Cost and Performance Benefits of Switching From Metal to Plastic Parts

For OEMs that use metal as their primary material, it’s likely they’re very happy with the parts they’re producing. There are a number of key benefits to using metal components, and if it ain’t broke, don’t fix it, right?
Using a generally accepted practice that “ain’t broke” may get the job done, but it could be costing you time, money and efficiency.
Converting metal components to plastic, on the other hand, could actually provide more advantages for your production process and final product. In fact, OEMs that choose to make the switch capitalize on the added versatility of plastic, and realize a number of valuable benefits metal simply cannot match.
Cost Benefits
One of the biggest drivers of change across any industry is the cost of production. If there are lower cost alternatives that provide the same or better results, naturally a company should pursue those. When it comes to metal-to- plastic conversion, perhaps the biggest advantage of plastic parts is their ability to potentially provide an overall cost savings of 25-50% over metal.
Also, using plastic often streamlines the number of secondary operations commonly associated with metal parts and reduces the number of assembly steps required. With plastic, OEMs have the ability to combine multiple components into a single molded part design, as opposed to making numerous individual components out of metal and welding or fastening them together. OEMs can even create complex plastic parts with tight tolerances that require no secondary machining using scientific molding processes. Having fewer production steps and less assembly time can provide a significant cost savings, as well as provide more design flexibility.
Time Benefits
In addition to streamlining assembly, injection molding gives manufacturers the time-saving advantage of having the color and surface finish ready to go right out of the mold, instead of tacking on time-consuming steps afterwards, as is the case with metal parts. Also, the injection molding process typically has faster cycle times (more parts made per machine hour) than metal components, all while producing repeatable, durable parts.
Weight Benefits
Plastic parts are typically 50% lighter than their metal counterparts, and provide more production quantity — that is, you get more more parts per pound with plastic versus metal. Below is a comparison of the specific gravity values of the two materials, which shows how drastic the difference in weight can be:
Industries Served
Manufacturers across numerous industries have embraced metal-to-plastic conversion and continue to realize the unique benefits plastics offer their projects and outcomes:
Automotive
The auto industry has been one of the biggest drivers of metal-to-plastic conversion, as car makers look for ways to lower the weight of their vehicles and increase fuel efficiency in order to comply with federal mandates. Carbon fiber-reinforced plastics are particularly popular here, as they offer more lightweight options for parts like side panels, and certain polymers can trim weight without compromising the performance of under-the-hood components.
Aerospace/Aviation
Similar to automotive manufacturers, aerospace and aviation engineers have long been using plastic parts to decrease the weight of their components. From electronics and other instrument housings used in the aircraft to more structural parts, there are many uses for plastics in today’s airplanes and spacecraft that are lighter, more efficient solutions than metal.
Military/Defense
From lightweighting military vehicles to reducing the weight of armed forces’ gear and equipment, plastic has many uses and applications for today’s military. Troops outfitted with gear made from plastic components have less of a burden to carry and are more agile, helping improve safety and mobility across the board. Advanced resins are also increasingly called upon to improve military vehicle safety by enhancing certain characteristics, like aircraft stealth capabilities or tank and other military vehicle body armor.
Consumer Appliances
With products and appliances getting smaller and more efficient, plastic components have been a lifesaver for OEMs by providing durable, seamless parts with reduced size, weight, and thickness. Injection molded parts can be made smaller and thinner than metal parts while providing the same functionality.
Industrial Lighting
Given the rise of LED lighting, plastic components are becoming more and more popular in industrial lighting applications. With LED lights, manufacturers don’t have to worry about the heat created by their lighting fixtures, and plastic housings are now much more viable, economical and versatile than metal structures.
Metal-to-plastic conversion may not be viewed as a necessity when metal components can get the job done, but more and more OEMs are understanding the benefits and practicalities of making the switch. Learn more in our whitepaper, Metal-to-Plastic Conversion: Revolutionizing the Manufacturing Process. Click the button below to access your copy now.
Subscribe
TO OUR BLOG
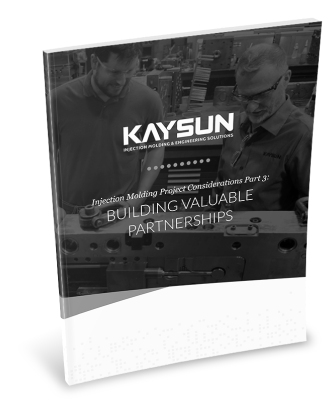
How Do Injection Molder Partnerships Influence Project Costs?
You Might Also Like...
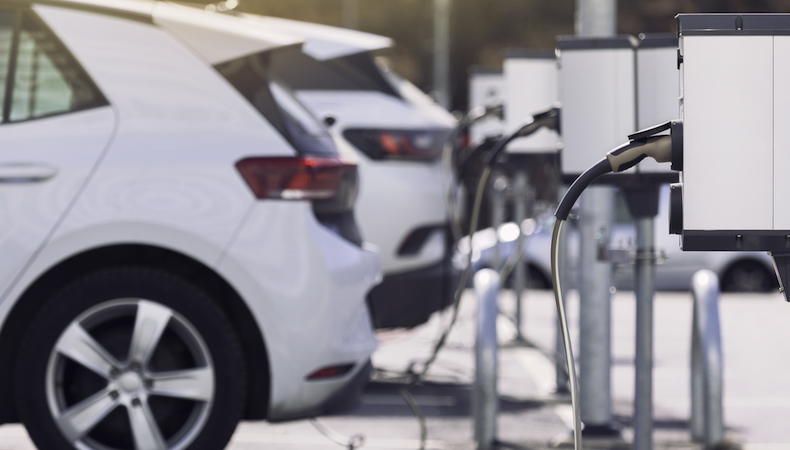
Gas or Electric: Do Vehicle Power Sources Impact Automotive Plastics Selection?
Environmental protection and the legislation surrounding it have heightened people…
READ MORE
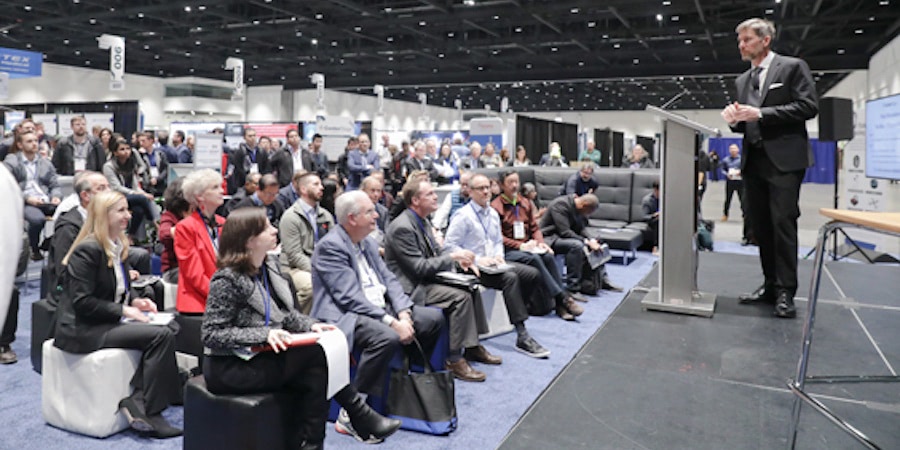
5 Presentations You Need to See At MD&M West 2022
On April 12-14, 2022, the Anaheim Convention Center (Anaheim, California) will pla…
READ MORE
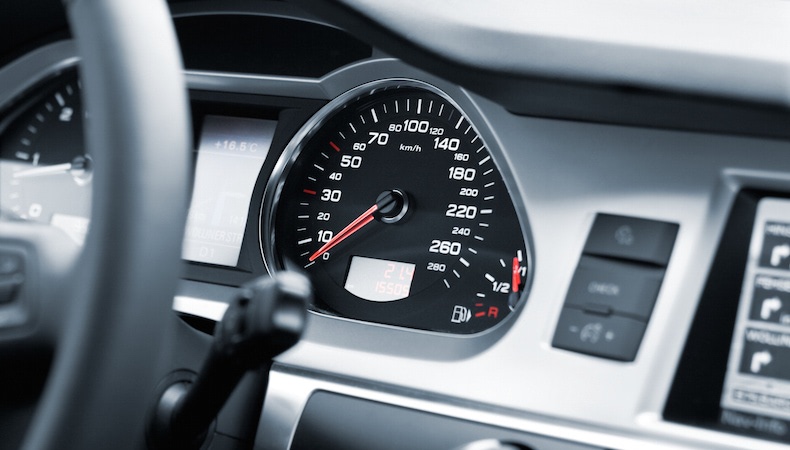
4 Automotive Plastic Parts Trends That Are Redefining the Industry
By 2024 the need for automotive plastics, parts, and innovations will push the val…
READ MORE