Gas or Electric: Do Vehicle Power Sources Impact Automotive Plastics Selection?
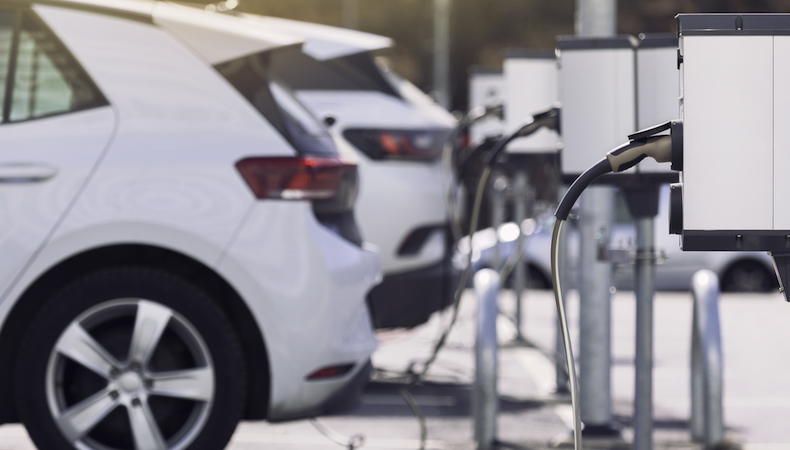
Environmental protection and the legislation surrounding it have heightened people’s sense of social responsibility when it comes to their impact on the planet. Industries, too, have embraced eco-centric initiatives that not only reduce industrial carbon footprints, but also have manufacturers rethinking the products they introduce into their markets.
The shifts in consumer and manufacturer thinking is perhaps most evident in the automotive industry. The transition from decades of gasoline-powered domination to vehicles fueled by electricity has been met with slow but steady acceptance by consumers. Recent J.D. Power survey results show about 25% of shoppers are “very likely” to consider an electric vehicle (EV) — a 4% uptick over 2021 findings.1
Car dealers point to a wider variety of EV models as a major contributor to the increase in consumer interest. That’s great news for automotive trends and sales, but what does greater EV production mean for OEMs and their suppliers? How are resin selection and automotive injection molding impacted? I sat down to discuss the topic with John Cahill and David Williston from Eynon Associates Inc., a representative for a select group of suppliers that manufacture highly-engineered automotive components and assemblies.
Different power sources, different performance considerations?
Interestingly, the shift from traditional combustion engines to battery-powered electric vehicles has caused little difference in performance considerations. OEMs must still prioritize safety, strength, and durability in the EV plastic they choose.
As such, the characteristics of the resins used remain largely unchanged between gas- and electric-powered vehicles. Automotive plastics for these applications need to provide:
- Excellent flame retardancy to prevent fire risk to injection-molded components, connectors, and cables that are configured to operate in smaller, extremely hot under-hood spaces
- High heat tolerance to maintain components’ tight tolerances and complex geometries, withstand high-voltage EV charging, and aid in battery cooling by consistently dissipating heat accumulated in battery fuel cell systems
- Chemical resistance to minimize the effects of EV plastics’ exposure to harsh substances under the hood and in external environments (e.g., corrosive road salt)
- Strength and aesthetics that may require EV plastics to be glass-filled, fiber-reinforced, or otherwise formulated to meet the durability and appearance expectations of interior and exterior vehicle applications
Lightweighting and its impact on EVs
Lightweighting gained traction in the automotive industry as a fuel economy improvement measure. A 10% reduction in vehicle weight translated to a 6-8% average fuel savings.2 For EVs, lightweighting improves battery range in similar fashion. In some instances, lighter EV weights can lead to the use of smaller batteries without reducing range.
As with traditional gasoline-powered vehicles, metal-to-plastic conversion plays a role in EV lightweighting. However, with EVs, different opportunities exist for using automotive plastics in place of metal.
Battery pack enclosures are of particular interest. Replacing aluminum enclosures with plastic composites means lighter construction overall from a materials perspective. Also, plastic enclosures can be formed and sealed using fewer parts than aluminum which further reduces weight. Although not weight-related, the ancillary benefit of a plastic battery enclosure’s improved EMI and RFI shielding capabilities is indispensable in preventing electronic component failure.
To maximize the automotive injection molding opportunities presented by EVs, it’s imperative that automotive plastics not be chosen arbitrarily. Having the guidance of an expert injection molder with specialized knowledge in resin behaviors and selection is your guarantee of achieving your EV performance, safety, and lightweighting goals.
For more on how a full-service injection molder like Kaysun can help, read Converting Metal Automotive Parts to Plastic: A Manufacturer’s Guide. Click the button below to download your copy now.
SOURCES:
1Detroit Free Press, J.D. Power survey: More buyers 'very likely' to consider EVs, May 26, 2022
2Energy.gov, Lightweight Materials for Cars and Trucks | Department of Energy, Undated
Subscribe
TO OUR BLOG
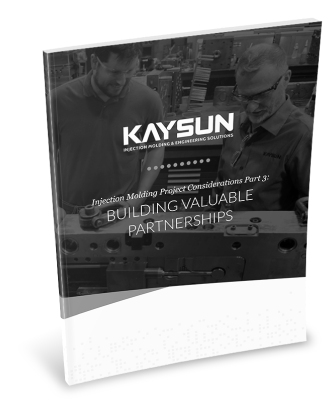
How Do Injection Molder Partnerships Influence Project Costs?
You Might Also Like...
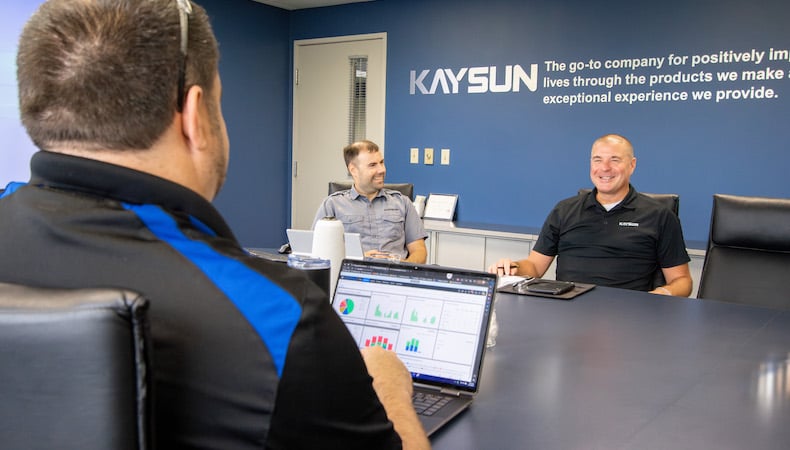
Top 3 Custom Injection Molding Trends to Watch in 2025
Despite being considered more energy efficient and producing less waste than other…
READ MORE
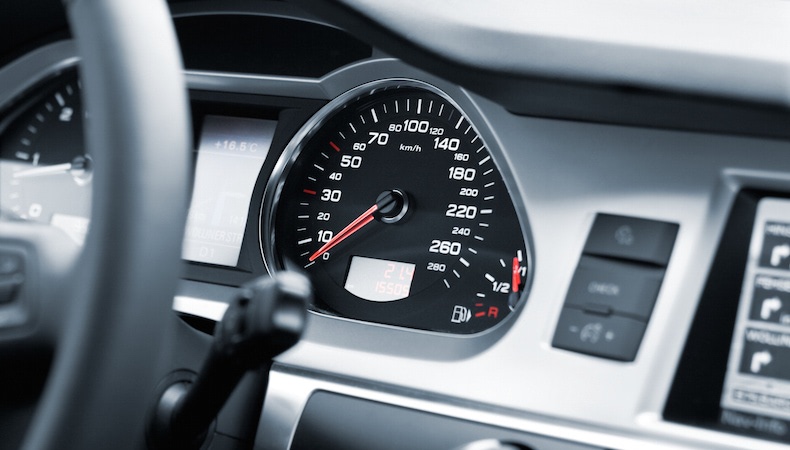
4 Automotive Plastic Parts Trends That Are Redefining the Industry
By 2024 the need for automotive plastics, parts, and innovations will push the val…
READ MORE
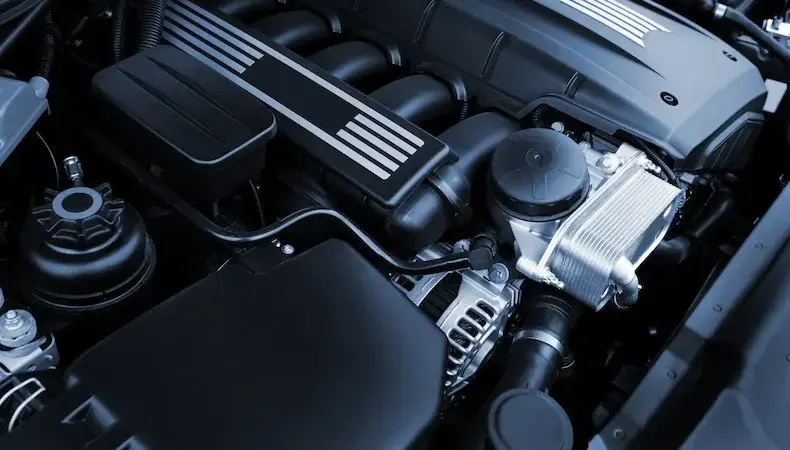
Precision Automotive Plastics: How Molders' Material Expertise Benefits Components
Precision automotive plastic components aren’t limited to sleek dashboards, seats,…
READ MORE