Overmolding: What it is and What it Means for Products and Profits
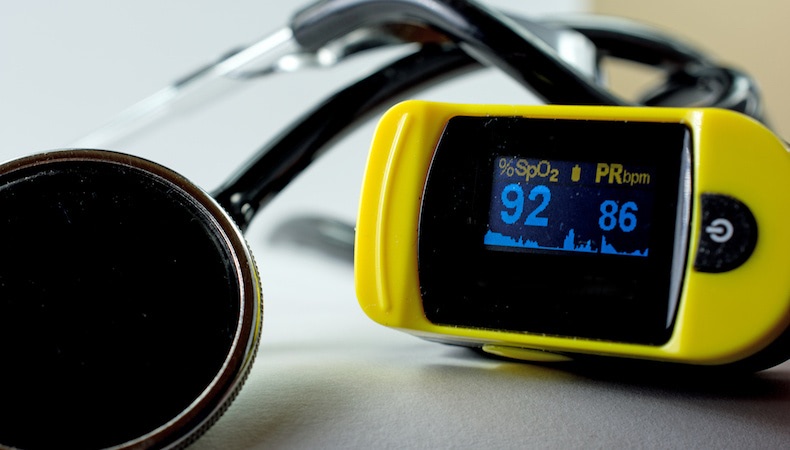
Increasingly popular with manufacturers of consumer products, medical devices, and portable devices, plastic overmolding improves functionality, performance, and aesthetics.
But, what is overmolding? And, more importantly, how can it affect how products are designed and profits achieved?
WHAT IS Overmolding?
Overmolding is a unique custom injection molding process that results in a seamless combination of multiple materials into a single part or product.
It typically includes a rigid, plastic-base component overlaid with a thin, pliable, rubber-like thermoplastic elastomer (TPE) exterior layer or other materials using either a single-shot (insert molding) or two-shot (multiple-shot molding) technique.
The plastic overmolding process may be a great option for your next project after you consider the significant advantages it provides.
What's Possible with PLASTIC Overmolding?
- Add a soft-touch exterior to products
- Enhance grip or “feel”
- Provide a stylish appearance that’s attractive to consumers
- Reduce shock and vibration
- Dampen sound
- Provide electrical insulation
- Improve chemical/UV resistance
- Increase product longevity
Overmolding plastic also lowers production costs as it improves product viability and customer satisfaction. It’s easy to see why manufacturers are so drawn to overmolding.
OVERMOLDING FUNDAMENTALS FOR OEMS
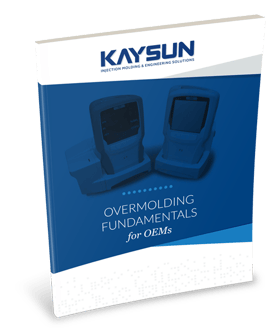
Have you considered how overmolding can further improve product design, performance, and aesthetics?
A Closer Look at Overmolding's Advantages
Better ProduCt Performance
A primary reason to design and manufacture a plastic overmolded product or part is improved product performance.
As mentioned earlier, TPE is an ideal material for creating a soft, non-slip grip. This is especially useful for products requiring tactile sensitivity, such as medical products, surgical instruments, and other handheld devices.
Plus, a TPE surface acts as an environmental barrier, protecting a product and extending its life by reducing shock, vibration, and noise — all key benefits of the overmolding process.
Increased Shelf Appeal
Overmolding helps a product stand out from the competition. TPE not only creates a visually attractive surface, it comes in a wide range of colors and can be engineered for different finishes.
Imagine a clear TPE surface carrying a corporate logo, message, or operation instructions. These can also be overmolded on patterned or customized substrates.
Lower Production Costs
Overmolding is a rare process that adds advantages in several ways (see list above) and also lowers production costs. How? Overmolding reduces the number of manufacturing steps needed.
In the automotive market, for example, overmolding eliminates the need for injection molding and assembly for components (such as gaskets or bumpers), as well as secondary finishing operations (priming, painting, or coating).
Is Overmolding Right for Your Project?
Overmolding plastic is appropriate for so many applications. Yet, several factors must be considered before determining if it’s the best solution for your project:
- Product design
- Materials selection
- Injection molding tooling quotes and equipment budgets
- Labor costs
- Production volume
From selecting materials to handling high volumes to producing high-quality parts, the overmolding process requires special skills and experience.
Partnering with an experienced custom injection molder — especially one with scientific molding expertise, such as Kaysun — helps you navigate the pros and cons of using overmolding on your project. The right partner collaboratively guides you to the best decision for your application and bottom line.
Learn more about how overmolding improves performance while lowering production costs by reading our Overmolding Fundamentals white paper. Click the button below to get your free copy today
Subscribe
TO OUR BLOG
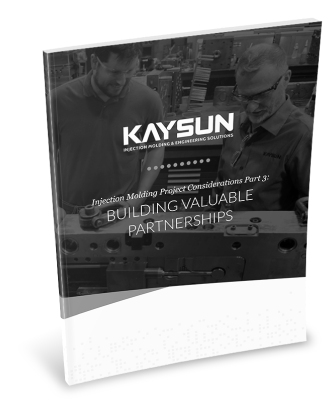
How Do Injection Molder Partnerships Influence Project Costs?
You Might Also Like...
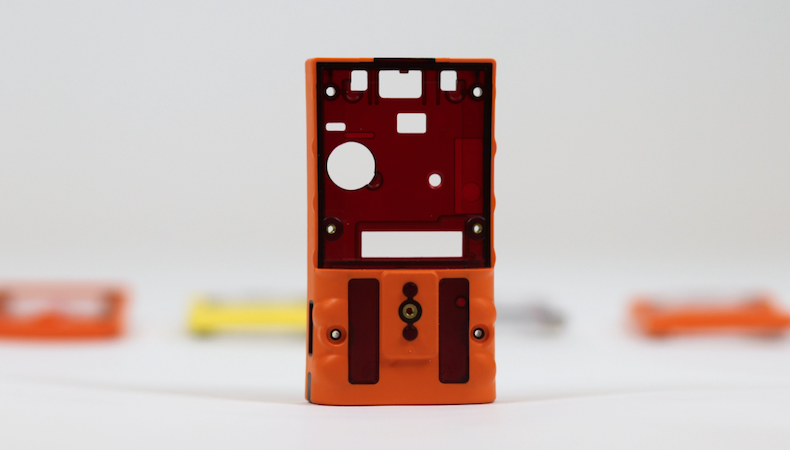
Two-Shot Injection Molding v. Overmolding: 14 Pros & Cons You Need To Know
Injection-molded parts are integral to the performance and aesthetics of a wide ra…
READ MORE
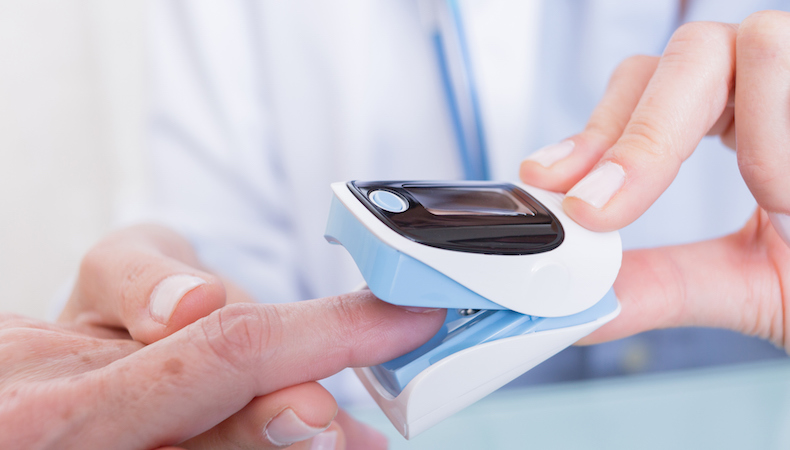
How Overmolding Enhances Handheld Medical Devices
Popular across many industries, overmolding may initially appear to simply enhance…
READ MORE
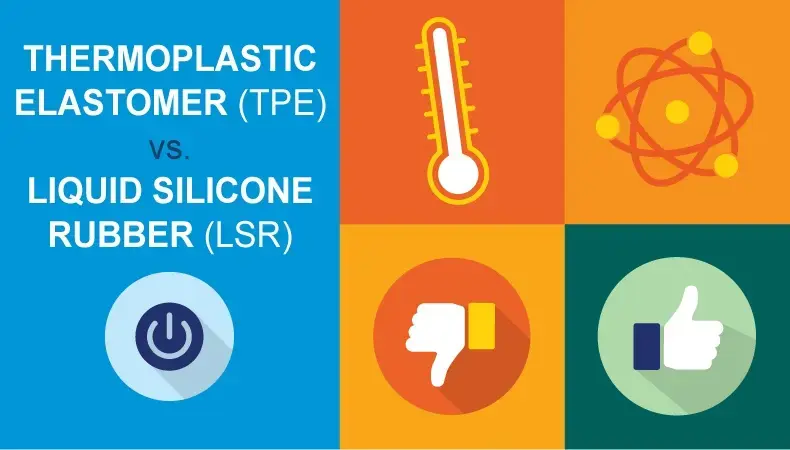
Thermoplastic Elastomer (TPE) vs. Liquid Silicone Rubber (LSR)
Confusion about which plastics align with a particular application causes uncertai…
READ MORE