Injection Molding Tonnage Calculation: How Clamping Force Drives Quality and Costs

Injection molding is a complex, dynamic system with multiple, interacting factors—all of which impact performance, cost, and quality. One of these factors is the injection molding machine tonnage calculation, also known as the clamping force.
Let's start with the definition of tonnage. This is the measure of force that's required to keep the tool closed during the injection process, and it determines the injection molding machine size required for producing the part. This may seem simple, but a lot is riding on an accurate calculation of tonnage, which is why working with an experienced injection molder is critical to producing complex plastic components.
Impact of Improper Tonnage CALCULATION
A clamping force that is too low likely leads to inconsistent results or defects, including variable size and weight, flash, short shots, wall thickness variations, and irregular surface finish. Too much clamping force reduces the life of a tool by adding unnecessary wear and tear, which ultimately increases production costs to rebuild the tool more frequently.
Machines that deliver high clamping forces are more expensive than machines that deliver lower clamping forces, and a less experienced or commodity molder may not have the right-size machine for your project. Plastics engineers at a custom injection molder can accurately calculate tonnage, ensuring the proper machine is used and eliminating the risk for overclamping.
Cutting Costs with Tonnage Calculation
A tonnage calculation is often presented as a range (for example, from 550 tons to 750 tons for a single-cavity tool). An injection molder can certainly save money by purchasing a smaller machine that can deliver the lowest clamping force in the range and claiming it will do the job just fine. However, if the optimum tonnage calculation is actually in the mid-to-upper part of the range, this increases the risk to you, the manufacturer, that your plastic parts will have flash. Flash is when the tool opens slightly during injection because the machine lacks sufficient clamping force to produce a flash-free part.
Instead of using an injection molding machine tonnage calculator, many molders often estimate tonnage by using a “rule of thumb” equation that involves the area of the part, type of plastic, viscosity, and a “clamp factor” that ranges from 2 to 8. Depending on the part and type of material, some molders simply go with an “average” clamping factor of 5 to calculate the tonnage.
This approach can result in an inaccurate tonnage calculation that is too small (resulting in quality problems and delays) or is too large (resulting in increased mold costs and premature deterioration).
A more accurate way to determine the injection molding machine tonnage calculation is through mold filling analysis, which removes much of the guesswork from the calculation. It’s been our experience that using mold filling analysis to determine the tonnage factor, and then adding a “safety factor” of about 15 percent, results in a highly accurate clamping force and flash-free parts.
Mold Filling Analysis' Effect
Mold filling analysis is also an effective method for determining the impact of other production variables, such as number of gates (more gates will lower tonnage requirements) and flow length (longer flow lengths require higher pressures and therefore a higher tonnage). Using mold filling analysis early in the design process also helps determine the best gating scheme for the mold.
Be cautious of the flow simulation analysis software you use, as it may only provide the pressure needed to fill the part; it may not always include the pressure during the pack phase. This can be a drawback. Tonnage requirements are also a function of the pressure required to fill or pack the part. It is often easy to fill the part when using an easy-flowing material like nylon. In these cases, flow simulation analysis software will show low pressure. However, this cannot be used for the tonnage calculation because the higher packing pressure still needs to be applied to eliminate sink. If the packing pressure is higher than fill pressure, it must be accounted for in the tonnage calculation.
There are many variables that go into calculating an accurate tonnage that can heavily impact the quality and profitability of your plastic parts. Having the right injection molding partner is key to ensure these calculations are measured correctly to set your project up for long-term success. To learn more about achieving project success by working with an experienced molder, read our eBook, 5 Steps to Get New Injection Molded Products to Market Faster.
Subscribe
TO OUR BLOG
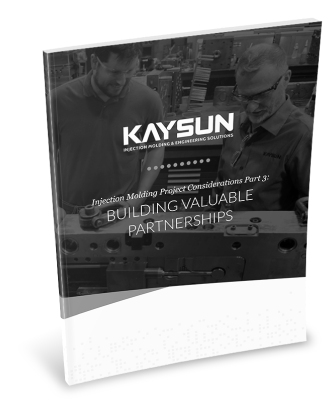
How Do Injection Molder Partnerships Influence Project Costs?
You Might Also Like...
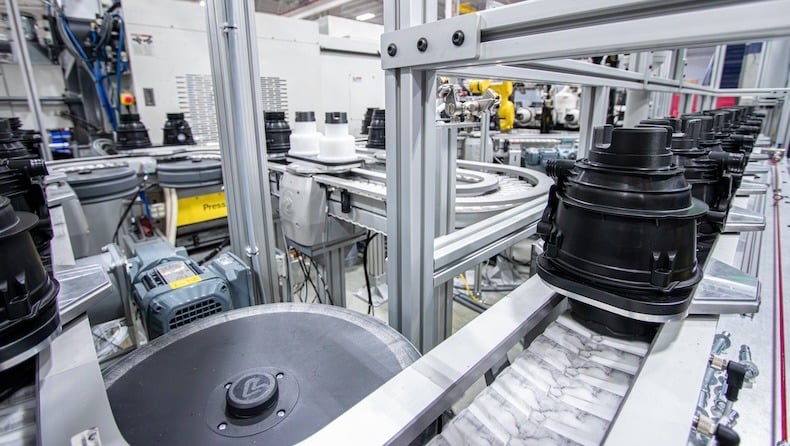
Kaysun Integrates AI on the Production Floor with RJG CoPilot
Industry 4.0 has made manufacturing more dynamic than ever before. Merging IoT, AI…
READ MORE
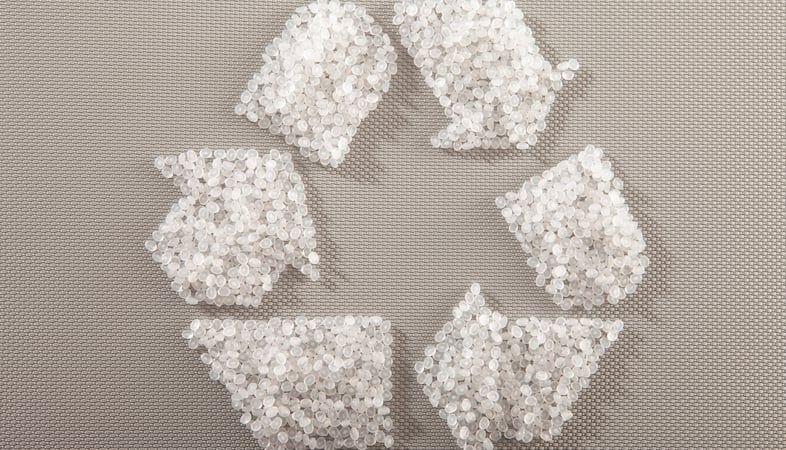
How Kaysun’s Culture of Sustainability Benefits OEMs and The Planet
Injection-molded parts and products are staples for OEMs in industries ranging fro…
READ MORE
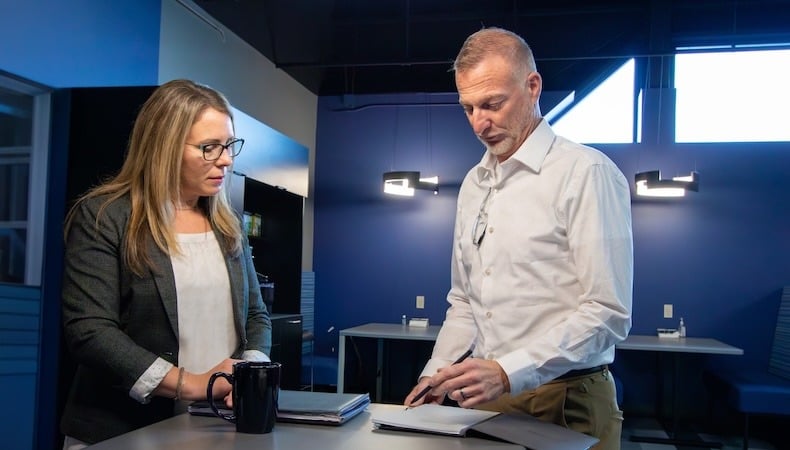
12 Common Injection Molding Questions — Answered!
Injection molding is a versatile and precise process, making it ideal for OEMs tha…
READ MORE