Top 3 Custom Injection Molding Trends to Watch in 2025
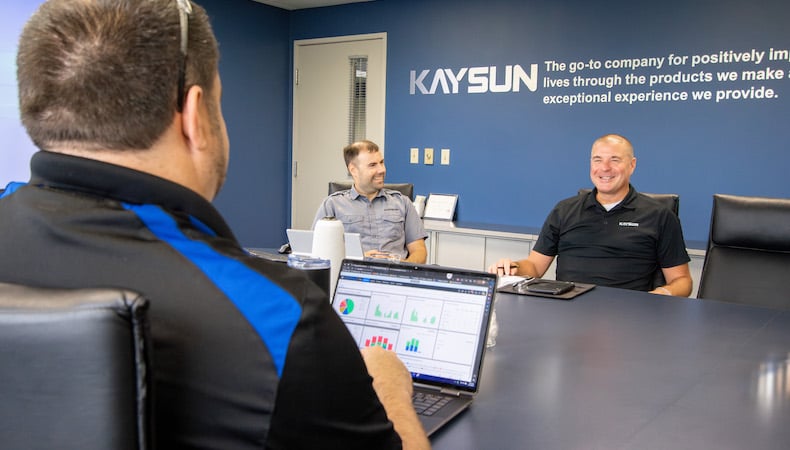
Despite being considered more energy efficient and producing less waste than other molding methods, injection molding continues to be viewed with skepticism when it comes to environmentalism. Ironically, process efficiencies and the impact of materials are generally the areas of most concern and scrutiny.
As the industry continues to lean into overcoming these challenges, it’s no surprise that some of the biggest trends forecasted for 2025 are largely tied to more sustainable practices and productivity.
2025 Injection Molding Trends:
1. AI-driven Operations
Decades of machine learning in industrial settings and the advancements of the Industrial Internet of Things (IIoT) suggests that artificial intelligence has always been part of the manufacturing landscape.
Undoubtedly, Industry 4.0 accelerated the adoption of connectivity, machine learning, and data exchange with the primary aim of rule-based automation. As the IIoT advanced, so did cloud computing, edge computing, and reliance on Big Data in decision-making.
Early iterations of artificial intelligence (AI) harnessed the power of these insights. Recent years have seen AI fuel Industry 5.0 — essentially, humans and smart machinery working together to build more resource-efficient and sustainable operations. It appears 2025 will also find AI front-and-center in automation and robotics that continue to refine:
- Process optimization through automatic, real-time monitoring and adjustment of key injection molding parameters such as temperature, pressure, and cycle times
- Predictive maintenance based on tracking physical wear and tear on equipment, and identifying patterns that signal potential failure and the need for proactive maintenance to prevent costly downtime
- Supply chain and inventory management that uses data such as market trends, order history, and optimal inventory levels to forecast production needs and vendor strategies
2. Greater Energy Efficiency and Smaller Carbon Footprint
Injection molding was first done on hydraulic equipment, and hydraulics were the mainstay in the plastics industry from the late 19th century through the mid-20th century
Hydraulic equipment’s massive operational energy requirements, oil use and mishandling, and elevated greenhouse gas emissions during lengthy machine start-up and frequent production interruptions, raised significant environmental concerns.
While still in use, hydraulic equipment has largely given way to all-electric machines designed to address and remediate environmental threats brought about by hydraulics. As sustainability initiatives proliferate in 2025, expect to see injection molders leverage electric machines to:
- Increase energy efficiency on the line and reduce reliance on fossil fuels
- Eliminate hydraulic oil use and the related potential negative impacts
- Reduce carbon footprint by inherently lowering energy demand and greenhouse gas emissions, along with introducing more options for using alternative energy sources
3. Less Waste Through Smart Technology
The consistency and precision of robotics and automation have revolutionized injection molding efficiency, and have proven to help lessen the impact of skilled labor shortfalls.
Equally as important is how these technologies contribute to waste reduction through:
- Waste-free material handling that ensures accurate measurements, essentially no spillage or overuse, minimal contamination risk, and efficient purging during material changeovers — as demonstrated by our own central material handling system
- Minimizing risk human error that could negatively impact part consistency and quality, leading to a greater number of defects
- Reduced cycle times resulting from part cooling optimization, streamlined finished part removal, and faster preparation of machines for subsequent cycles
- Automated regrind of runners, sprues, scrap, and defective parts to divert plastic waste from landfills
Maximizing the benefits of robotics and automation is as crucial in 2025 as ever before. Look for amplification of technologies in support of more sustainable practices.
Staying On-Trend
Heading into 2025 there are several opportunities for greater environmental awareness and more sustainable practices. The choice you make in injection molding partners will likely influence how quickly — and how well — you capitalize on emerging trends.
5 Questions OEMs Must Ask Before Partnering With a Custom Injection Molder details the information you need to objectively evaluate and select the injection molder that can support your goals. Download your copy of the guide now.
Subscribe
TO OUR BLOG
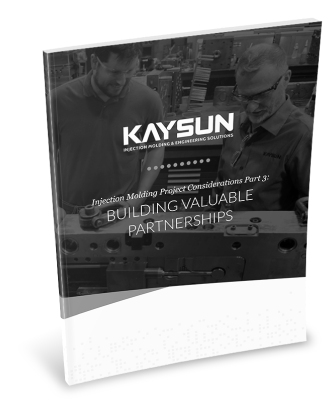
How Do Injection Molder Partnerships Influence Project Costs?
You Might Also Like...
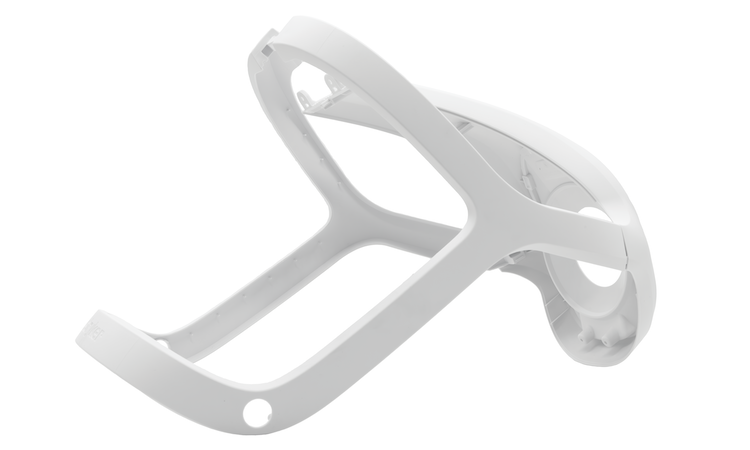
Stryker Turns to Kaysun for Steri-Shield® 8 Helmet Solution
When Stryker set out to develop its next-generation Steri-Shield® 8 Personal Prote…
READ MORE
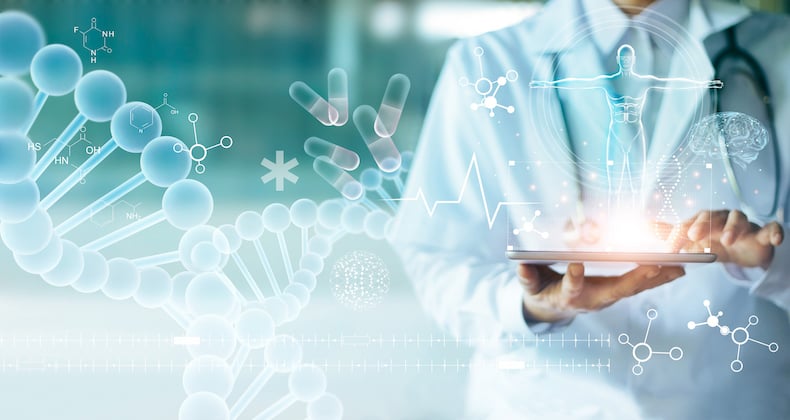
How MD&M West 2024 Keeps MedTech Professionals Ahead of the Curve
MD&M West is one of the largest and most respected medical device trade shows …
READ MORE
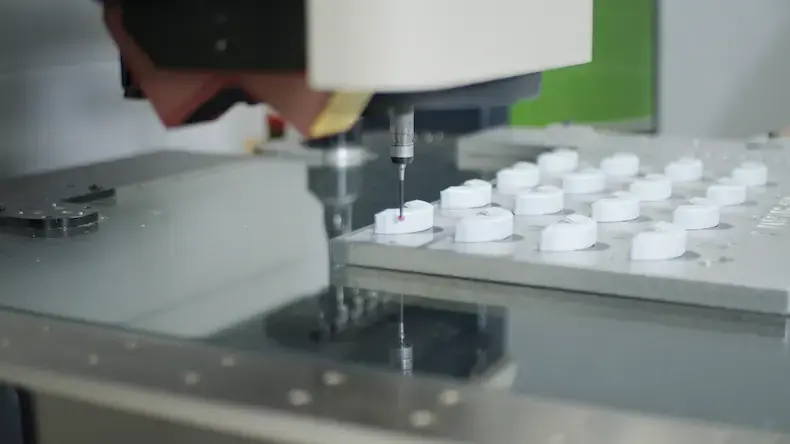
How MedAccred Accreditation Helped Kaysun Enhance Processes & Quality Systems
When you operate at the top of your game, reach higher. Kaysun had already shown i…
READ MORE