How Shrink Rate Dictates Injection Molding Outcomes and Part Quality
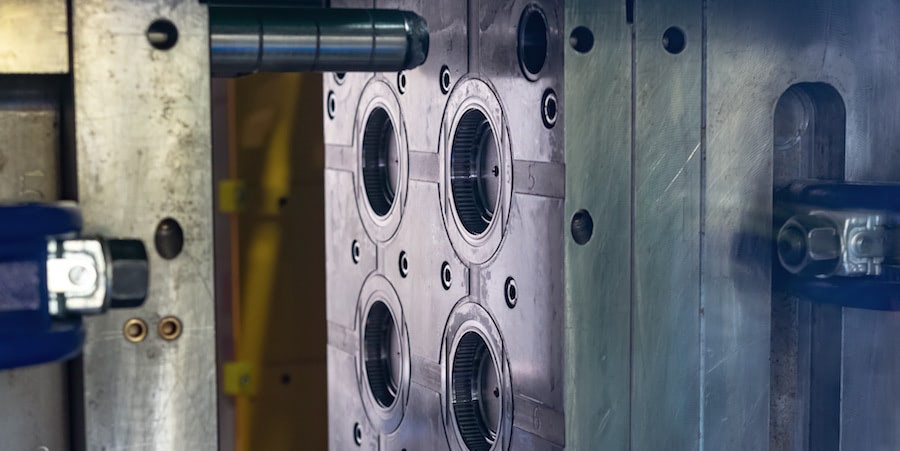
Not taking the time to properly determine shrink rate can have a big impact on the quality of an injection molded part's geometry, performance, and appearance.
To facilitate this calculation, materials suppliers typically provide shrink rate numbers based on ASTM Standard D955 and a .125-inch thick plaque with a specific gating size and location. Although a good place to start, this value is usually not accurate enough for many products, especially critical, highly complex parts.
Factors That Influence Shrink Rate
Wall thickness, gate size, and processing conditions such as packing pressure and tool temperature are major factors in determining part shrinkage. For example, thinner wall sections cool faster, resulting in less shrinkage. Likewise, larger gates have longer packing time and, therefore, less shrinkage.
Shrink rates also vary according to flow direction, which must be carefully analyzed after gate locations are selected. On long, narrow parts — gated at the end, for instance — flow will essentially parallel the length of the part. In these cases, the “in-flow” shrink rate is used for the long dimension. “Cross-flow” shrinkage is used for dimensions that are perpendicular to the long dimension. For parts with random fill directions, an average of the in-flow and cross-flow directions can be used. For injection molded parts with critical dimensions, prototyping is the safest option.
Gating and Shrink Rates
The impact of gating must be given due consideration when determining shrink rates:
-
Gate Location. It is important to have a gate location that provides the most uniform fill and plastic pressure within the cavity. Since shrinkage is proportional to the pressure, having a large pressure drop throughout the part will provide varying shrink rates. This could result in low shrinkage on the end of the part with high pressure, and high shrinkage on the other side of the part with the low pressure.
-
Sprue/runner and gate size. Any premature freeze-off of these items could increase the variation of the packing of the part, resulting in inconsistent shrink rates.
The Best Method for Predicting Shrinkage
The best method for predicting shrinkage is building a prototype tool with the exact cooling and gating as the final production tool. This way, the shrink rate can be exactly determined for the part. An alternative to a prototype tool is running the chosen material in a comparable tool, with a similar wall section and gate scheme. Measurements taken from the tool steel and molded parts can be used to determine a “likely” shrink rate, based on a similar part. Prototyping also provides an opportunity for the tool to be left steel-safe so critical areas can be “tweaked” if needed after a production tooling process is established.
Want to learn more about tooling design? Be sure to read ourTooling Design for Injection Molding whitepaper below!
Subscribe
TO OUR BLOG
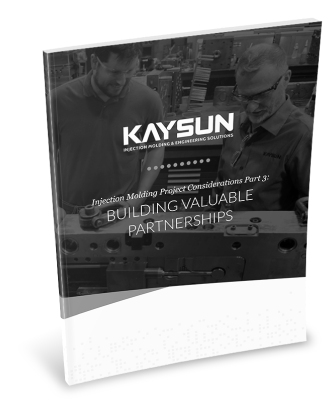
How Do Injection Molder Partnerships Influence Project Costs?
You Might Also Like...
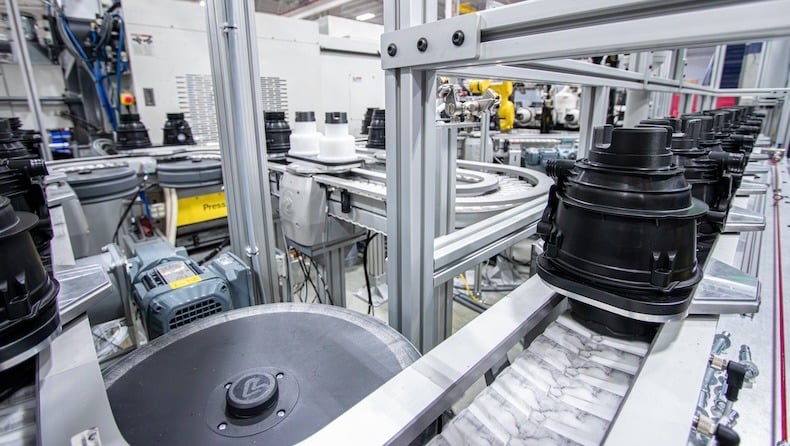
Kaysun Integrates AI on the Production Floor with RJG CoPilot
Industry 4.0 has made manufacturing more dynamic than ever before. Merging IoT, AI…
READ MORE
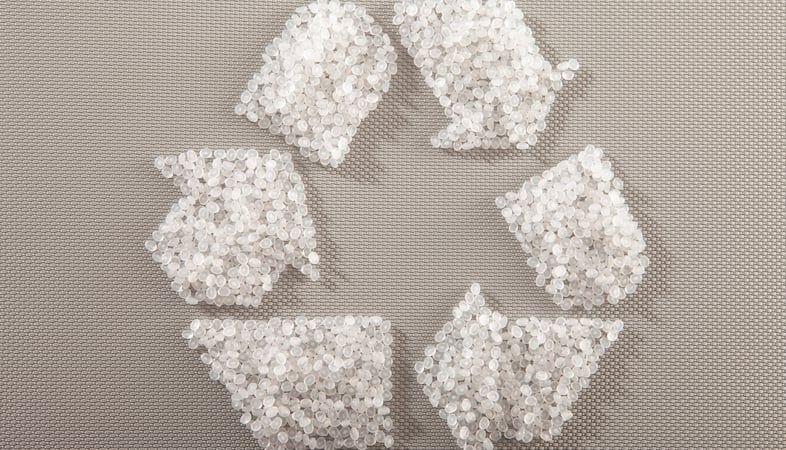
How Kaysun’s Culture of Sustainability Benefits OEMs and The Planet
Injection-molded parts and products are staples for OEMs in industries ranging fro…
READ MORE
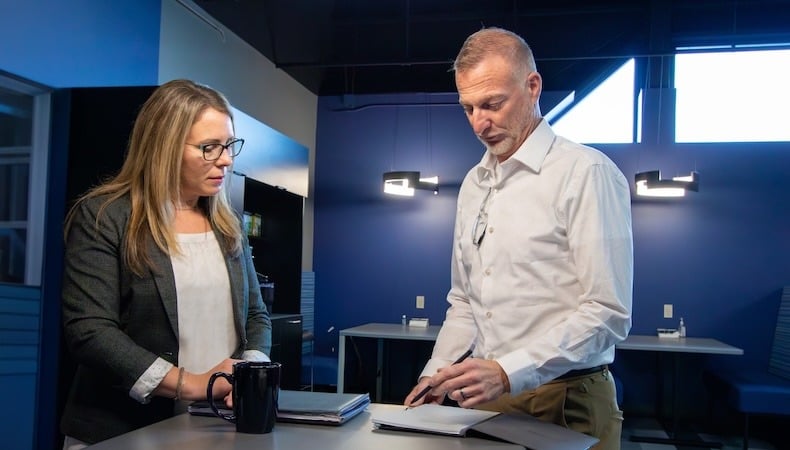
12 Common Injection Molding Questions — Answered!
Injection molding is a versatile and precise process, making it ideal for OEMs tha…
READ MORE