steri-Shield® 8 Helmet Solution
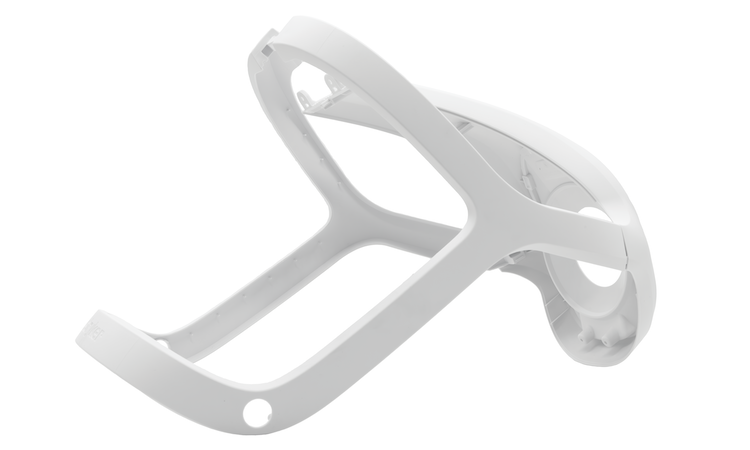
Stryker Turns to Kaysun for Steri-Shield® 8 Helmet Solution
READ MORE
A Reshoring Roadmap for OEMs Facing Tariff Pressures & Challenges
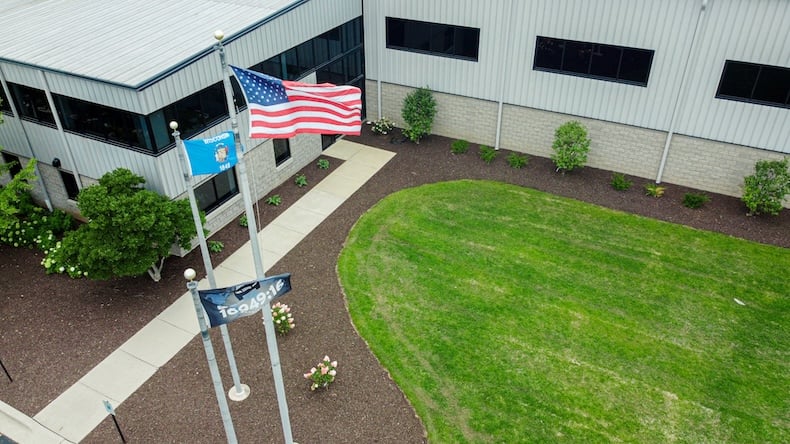
A Reshoring Roadmap for OEMs Facing Tariff Pressures & Challenges
READ MORE
Kaysun Integrates AI on the Production Floor with RJG CoPilot
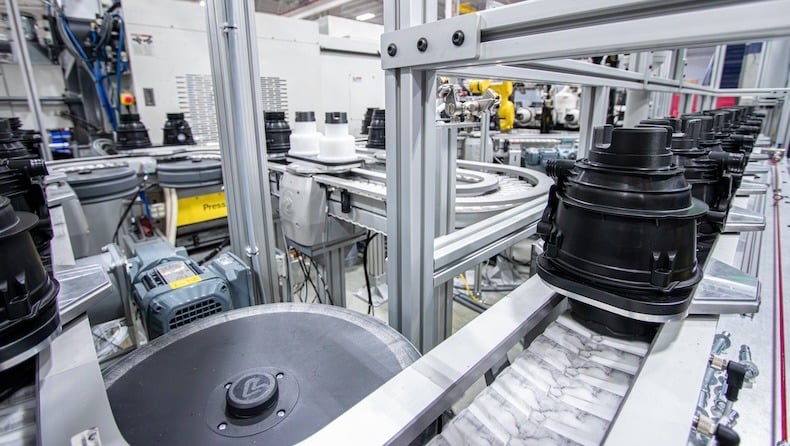
Kaysun Integrates AI on the Production Floor with RJG CoPilot
READ MORE
Browse All Kaysun Articles
Injection Molding Quotes: 5 Tips to Help Get Tooling Right
Injection Molding Quotes: 5 Tips to Help Get Tooling Right
Few things impact injection-molded part quality as much as tooling design, materials…
READ MORE
4 Ways Reshoring Remains A Win for American Manufacturing
4 Ways Reshoring Remains A Win for American Manufacturing
International trade tensions have brought heightened awareness to reshoring. Recent …
READ MORE
Top 3 Custom Injection Molding Trends to Watch in 2025
Top 3 Custom Injection Molding Trends to Watch in 2025
Despite being considered more energy efficient and producing less waste than other m…
READ MORE
How Kaysun’s Culture of Sustainability Benefits OEMs and The Planet
How Kaysun’s Culture of Sustainability Benefits OEMs and The Planet
Injection-molded parts and products are staples for OEMs in industries ranging from …
READ MORE
The Impact of Non-Uniform Injection Molding Wall Thickness
The Impact of Non-Uniform Injection Molding Wall Thickness
Shrink rates for plastic parts vary depending on the materials used and the uniformi…
READ MORE
12 Common Injection Molding Questions — Answered!
12 Common Injection Molding Questions — Answered!
Injection molding is a versatile and precise process, making it ideal for OEMs that …
READ MORE