Is Injection Molding the Right Fit for Your Plastic Component Project?
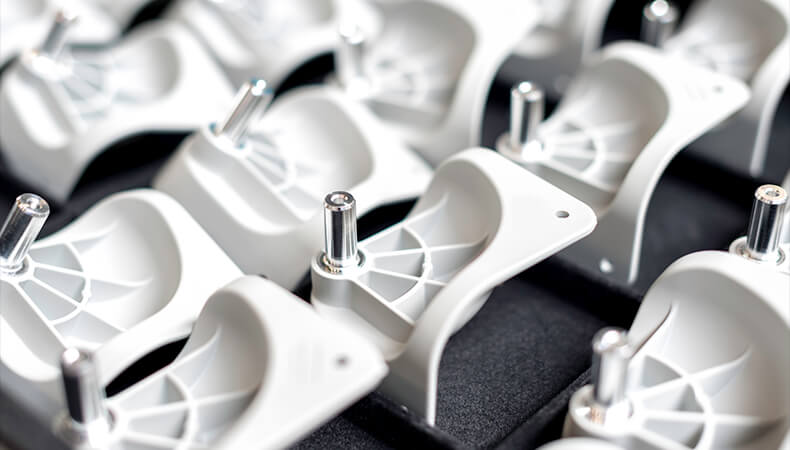
In many industries, injection molding is a proven solution to complex plastic part engineering and design challenges. However, not all projects are well-suited for the process and will not fully benefit from injection molding efficiencies.
A project’s characteristics largely dictate if it’s a good fit for injection molding. Using the lists below, evaluate your current or upcoming project to determine the appropriate process:
Most Acceptable Projects for Injection Molding
- Large annual volume productions that justify the injection mold tooling investment
- Component design geometries that involve complex designs and shapes
- Critical-use applications that require precision, extremely tight tolerances and a consistent, exceedingly high level of quality
- Part consolidation or metal-to-plastic conversion opportunities that streamline production and may also address industry mandates, like vehicle lightweighting faced by automakers
- Applications constructed from expensive material(s) that would result in excessive waste and significant budgetary concerns if machined
- Projects where part design will not change over several years, thereby maximizing the value of the mold tooling investment
- Applications where surface finish is a factor, as injection molding can yield glossy surfaces or a wide variety of textured surfaces
Projects Not Suited for Injection Molding
Injection molding processes aren’t cost effective for some project types, such as:
- Parts with large variations in wall thicknesses as this results in quality problems like warping and reduced mechanical strength. Additive manufacturing or machining parts are better alternatives in this case.
- Low annual volume productions that cannot support the mold tooling expense. Additive manufacturing or machining parts are better alternatives in this case.
- Most hollow parts. While injection molding can be used for these applications, the welding necessary to join pieces post-molding adds to project complexity, cost and time. Blow molding is typically used for high annual volume productions, and rotomolding is typically used for very large and/or low volume applications (think kayaks or underground gas tanks).
Alternatives to Injection Molding
Since injection molding isn’t a universal solution, a logical question is which type of molding is appropriate for certain projects. Generally, the method is decided by product construction. For example, blow molding might be best for projects with hollow parts; compression molding for thermoset parts; extrusion molding for parts with a continuous cross-sectional shape; rotational molding for large, hollow parts; and, additive manufacturing or machining for low annual volume productions.
Pairing an appropriate injection molding project with an experienced molder that has deep design and engineering knowledge, like Kaysun, is your surest path to success.
Learn more in our case study, Why Molder Experience Matters in Life-Saving Applications. Click the button below to access your copy now!
Subscribe
TO OUR BLOG
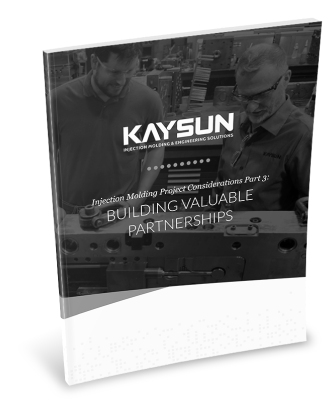
How Do Injection Molder Partnerships Influence Project Costs?
You Might Also Like...
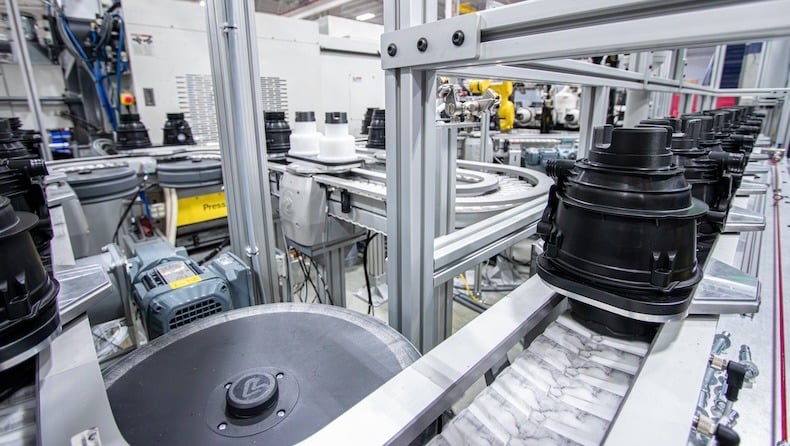
Kaysun Integrates AI on the Production Floor with RJG CoPilot
Industry 4.0 has made manufacturing more dynamic than ever before. Merging IoT, AI…
READ MORE
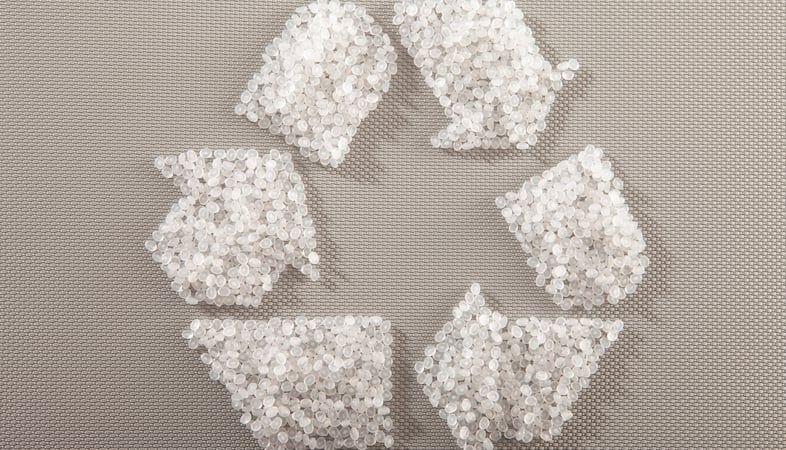
How Kaysun’s Culture of Sustainability Benefits OEMs and The Planet
Injection-molded parts and products are staples for OEMs in industries ranging fro…
READ MORE
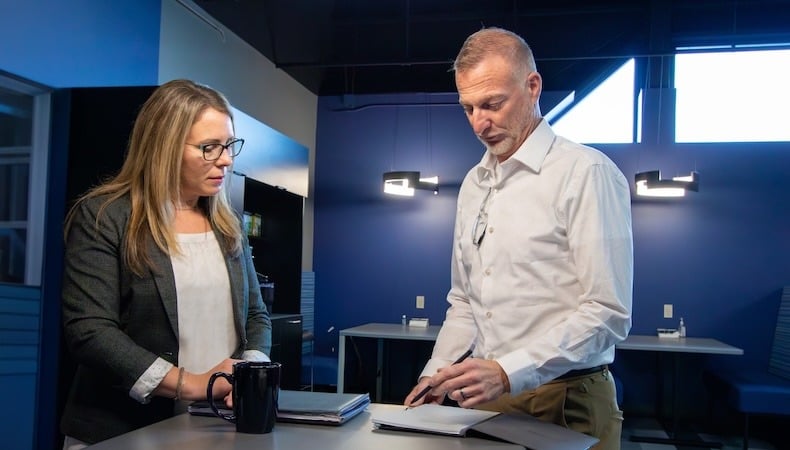
12 Common Injection Molding Questions — Answered!
Injection molding is a versatile and precise process, making it ideal for OEMs tha…
READ MORE