Thermoplastic Elastomer (TPE) vs. Liquid Silicone Rubber (LSR)
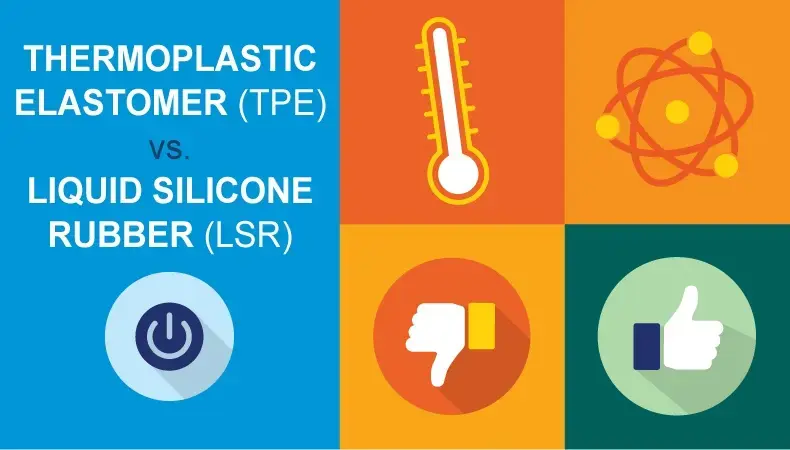
Confusion about which plastics align with a particular application causes uncertainty about when to use custom injection molding. As a result, OEMs may not take advantage of how plastics benefit product design.
“Thermoplastic” and “thermoset” sound similar, and both categories offer choices appropriate for complex applications in a range of markets. However, it's the properties and processing behaviors of the materials within the categories that ultimately reveal the best choice for your injection molding project.
For a better understanding of similarities and differences, let’s compare one plastic from each group: thermoplastic elastomer (TPE) — a thermoplastic — and liquid silicone rubber (LSR) — a thermoset.
What is TPE? WHAT IS LSR?
Thermoplastic elastomer (TPE) is a synthetic plastic that melts upon heating and hardens on cooling without changing the plastic's chemistry. Liquid silicone rubber (LSR) is synthetic plastic containing polymers joined and structured by chemical bonds that harden permanently after one application of heat.
The main difference between the two is how they react to heat. After TPE is heated, reprocessing is possible. LSR cannot be altered once heat is applied.
Moldability process
Moldability is determined by the properties and behaviors of TPE and LSR during heating:
- TPE: Plastic pellets are heat-liquified and pressure-molded into components that strengthen and hold shape upon curing without using a chemical bond. Molding can be reversed (regrind/melt) to correct defects and the plastics reused multiple times
- LSR: Viscous plastic is heated to cause polymer cross-linking, and the resulting chemical bond provides irreversible strength and shape after curing. Another common way to initiate cross-linking in LSR is to mix a catalyst with another component prior to injection into the mold
Advantages and disadvantages
Selecting TPE over LSR or vice versa may impact certain aspects of moldability and project outcomes. Therefore, it’s important to understand the advantages and disadvantages of each plastic:
- TPE advantages include:
- Recyclability and less energy consumption for production
- Re-molding opportunities without chemical change
- Easier molding than thermoset LSR
- Shorter molding cycles
- Less expensive molding process
- Heat sealability
- Easy coloration using most dyes
- Greater number of two-shot molding options
- TPE disadvantages include:
- Post-cure melting if exposed to high temperatures
- “Creeping” and deformation if exposed to sustained pressure or another stressor
- Tooling can be costly
- LSR advantages include:
- Better resistance to high temperatures than thermoplastics
- Design flexibility, including thick-to-thin wall constructions
- High tear strength
- Biocompatibility
- High chemical resistance
- Superior compression set
- LSR disadvantages include
- No recyclability
- Inability to be re-molded after curing
- Possibility of burning if heated after curing
- Lengthy curing period, which adds to production time and cost
- Potential for production delays as equipment must be disassembled and cleaned if early cure occurs
- Liquid plastic can be difficult to handle
- Bulky or thick appearance
Common applications
After considering the various aspects of TPE material vs. LSR material, deciding which is right for your particular complex application, overmolding, or metal-to-plastic conversion may seem a little daunting. While an experienced injection molder like Kaysun evaluates every project on its own merit, here are some examples of projects typically well-suited for TPE and LSR:
- TPE is ideal for:
- Soft-touch grips, seals, impact-resistant devices, and component housings
- Sealing rings
- Some food-contact-approved applications like bottle cap and closure liners, baby bottles, and toddler cup spouts (presuming FDA regulatory compliance)
- Alternatives to latex, silicone, PVC, or rubber in some medical/healthcare applications such as gloves and parts for non-invasive equipment
- LSR is ideal for:
- Medical implantables
- Gaskets and hardware in consumer appliances such as microwaves
- Electronic interfaces on device keyboards or touchpads
- O-rings, wire harnesses, coverings, stoppers, and other plastic automotive parts exposed to harsh chemicals and/or high heat
Undoubtedly, this TPE vs. LSR comparison covers a lot of ground. For future reference and review, we encourage you to download the infographic.
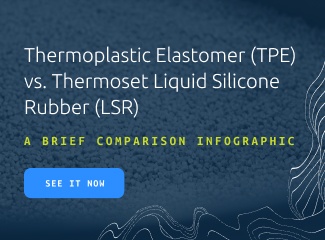
Subscribe
TO OUR BLOG
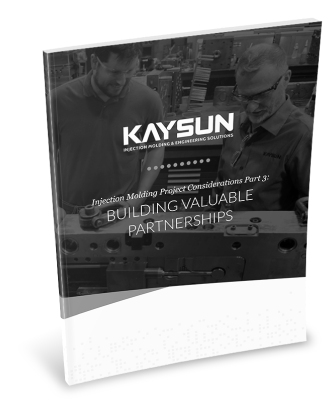
How Do Injection Molder Partnerships Influence Project Costs?
You Might Also Like...
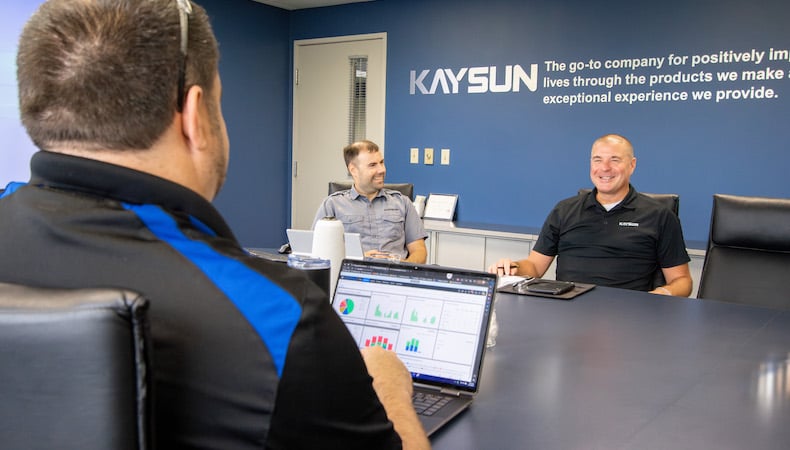
Top 3 Custom Injection Molding Trends to Watch in 2025
Despite being considered more energy efficient and producing less waste than other…
READ MORE
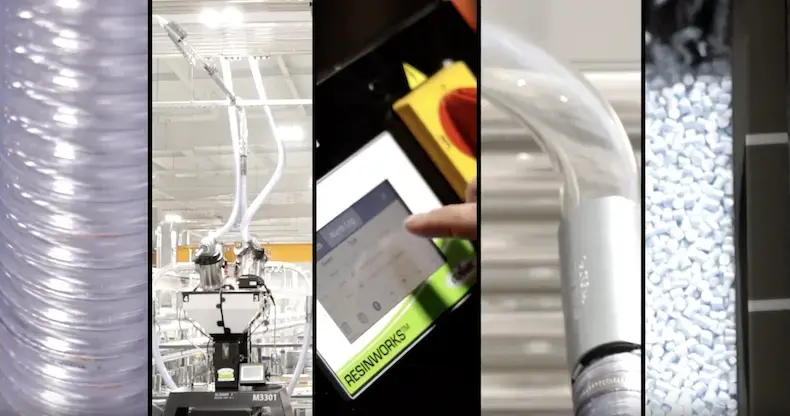
How Centralized Material Handling Streamlines Injection Molding
We consistently look for new ways to deliver timely service and top-quality parts …
READ MORE
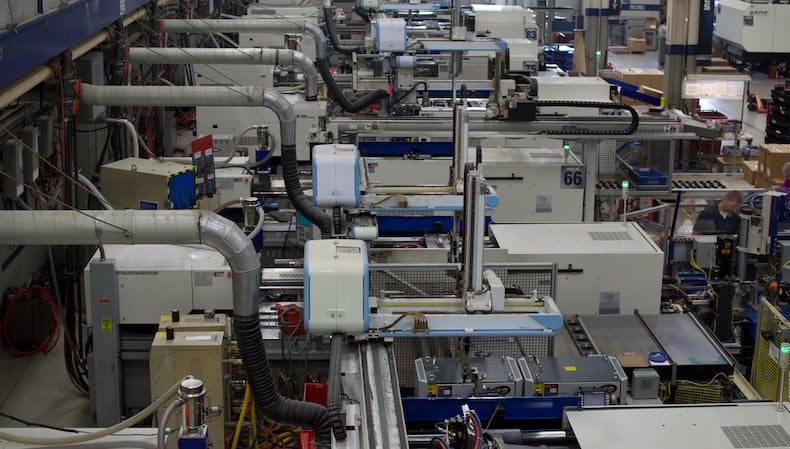
Top 14 Benefits of Injection Molding
OEMs across many industries enjoy the benefits of injection molding. It’s ideal fo…
READ MORE