Top 5 Injection Molding Defects in Medical Applications
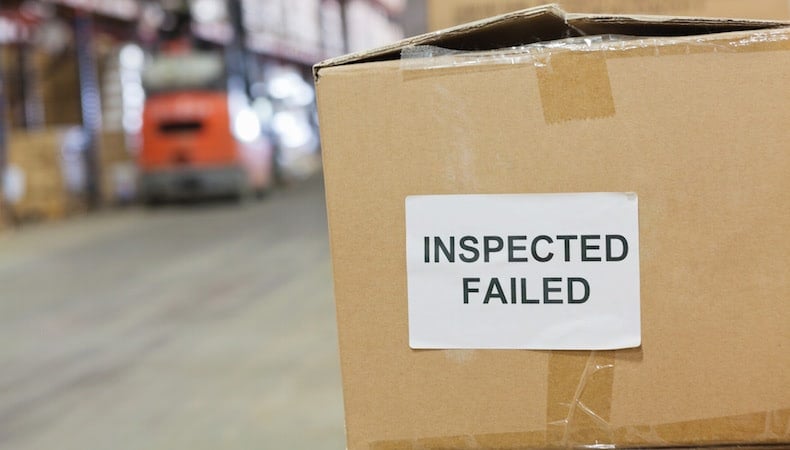
Complex injection molders entrusted with producing plastic components for medical and other critical-use applications assume a high degree of responsibility to ensure the device performs properly, without fail in sometimes life-endangering situations.
A molder’s experience will dictate how well they understand what can go wrong in the molding process and how to troubleshoot injection molding defects for critical-use medical applications. Kaysun has confronted and resolved a number of molding challenges on behalf of our customers, and we’ve compiled a list of common injection molding defects and their impact on part aesthetics and performance:
Residual Stress results from internal forces that accumulate while a part is cooling in the mold and can’t shrink into a shape the resin naturally wants to, but instead it must conform to the mold. Residual stress often fluctuates due to a tooling or injection molding machine change. The fluctuations are imperceptible visually and, despite dimensions and all other factors being the same, residual stress could cause a part to perform poorly in the field.
Warping is an unplanned and unwanted bend, curve or geometry in a molded part. Warping typically appears either during prototyping or full-scale production, introducing potentially significant increases in project time and cost.
Sink marks are visual, measurable marks — usually in the form of depressions or craters — that appear on a plastic part. Sink marks are not only aesthetically displeasing, they can be detrimental to component functionality and how it assembles to other parts.
Short Shots are voids in a molded part where plastic is physically missing. Short shots form incomplete molded parts that can be misshapen, the wrong size or will not hold correct dimensions — making them unusable.
Flash is liquid resin that escapes from a mold parting line and solidifies on the outside of a part. Flash can be extremely sharp, making general handling dangerous. It can also easily damage packaging or cut through O-rings and seals.
Understanding what can go wrong in the molding process and how those defects influence medical application performance is a top priority for injection molders, but solving them is the true end game. Check out Part 2 of this blog series, where we discuss how to proactively prevent and fix defects in injection molded medical parts and products.
Subscribe
TO OUR BLOG
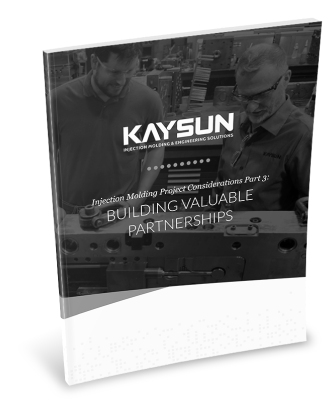
How Do Injection Molder Partnerships Influence Project Costs?
You Might Also Like...
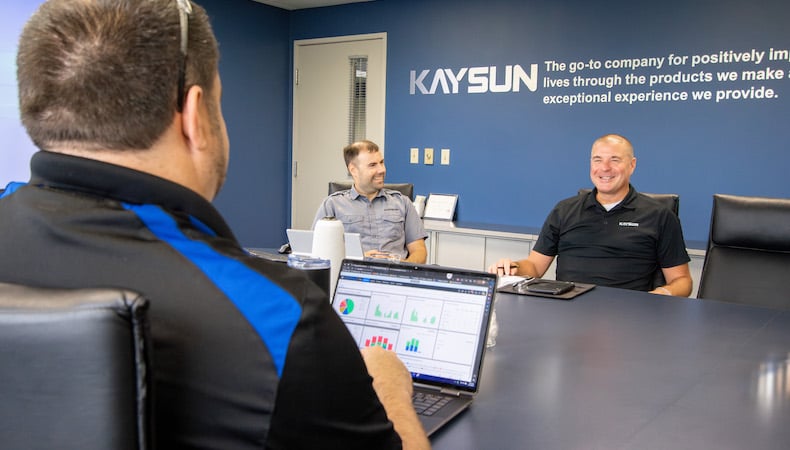
Top 3 Custom Injection Molding Trends to Watch in 2025
Despite being considered more energy efficient and producing less waste than other…
READ MORE
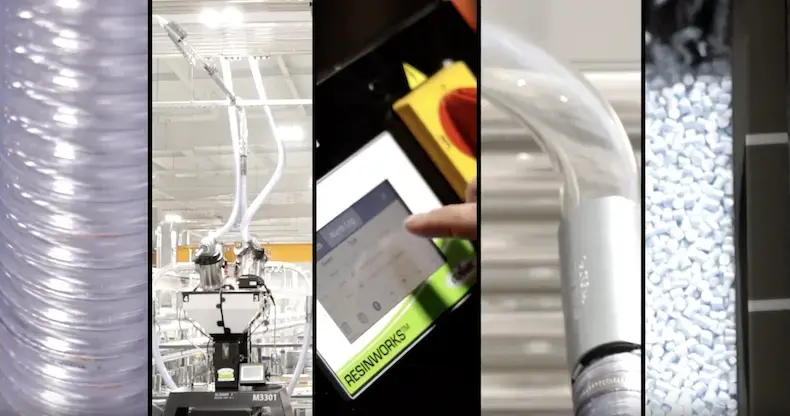
How Centralized Material Handling Streamlines Injection Molding
We consistently look for new ways to deliver timely service and top-quality parts …
READ MORE
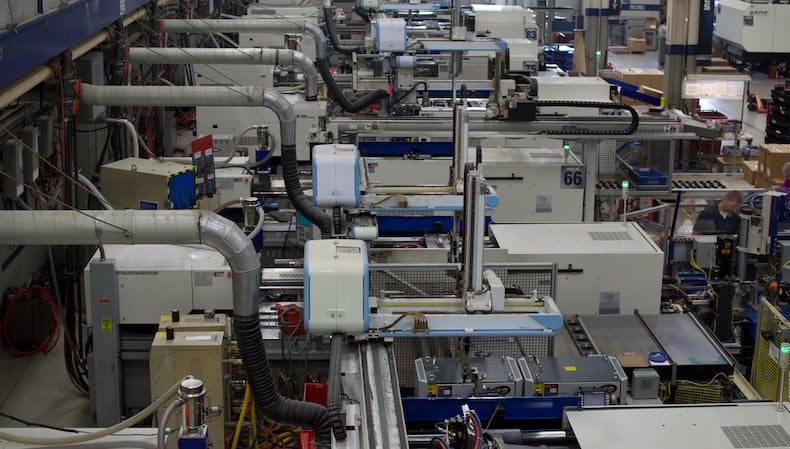
Top 14 Benefits of Injection Molding
OEMs across many industries enjoy the benefits of injection molding. It’s ideal fo…
READ MORE