Move Over Metal: Why Auto Makers Are Rethinking Injection Molding
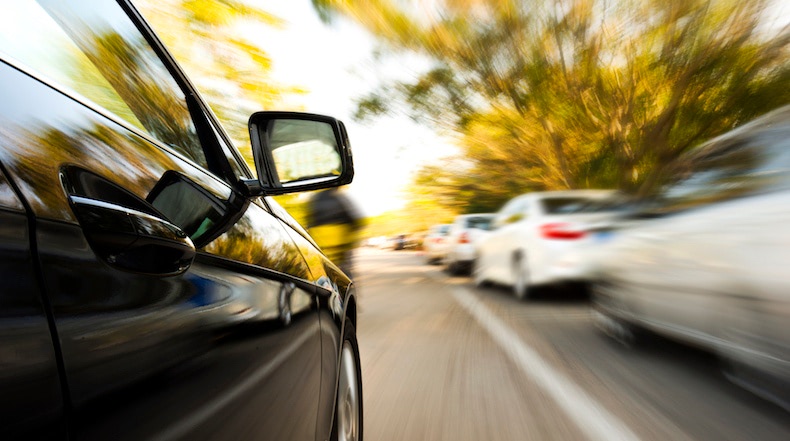
In 2012, President Obama finalized standards to increase fuel efficiency in cars and light-duty trucks to nearly 55 mpg by model year 2025, with the aim of saving Americans more than $1.7 trillion at the gas pump and reducing U.S. oil consumption by 12 billion barrels.
While there are several ways to meet this mandate, reducing the car’s weight is one of the best – and easiest – ways to improve fuel economy without impacting other design and safety factors. That's why many automakers are rethinking production and using custom injection molded plastic components instead of metal assemblies.
Plastics in the Automotive Industry: A New Perspective
There was a time when plastics in the automotive industry were considered a cheap, alternate material for non-critical automotive components. However, advancements in plastics have put them on par with metal in many cases, and metal to plastic conversion has gained proven acceptance. Plastic’s physical properties of heat and chemical resistance, high strength, impact strength, and molding ease offer automotive engineers design flexibility unheard of in past generations, including how they approach exceptionally complex vehicle systems — like powertrains and transmissions — to reduce weight and lower assembly costs without compromising functionality.
Unlike with metal, materials suppliers can tailor the performance characteristics of plastic resins to meet a designer’s particular needs, adjusting additives, fillers and fiber reinforcements to align with specific requirements. For example, polyetherimide is a preferred plastic in under the hood applications because of its superior dimensional, heat, and creep performance. Plus, a single injection-molded piece of nylon can replace several steel components, making it a value-add to the bottom line.
Auto Manufacturing: An Injection Molder's Role
These newly developed raw plastic materials can present a challenge for automotive engineers from design through production if they aren't working with an experienced injection molder. Many of the resins are either carbon or glass fiber reinforced (anywhere from 5% to 60%), increasing the need for specialized tooling, processing and part design techniques.
Partnering with an experienced injection molder gives automakers access to the input and design guidance required to align materials with the project, and the advanced techniques like scientific molding for achieving exacting performance specifications and tight tolerances in injection molded plastic components that weigh less, but don't weigh down production.
For more on how plastic components and experienced injection molders are helping automakers cut vehicle weight, production time and costs, read Converting Metal Automotive Components to Plastic: A Manufacturer's Guide. Click the button below to access your copy.
Subscribe
TO OUR BLOG
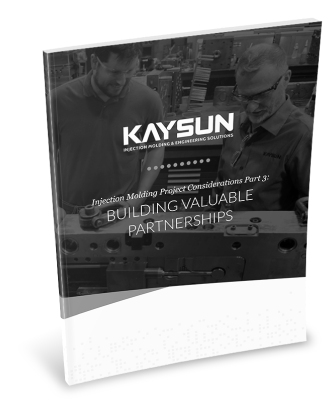
How Do Injection Molder Partnerships Influence Project Costs?
You Might Also Like...
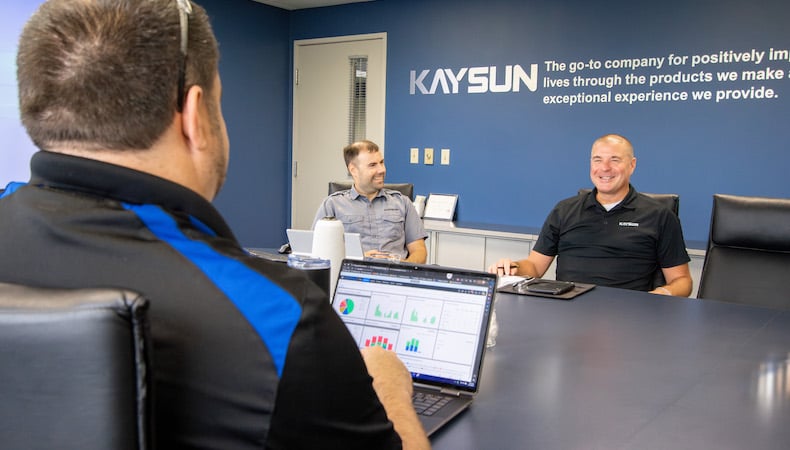
Top 3 Custom Injection Molding Trends to Watch in 2025
Despite being considered more energy efficient and producing less waste than other…
READ MORE
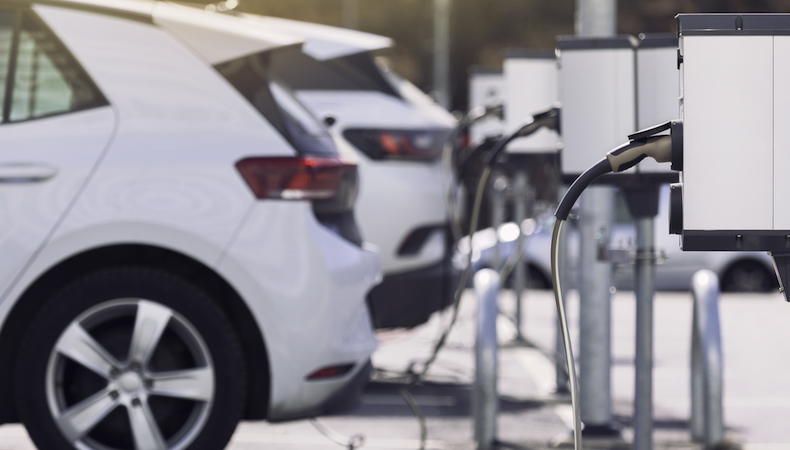
Gas or Electric: Do Vehicle Power Sources Impact Automotive Plastics Selection?
Environmental protection and the legislation surrounding it have heightened people…
READ MORE
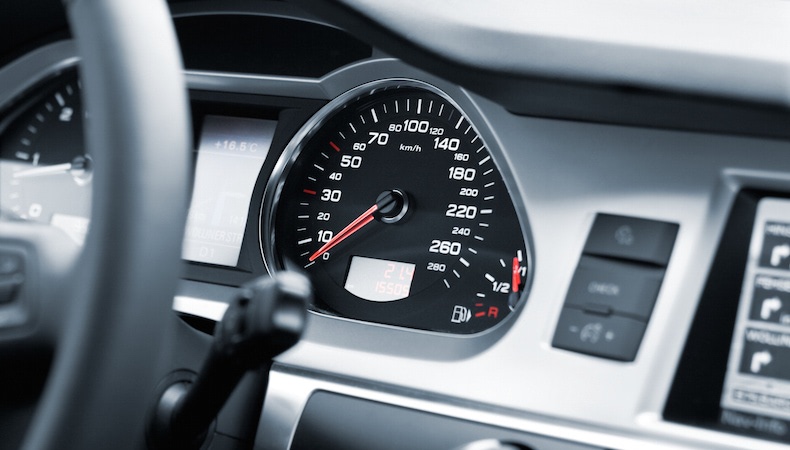
4 Automotive Plastic Parts Trends That Are Redefining the Industry
By 2024 the need for automotive plastics, parts, and innovations will push the val…
READ MORE