3D Printing vs Injection Molding – Which is Better?
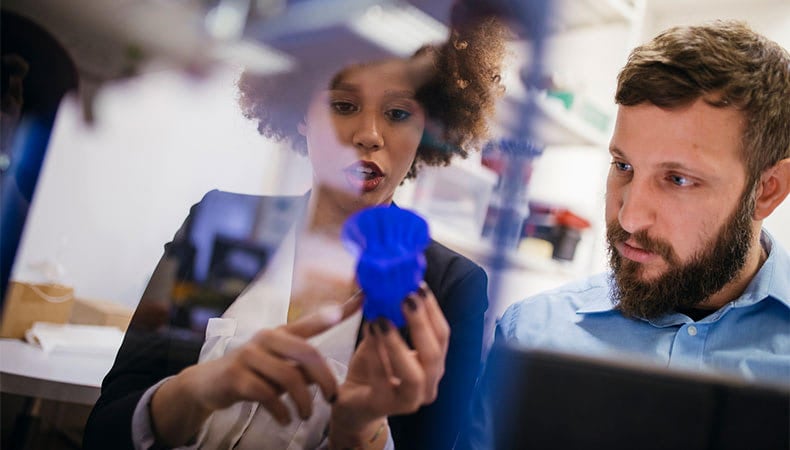
Today’s manufacturers often see a battle when weighing options for producing complex plastic parts and components: 3D printing vs injection molding. While originally considered competing technologies, these techniques are now each largely recognized as having unique advantages and can even be used together to help optimize production efficiency.
For OEMs considering a 3D printer for making plastic parts or simply wondering how it stacks up against plastic injection molding, we’ll explain when to use each technique and how they can be used collectively to support one another.
3D PRINTING VS PLASTIC INJECTION MOLDING: WHEN TO USE EACH
3D printing and plastic injection molding are each helpful processes in their own right. 3D printing has given engineers the power to create plastic designs at their desks and bring them to life in a matter of hours. Injection molding, on the other hand, is the go-to for quality and value. It is commonly used to quickly and reliably produce high-volume runs of complex plastic designs.
3D Printing is BEST SUITED For:
- Quick turnaround times (1-2 weeks)
- Low volume production runs (100 parts or fewer)
- Designs with frequent changes
- Relatively small plastic parts or components
PLASTIC Injection Molding is BEST SUITED For:
- Longer turnaround times (5-7 weeks for simple parts)
- High volume production runs (1,000+ parts per run)
- Final part design (no more prototyping)
- Parts of any size or complexity
Alternatives to injection molding, especially innovative and experimental 3D printing, have been grabbing recent headlines. But, the reality is that the majority of today’s plastic parts are manufactured using plastic injection molding. The choice is understandable given how the process helps OEMs control quality, costs, and design complexities such as tight tolerances.
Tooling Design
Tooling design is one of the most expensive and time-consuming parts of the injection molding process. It is also an opportunity for some injection molders to leverage 3D printing to create tools during prototyping that help reduce development time and lower tooling costs. Stereolithography (SLA) 3D printing, for example, can be a cost-effective alternative to metal tool fabrication, as SLA parts are fully solid and isotropic, and can withstand the pressure of low-volume molding.
For larger volume production runs and more precise molds, however, traditional tooling remains the best option. Likewise, if a part requires the use of thermoplastics, metal tools are the best option to handle resins with melting temperatures at or exceeding 500°F.
Custom PLASTIC Part Design
Due to its ability to create custom plastic part designs and prototypes in a matter of hours or days, 3D printing technology has exploded in popularity. The medical industry, for example, has embraced the quick-turn technology to create custom items like prosthetics, dental products, orthopedics, exoskeletons, bones, implants, artificial heart valves, and more, with researchers even working on 3D organ printing technologies.
That's not to diminish plastic injection molding's contributions and ongoing demand within the medical community. The value of consistently producing large quantities of defect-free, complex medical devices and components simply cannot be underestimated.
Viewing 3D printing and plastic injection molding as complementary instead of competing technologies is beneficial for OEMs and molders alike. Combining these two techniques as situations warrant can ultimately help shorten pre-production iteration cycles and allows for better testing, manufacturing, and outcomes. Interested in learning more about how the tool qualifying process helps to ensure quality outcomes? View our infographic.
Subscribe
TO OUR BLOG
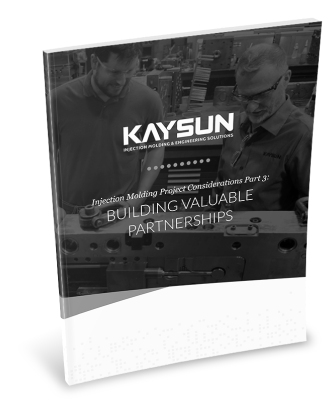
How Do Injection Molder Partnerships Influence Project Costs?
You Might Also Like...
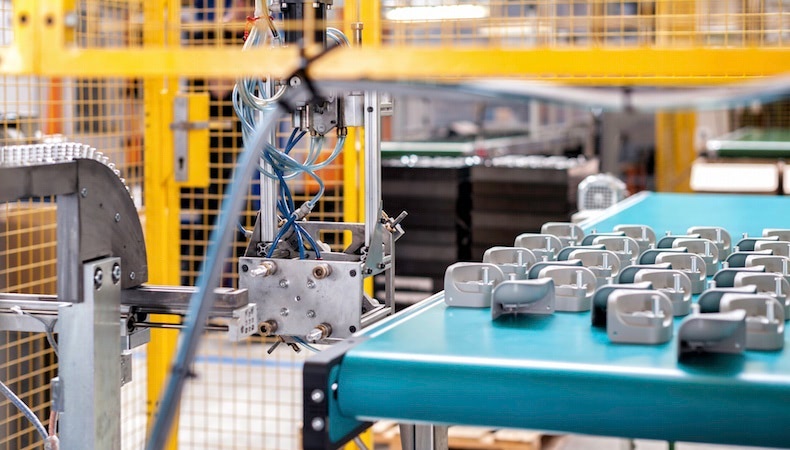
The Impact of Non-Uniform Injection Molding Wall Thickness
Shrink rates for plastic parts vary depending on the materials used and the unifor…
READ MORE
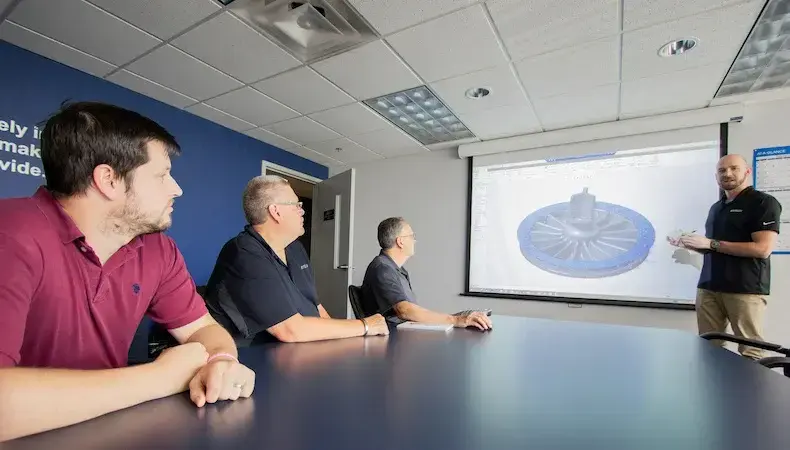
5 Engineering Factors That Improve Your Injection Molding Project
In many complex industries, decisions about which injection molder to use for cust…
READ MORE
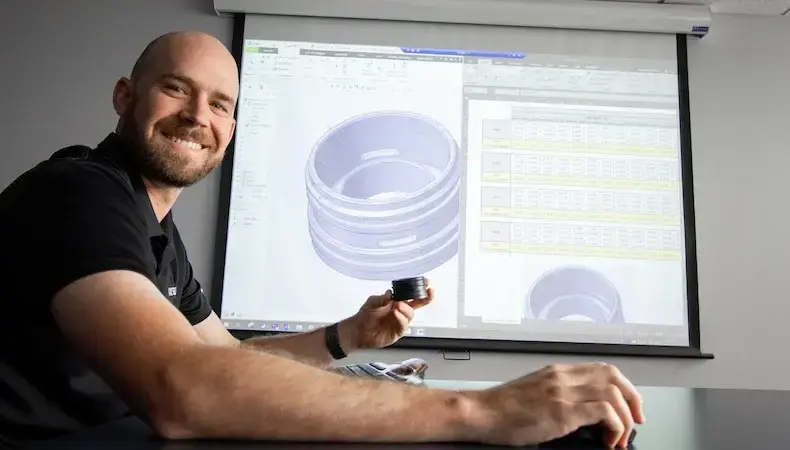
Why Continuing Plastic Engineering Education Matters to OEMs
Technologies, product needs, and customer expectations are rapidly advancing. OEMs…
READ MORE