Use Mold Fill Analysis to Maximize Complex Injection Molding Outcomes
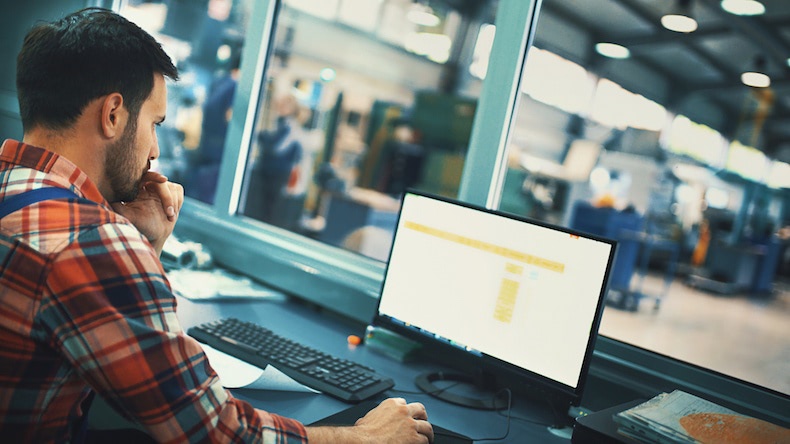
Moldfill analysis is a frequently used term in the injection molding industry but it is often poorly understood. The process uses a sophisticated computer program to analyze and predict the flow and cooling of plastic during all phases of the injection molding process. Since there are different levels of analytical software available, selecting the right one for your project is as important as interpreting the data for successful results.
Moldfill Analysis Levels
Undertaking moldfill simulation and analysis during the design phase ensures higher-quality parts and optimizes cycle times and reduces the number of tooling trials. The level of analysis required depends on the complexity of the part and desired outcomes.
The most basic level of moldfill analysis includes a simulation of the fill and packing phases. This helps optimize gate location, gate sizes, balance runners and process conditions.
More advanced simulations compare runner systems, mold temperatures and can even predict fiber orientation. They provide critical information for predictions regarding more complex parts and processes, and help engineers properly gauge:
- Shrink which is unavoidable in plastic, and generally occurs because of material structure (for example, semi-crystalline or amorphous), packing pressure and wall thickness. Engineers must be able to accurately estimate shrinkage to properly size the mold.
- Warp that results from one of three sources: unbalanced mold cooling, fiber orientation and non-uniform shrinkage. Warpage analysis reveals the causes of warpage and where warpage will occur before the mold is built, allowing engineers the opportunity to optimize part design, mold design and processing parameters to minimize deformation before production starts.
Predictive Parameters and Better Results
Other key parameters that can be predicted through moldfill analysis are:
- Processing conditions
- Flow-induced shear stress
- Weld line location
- Air trap prediction
- Sequential valve gauging
- Cavity/part temperature differential
- Coolant temperature
Because moldfill analysis identifies and mitigates potential problems related to these parameters before the mold is constructed, it reduces risk, improves quality and lowers overall production costs. With all of these benefits, you may be tempted to run moldfill analysis on all projects. However, in the case of extremely simple parts made from common materials, moldfill analysis may not be required or even be very beneficial. But, most projects with complex, high-tolerance parts that require precise dimensional stability are ideal for moldfill analysis and will realize the greatest advantage.
Compare More Than Cost
It's important to note that top-level moldfill analyses are expensive and require highly skilled personnel to run them and interpret their results, and not every supplier that claims to have the capability can actually deliver. That said, don’t make a moldfill decision based simply on cost. Work with an experienced injection molder like Kaysun to discuss the complex geometries, tight tolerances and other intricacies of your project to determine the best moldfill option for your needs.
For more information on improving manufacturability and quality while reducing costs, read our white paper Tight Tolerance is Critical for Top Quality and Superior Performance. Click the button below to download your free copy:
Subscribe
TO OUR BLOG
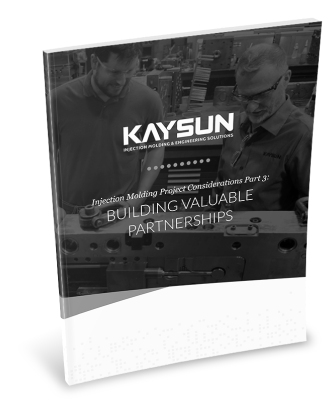
How Do Injection Molder Partnerships Influence Project Costs?
You Might Also Like...
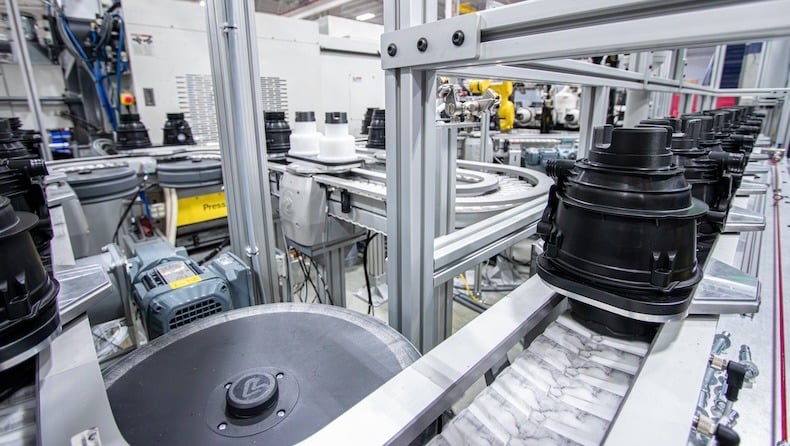
Kaysun Integrates AI on the Production Floor with RJG CoPilot
Industry 4.0 has made manufacturing more dynamic than ever before. Merging IoT, AI…
READ MORE
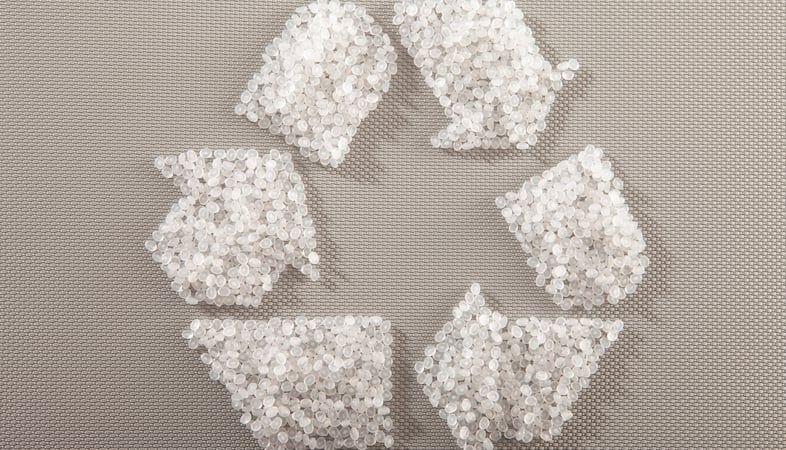
How Kaysun’s Culture of Sustainability Benefits OEMs and The Planet
Injection-molded parts and products are staples for OEMs in industries ranging fro…
READ MORE
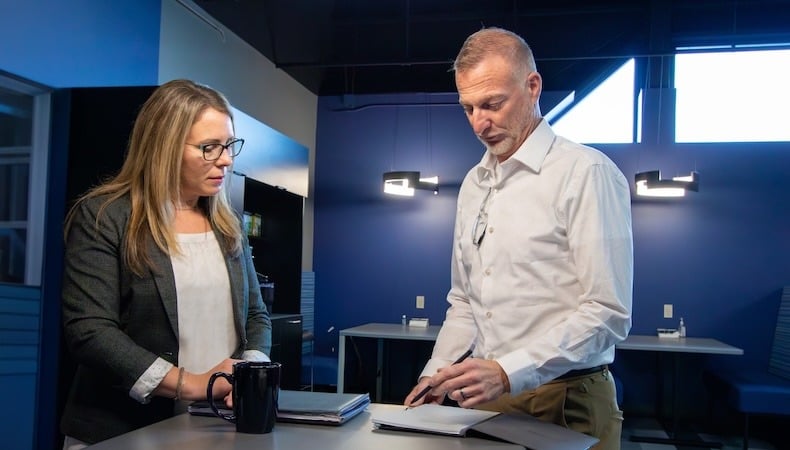
12 Common Injection Molding Questions — Answered!
Injection molding is a versatile and precise process, making it ideal for OEMs tha…
READ MORE