Engineering Plastics 101: What is Engineering Grade Plastic?
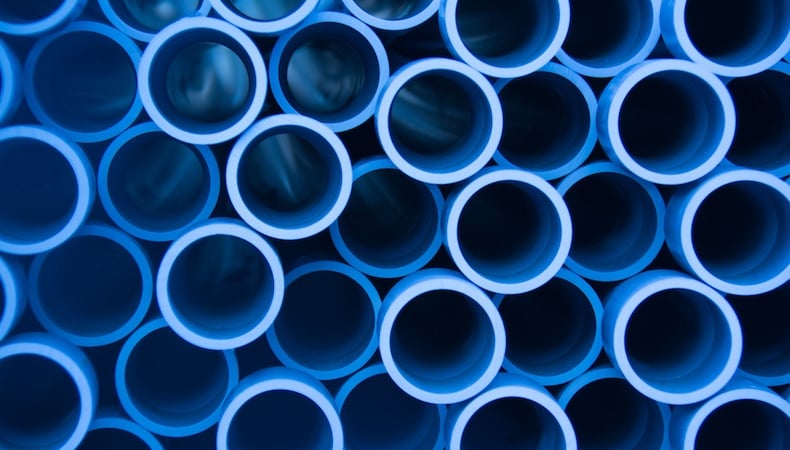
Commodity plastics are versatile materials appropriate for a breadth of applications. However, specialty or custom injection molded parts (required for medical, fire, and safety industries) may contain requirements — chemical resistance, fire retardant properties, mechanical grade strength — that mainstream polymers can’t fulfill.
In these instances, engineering grade plastics (or engineering plastics) are viable solutions that may cost a little more at the outset of a project. Yet, their ability to deliver on unique project specifications and minimize failure risk in engineered plastic products quickly prove their value.
Benefits of EngineerING Plastics
Selecting engineering plastics for medical injection molding and other specialty industrial applications provides a host of advantages that impact the moldability and quality of plastic parts, including:
- Performance characteristics like heat resistance exceeding 100℃/212℉, chemical resistance that spans a variety of substances, and enhanced fire retardancy.
- Malleability when the thermoplastic reaches a specified temperature, which enables moldability and solidification upon cooling that holds tight tolerances and geometries. Further, engineered plastics offer the unique ability to be remelted and formed again — a time and cost saver in the event of revisions.
- Ease in manufacturing as compared to wood or metal, typically providing similar weight and strength as these substances but with the added benefit of being able to be molded into complicated shapes.
Uses for Engineering Grade PlasticS
Many industries combine engineering plastics with complex injection molding production processes to create parts that can withstand varying degrees of handling, exposure, and functionality.
Among the most popular thermoplastic choices for medical applications are:
- Polyether Ether Ketone (PEEK)
- Polyetherimide (PEI)
- Polyethersulfone (PES)/Polysulfone (PSU)
- Polyphenylene Sulfide (PPS)
- Thermoplastic Polyurethane (TPE/TPU)
While these are preferred materials for medical injection molding, it doesn’t preclude the use of engineering plastics that are prevalent in other industries, such as the following (which are listed with examples of typical applications):
- Acetal (POM): springs, bearings, and valve parts
- Acrylonitrile Butadiene Styrene (ABS): car bumpers and dashboard trims
- Polyamides (nylon): bearings, textiles, and automotive applications
- Polycarbonate: electronic components, construction materials, and data storage (also widely used in medical devices exposed to gamma radiation)
- Polybutylene Terephthalate (PBT): electronic components, housings, and automotive connectors
- Polyethylene Terephthalate (PET): infant products, sterilizer lids, and dishwasher parts
Engineering plastics have unique characteristics which are appealing to both medical and heavy industrial manufacturers, especially as it relates to strength, chemical/heat/fire resistance, and durability of plastic injection molded parts. These benefits outweigh the comparatively higher material costs and should be carefully considered for your next critical-use application.
For more information on aligning materials with your product development needs, download our guide, Resin Selection for Industrial Applications. Click the button below for your free copy.
Subscribe
TO OUR BLOG
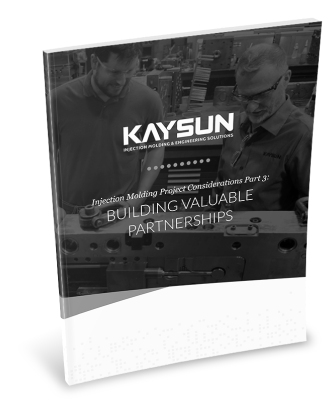
How Do Injection Molder Partnerships Influence Project Costs?
You Might Also Like...
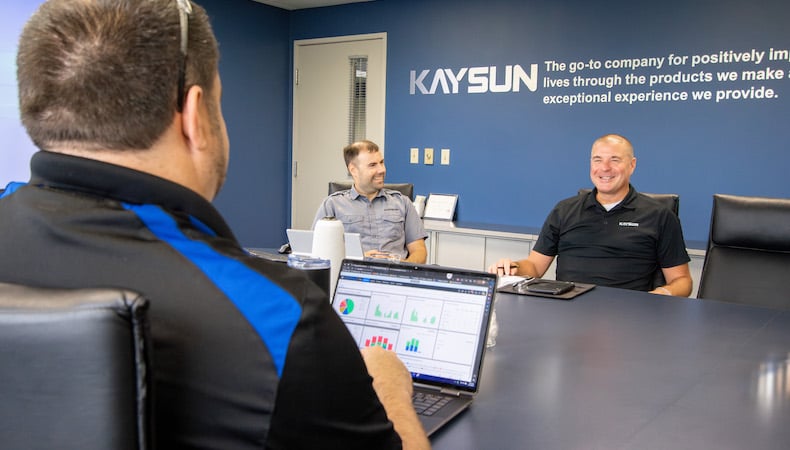
Top 3 Custom Injection Molding Trends to Watch in 2025
Despite being considered more energy efficient and producing less waste than other…
READ MORE
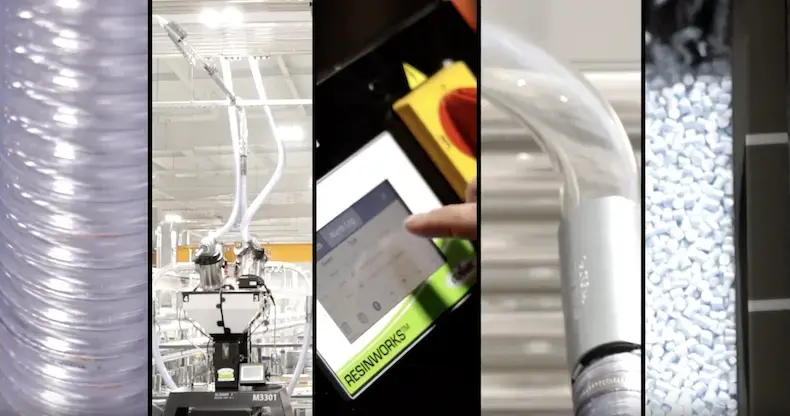
How Centralized Material Handling Streamlines Injection Molding
We consistently look for new ways to deliver timely service and top-quality parts …
READ MORE
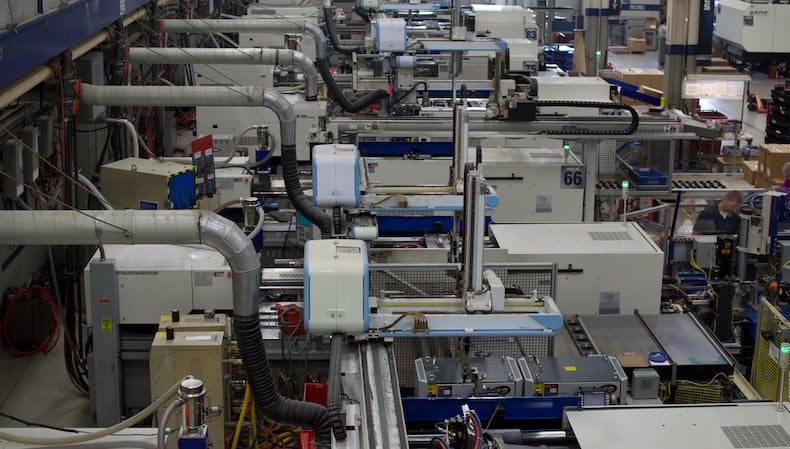
Top 14 Benefits of Injection Molding
OEMs across many industries enjoy the benefits of injection molding. It’s ideal fo…
READ MORE