GD&T for Injection Molded Parts: A Practical Approach
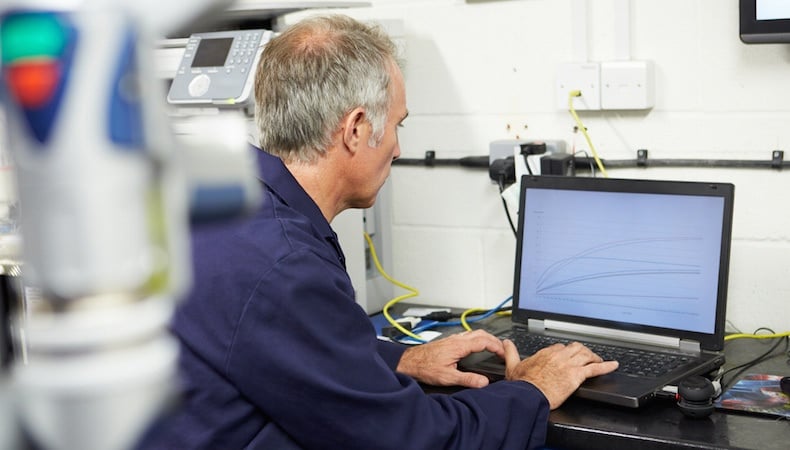
Let's begin with the basics: What is GD&T, and why is it important for injection molded parts? Geometric dimensioning and tolerancing (GD&T) is a symbolic language that is used on engineering drawings and computer-generated models.
GD&T communicates geometric dimensions and allowable tolerances for various parts. Not only is this a useful exercise for product design, it’s also helpful on the manufacturing floor because engineers and operators can quickly see the degree of tolerance that is required for each part.
GD&T is a basic yet important approach that focuses attention on the functionality of the product, and how that defines design, dimension and tolerance. As a universally accepted graphic language with both national and international standards, GD&T improves product design and quality by emphasizing function.
Increasingly implemented across a wide range of manufacturing industries, using GD&T for injection molded parts is also more and more common. It adds details to a part, print or drawing, which are based on functional use versus traditional specifications.
Considerations of Use
Before engineers can apply GD&T, they must understand a part’s application — how and where it will be used. By thoroughly understanding the designer’s intent for the part or product, the engineers can then better apply functional specifications to test the design and possibly improve on it. This is done by using datums and datum systems to define dimensional requirements, especially with respect to injection molded part interfaces.
GD&T for injection molded parts, as with other applications, shows dimensions and related tolerances based on functional relationships. It also helps determine how a part should be shaped to achieve its highest function. These results can also be used to control tooling and assembly interfaces. The use of GD&T helps to eliminate any confusion regarding nomenclature by applying universally accepted symbols and syntax. This can be especially helpful when communicating and exchanging data with overseas operations.
Importance of Datum Repeatability
Datum structure setup and construction does impact the dimensional results — and therefore product development — when done correctly. Improper construction of datums in the coordinate measuring machine will yield inconsistent, inaccurate results.
Engineers must be certain datums are repeatable and reliable before evaluating the dimensional results. When creating an axis, it is important to have enough surface area to accurately represent the axis; if the area is too small, it may not be possible to create a datum that is repeatable. For example, trying to establish a datum axis for a short cylinder (under .080”) can easily result in non-realistic data points and non-repeatable results — simply bad data that cannot be used. This analysis is especially critical before making steel adjustments.
The option to use “bonus” tolerance can make the manufacturing process easier because tolerance doesn’t have to be as tight. Bonus tolerance is applied in GD&T where the designer can use maximum material condition (MMC) or least material condition (LMC), which gives the manufacturer “bonus” tolerance based on the feature’s size. So a bolt hole of .250” +/- .005”, which has a true position call-out applied of .005” with a MMC modifier, allows for an actual part with a hole size of .245 to gain .010” of bonus tolerance on top of the .005” true position tolerance.
Effect on End Product
Another example is profile call-outs — GD&T will only let an engineer know if the part meets the specification or not. In order to analyze this call-out, the actual position results (X-Y-Z) are required, in addition to the feature’s flatness and perpendicularity to the datums. Again, this additional data needs to be included in the development inspection phase.
GD&T does create additional work in the development phase — however, once developed, it provides a simplified inspection plan for injection molding production that fully supports the product’s functionality. When vetting potential injection molding partners, ensure that they are following the ASME Y14.5 standard which defines how to properly use GD&T.
Now that you know what GD&T is (and its importance), learn about a complementary process: scientific injection molding. This advanced process is highly accurate and repeatable across multiple production runs, delivering products with tolerances as tight as +/- .001 inches — an especially valuable tool for the automotive, defense/security, medical and consumer/industrial markets. Learn more by reading our whitepaper:
Subscribe
TO OUR BLOG
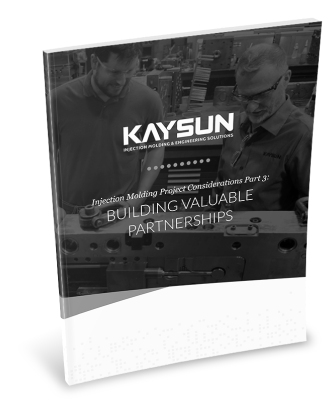
How Do Injection Molder Partnerships Influence Project Costs?
You Might Also Like...
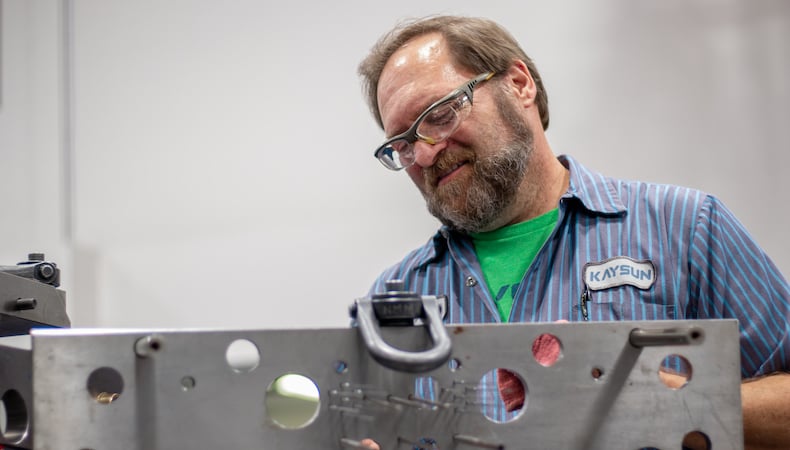
Injection Molding Quotes: 5 Tips to Help Get Tooling Right
Few things impact injection-molded part quality as much as tooling design, materia…
READ MORE
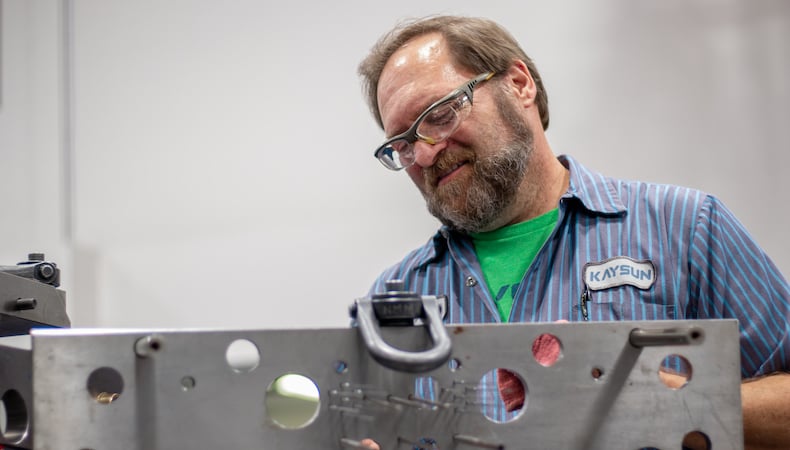
Tooling Audits & Evaluations: How Molders Help OEMs Gauge Health of Assets
When an OEM pursues an injection molding program, tooling is among the most highly…
READ MORE
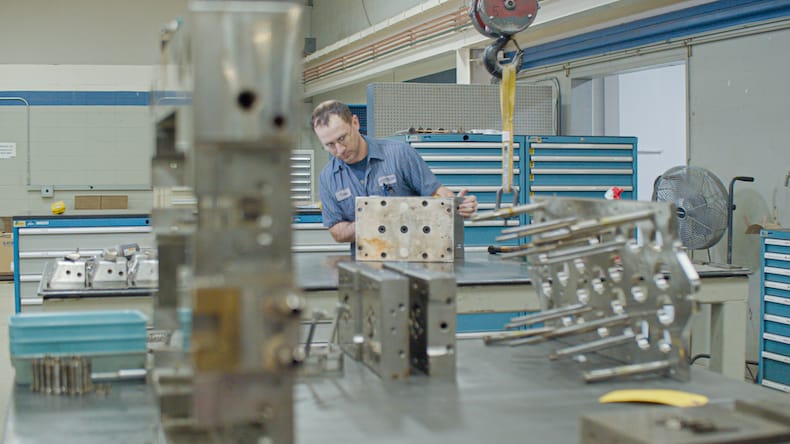
How Concurrent Design Review Aligns Injection Molding Tooling and Parts [VIDEO]
Tool design is an essential and sometimes underestimated part of injection molding…
READ MORE