How Injection Molders Help Find Alternatives During the Resin Shortage
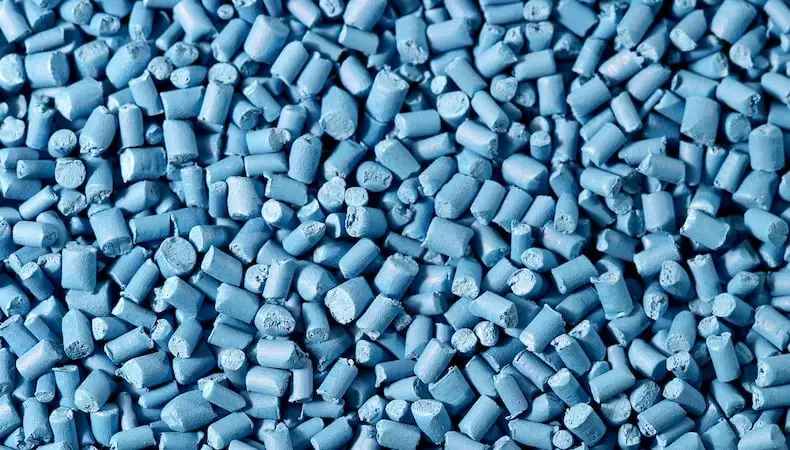
The gaps between raw materials, demand, and delivery continue to define a very uncertain future for the plastics industry. Manufacturers, injection molders, and all others dependent on plastics are understandably at a loss.
Finding solutions generally requires finding replacements for nylon, acetal resins, polysulfone (PSU), polyphthalamide (PPA), polyphenylene sulfide (PPS), polyphenylene oxide (PPO), and syndiotactic polystyrene (SPS) — a task not easily completed in light of the catastrophic resin shortage.
For many manufacturers, the collaborative partnership they have with their injection molder is proving beneficial. Getting the guidance required for appropriate material alternatives directly from experts allows critical decisions to be proactive instead of reactive. Further, injection molders may be able to source similar resin grades from the same supplier — meaning streamlined materials management and potential lead time reductions.
But, simply swapping plastics or resin grades isn’t a surefire solution to the challenges brought about by “Resin Shortage 2021.” Kaysun diligently works with our customers to accurately understand and address burgeoning needs.
Qualification: Protecting Injection-Molded Part Quality
Not surprisingly, manufacturers across industries are reaching out to their injection molding partners to find the most feasible and cost-effective solutions for alternative materials.
A top priority in this pursuit is identifying plastics that behave in ways similar to the original material when in the mold. Tooling is expensive, and modifying it is not ideal for a potentially short-term fix. There’s also the prospect of having to re-modify any tooling to “switch it back” once the originally specified plastic is available — more money and time that no manufacturer can afford to invest in a temporary solution.
That’s where the plastics experts at Kaysun come in. By combining specialized training with sophisticated Design for Manufacturability (DfM) processes, appropriate grades of plastics — typically upgrades from existing materials — are proposed based on properties, behaviors, and performance. Further, these resins align with existing tooling in a majority of cases, making them qualified alternatives for further consideration.
Testing: Determining If Alternative Materials Are Truly Solutions
Having narrowed down a field of more than 25,000 possibilities to those plastics with characteristics that match the application is a value-add in and of itself.
However, having the ability to produce, test, and sample injection-molded parts made from alternative materials adds another layer of assurance to the process.
Kaysun engineers test and approve more than one plastic so they can pivot quickly to another solution in the event a specific material isn’t available or perhaps will not perform as intended without tooling modifications. All findings, approvals, and other testing notes are carefully documented on part prints so the data is readily available.
Failsafe: Implementing A Global Supply Strategy
While there is plenty of speculation about the resin shortage, no one can point to an end date. Some industry authorities point toward current signs of a slow recovery. Others indicate no movement will likely happen until Q1 of 2022.
There’s simply no way of knowing, so a cadence of materials management, optimization, expediting, procurement, and prioritization has emerged to navigate the resin shortage. To that end, Kaysun plays a pivotal role for our customers.
In addition to qualification and testing, we are committed to developing a global supply strategy in collaboration with customers who want to invest in this approach to regional supply disruption mitigation. Simply put, we work with our customers to identify different countries of origin (typically at least one onshore and one offshore plastics supplier) for materials fulfillment. In the event a vendor is unable to fulfill an obligation, a backup is already vetted and ready to step in.
It’s a failsafe option that Kaysun has developed to keep confidence and productivity high, while also managing costs that can easily spiral upwards in a crisis. We believe it is a unique value-add and that our customers deserve the best possible service and outcomes Kaysun can offer.
Finding answers and alternatives in the midst of this unanticipated and highly impactful resin shortage is necessary albeit sometimes difficult. Kaysun is cultivating transparent, collaborative partnerships with our customers to help where and when it’s needed most.
Learn more about the materials and processes we are finding to be versatile and valuable alternatives in our white paper, An Overview for OEMs: High-Temperature & High-Performance Plastics. Click the button below to download your copy now.
Subscribe
TO OUR BLOG
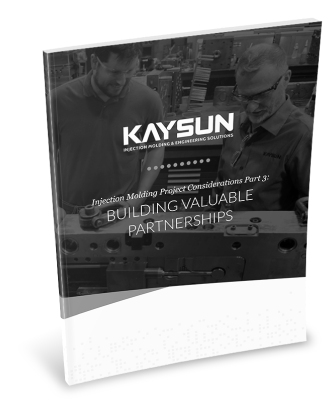
How Do Injection Molder Partnerships Influence Project Costs?
You Might Also Like...
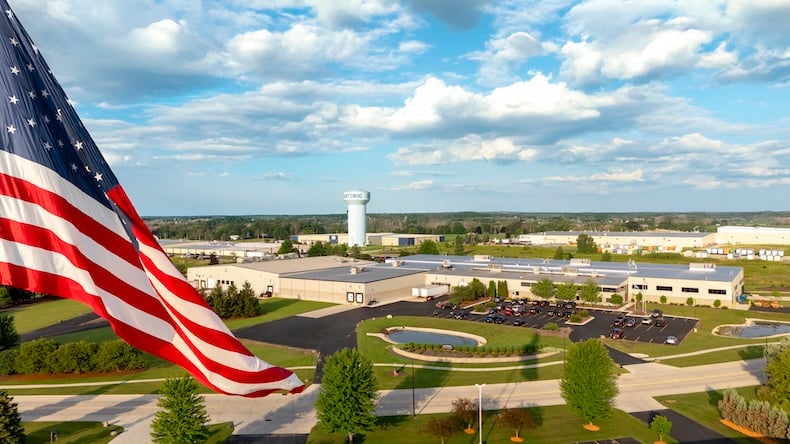
4 Ways Reshoring Strengthens an OEM Supply Chain Strategy
TL; DR (Quick Article Summary) Why is reshoring a smart OEM supply chain strategy?…
READ MORE
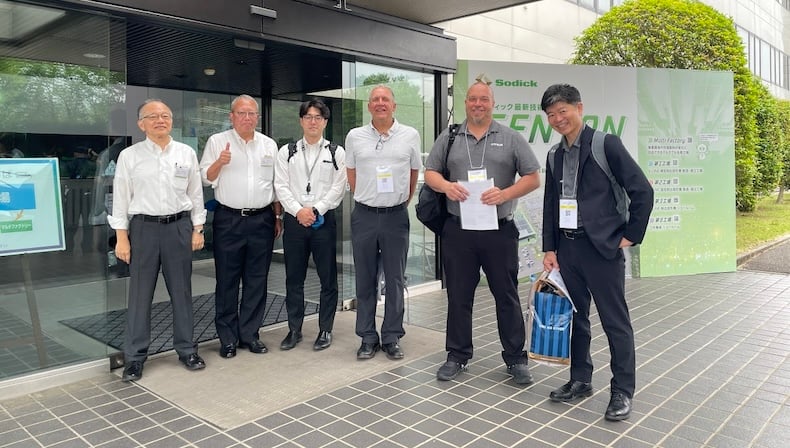
Kaysun and Sodick: A Partnership Built on Precision, Proven by Performance
Precision presses are central to producing injection-molded parts for complex appl…
READ MORE
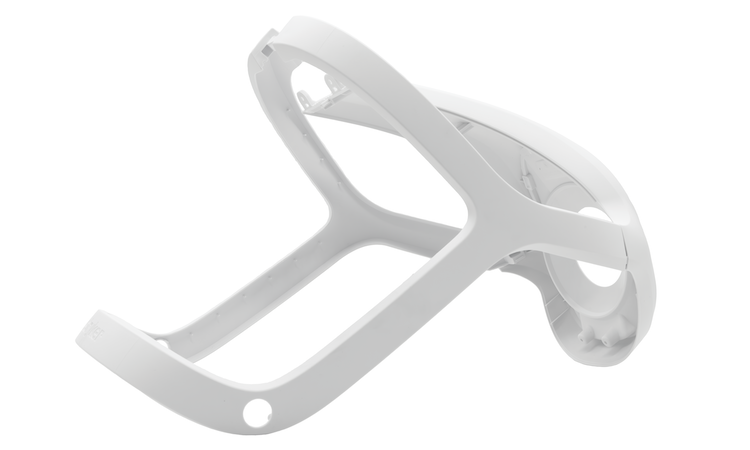
Stryker Turns to Kaysun for Steri-Shield® 8 Helmet Solution
When Stryker set out to develop its next-generation Steri-Shield® 8 Personal Prote…
READ MORE