What is Finite Element Analysis? How Does it Improve Part Performance?
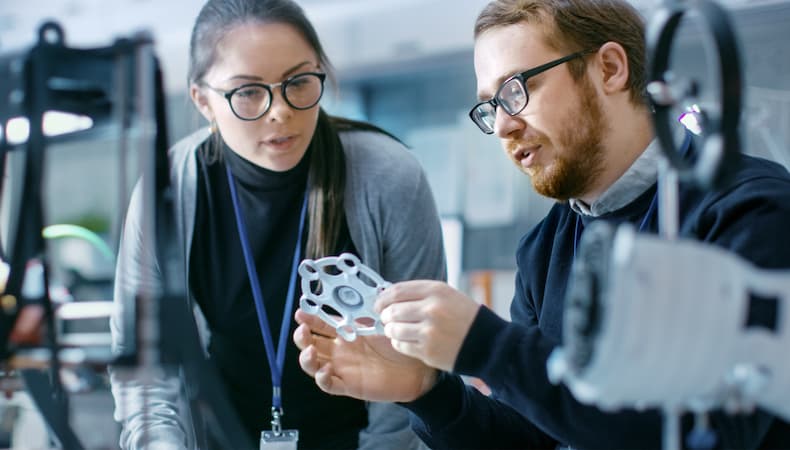
Plastics continue to become manufacturers' primary solution to weight, sustainability and compliance challenges. Yet, performance is largely dictated by the resin chosen for a specific injection-molded part.
The question is, which material is the right one?
For an accurate answer, manufacturers turn to Finite Element Analysis (FEA) of plastic components and custom injection molders experienced in all aspects of testing.
fea calculations: stress-strain curves
Strength and flexibility are key characteristics in determining a resin's suitability for use. FEA allows for the precise examination of both by dividing an injection-molded part into finite-sized units of simple shape. Mathematical equations are used to test each unit for displacement, from which key stress and strain data are derived.
FEA revolves around the stress-strain curve (or plot), which is distinctive for each resin. The stress-strain curve reflects the amount of deformation (strain) that is caused by tensile/compressive loading (stress, or pressure).
The shape of the curve is determined by:
- Resin type
- Resin temperature
- Loading speed
The final curve reveals the critical properties of the resin and its potential alignment with the intended use. Stress-strain curves may be non-linear or linear, depending upon if the resin being analyzed is unreinforced or reinforced.
non-linear curves
Unreinforced plastics have a very non-linear (curvy) stress-strain line up to the yield point and must be analyzed with equations derived for non-linear materials, not linear materials.
This is an important distinction as some molders:
-
- Choose not to invest in non-linear FEA software that is more expensive, takes more time to set up, and takes more time to run. They simply default to software that is familiar and perhaps more in keeping with budget management
- Rely on the published Young's modulus value data provided by the supplier rather than analyzing the stress-strain curve of the material being evaluated. Modulus value data can skew outcomes since it represents a single point on the stress-strain curve
Either shortcut can provide misleading results. An experienced injection molder will use the actual stress-strain curve information to ensure accuracy in non-linear FEA testing.
linear curves
Glass can be added for strength/stiffness and to increase temperature resistance in many plastics. Glass-reinforced plastic parts may be easily evaluated using linear FEA techniques. Linear FEA assumes “small displacement” of the part being analyzed and uses an appropriate equation to solve the calculations more quickly.
Typically, yield strength and ultimate strength are equivalent so the stress-strain curve stays linear. Glass fiber is much stiffer than the base resin and overwhelms the non-linear properties of the resin. Fiber-reinforced resins behave much like metal, but rather than stretching/yielding at a certain point, the material just breaks. There is no true yield point.
knit line strength
Another reinforcement issue is knit line strength. A resin melt flow front splits to go around a core pin or opening in the part during the injection molding process. When the flow front meets the other half of the split on the backside of the opening, a knit line occurs.
A butt-type knit joint where the flow fronts meet “face-to-face” is the most detrimental injection glass-reinforced resin injection molding outcome. A flow front pushes any smoke, trapped air, or mold surface contamination ahead of it. All of these elements are concentrated at the knit line and weaken the bond between the two fronts. Should butt-type knit joints occur when using fiber-reinforced resin, the knit joints are even weaker since the fiber cannot cross over knit lines.
A similar condition exists wherein the flow fronts meet and then flow side-by-side to finish filling the injection-molded part. While not desirable, this molding defect is less severe than a butt-type knit joint since any contamination could be pushed and deposited in front of the flow front.
Using FEA Mold flow software
Generally speaking, sophisticated FEA mold flow software predicts resin flow within tooling. Results from an FEA simulation are used to:
- Infer fiber orientation and knit line locations to guide design decisions about part strengthening by preventing high-stress areas coinciding with knit lines and/or gating misplacement
- Conduct Structural FEA using mechanical properties of “in-flow” and “cross-flow” directions to get a better understanding of how the part will perform/react
The information gleaned from mold flow analysis is granular and critical. It's imperative to partner with a proven injection molder that has in-house engineers capable of running mold flow software and accurately interpreting results. Production and performance of an injection-molded part's complex geometries, tight tolerances, and other intricacies could hang in the balance.
ENGINEERING A SOLUTION
Effective FEA processes and simulation hinge on the in-depth knowledge engineers possess about the material they are evaluating and could ultimately be using. Not all injection molders are able to tap into this level of experience. Fewer still have in-house engineers who are specially trained in plastics behavior — a notable distinction for Kaysun, and a competitive advantage for you.
Plastics Selection for Industrial Applications explores how a true, well-rounded injection molding partner like Kaysun can help you assess injection molding projects from a materials perspective to potentially save time, money, or both. Click the button below to download your copy of this valuable guide now.
SOURCE: Grand View Research, Plastic Market Size, Share, and Trends ... 2021-2028, April 2021
Subscribe
TO OUR BLOG
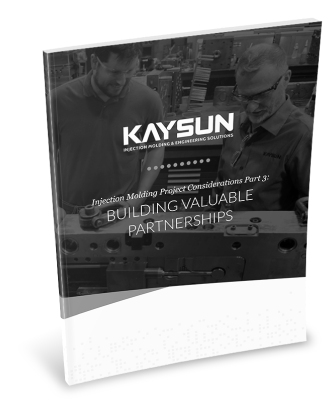
How Do Injection Molder Partnerships Influence Project Costs?
You Might Also Like...
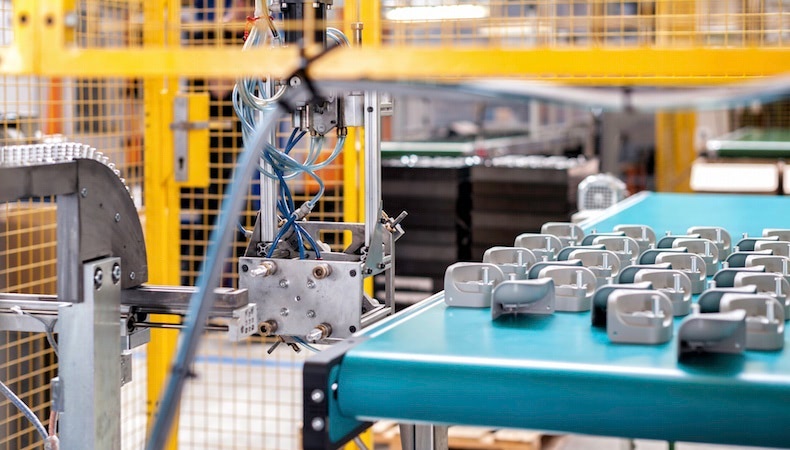
The Impact of Non-Uniform Injection Molding Wall Thickness
Shrink rates for plastic parts vary depending on the materials used and the unifor…
READ MORE
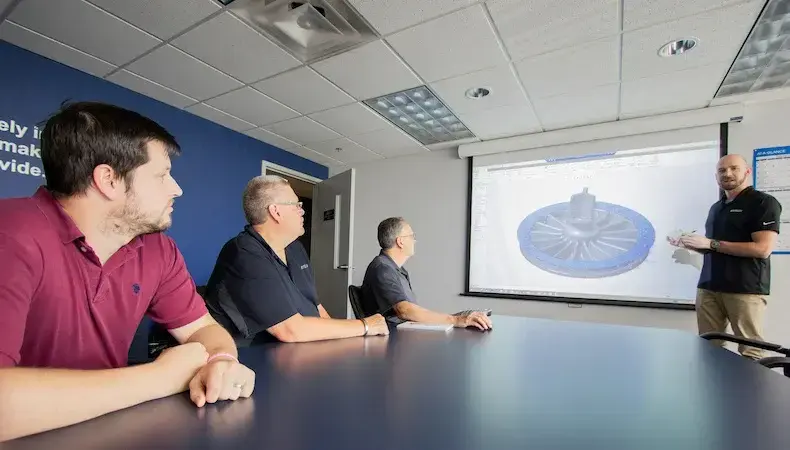
5 Engineering Factors That Improve Your Injection Molding Project
In many complex industries, decisions about which injection molder to use for cust…
READ MORE
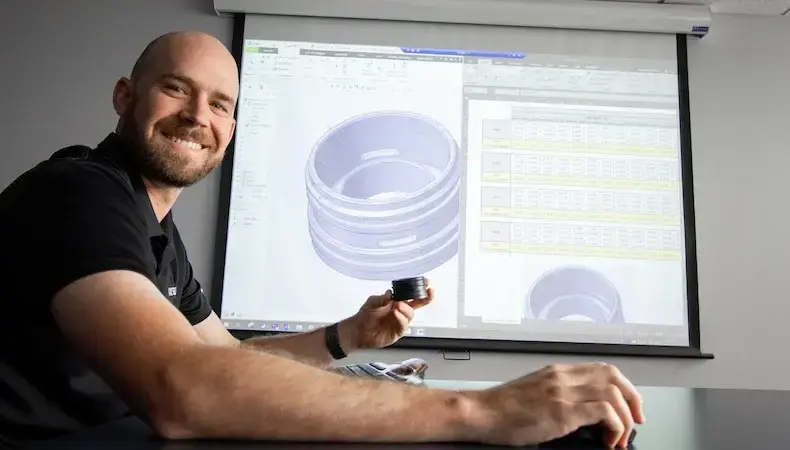
Why Continuing Plastic Engineering Education Matters to OEMs
Technologies, product needs, and customer expectations are rapidly advancing. OEMs…
READ MORE