Designing for Medical Device Assembly
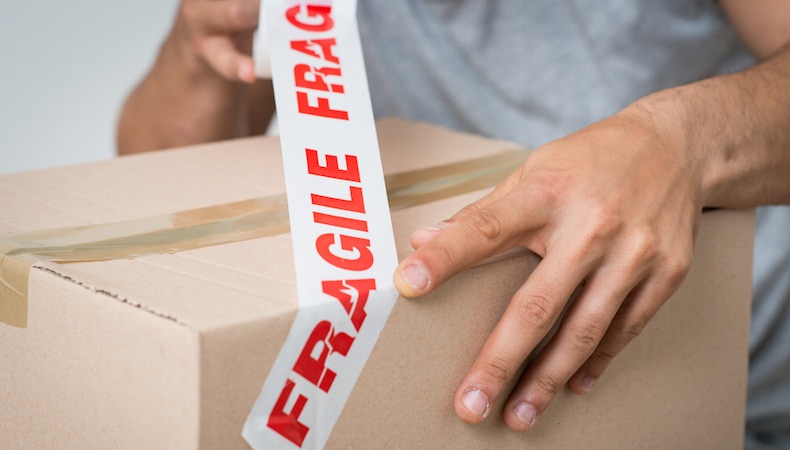
There is no room for error when designing critical-use medical devices and equipment. Taking a holistic view of the part/component during the design phase—including assembly implications—allows for a thorough understanding of how all of the factors involved impact the end product. It also helps injection molders identify and correct injection molding defects in engineered plastic components during early project phases, which ultimately saves money and reduces time to market.
To ensure efficiency and quality once the component is assembled into the finished medical device or piece of equipment, design engineers and injection molders must pay close attention to three specific design factors:
Tolerances
The acute use of medical devices and the potential for compromise during automatic or hand assembly necessitate designing for the tightest tolerances possible. The product design must be reviewed for areas that will naturally align during production and assembly, and others that require tighter tolerance to create the appropriate fit. In the case of the latter, designs must compensate for ease of part assembly and the applied force from the machinery for successful outcomes.
Fragility
The assembly process can compromise injection molded plastic parts and components in a variety of ways. If the shape of the designed part is irregular, for example, it may require additional time-consuming steps like buffering, have unreasonably small parts that are subject to breakage, or may cause failure-inducing variability in wall thickness. Further, the injection molding process can introduce component fragility if not done properly. Parts cannot be assembled too soon after molding as they may not be fully cooled which will cause them to stick or warp and be defective. Similarly, parts requiring multiple changeovers are at greater risk of damage from machine mounting and general handling. Given these variables, partnering with a molder like Kaysun that combines a streamlined process and assembly capabilities under one roof is ideal.
Special Conditions
Medical applications are often heavily regulated and devices/products must follow strict protocols. To that end, prints often include special parameters that need to be called out early on in the design phase so accommodations can be made. For instance, highly sensitive, “no touch” product areas like the needle end of syringes or bodily fluid tubes must remain sanitary and, therefore, are not candidates for automatic assembly. Likewise, device grip and handling may be paramount. Overmolding then figures into design, and adjustments need to be made for inclusion of silicone for rubber handles or tabs.
Experienced injection molders, like Kaysun, that are aware of the importance of these design considerations can complement engineering expertise for the successful design, manufacture and assembly of critical-use medical devices and equipment. Explore more in Designing Plastic Parts & Products for Critical-Use Medical Applications. Click the button below to download your free copy.
Subscribe
TO OUR BLOG
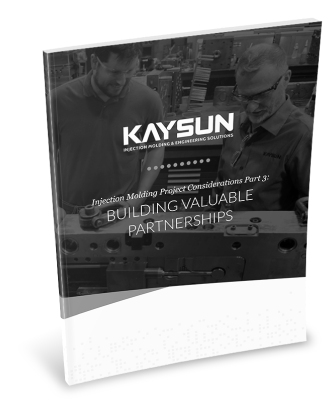
How Do Injection Molder Partnerships Influence Project Costs?
You Might Also Like...
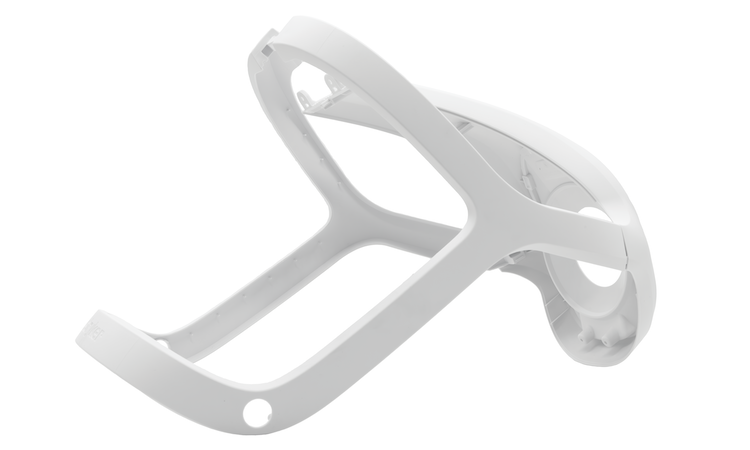
Stryker Turns to Kaysun for Steri-Shield® 8 Helmet Solution
When Stryker set out to develop its next-generation Steri-Shield® 8 Personal Prote…
READ MORE
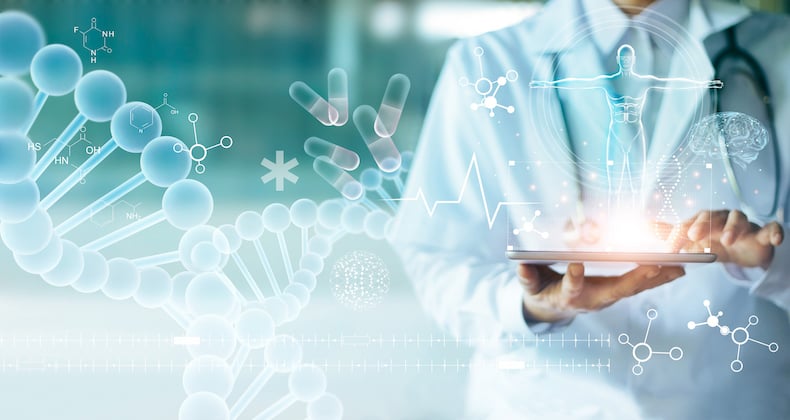
How MD&M West 2024 Keeps MedTech Professionals Ahead of the Curve
MD&M West is one of the largest and most respected medical device trade shows …
READ MORE
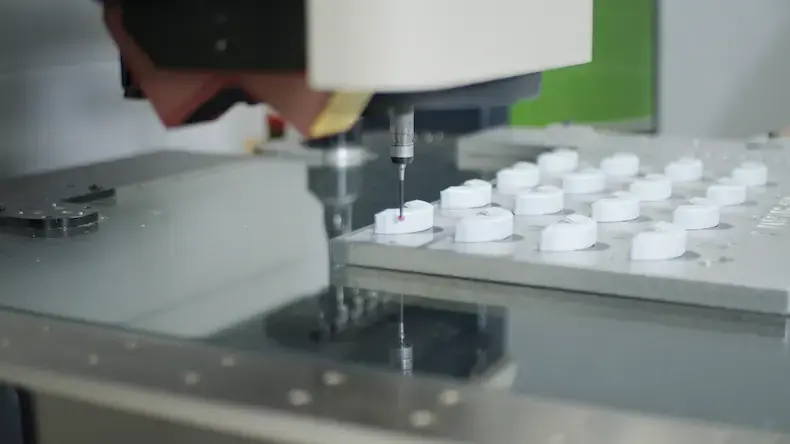
How MedAccred Accreditation Helped Kaysun Enhance Processes & Quality Systems
When you operate at the top of your game, reach higher. Kaysun had already shown i…
READ MORE