Injection Molding Expertise is Critical to Project Success
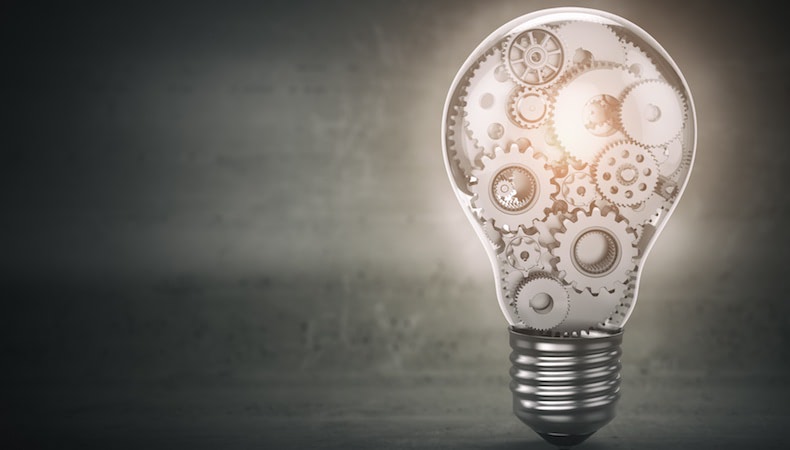
It's almost impossible to imagine a world without plastic injection molded components. They turn up in just about everything we use, and most of us aren’t even aware of their presence, or the amount of technical expertise that has been used to produce them. From the first glimmer of an idea to the production of the finished product, there is a chain of knowledge that has been incorporated into their design and manufacture, and this process doesn't happen by chance; it's the culmination of many years of experience by highly trained and skilled designers and engineers.
For OEMs looking to manufacture these components, finding the right combination of injection molding experts under one roof is essential to successfully completing a production job. There are many things molders must be knowledgable of in order to efficiently produce the plastic parts needed, as every injection-molded component is different, and each has its own set of variables that the molder must understand.
When evaluating who to partner with, there are three areas of expertise your injection molder should be fluent in:
Material Selection
The choice of resins – and there are literally thousands available – has to be determined by an evaluation of the conditions that the finished product will be exposed to, as well as the physical demands the product must meet. Electrical insulating qualities may be of prime importance, and close dimensional tolerance can be critical. When selecting an injection molding company as the supplier of plastic components, it's mandatory that the company has the expertise to satisfy the particular demand of the product in its final application. In too many instances, many molding companies limit their suggestion of which raw material to use — not for what’s best, but instead to adapt to either the limitations of their machinery or to their limited knowledge of molding techniques required for different resins.
Tooling Design
Just as important as the selection of an injection molding partner is the selection of a tooling design, and the right tooling design expert who has the knowledge needed to ensure that the finished molded product will meet all required specifications. Material flow, clamping force, sprue length and shape, cavity size and machine capacity are all factors that will affect the end product’s performance. The number of cavities within the tool is determined by the size of the production run and will have a directly proportional bearing on the cost. Molding experts will calculate mold flow studies for each resin to ensure that the finished molded component reaches its optimum level and imparts its own unique properties to the component.
Molded Part Finishes
As plastic injection molded parts are being used more and more to replace conventional materials, such as metal castings and forgings, the need to make them look like metal has become an important requirement. Shiny metal coatings or matte black enamel finishes are now standard on phones and cameras, and the injection molder must take into consideration the different molding techniques demanded by these variations in finish.
It's clear today more than ever that the selection of an experienced injection molding partner is critical, and will help OEMs create better, more efficient components while positively impacting total project costs. From tooling design to material selection, it's crucial that you work with an injection molder that has a vast amount of skill and experience. For more information, read our whitepaper, below.
Subscribe
TO OUR BLOG
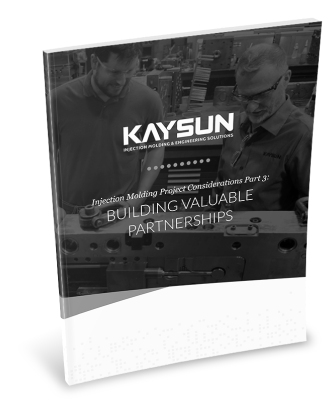
How Do Injection Molder Partnerships Influence Project Costs?
You Might Also Like...
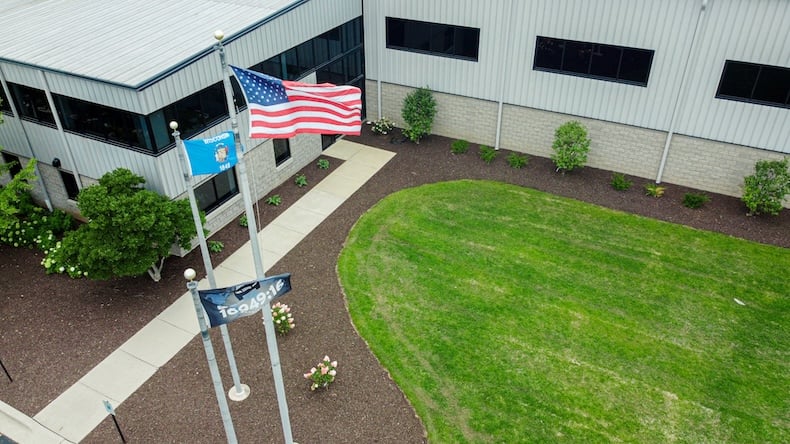
A Reshoring Roadmap for OEMs Facing Tariff Pressures & Challenges
Tariffs, geopolitical uncertainty, global supply chain disruptions, and shifting c…
READ MORE
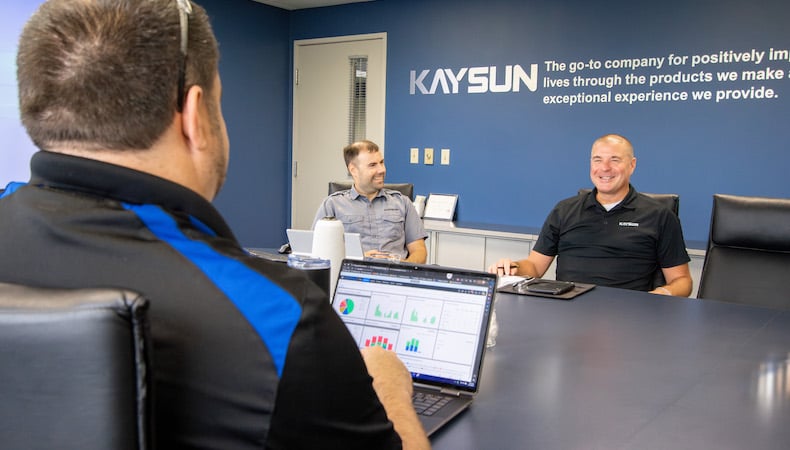
Top 3 Custom Injection Molding Trends to Watch in 2025
Despite being considered more energy efficient and producing less waste than other…
READ MORE
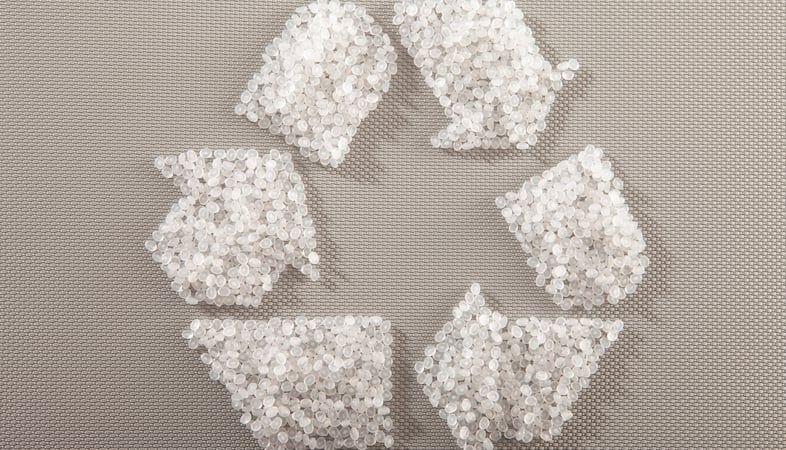
How Kaysun’s Culture of Sustainability Benefits OEMs and The Planet
Injection-molded parts and products are staples for OEMs in industries ranging fro…
READ MORE