Advanced Plastics Make Vehicles Efficient, Affordable & Attractive
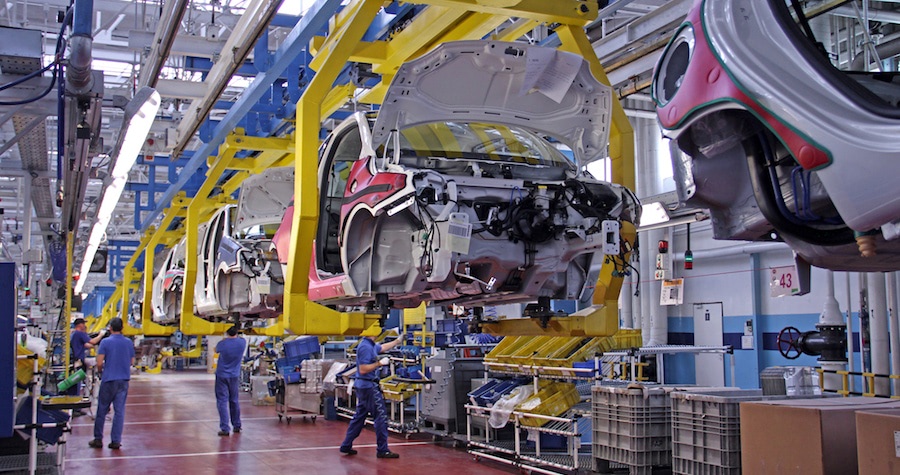
When engineering-grade resins were introduced in the 1950s, some auto manufacturers were unfamiliar with the benefits of metal-to-plastic conversion, i.e. how to design plastics into products, and how to manufacture with plastics. Today this practice, also known as “lightweighting,” is becoming increasingly popular with automakers as they race to comply with a federal mandate calling for automobiles to average 54.5 miles per gallon by 2025.
Converting existing metal products or parts to plastic increases fuel efficiency because metal is far heavier than plastic and, with proper design, engineered plastic parts can be just as strong as metal and cost less. Plastics’ chemical resistance and heat resistance, combined with their lighter weight, make them especially useful for fuel systems, fluid handling systems and other under-the-hood, high-temperature applications.
With developments in materials and technologies, plastics like polyether ether ketone (PEEK) are being used for vehicle body components and an increasing number of working parts. Some common applications include piston rings in automatic transmissions and wear plates in gear systems.
Other engineered plastics have dampening qualities that absorb vibration better than metal, and can be formulated to be thermally and electrically conductive. This makes them ideal for use in electromagnetic interference (EMI), radio frequency interference (RFI) shields, and acceptable for certain types of heat sinks.
Metal-To-Plastic Conversion a Plus for the Automotive Industry
With appropriate design, plastic parts can perform as well as metal in many automotive applications. For example, plastic parts can achieve the same tight tolerances, but require fewer secondary manufacturing operations. Including additives such as glass-fiber and carbon-fiber can help plastics deliver comparable tensile strength in certain components like brackets and exterior panels.
Plastics also exceed metal in several key areas. This includes highly repeatable production with less scrap, up to six times longer tool life, enhanced regulatory compliance, and greater design flexibility.
Until recently, most engineers who worked primarily with metal parts were not familiar with the history or success of reinforced plastics. Here are a few of the reasons why this metal-centric perspective is rapidly fading from the scene.
Lower Cost
Competition has become tough in the global automotive marketplace and operations are squeezed to be lean.
Let’s say you are using a metal part. If a plastic part is just as good as the metal part, if not better, why change to plastic if there’s no compelling performance advantage? The answer is because in addition to meeting specs for durability, strength and style, injection- or insert-molded plastic improves product quality and reduces costs in seven key areas:
- Decreased piece part prices. After covering initial tooling costs, plastic piece part pricing is usually much lower than the same part produced in metal, whether it is a stamped, cast, or a die-cast part, largely because the injection molding process has faster cycle times (more parts made per machine hour).
- Elimination of time-consuming and costly secondary operations. For example, plastic stock can be colored with color concentrates before molding, eliminating secondary painting operations. Similarly, a plastic part can be textured or given various levels of polish by treating the working surface of its injection mold. Assembly also offers opportunities for savings. Fastening metal stampings or castings together is expensive. They can often be replaced by a single injection molded part or one with snap-together components that eliminate welded joints and fasteners that slow production time and introduce failure risks.
- Reduced product weight and improved ease of use. Weight reduction reduces shipping costs and makes the product easier for the end-user to handle. In automotive applications, it helps lighten vehicles to save fuel.
- Greater product structural strength. Plastic parts made with engineering-grade resins can actually be stronger than metal parts. In addition, molding in features such as ribs, bosses and gussets as the part is produced further increases its structural strength without secondary operations.
- Increased product design options. Plastic’s form flexibility makes it easier to design and produce complex parts, especially those requiring tight tolerances and advanced molds or tooling. In addition, high-pressure injection molding allows for constructing thin-walled plastic parts that replace costlier, thicker and heavier features of die-cast metal parts. Prototyping, too, becomes easier with plastics. Inexpensive soft tools can be used to try out different materials and finalize a design before making the substantial upfront investment in hard tooling. Prototype parts may also be easily machined out of plastic stock to reduce materials costs during initial design evaluations.
- Plastic materials can be quickly reused on-site. While steel must be re-smelted at a reprocessing facility, most thermoplastic scrap can be easily processed into “regrind” and mixed with virgin material to save time and up to 40 percent in materials cost. A word of caution: thermoplastics can be reprocessed, but thermoset materials cannot.
- Improved product life. Most plastic materials have greater chemical resistance than most metals. They do not rust or oxidize as metals do, and many are not affected by acids or base compounds.
Plastics Offer Variety and Versatility
There are more than 25,000 off-the shelf engineered plastic materials, each with its own application-specific properties. If needed, higher-performance blends and hybrids can be custom-designed to meet very specific performance requirements. There are several considerations needed to leverage the key characteristics of plastics to best align the material with the project. These include:
- Base material selection: Each base material has its own set of advantages and disadvantages. To determine the ideal material type for your application, identify critical project requirements such as chemical resistance, impact, flow, processing, etc.
- Additives: Plastic additives are used to improve a material’s properties such as strength, rigidity, UV resistance and flame resistance. Some of the most common additives include:
- Long glass fiber additives improve stiffness and strength, increase temperature performance up to 150°C, and create a moderate surface appearance.
- Short-glass fiber additives improve stiffness, increase temperature performance and improve appearance over long glass additives. Glass content of 30% or less allows parts to look comparable to unreinforced plastic parts.
- Carbon and stainless steel fillers improve conductive and/or shielding properties.
- Lubricant fillers improve wear and friction properties.
- Mineral fillers improve electrical performance, weighted feel, sound dampening capabilities, dimensional stability and specific gravity.
- Impact modifiers improve toughness.
- Flame-retardants increase resistance to burning.
Other Design Considerations
Manufacturing Efficiency
Injection molding is faster, more efficient and can achieve higher tolerances compared to making automotive die-cast metal parts. In fact, it is easier to make complex, high-performance parts or products with highly controlled injection molding processes that require fewer steps, especially as it relates to secondary operations, part consolidation and inventory maintenance. In addition, plastic molding tools can last 500,000-1,000,000 cycles longer than those used for die-casting, and require less maintenance and downtime.
Design Freedom
Style is a critical element of automotive designs, and plastics give engineers greater latitude to innovate. By making a wider range of geometrical possibilities possible, plastics help designers think in more creative ways about complex forms, performance in harsh environments, shielding considerations, weight and structural limits, thermal management, and product differentiation—both for performance and aesthetics.
Maintaining Automobile Safety
It’s important to note that directly substituting plastic for metal in a design rarely works because the differences in mechanical properties of plastics and metals will affect product performance. In most cases however, a smart designer can easily compensate for these variations by adding reinforcement features like ribs, gussets, thicker walls and radii.
Determining how a plastic performs in the end-user environment often depends on prototype testing (for example, analyzing post-mold shrinkage and warpage). For automotive safety, it is especially important is to evaluate plastics for strength, hardness, flexibility, corrosion resistance, fatigue and long-term creep. Metals, being much more thermally conductive (without as much hysteretic loss), don’t necessarily present the same challenges. As such, testing needs to be appropriate to capture true fatigue resistance and creep. In general, metal creep does not exist at typical, everyday usage temperatures and loads. On the other hand, if plastic parts are not designed correctly, they can creep, stress or relax.
In conclusion, engineered plastics already offer many advantages, including lighter weight, parts consolidation, net shape components, aesthetic improvements and better durability. Meanwhile, material suppliers continue to develop high-strength thermoplastics that are increasingly resistant to impact, corrosion and heat. As a result, more auto suppliers are converting from metal components to plastic.
Thanks to these advances, plastics are poised to revolutionize automotive manufacturing with improved performance and enhanced manufacturability of complex, mission-critical automotive parts. To learn more, read our whitepaper, Converting Metal Automotive Components to Plastic: A Manufacturer’s Guide, by clicking below.
Subscribe
TO OUR BLOG
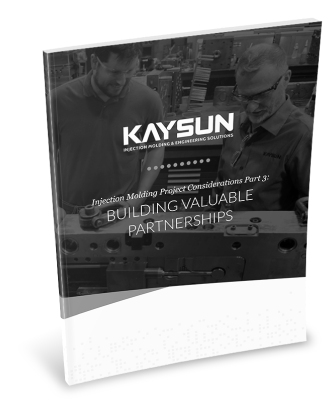
How Do Injection Molder Partnerships Influence Project Costs?
You Might Also Like...
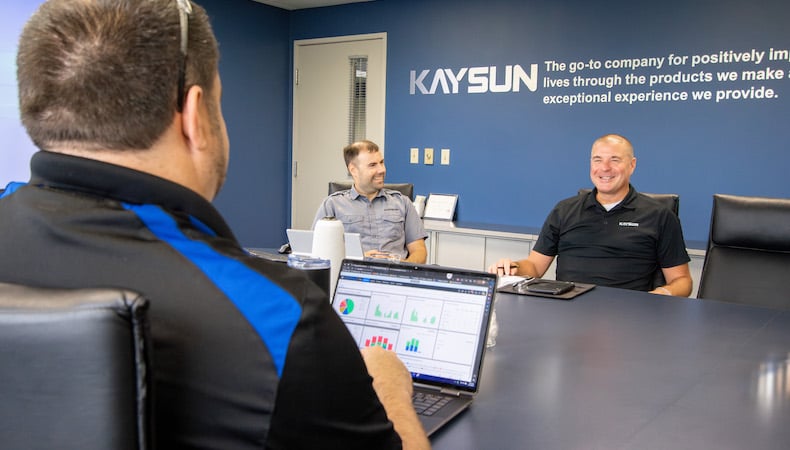
Top 3 Custom Injection Molding Trends to Watch in 2025
Despite being considered more energy efficient and producing less waste than other…
READ MORE
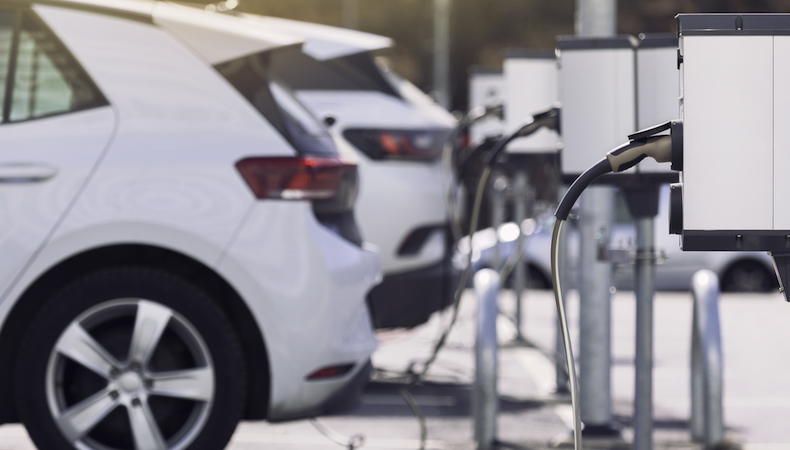
Gas or Electric: Do Vehicle Power Sources Impact Automotive Plastics Selection?
Environmental protection and the legislation surrounding it have heightened people…
READ MORE
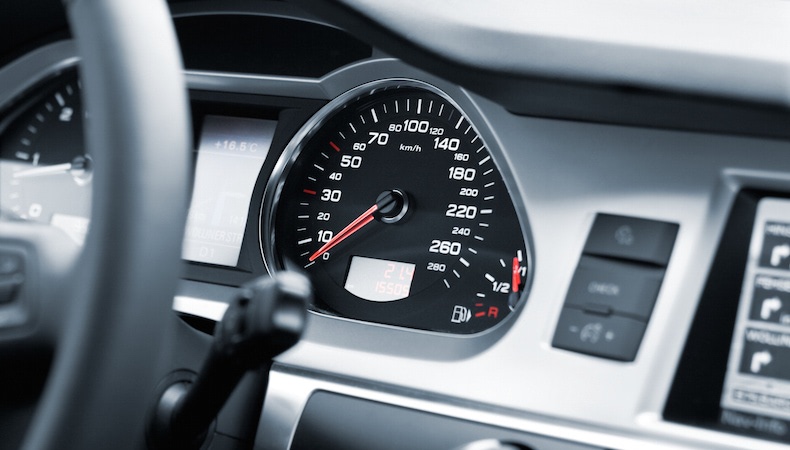
4 Automotive Plastic Parts Trends That Are Redefining the Industry
By 2024 the need for automotive plastics, parts, and innovations will push the val…
READ MORE