Choosing the Right Materials for Complex Applications
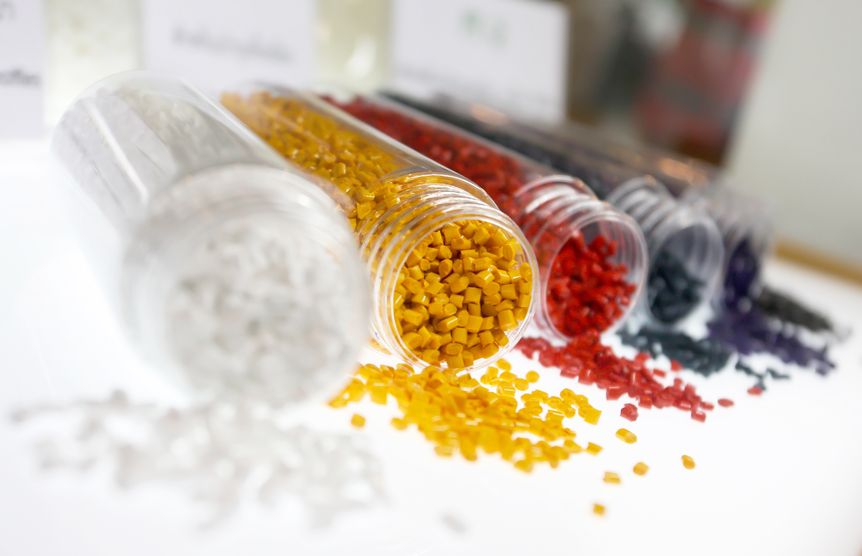
With the freedom to create new features and cost-effectively achieve process efficiencies, it's obvious why many design engineers prefer to use custom injection molding to create complex plastic parts and components.
What isn’t always clear, however, is the myriad considerations required at the onset of the process. Among them is selecting the appropriate materials to make the actual mold as well as plastic injection molding materials for the part. Here are key points to keep in mind when working through it with an injection molder partner.
Mold Design and Materials Considerations
Since almost everything is riding on the tool, it's imperative that the mold be built from materials that accommodate the project at hand. To achieve successful outcomes, consider these factors:
- Production volume and mold complexity: For a small or finite run on a simple, single-cavity mold, it’s fine for the mold to be made of an inexpensive material like aluminum, which is easily machined and not expected to last for a long time. Conversely, greater production volumes and complex, multi-cavity molds call for the durability of hardened steel.
- Cost: Generally speaking, the harder the steel, the more effort and expenditure that will go into it – and the higher the cost. While they cost more upfront, harder steel molds last considerably longer and return higher-quality parts with greater consistency. The same can’t be said for molds built from softer metals, such as P20 steel and aluminum, which can be easily machined for less cost but don't hold up to long-term repeated use.
- Corrosion resistance: Stainless steel is usually the mold material of choice since it resists corrosion, pitting and wear, while also supporting smooth finishes. For maximum corrosion resistance, however, the mold steel should be selected to correspond with the plastic injection molding materials injected into it. Careful attention must be paid to if the plastics have a high degree of acidity, such as resins in the PVC family, or additives like flame retardants.
Injection Molding Materials Considerations
As crucial to proper mold design is selecting plastic materials with characteristics appropriate for the project. Working with an experienced molder will help you ask and answer the critical questions, including:
- What is the physical load? The impact expectations of the part must be determined to ensure it will stand up to the conditions of everyday fatigue.
- What is the mechanical function? The polymer chosen must be right for the rigors of the application to ensure success.
- What are thermal conditions? In some cases, the polymer must be able to endure fluctuating and extreme temperatures.
- What is the exposure to chemicals? The ability to withstand extreme environments, such as those in the medical, automotive fields and other industries, will influence a host of decisions about proper materials.
- Will dissimilar materials be used? If so, multi-shot technology or overmolding may be appropriate; however, both the materials and the processes need to be thoroughly vetted.
- Does the part require high-heat resins? These materials are more difficult to work with mainly due to their higher melting points, driving the need for careful deliberation about everything from safety to the molding process used.
Making informed decisions about materials for the mold and materials used in complex injection molding projects improves overall plastic part quality and production efficiencies, allowing for reliable products to consistently get to market faster, differentiating you from your competitors. Learn more in our white paper, Custom Injection Molding for a Competitive Advantage. Click the button below to download your free copy.
Subscribe
TO OUR BLOG
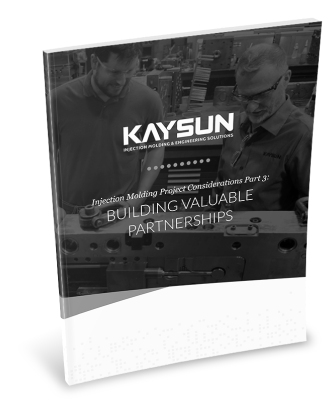
How Do Injection Molder Partnerships Influence Project Costs?
You Might Also Like...
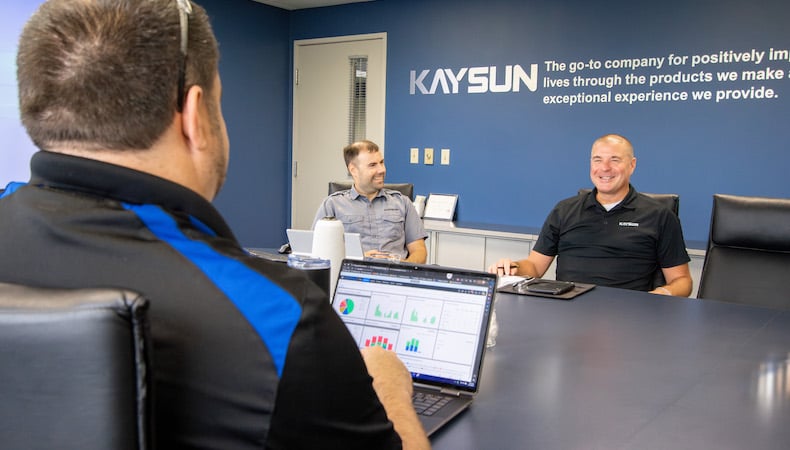
3 Key Custom Injection Molding Trends Emerging In 2024
Recent market analysis shows that demand in plastics injection molding has bounced…
READ MORE
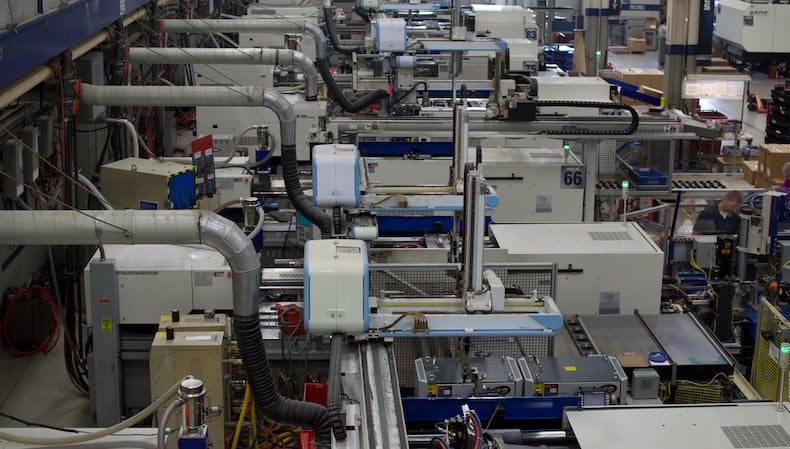
Top 14 Benefits of Injection Molding
OEMs across many industries enjoy the benefits of injection molding. It’s ideal fo…
READ MORE
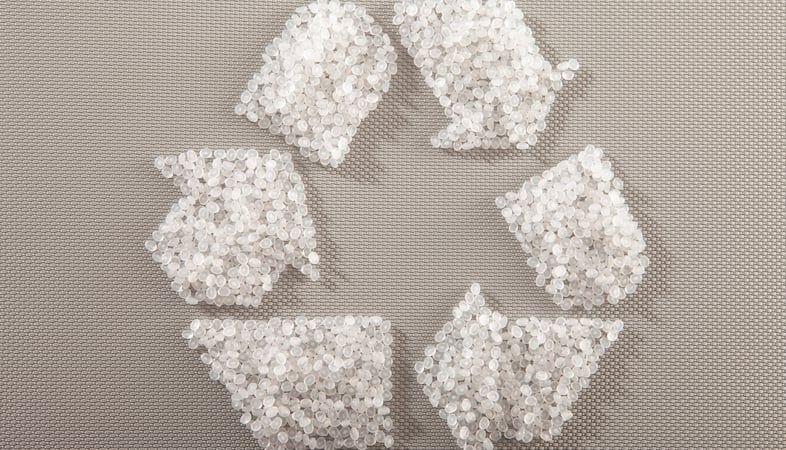
Kaysun Sets and Achieves Plastic Regrind Recycling Milestone
The 1,250 landfills in the United States are projected to reach maximum capacity w…
READ MORE