Medical Device Product Development Timelines: 6 Best Practices
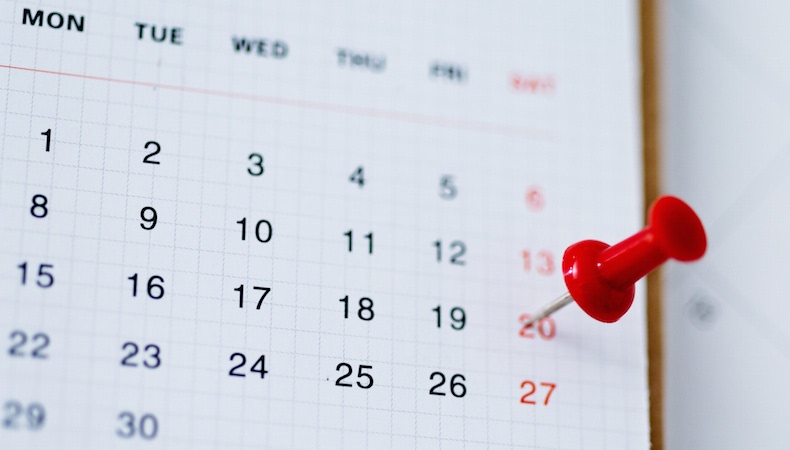
When working on a plastic medical device that could potentially save lives, it’s crucial to get that device to market quickly. Every day you save during a medical device product development timeline is an extra day people who need your device have access to it. Plus, if a competitor releases a similar device before you, they reap the rewards of being the first to market.
Yes, new medical device product development presents many hoops for manufacturers to jump through. Yet, the proper planning and manufacturing partnerships can help avoid the causes for a medical device or product going beyond its development timeline.
Common Delays in Medical Device Development
1. Incomplete qualification package
Not having the necessary regulatory and compliance paperwork completed correctly and with enough lead time to get your final product to market could cause a lengthy delay.
2. Improper submission to the FDA
Not properly submitting your device to the FDA in a timely fashion jeopardizes your speed to market because of the review and approval process.
3. Neglecting the supply chain early in design
Sourcing raw materials and parts can impact when production begins. For example, when sourcing from 12 different suppliers, all materials/components need to arrive on time in order to start assembly. Consolidating suppliers makes logistics easier.
4. Tooling requirements addressed too late
When trying to meet a strict deadline, avoid having to switch plans midway through the process by addressing all necessary design features and tooling requirements upfront.
6 BEST PRACTICES FOR HITTING MEDICAL DEVICE DEVELOPMENT TIMELINES
1. Create a realistic timeline based on critical design features
If you want to stay on top of your product development schedule, start by making a realistic action plan as early as possible. Be honest about what features of your product are critical and non-critical. Things like unnecessarily tight tolerances will impact your manufacturability and production time.
2. Analyze your competitors
Knowing what your competitors are doing helps your medical device product development team set and meet deadlines. Keep your ears to the ground for any projects that may threaten yours so your company can win the race to market.
3. Centralize your company’s data
The FDA requires a Quality Management System, yet a paper-based system is inefficient for finding/sharing documents. An all-digital system, such as a cloud-based ERP, provides access to all production and quality data on-demand.
4. Clearly communicate qualification documentation needs to all manufacturing partners
Because incomplete qualification packages cause delays, choose vendor partners who know the medical industry. Then clearly communicate to them upfront what documentation is needed. This helps ensure you have enough time to submit your qualification package and meet your full medical device development timeline.
5. Source suppliers and equipment early in the design process
Choose a custom plastic injection molder that provides extensive DfM support, ISO 13485 certification, and medical injection molding expertise, and involve them early in the design process to accelerate speed to market. Their engineers will guide material selection and show how to optimize your part design for moldability and final product assembly. For example, if your medical device requires an antimicrobial finish, your molder will help choose an antimicrobial resin that’s compatible with other materials in your device.
6. Strongly consider a MedAccred accredited injection molder
More and more medical OEMs are searching for injection molders that can capably and confidently serve the medical industry. That’s assured with MedAccred accreditation, the unparalleled benchmark of production and quality standards. Only an elite group of injection molders can help streamline the production process while meeting — and exceeding — the highest expectations for injection molded medical devices and components.
NOW IS A GOOD TIME TO START AVOIDING DELAYS
With speed to market largely determining a product’s profitability, avoiding costly delays can have a tremendous impact on your bottom line. Organize your information, align your products with regulatory standards, and work with suppliers that understand your industry and sense of urgency. Do these things and start regularly hitting your medical device product development timelines.
Keep your competitive advantage when launching a new product by first reading our eBook, 5 Steps to Get New Injection Molded Products to Market Faster. Click the button below to get your copy now!
Subscribe
TO OUR BLOG
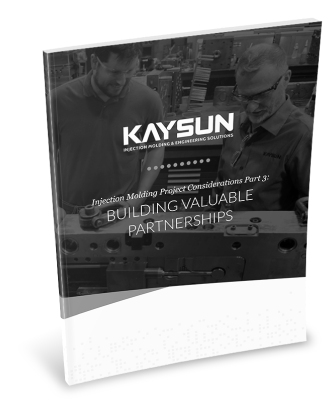
How Do Injection Molder Partnerships Influence Project Costs?
You Might Also Like...
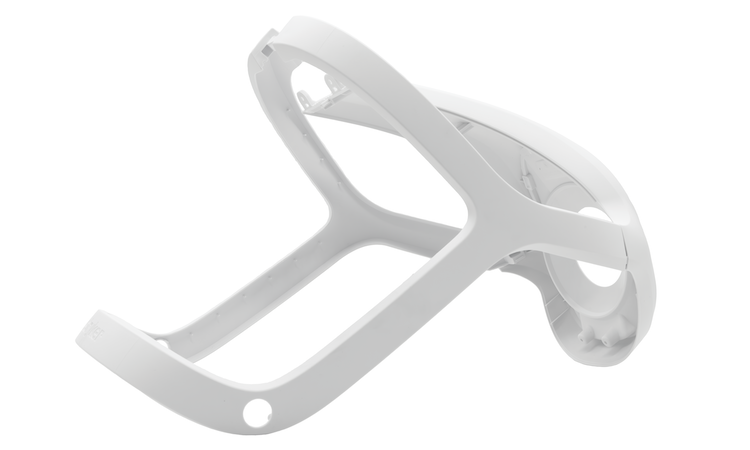
Stryker Turns to Kaysun for Steri-Shield® 8 Helmet Solution
When Stryker set out to develop its next-generation Steri-Shield® 8 Personal Prote…
READ MORE
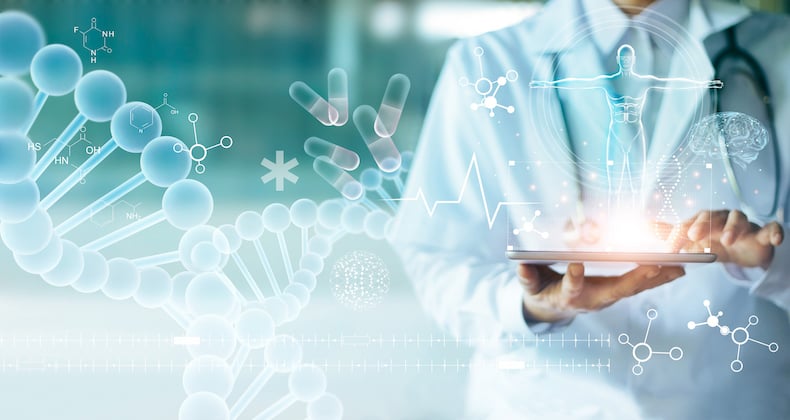
How MD&M West 2024 Keeps MedTech Professionals Ahead of the Curve
MD&M West is one of the largest and most respected medical device trade shows …
READ MORE
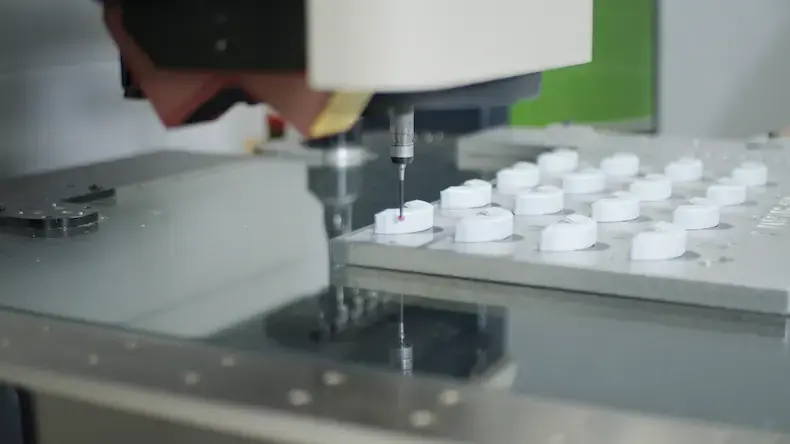
How MedAccred Accreditation Helped Kaysun Enhance Processes & Quality Systems
When you operate at the top of your game, reach higher. Kaysun had already shown i…
READ MORE