Scientific Molding: The Key to Quality, Consistency and Profitability
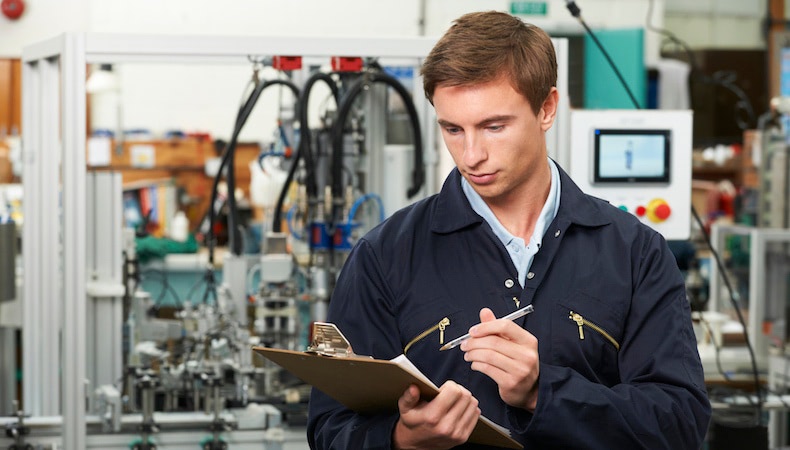
In this age of global competitiveness and tough regulation, superior quality is the name of the game in differentiating you from competitors and increasing your market share.
OEMs in various industries are designing increasingly complex components, products and devices with higher injection molding tolerances that must meet stringent quality standards, regulatory compliance and cost-effectiveness. This can be achieved through scientific molding, the best designed and controlled manufacturing process possible.
Why Scientific Molding?
While standard "trial and error" molding is sufficient for simple parts and products like food storage containers and toys, more manufacturers want scientific molding because it gives them a competitive advantage in the marketplace when it comes to critical-use, complex parts and devices or precision-molded plastic parts.
Scientific molding relies on material science and precise measurement to completely understand, down to the molecular level, what’s happening during every stage of the injection molding process. By fully understanding how all the different parameters interact in detail, high precision across multiple production runs can be maintained. Because all the data is recorded, it is easy to replicate the manufacturing process as needed—even when production is transferred from one machine to another—saving a tremendous amount of setup time.
The Role of Design for Manufacturability
An essential part of scientific molding is Design for Manufacturability (DfM) wherein engineers develop a hypothesis about the best design and process, test it, refine it and perfect it until the results are reproducible many times. Based on the design, a tightly controlled and repeatable manufacturing process is implemented for consistent production of defect-free parts. Sophisticated software and sensors are used to collect data that documents every phase of the manufacturing process: design and building of the tool, debugging of the tool, material selection, and the injection-molding process.
Engineering for Peak Efficiency
Highly-trained engineers know how to use scientific molding data—they understand exactly what is happening with the material inside the mold at every step of the process; they know how small changes in pressure, temperature, and flow rate impact quality of the final product. By recording data when the machine is producing at peak efficiency (top productivity with minimal scrap), engineers create a template by which process parameters can be replicated, or easily adjusted in real time if deviations are identified.
Scientific molding engineers are often specialized in a particular phase of product development: tool design and construction, molding production, and process conformation, for example. They have deep knowledge of how all the process variables react in certain ways according to temperature, pressure, material flow rate, material chemistry, cooling time and rate, material moisture rate, fill time, and mold conductivity. Cooling time, for example, is influenced by the heat level in the material, the conductivity of the tool steel and the geometry of the part. Since engineers have been trained to consider everything from the perspective of the plastic, they know exactly how to manipulate the variables back to peak efficiency.
Control Testing and Monitoring
Even the slight fluctuations can result in scrap, so control is incredibly important. Engineers monitor process parameters according to the “peak” template with ongoing quality testing and inspection. Some testing and monitoring tools used during tool development and production include rheology curves (or viscosity curves), velocity profiling, cavity pressure readings, and gate seal (or gate freeze) studies.
Successful scientific molding requires engineers possess deep knowledge, experience, analytical skills, and access to the highest-quality equipment and tools. Through their expert analysis and interpretation of the collected scientific molding process data, engineers can design and document a robust and repeatable process that delivers high quality, compliant and defect-free parts in less time at lower cost—maximizing profits and speeding time to market for a sustained competitive advantage.
For more information on achieving precision, tight tolerances and repeatable top quality, read Scientific Molding: A Manufacturer's Guide. Click the button below to download your free copy:
Subscribe
TO OUR BLOG
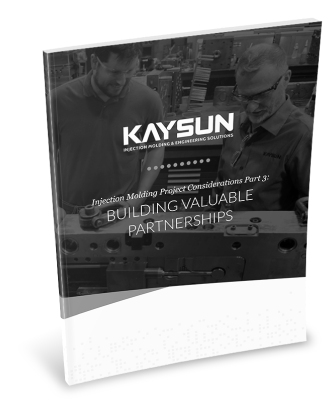
How Do Injection Molder Partnerships Influence Project Costs?
You Might Also Like...
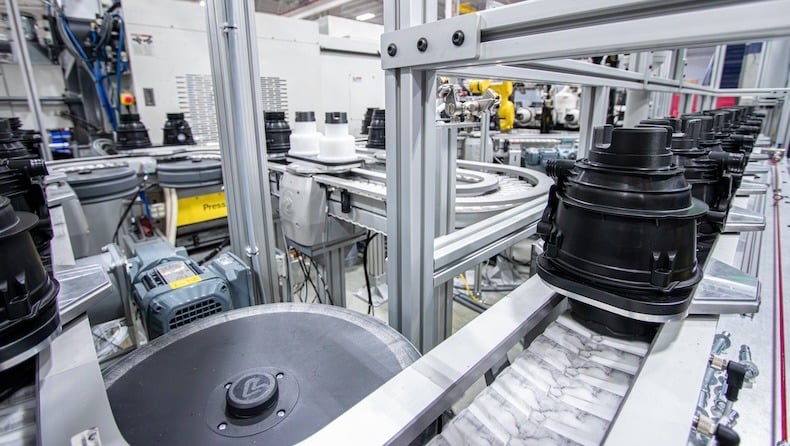
Kaysun Integrates AI on the Production Floor with RJG CoPilot
Industry 4.0 has made manufacturing more dynamic than ever before. Merging IoT, AI…
READ MORE
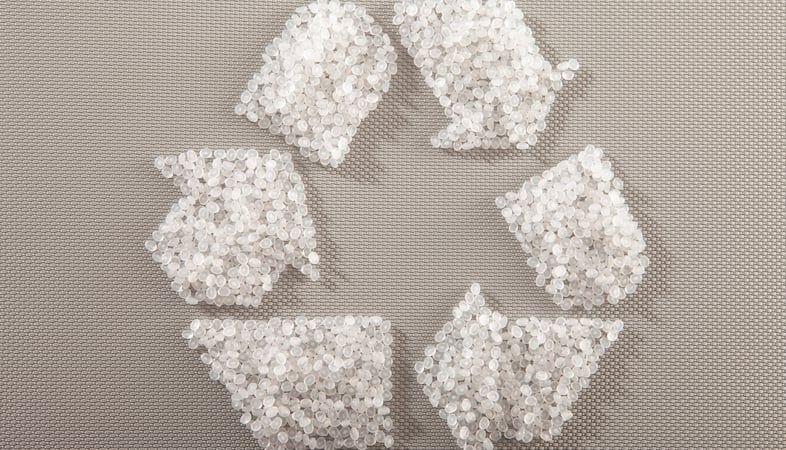
How Kaysun’s Culture of Sustainability Benefits OEMs and The Planet
Injection-molded parts and products are staples for OEMs in industries ranging fro…
READ MORE
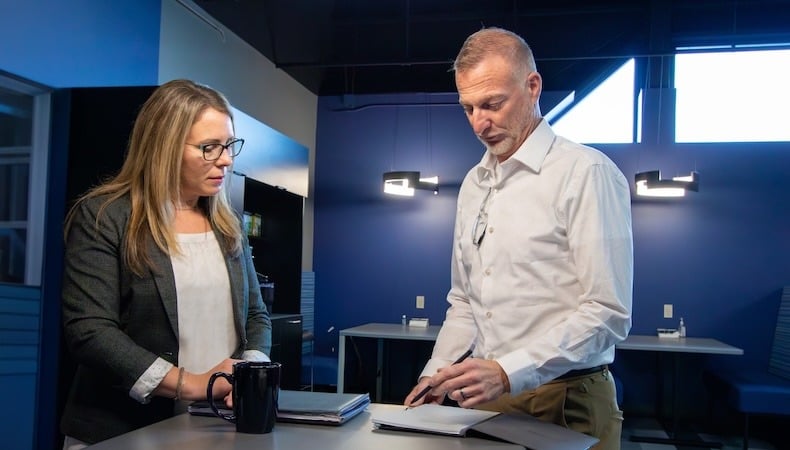
12 Common Injection Molding Questions — Answered!
Injection molding is a versatile and precise process, making it ideal for OEMs tha…
READ MORE