7 High-Priority Design Considerations for Injection Molded Parts
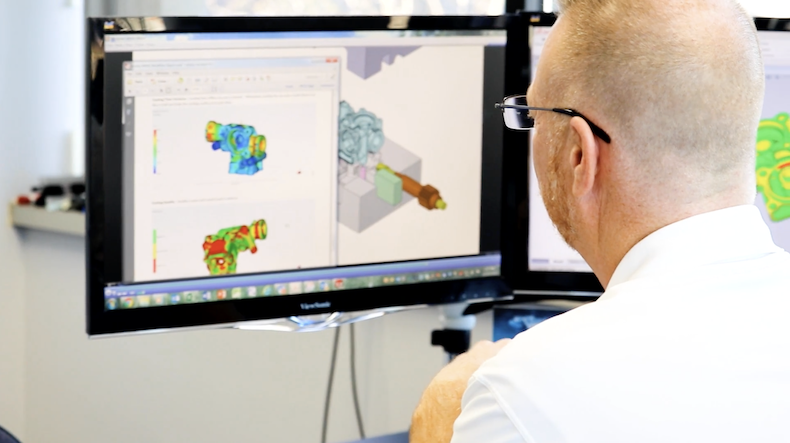
The design of injection molded parts can be incredibly complex. Sometimes, it’s a byproduct of what’s needed for the application; other times, it could be a result of over- or under-thinking what needs to be accomplished.
Working with a custom injection molder that relies on Design for Manufacturability (DfM) practices to establish realistic design goals and production expectations is a significant advantage. However, there are certain design considerations for injection molded parts an OEM can contemplate — and correct, if needed — before collaborating with a molding partner and their DfM team.
What signals design-related failure?
Defective designs result in defective parts. How defects manifest varies from part to part, but the trained eye of an experienced injection molder can detect four common design-related failures, specifically:
- Environmental stress cracking (ESC) triggered by application of the threshold concentration of a particular chemical and a threshold stress to plastic. The resulting molded-in stress, press-fit stress, high stress at sharp corners, or stress from part usage cause cracks and breakage
- Ultraviolet (UV) light degradation generates photochemical processes and oxidation that weaken electrochemical bonds and part integrity over time. UV degradation typically starts as a surface defect due to improper photon penetration into the plastic. Once surface cracks appear, they quickly spread to the part’s interior, causing it to fail
- Cycle fatigue occurs when plastic is bent back and forth at a hingepoint. If the hinge is molecularly misaligned, the joint’s bonds are fundamentally weakened and poor resistance to bending causes breakage. Likewise, in the case of high-frequency bending, heat build-up within the plastic isn’t dissipated and the part fails due to high temperature
- Viscous-related creep and stress relaxation are brought about by subjecting plastic molecules to sustained loads. Depending on the plastic, it either springs back into its original shape after being released from a short-term load (as in thermoplastics and other visolastic resins), or molecules slowly start to flow under the stress of a long-term load, causing viscous creep that never recovers the original shape
Design elements that impact injection molded part quality
While these examples are common, they aren’t the only design-related failures that could happen. Mitigating failure risk is essential and requires careful consideration of certain design elements.
1. Plastics selection
Selecting plastics isn’t an arbitrary design decision. The quality, performance, and cost of injection molded parts hang in the balance. It's essential to work with an injection molder that can narrow down the 25,000+ choices to the best plastics options for strength, durability, chemical resistance, appearance, and other part-specific requirements.
2. Features moldability
Sharp edges and corners, undercuts, shutoff angles, and other features need to be carefully assessed during design. At times they may be unavoidable, which then requires expert engineering and input from an experienced injection molding partner. Otherwise, if reasonable design adjustments can be made to arrive at the same result — perhaps rounding an edge or eliminating a snap-fit — do it. There will be less stress on the materials and parts during production, fewer tooling concerns, consistent moldability, and a higher overall success rate.
3. Tolerance feasibility
Overcompensating on tolerance requirements in design to ensure part reliability is a common practice among product engineers, but it isn’t necessarily realistic. Tight tolerances and other stringent parameters may be unachievable using the proposed injection-molding plastic. Or, the elevated level of design requirements could simply be unnecessary for a successful part. Infeasible tolerances typically don’t add to design or part reliability — but they can quickly add to the cost of production.
4. Draft angles
The taper of the injection-mold part surface and the direction of pull must align, or the part may be damaged upon removal from the tool. Wall thickness, shrink rate, and the need for surface texturing all impact draft orientation decisions. In turn, how draft angles are handled can impact tool design, parting line and ejector pin placement, component interrelationship, performance, and cost.
5. Wall thickness
Wall thickness uniformity is a critical aspect of part design. Without it, internal stresses could build and ultimately cause failure in production or use. Variations in wall thickness could also interfere with cooling rates, increasing the potential for warping, sink marks, and voids.
6. Gating
As the tool’s injection entry point for molten plastic, gating impacts several aspects of the design of injection molded parts. The size, type, and location of the gate determine part packaging, gate removal, component aesthetics, part dimensions, and degree of warping. However, gates aren’t a one-size-fits-all solution. Their size and shape vary depending on the plastic being molded, and the size of the part. Mismatching gate and part sizes may result in a visually pleasing design, but there could be consequences. For example, using smaller gates on larger parts may inhibit plastic flow, lengthen molding time, imbalance fill pressures, and compromise part integrity.
7. Secondary operations
The cost and technical aspects of required secondary operations need to be accounted for upfront during part design. Injection molders with comprehensive in-house value-added services will often be proactive in leading discussions, collaboration, and coordination of needed secondary operations. The resulting seamlessness of keeping secondary operations with one vendor provides better quality control and outcomes.
Getting well-designed, reliable injection molded parts to market is a win for OEMs in any industry. Working with an experienced injection molding partner provides another layer of expertise and consistency.
Explore how a molder’s guidance in managing time, budgets, and outcomes can translate to competitive advantage when you use the Injection-Molded Part Quality Control Checklist.
Subscribe
TO OUR BLOG
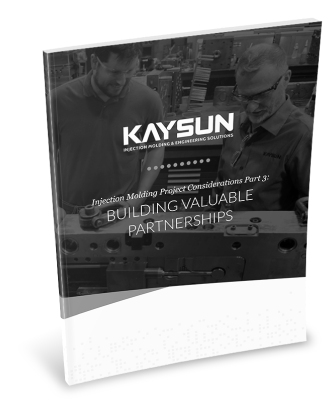
How Do Injection Molder Partnerships Influence Project Costs?
You Might Also Like...
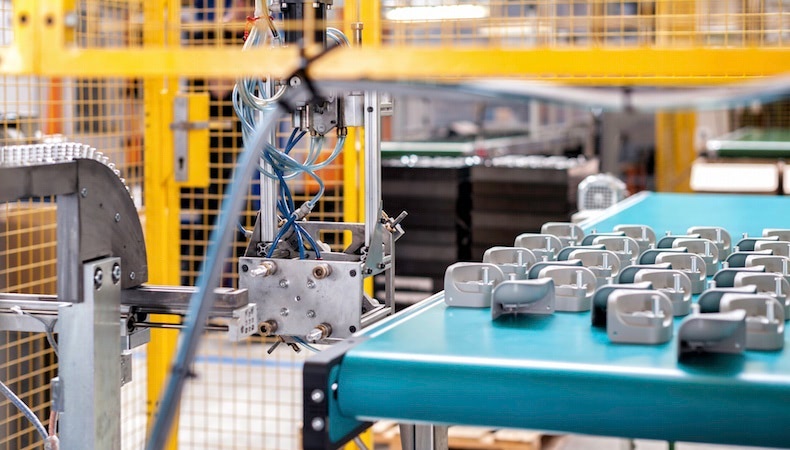
The Impact of Non-Uniform Injection Molding Wall Thickness
Shrink rates for plastic parts vary depending on the materials used and the unifor…
READ MORE
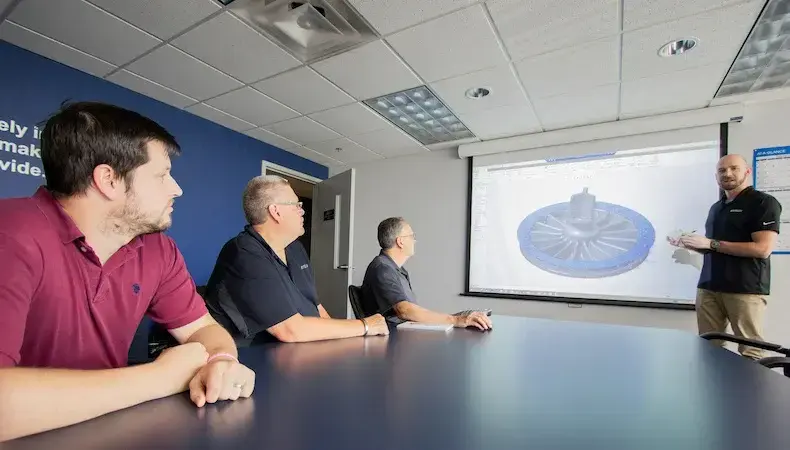
5 Engineering Factors That Improve Your Injection Molding Project
In many complex industries, decisions about which injection molder to use for cust…
READ MORE
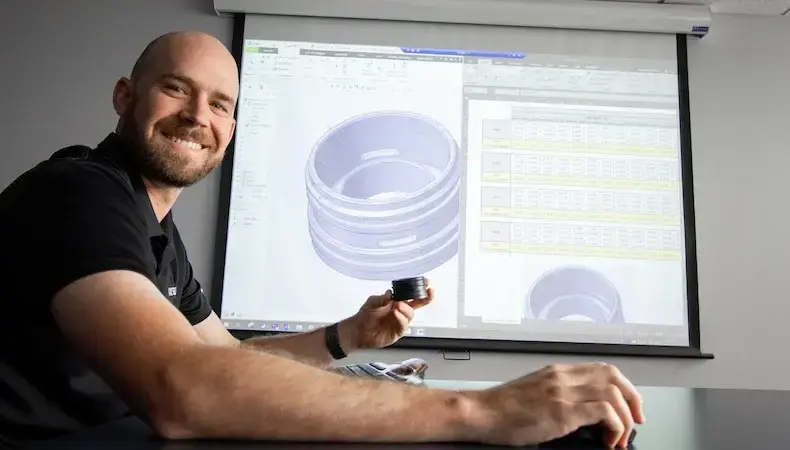
Why Continuing Plastic Engineering Education Matters to OEMs
Technologies, product needs, and customer expectations are rapidly advancing. OEMs…
READ MORE