6 Plastics Industry Trends Predicted to Impact Manufacturers in 2020
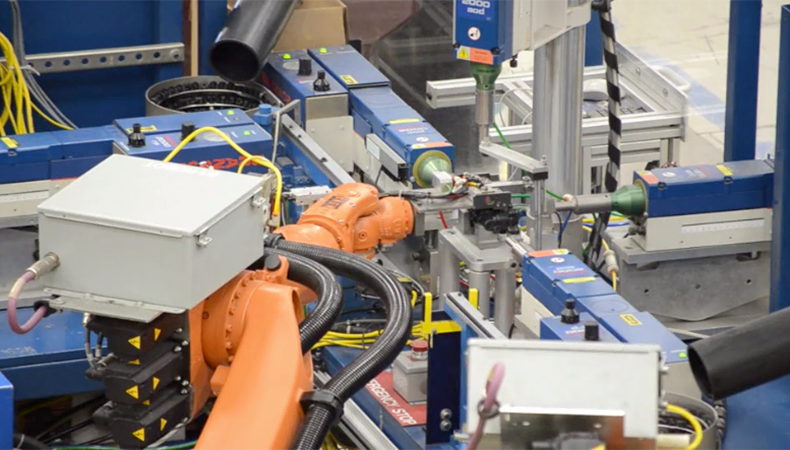
What does 2020 hold for the plastics industry? Several trends that emerged in 2019 continue to be refined and amplified:
1. SUSTAINABILITY
OEMs are assuming more responsibility for sustainability by working with suppliers that are committed to low- or zero-waste initiatives and the use of recycled materials. Injection molders are tasked with refining processes to include scrap reduction and/or recycling to aid the circular economy, along with introducing more earth-friendly resins and additives into projects as appropriate.
2. Bioresins and Eco-Friendly Plastic Additives
The environmental impact of traditional resins remains under close scrutiny, leading many manufacturers to reconsider their approach to selecting materials. Bioresins are gaining traction as alternatives since they’re all based on natural plant and vegetable extracts or renewable resources, which aid in green practices through benefits such as safer disposal, energy-efficient manufacturing and decreased toxic emissions.
Along with developing plastic substitutes, solutions for making conventional thermoplastics biodegradable are coming to the fore. Prodegradant concentrates (PDCs) in the form of metal compounds, such as cobalt stearate or manganese stearate, are being added to plastic to promote oxidation and disintegration. In turn, the plastic breaks down into tiny fragments that microorganisms ingest and convert into carbon dioxide, water and biomass, without the threat of harmful residues.
3. Reinforced Plastics
At the end of 2019, the projected value of the global reinforced plastics market was estimated at nearly $16 billion. Carbon, glass, metal and graphite-reinforced plastics are perhaps most notably embraced by the automotive industry as substitutes for metal components. However, they are also gaining popularity in medical and defense applications for their low weight, durability and design versatility.
4. SLIM, LIGHTER WEIGHT PARTS AND TOOLS
Given mandates surrounding improved gas mileage in traditional vehicles and longer battery life for hybrids and electric cars, lightweighting remains a key focus for automotive OEMs in 2020. However, the auto industry isn't the only one requiring a switch to slimmer, lighter weight injection-molded plastic parts. Medical OEMs are seeing shifts in how plastics are used within their industry, largely in concert with advanced technologies. There are a myriad of internal applications (stents, joint replacements, mesh scaffolds, etc.) for specialized medical-grade plastics, but there is also an uptick in the call for injection-molded tools, equipment, and devices to better manage the increasing mobility of healthcare, the associated costs, and outcomes.
5. 3D Printing and Production Efficiencies
3D printing is improving many aspects of plastics manufacturing and remains a catalyst for reimagining options for plastic parts. While in some cases 3D printing is not a viable alternative to injection molding, advancements in the technology are leading to some impressive results with direct benefits for certain OEMs, including:
- New options for projects of 100-500 cycles, as less time is required to produce a part using 3D printing
- More efficient production molds with printed-in conformal cooling channels that reduce cycle times without compromising part quality
- Prototyping without hindering production; for certain applications a desktop polymer printer can produce a suitable prototype with functionality similar to one produced on the line
6. Automation and Industry 4.0
Automation is meeting the plastics industry demand for process simplification and cost savings. The advent of Industry 4.0 provides prime opportunities for further integration of robotic technologies and machine controls in order to:
- Make cycles faster, facilitate maintenance and simplify programming
- Use automated cells with multiple downstream operations integrated beside the press
- Substitute traditional pneumatics for “collaborative” robotic initiatives — meaning those with multiple, axis-jointed arms, servo wrists and advanced safety features — for faster, more precise programming on the line to aid in all facets of production, saving time and increasing throughput
Understanding how the plastics industry is evolving helps manufacturers capitalize on plastics trends. So does partnering with an experienced custom injection molder to assist in implementing solutions that help ensure end products perform as intended, and get to market when needed. Read our guide, 5 Steps to Get New Injection Molded Products to Market Faster, to learn more.
Subscribe
TO OUR BLOG
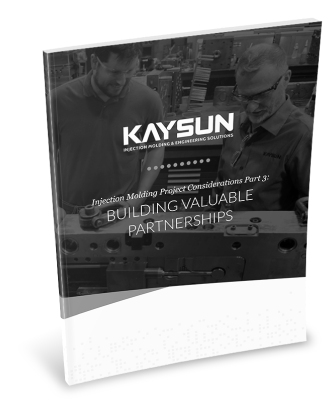
How Do Injection Molder Partnerships Influence Project Costs?
You Might Also Like...
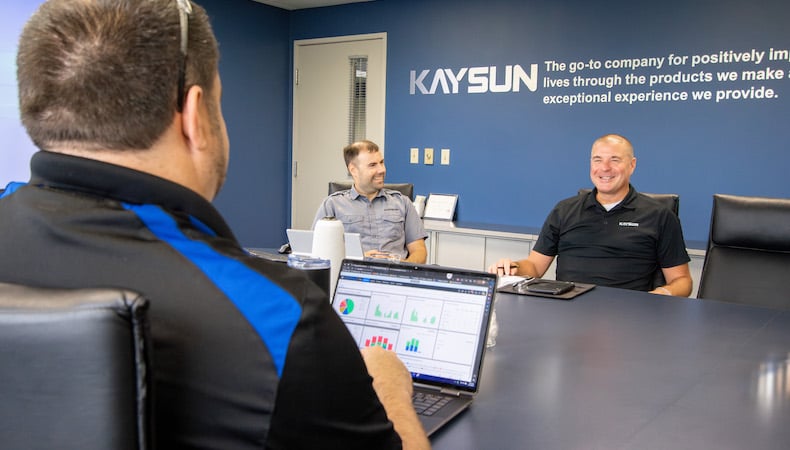
Top 3 Custom Injection Molding Trends to Watch in 2025
Despite being considered more energy efficient and producing less waste than other…
READ MORE
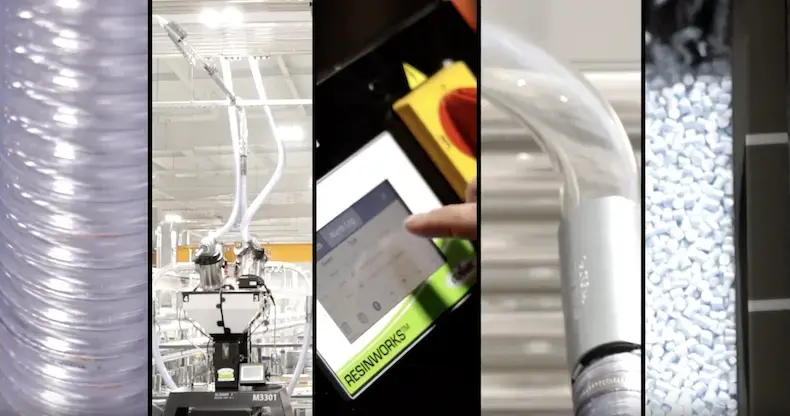
How Centralized Material Handling Streamlines Injection Molding
We consistently look for new ways to deliver timely service and top-quality parts …
READ MORE
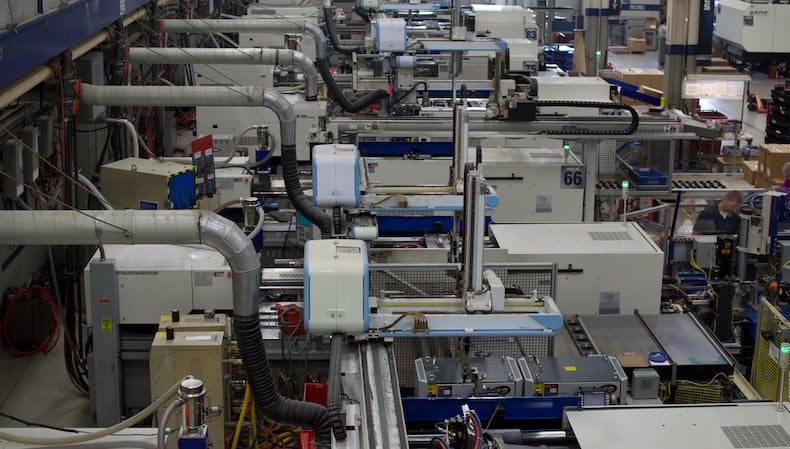
Top 14 Benefits of Injection Molding
OEMs across many industries enjoy the benefits of injection molding. It’s ideal fo…
READ MORE