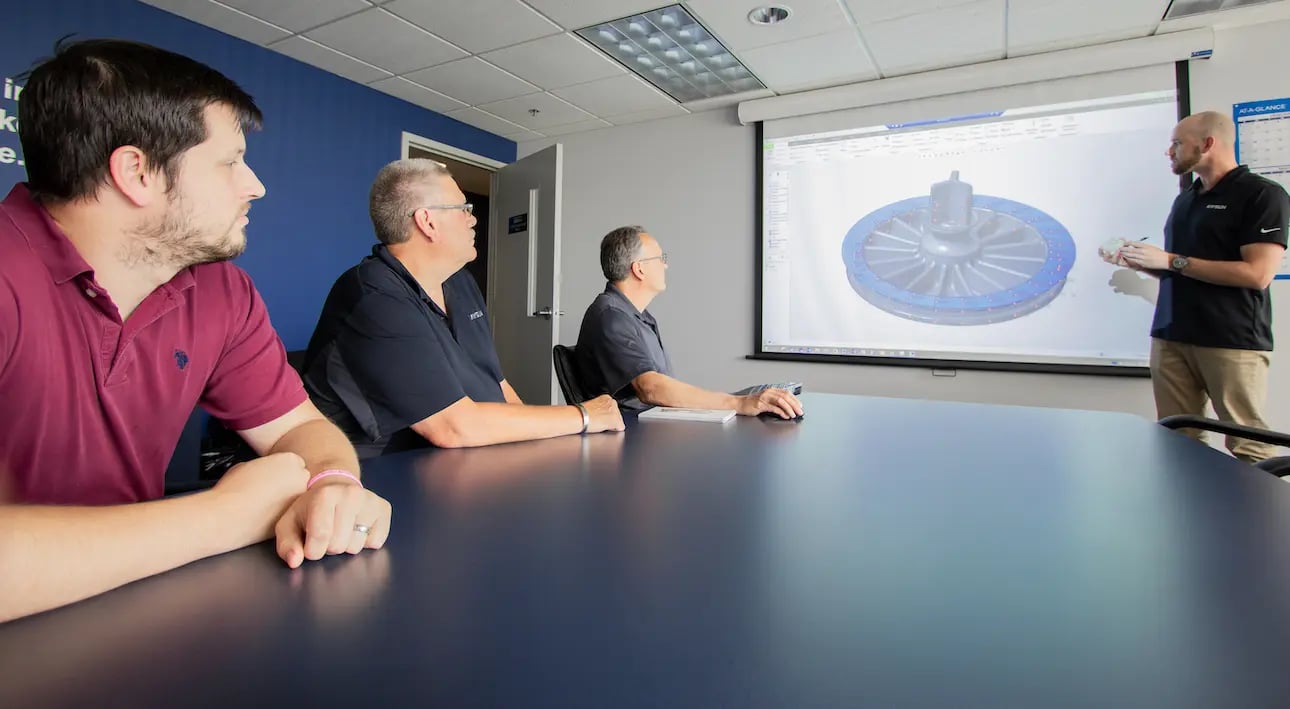
Engineering Support
Using injection molding tools and technologies isn’t a complete approach to making complex injection-molded plastic parts of the highest quality. Engineering services that fully support product development are also critical for success.
Accessing a wide range of plastic injection molding services is increasingly important as the size, geometry, and function of parts become more sophisticated. Kaysun offers in-house engineering services that provide just the right amount of customized support, including:
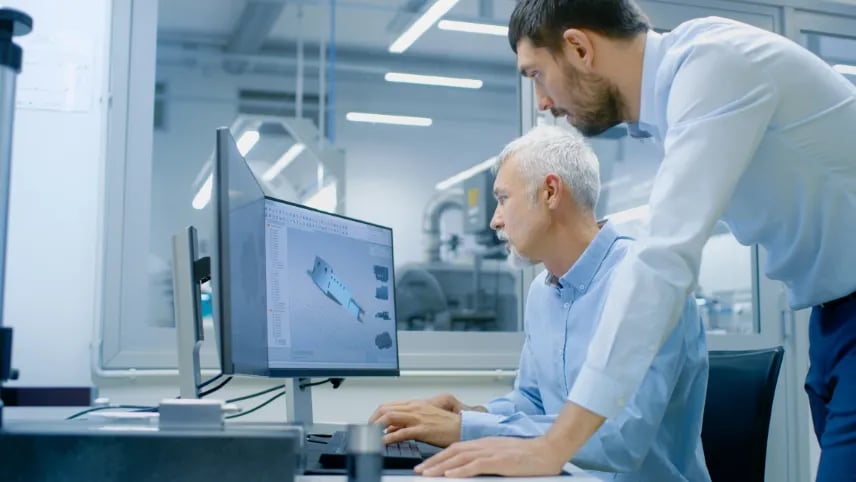
Design for Manufacturability (DfM)
Design for Manufacturability (DfM) — also known as Design for Manufacturing — is the process by which products are consciously and proactively designed to optimize all facets of manufacturing.
Specially trained injection molding engineers use the insights gained from DfM to identify and resolve potential moldability issues, simplify part design and tooling, select appropriate plastics, and maximize production and cost efficiencies. Since these steps are taken during the initial design phase, the benefit is twofold. It aligns engineering and production to prevent costly rework and ultimately save manufacturers time and money.
Material Selection
With more than 25,000 engineered materials to choose from, plastics selection can be a challenging task without expert guidance from Kaysun. Our deep knowledge of plastics behavior and material science saves customers time, and expense by efficiently identifying the best materials for the tooling and parts. Kaysun also helps customers with short- and long-term strategies to overcome resin shortages.
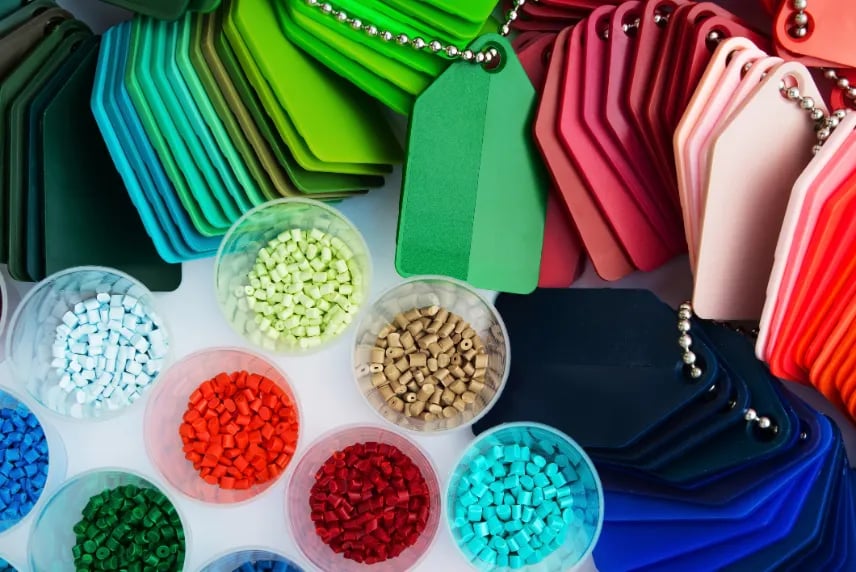
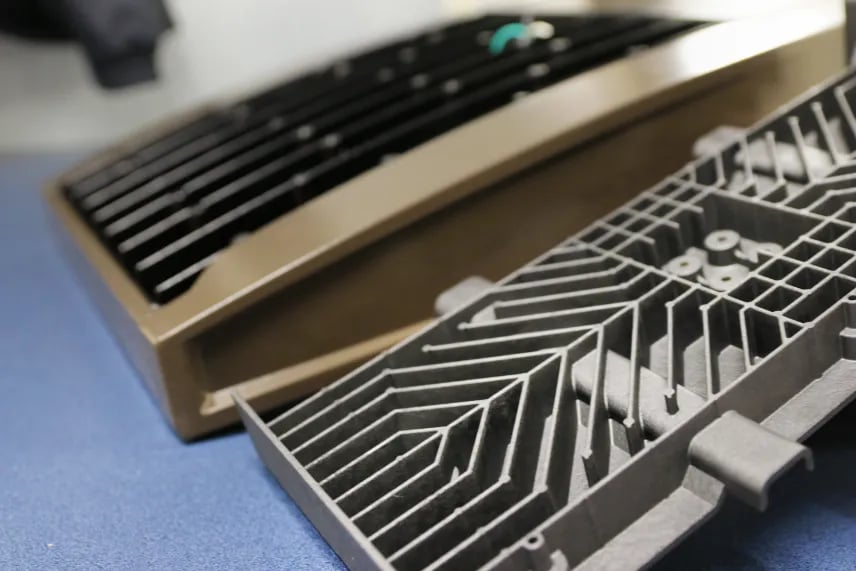
Metal-To-Plastic Conversion
Some manufacturers aren’t aware that plastic parts can be injection-molded with the same tight tolerances as their metal counterparts, and perform equally as well (if not better). Converting metal parts to plastic generally results in an overall cost savings of 25-50% without compromising quality or functionality.
Constantly seeking optimal efficiencies, Kaysun applies engineering expertise to foresee issues in production before they happen. With a thorough understanding of manufacturing processes and the ability to predict how products will be inspected, we can ultimately create a better design and set up each program for success right from the start.
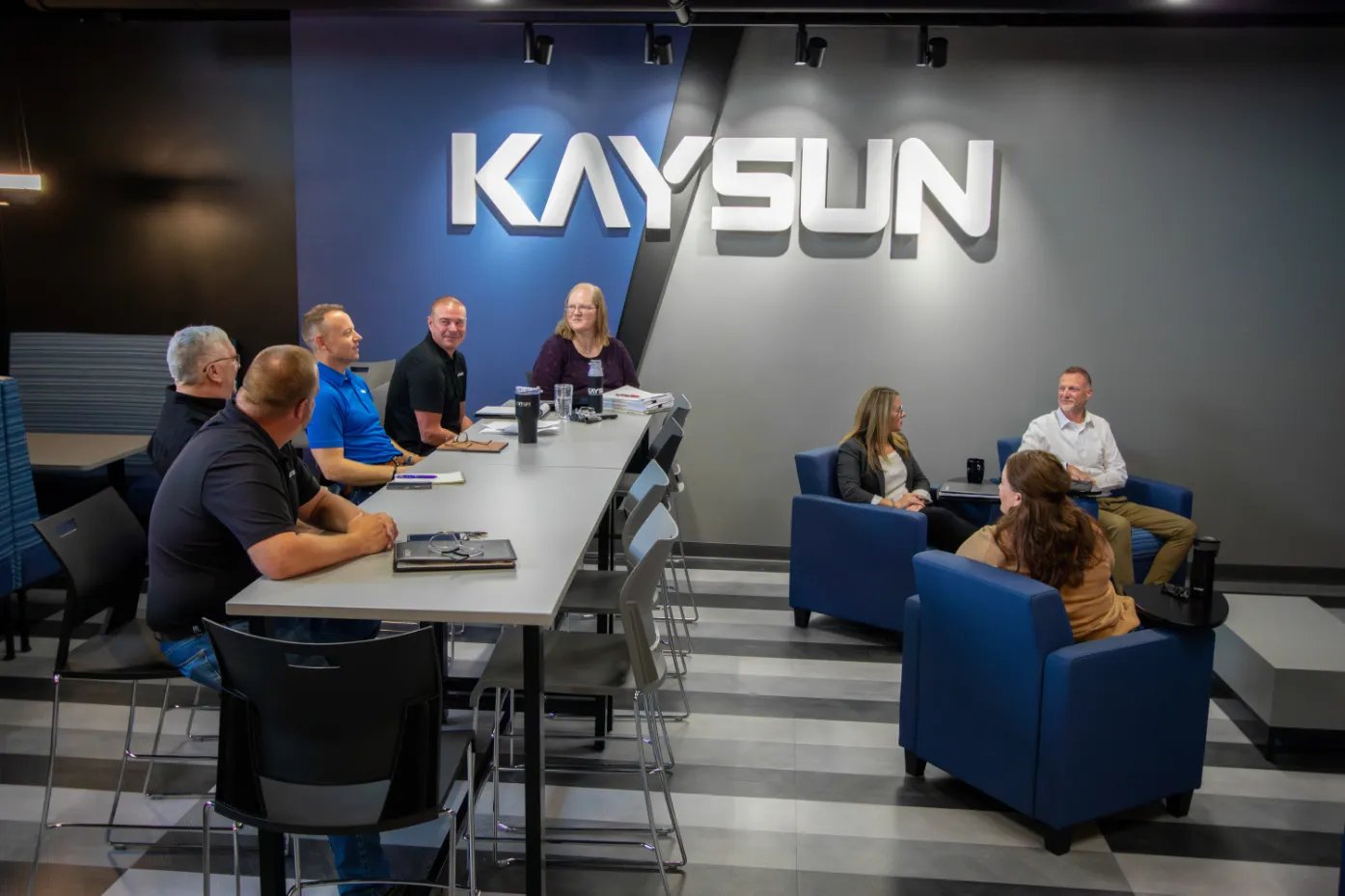
Does your company fit our ideal customer profile?
Complete the form to request a free consultation with our plastic engineering experts.