How Plastics Improve Military Technologies and Safety
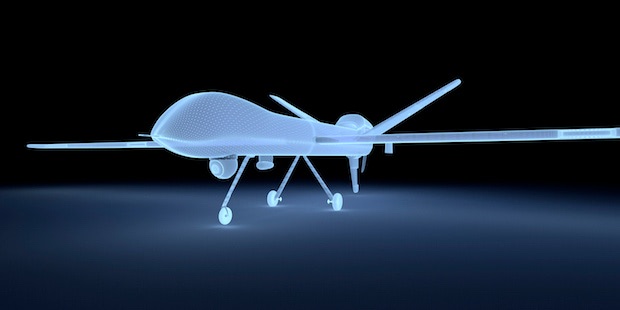
Light weighting for military applications has been a key focus for many defense contractors. Significant strides have been made in converting many components of armed forces gear from metal to plastic, reducing per-soldier equipment loads by as much as 50% while allowing service members to remain lithe, agile – and, above all, safe – when engaged in maneuvers or combat.
Plastics are changing the technological battlefield, too. Experienced, full-service molders like Kaysun are increasingly being called upon to devise, develop and produce complex injection-molded plastic components that make defense and public safety communications technology work smarter in the field and more economically in budgets – all without jeopardizing user welfare or supply chain continuity.
Here are some of the latest innovations in military and public safety gear and machinery brought about with the help of injected-mold plastic components:
Enhanced stealth
Remaining undetected gives fighting forces an upper hand, but traditional metal machinery leaves large electromagnetic radar/sonar echo signatures and infrared heat source footprints. A variety of non-conducting and insulating resins have been introduced to increase the stealth capabilities for military applications:
- Domes constructed from polymer matrix composites shield detection equipment and deaden position-revealing vibration on military ships and aircraft
- Military helicopters outfitted with multi-spectral stealth capabilities (radar, infrared and acoustic) like polymer foam blades and Kevlar-carbon fiber structural materials
- Flexible, polymer matrix-based coatings used on a number of military vehicles to thwart “normal” and “thermal” visual detection
Reinforced vehicle armor
Multi-layered steel/resin/fiberglass composite and matrix polymer ceramic panels have been used on tanks since the Cold War. Since then, layers of titanium, Kevlar and rubber have been added to vehicle armor to reduce weight but increase protective properties.
Advanced field gear
Kevlar has long been the standard bearer in military and public safety personnel protection, but plastics are playing a part in new approaches:
- A colloid blend of silica nanoparticles and polyethylene glycol (PEG) is being tested as a type of “passive and intelligent” body armor, meaning it is semi-viscous when equipment is not in active use, but hardens immediately upon impact
- Body suits with wireless connectivity act in tandem with explosion-resistant headgear that has advanced helmet-mounted displays, cameras and night vision to give soldiers a technological bump – they can “see” through the eyes of anything directly linked to their suits, be it a surveillance satellite or a launched drone
Location Recognition
Military personnel and first responders are often in perilous situations that leave them vulnerable and not always visible. Several GPS-based products currently exist to find people within structures, but outdoor location detection is lacking. The advent of Internet of Things (IoT) connectivity has led to the development of Artificial Intelligence (AI) that collects data about temperatures, gases and other danger signals that are transmitted to users through handheld or wearable sensors to help guide them safely through environments and keep tabs on their location and condition.
Drones
Unmanned flying devices (drones) offer technology and construction that is being adapted to automated and remotely controlled jet fighters. These next generation aircraft – stealth drones – are lightweight and polymer-shielded so as to be virtually “invisible” to enemy radar.
Defense contractors are responsible for giving military and public safety personnel the tools they need to efficiently and safely do their jobs, making a partnership with an experienced, complex injection molder particularly important. Before your next project, download our tip sheet, What Type of Injection Molder Do You Need? to evaluate and align injection molder capabilities with your design, development and production needs.
Subscribe
TO OUR BLOG
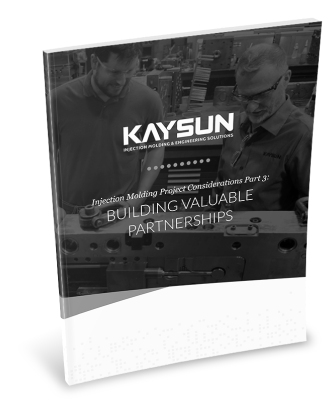
How Do Injection Molder Partnerships Influence Project Costs?
You Might Also Like...
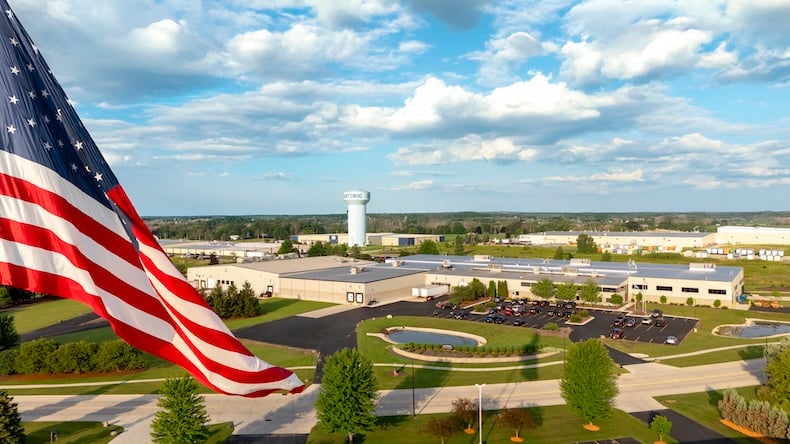
4 Ways Reshoring Strengthens an OEM Supply Chain Strategy
TL; DR (Quick Article Summary) Why is reshoring a smart OEM supply chain strategy?…
READ MORE
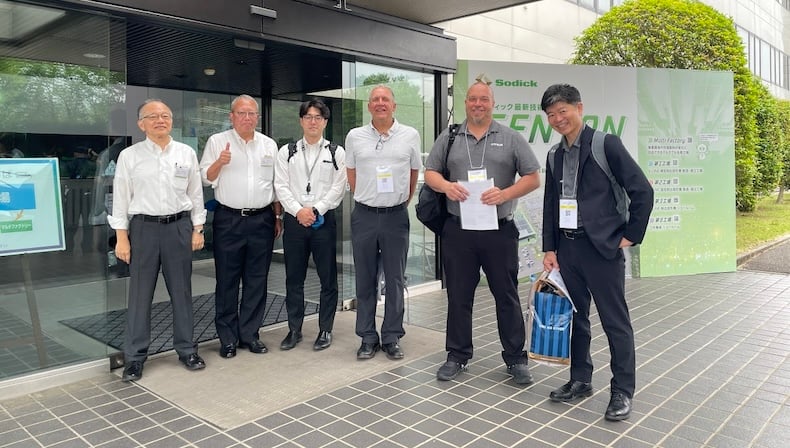
Kaysun and Sodick: A Partnership Built on Precision, Proven by Performance
Precision presses are central to producing injection-molded parts for complex appl…
READ MORE
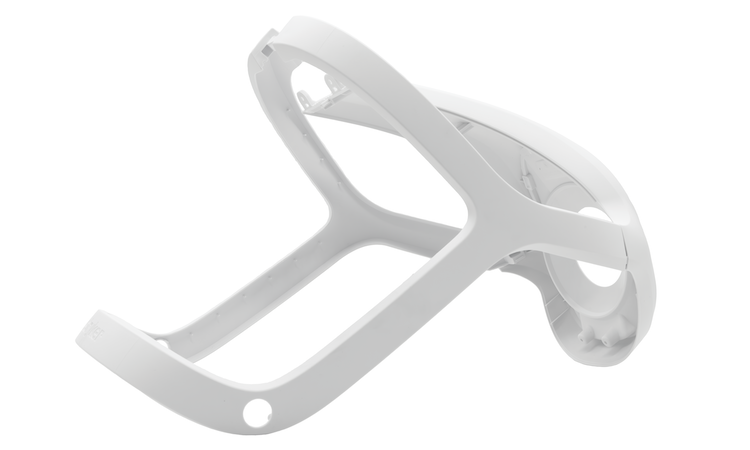
Stryker Turns to Kaysun for Steri-Shield® 8 Helmet Solution
When Stryker set out to develop its next-generation Steri-Shield® 8 Personal Prote…
READ MORE