How Injection Molding Engineers Help Bridge The Design Skills Gap
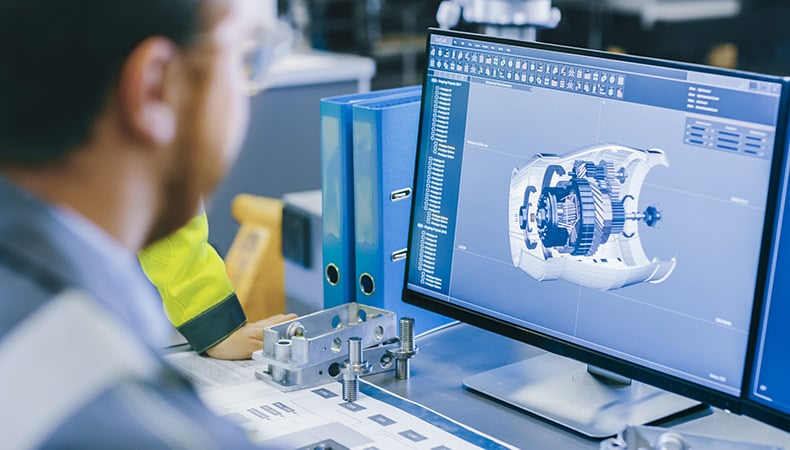
The impact of the widening skills gap is of ongoing concern for manufacturers. The 2018 Deloitte skills gap and future of work in manufacturing study reports that the average time to fill skilled production worker positions jumped from 70 days to 93 days between 2015 and 2018, surpassed only by finding engineers, researchers, and scientists which bounced from 94 days to 118 days over the same time period.
The Deloitte study points to three explanations for the current talent shortage: Baby Boomer retirements, misperceptions people entering the workforce hold about the manufacturing industry, and — most impactful — the “shifting skill set due to the introduction of new advanced technology and automation.” Regardless of the reason, the skills gap puts individual OEMs at a competitive disadvantage and the U.S. manufacturing economic output as a whole at a potential $2.5 trillion deficit by as early as 2028.1
To lessen the burden of the shortfall in skilled workers, 42% of the OEMs polled by Deloitte researchers identified outsourcing as their solution.1 Looking specifically at design engineering services, outsourcing for this category has increased by nearly 15% over its historical average in recent months,2 a trend that will likely continue despite OEMs identifying certain risks to product quality, among other concerns.1
Mitigating these risks is both essential and possible for OEMs that work with experienced custom injection molders. In addition to the depth of materials knowledge and process expertise that can be leveraged, an injection molder’s design and engineering teams are valuable collaborative resources for OEMs.
Of particular importance is how well-versed the injection molder is in advanced processes like Design for Manufacturability (DfM). Kaysun, for example, has a number of specially trained engineers who proactively design products to optimize all facets of manufacturing, including design, tolerances, functionality, tooling, materials performance, and costs. OEMs outsourcing to Kaysun can be confident in outcomes and will likely gain production efficiencies.
As the skills gap continues to compel OEMs to outsource engineering and design services, partnering with an injection molder that offers the breadth and depth to take on the challenge, reduce OEM risk, and preserve product quality is pivotal. Learn more in our white paper, Custom Injection Molding for a Competitive Advantage. Click the button below to access your copy now.
SOURCES
1Deloitte, 2018 Deloitte skills gap and future of work in manufacturing study, Undated
2Thomas, Skills Gap Pushes Manufacturing Companies to Outsource Design Engineering Work, July 22, 2019
Subscribe
TO OUR BLOG
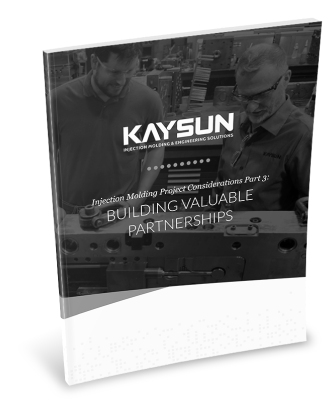
How Do Injection Molder Partnerships Influence Project Costs?
You Might Also Like...
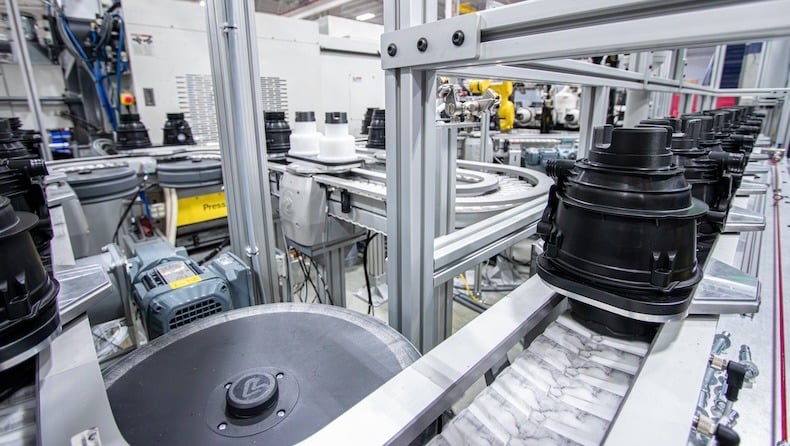
Kaysun Integrates AI on the Production Floor with RJG CoPilot
Industry 4.0 has made manufacturing more dynamic than ever before. Merging IoT, AI…
READ MORE
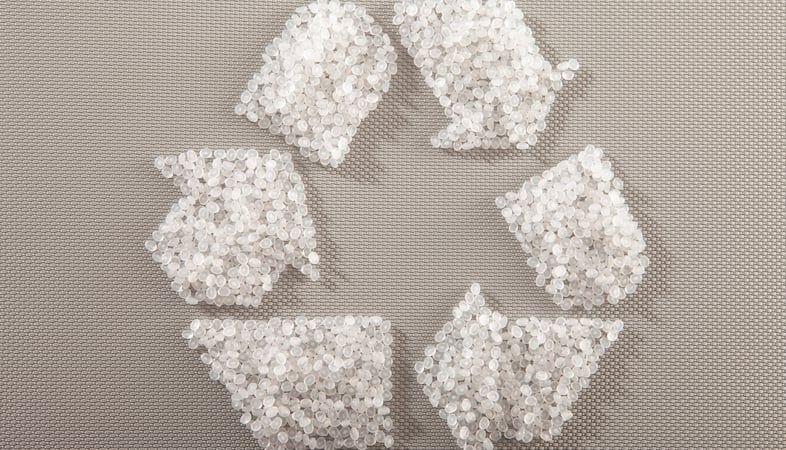
How Kaysun’s Culture of Sustainability Benefits OEMs and The Planet
Injection-molded parts and products are staples for OEMs in industries ranging fro…
READ MORE
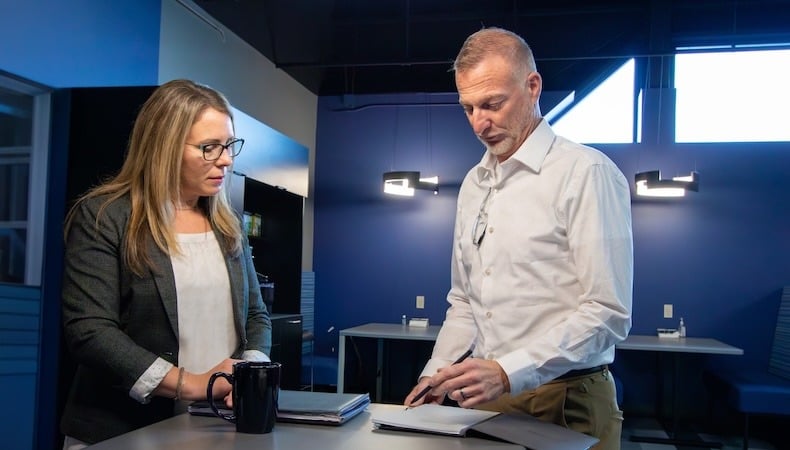
12 Common Injection Molding Questions — Answered!
Injection molding is a versatile and precise process, making it ideal for OEMs tha…
READ MORE