Featured Blogs
How Today’s Manufacturers Benefit from Scientific Injection Molding
How Today’s Manufacturers Benefit from Scientific Injection Molding
As technologies and demand rapidly increase the competition in many industries, there’s little room for traditional injection mo…
READ MORE
Tooling Audits & Evaluations: How Molders Help OEMs Gauge Health of Assets
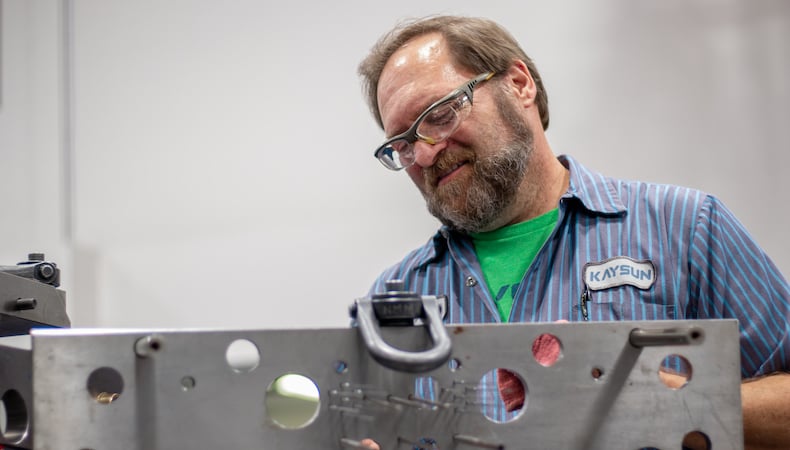
Tooling Audits & Evaluations: How Molders Help OEMs Gauge Health of Assets
READ MORE
4 Factors That Reveal an Injection Molder’s Plastic Engineering Bandwidth
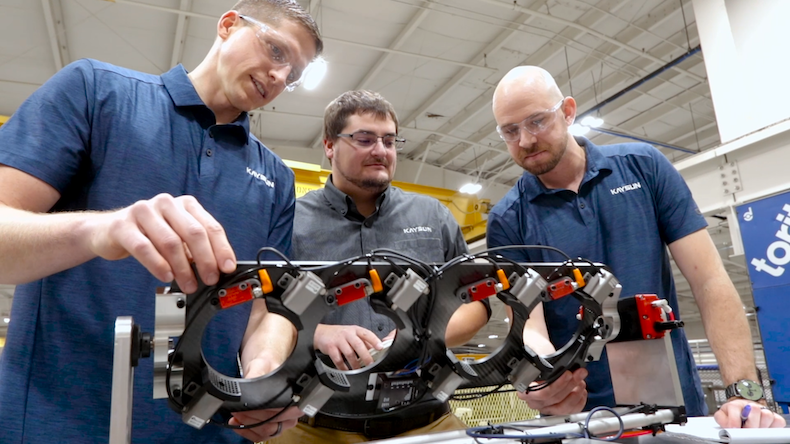
4 Factors That Reveal an Injection Molder’s Plastic Engineering Bandwidth
READ MORE
3 Key Custom Injection Molding Trends Emerging In 2024
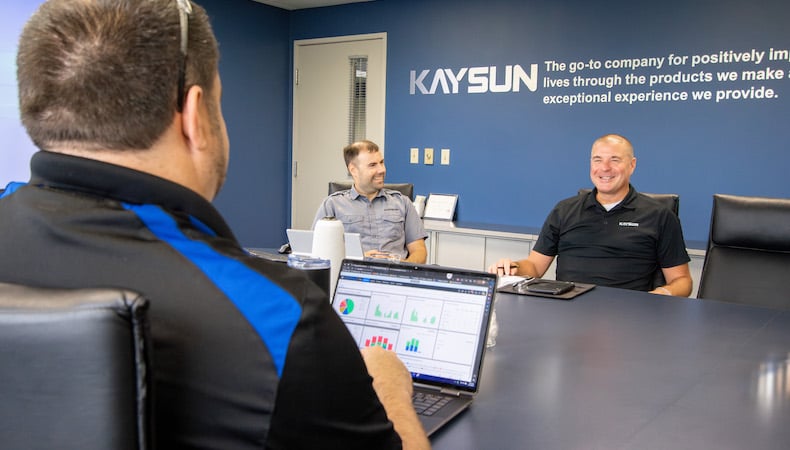
3 Key Custom Injection Molding Trends Emerging In 2024
READ MORE
Browse All Kaysun Articles
How MD&M West 2024 Keeps MedTech Professionals Ahead of the Curve
How MD&M West 2024 Keeps MedTech Professionals Ahead of the Curve
MD&M West is one of the largest and most respected medical device trade shows in…
READ MORE
How VA/VE Improves Injection Molding Quality Control
How VA/VE Improves Injection Molding Quality Control
Value Analysis/Value Engineering (VA/VE) is a systematic approach to cost management…
READ MORE
Molder Effectiveness: Market Specialization or Supplier Diversification?
Molder Effectiveness: Market Specialization or Supplier Diversification?
For companies that require tight-tolerance, sophisticated plastic injection molding …
READ MORE
The Bottom Line on Custom Injection Molding TCO vs. Per-Part Quotes
The Bottom Line on Custom Injection Molding TCO vs. Per-Part Quotes
Complex applications typically require custom injection molding solutions. It’s an i…
READ MORE
How to Design for Sustainable Injection Molding: Values, Materials & Processes
How to Design for Sustainable Injection Molding: Values, Materials & Processes
Sustainability is an increasingly urgent concern for businesses. On one hand, consum…
READ MORE
7 High-Priority Design Considerations for Injection Molded Parts
7 High-Priority Design Considerations for Injection Molded Parts
The design of injection molded parts can be incredibly complex. Sometimes, it’s a by…
READ MORE