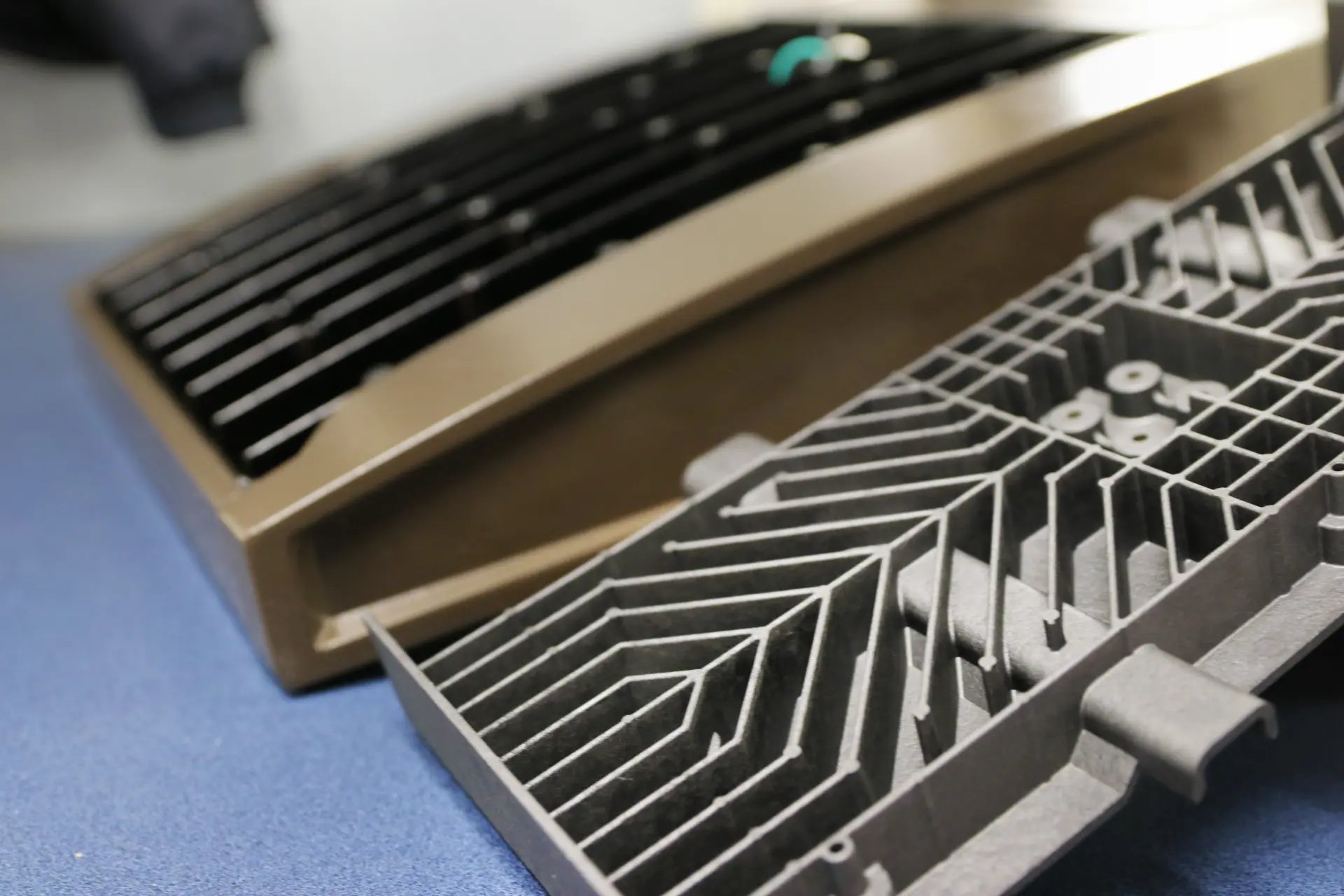
Metal-to-Plastic Conversion
It’s hard to break old habits — like using metal parts and metal products. However, there are three good reasons for changing from metal to plastic:
Lower manufacturing cost
Lighter Weight/Reduced Environmental Impact
Zero Corrosion
What many manufacturers don’t know is that — when done properly — plastic parts can be injection molded with the same tight tolerances and perform just as well as (or even better than) their metal counterparts.
How Can Plastic Parts Perform Just as Well as or Better Than Metal?
Careful design and planning, selection of appropriate materials, and use of scientific molding principles will control the main factors that affect precision, accuracy, and tight tolerances. These include material preparation, melt flow index, machine processing parameters, and, most importantly, using sophisticated sensor technology to track what is happening inside the tool in real time. Making these kinds of high-performance plastic parts and products therefore also requires a robust quality system that can monitor every step of the injection molding process.
Injection molders that consistently fail to meet tolerance specifications in plastic parts could drive up costs through additional machining, quality sorting, or warranty recalls – not to mention potential litigation.
.webp?width=866&height=606&name=KSN-metal-to-plastic-2%20(1).webp)
Advantages of Plastic vs. Metal
It only takes one bad experience with plastic parts to drive a manufacturer back to metal. But, by partnering with an experienced metal-to-plastic-conversion injection molder, there are some significant advantages to choosing plastic, such as:
Lower production costs
- No secondary process required to prevent oxidation
- Possible elimination of some assembly and/or machining
- Plastic is generally less expensive than metal
- Molded-in color/graphics capabilities vs. painting
Lighter weight
- Helps automotive OEMs comply with industry EPA standards
- Lower shipping costs
- Less physical fatigue on vehicle assembly line operators
- Improved vehicle fuel efficiency and performance
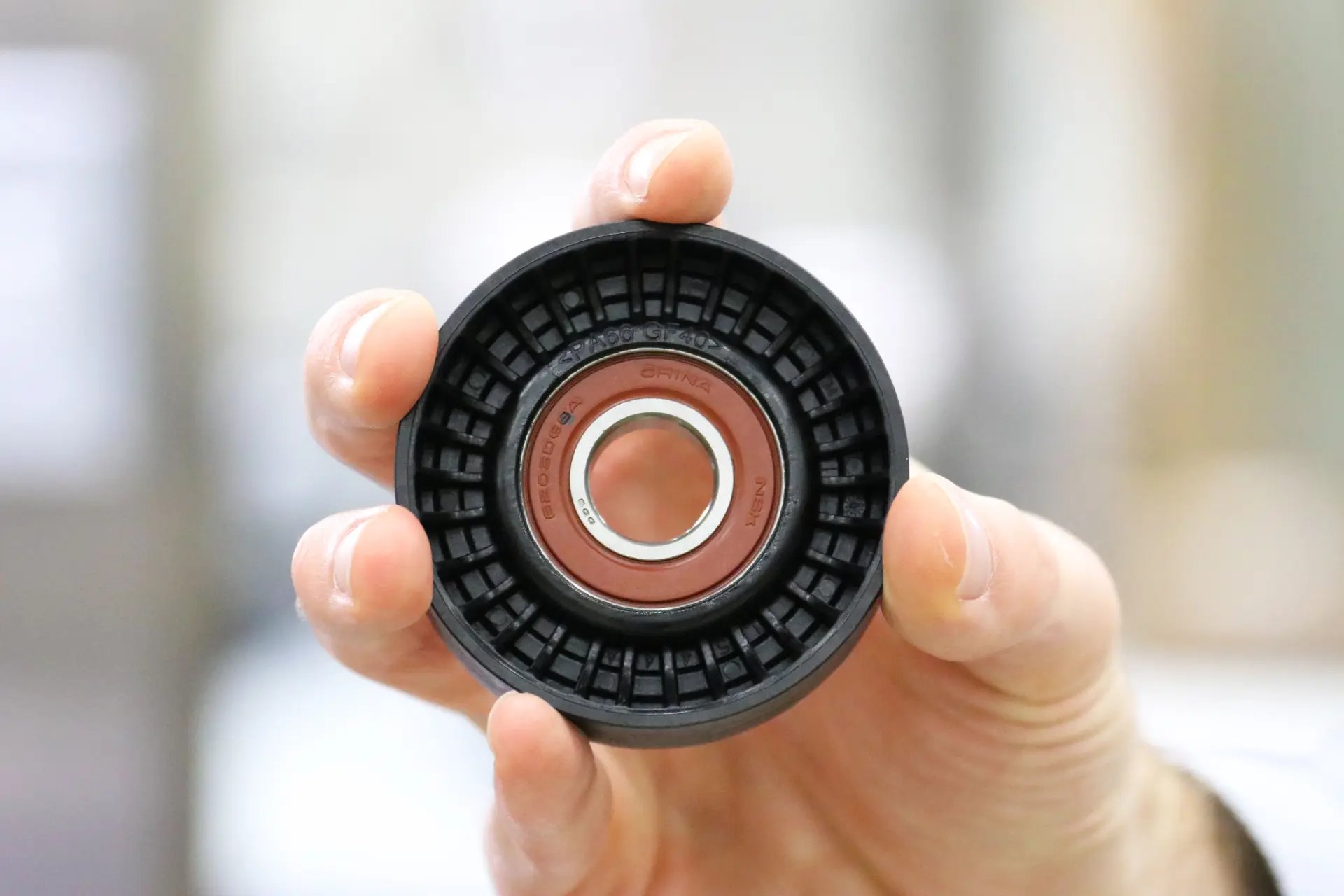
Read how Gates Industrial Corporation saw success using metal-to-plastic conversion solutions
Keys to a Successful Conversion
Successful metal-to-plastic conversion requires understanding the limitations of the process, materials, and tools before committing to the project. Every part or product isn’t a good fit for metal-to-plastic conversion. Important factors to carefully consider are the expected tolerances, materials, specific part design/configuration, and initial mold flow/analysis.
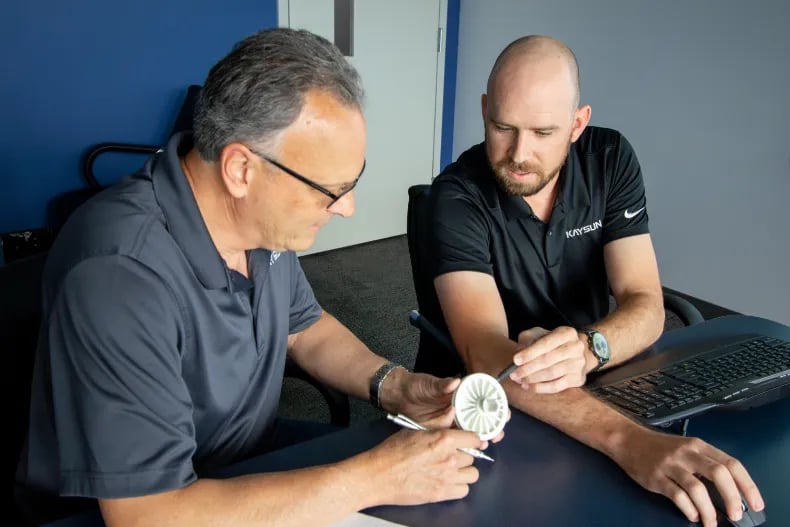
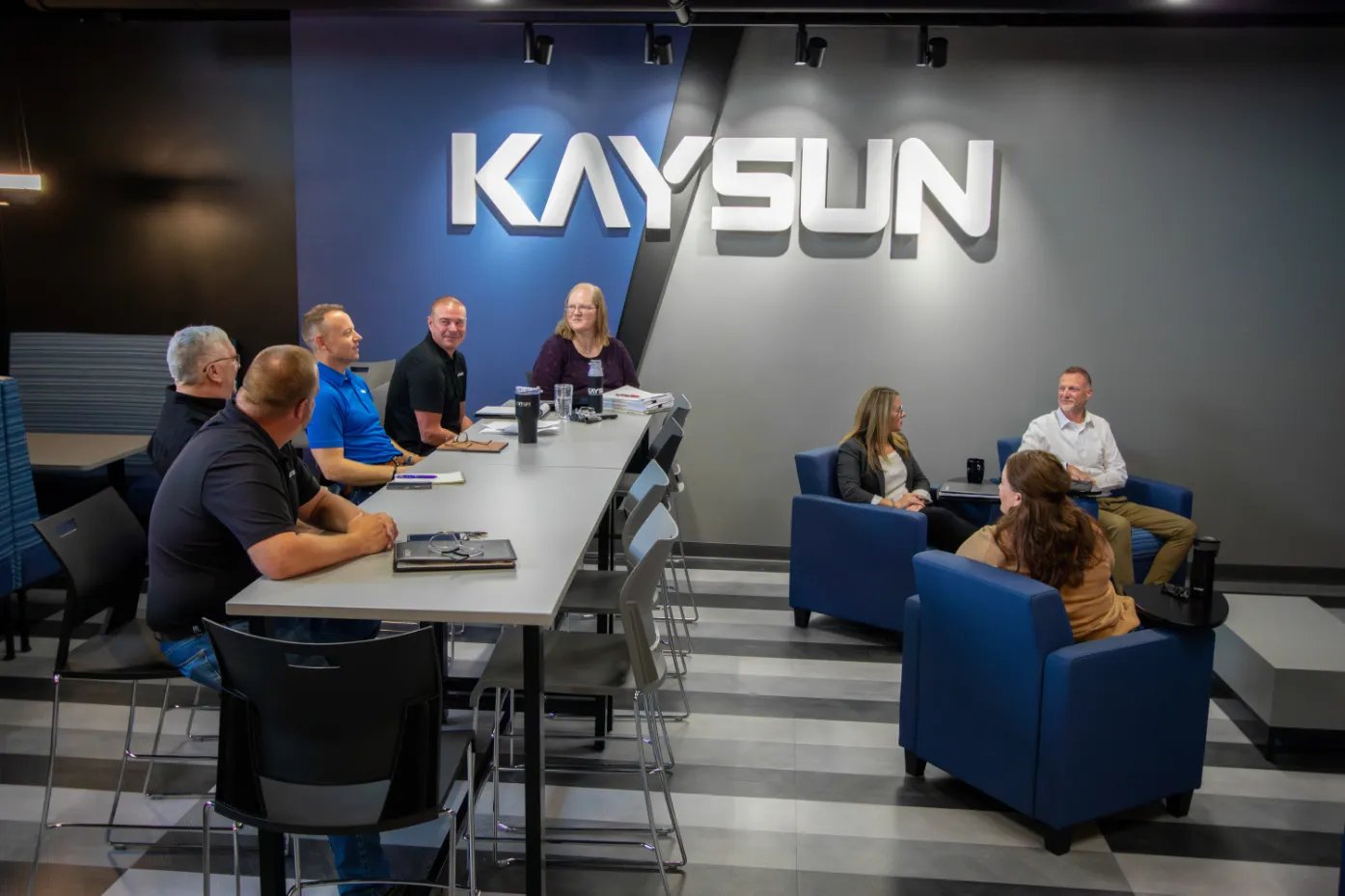
Does your company fit our ideal customer profile?
Complete the form to request a free consultation with our plastic engineering experts.