How Forecasting and Mapping Benefit Injection Molding Supply Chain Management
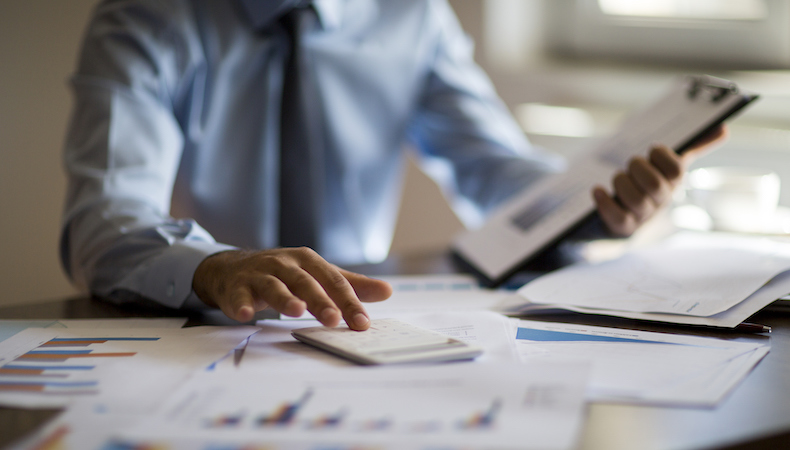
In a perfect world, supply chain management is cost effective and seamless. Materials, inventories, services, production, and distribution flow as anticipated with minimal difficulty.
It’s been a far from perfect world since 2020.
Global supply chain disruptions have altered the course of business in all industries. Plastics is certainly no exception. The resin shortage continues to dictate aspects of injection molding supply and demand. Manufacturers are left to deal with the aftermath of force majeure, raw materials unavailability, prolonged lead times, and escalating costs.
Are the benefits of supply chain management systems part of the pre-COVID past? Or, can keying in on supply chain transparency empower manufacturers and their injection molding partners to jointly navigate the plastic resin shortage and supply chain limitations?
Seeing the Future: Supply Chain Forecasting
Forecasting drives strategy in effective supply chain management. It revolves around analyzing internal data and external factors such as market trends and resin prices to determine future needs, planning, ordering, and budgeting.
However, the plastics industry and manufacturers who rely on it know how easily the unanticipated can upend forecasting strategies, especially when two devastating events converge. The global pandemic and an anomalous winter storm in the southern U.S. both contributed to the plastic shortage and the ensuing fallout still felt across the industry.
While forecasting metrics in place at the time of the events may have been negated, it doesn’t negate the importance of forecasting. It remains a vital component for managing supply chain sourcing, time lines, materials, inventories, and costs.
Routing Progress: Supply Chain Mapping
Supply chain maps are invaluable tools for heading off setbacks. Simply put, knowing detailed information about your materials vendors improves overall supply chain visibility. Being able to see the potential risks posed by vendor relationships — quality control issues, responsible sourcing breaches, weather-related delays, etc. — gives you the ability to take action to minimize adverse impacts.
Mapping the supply chain also provides insight into how well your vendors are positioned with their vendors to ensure continuity in customer service. Again, it’s about the details. The more you know the better able you are to manage customer demand, expectations and, ultimately, any competitive advantage.
Walking the Talk: Transparent Communication and Project Success
Supply chain forecasting and supply chain mapping increase visibility, which is beneficial for manufacturers. But, what makes the insights actionable? Transparent communication.
During unpredictable times, an injection molder that encourages collaboration and doesn’t shy away from honest discussions about your situation is an asset.
Kaysun has leaned into the sometimes uncomfortable conversations and emerged as a true strategic partner for manufacturers. However, our short- and long-term resin shortage strategies aren’t just talk. They pinpoint the collaborative value of a molder that can source, qualify, and test alternative materials as well as access global supply to help you manage costs and make fast, informed decisions.
Undoubtedly, there is a lot that is out of the direct control of injection molders and OEMs as the plastics industry continues to sort itself out. However, you can take a step toward managing what you can by reading our white paper, Supply Chain Mapping for Injection Molding Project Success. Click the button below to download your copy now.
Subscribe
TO OUR BLOG
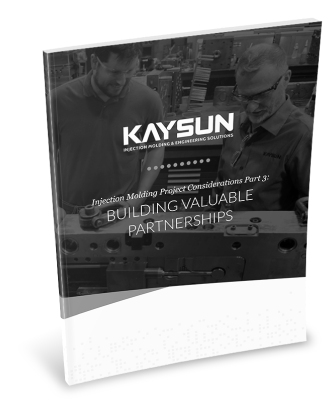
How Do Injection Molder Partnerships Influence Project Costs?
You Might Also Like...
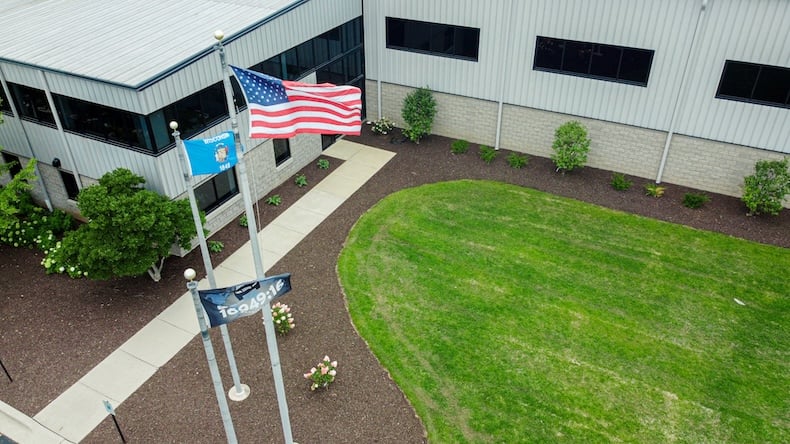
A Reshoring Roadmap for OEMs Facing Tariff Pressures & Challenges
Tariffs, geopolitical uncertainty, global supply chain disruptions, and shifting c…
READ MORE
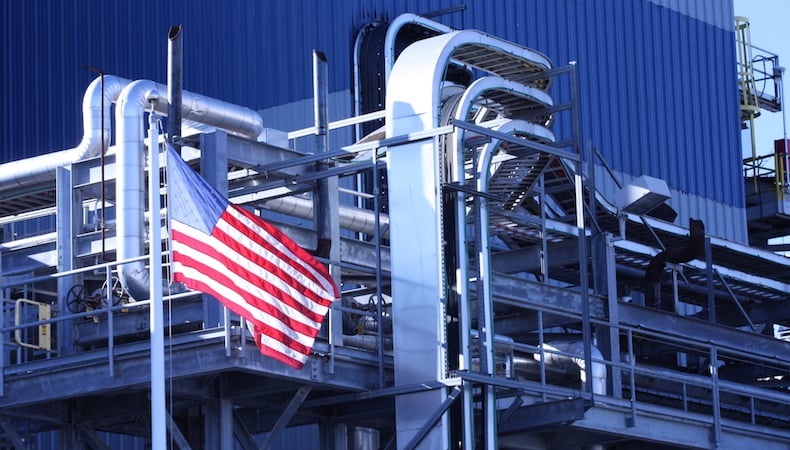
4 Ways Reshoring Remains A Win for American Manufacturing
International trade tensions have brought heightened awareness to reshoring. Recen…
READ MORE
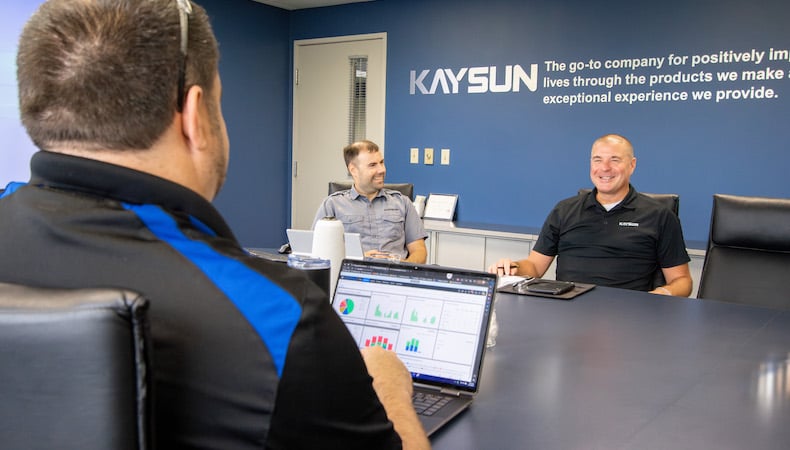
Top 3 Custom Injection Molding Trends to Watch in 2025
Despite being considered more energy efficient and producing less waste than other…
READ MORE