Injection Molding Design & Process Optimization
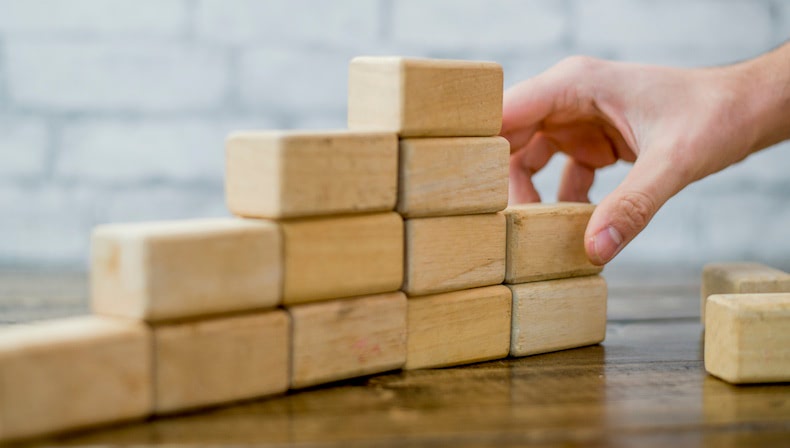
Scientific molding is the best way to deliver complex, high-performance parts. It is a highly precise, data-driven process that eliminates any guesswork and maximizes quality and manufacturability. Scientific molding is especially valuable when it comes to decisions about process optimization, molding and tooling design validation, and product quality.
This approach is superior to standard molding procedures because of the high level of scientific control utilized through upfront Design of Experiments (DoE), flow analysis, process monitoring, and quality control that can quickly detect and correct any process variations.
The Importance of DoE
DoE is a critical aspect of scientific molding. In fact, establishing the DoE process after considerable preparation and engineering regarding product design and process parameter selection is a big step toward developing and optimizing robust injection molding.
However, to ensure consistent and repeatable production of flawless molded parts, the process extremes must be completely investigated and the injection mold tooling evaluated before it’s called into action. This is how tooling weaknesses are identified and corrected.
Testing the Mold
Both the tool engineer and process engineer thoroughly examine every aspect of the mold’s mechanical functionality to make sure everything works as designed, using the material settings provided by the resin supplier. They then conduct short-shot testing to assess the dynamic pressure loss and, in a multiple-cavity mold, to check for any imbalance among the cavities. This step is also the stage for a crucial objective: establishing the rheology curve (or viscosity curve) to indicate the best fill rate and pattern.
After this, gate seal studies are performed from both the pressure curve and the weight of the sample parts to see if the gates seal fully, and at what point, on the mold cavity (or multiple cavities). Engineers examine the test parts from the processing extremes for any defects and record their findings along with recommendations for any adjustments in the process or the tooling in order to correct the defects. They also record data on the melt temperature, fill time, mold temperature, coolant flow, cycle time, and pressure curves.
Quality Control
The parts then go to quality control for examination of their measurements, shot-to-shot consistencies, and overall quality. That information is used for any necessary adjustments to the tooling before new samples are made. The new samples then undergo the same quality testing, with necessary adjustments made again as needed. Once all the process parameters meet their performance ranges, the mold is ready for action and production process has been optimized.
Mold design and process optimization is vital for creating highly efficient, low-cost injection molding outcomes by eliminating any problems or quirks before production starts—ensuring top quality and repeatability.
By understanding each phase of product development—especially mold design and process optimization—scientific molding engineers can build the most efficient and robust process window possible for your project, saving money on upfront quality and speeding up throughput. Learn more in our whitepaper, Mold Design & Tooling for Injection Molding. Click the button below to access your free copy.
Subscribe
TO OUR BLOG
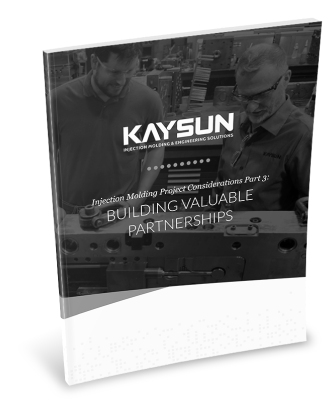
How Do Injection Molder Partnerships Influence Project Costs?
You Might Also Like...
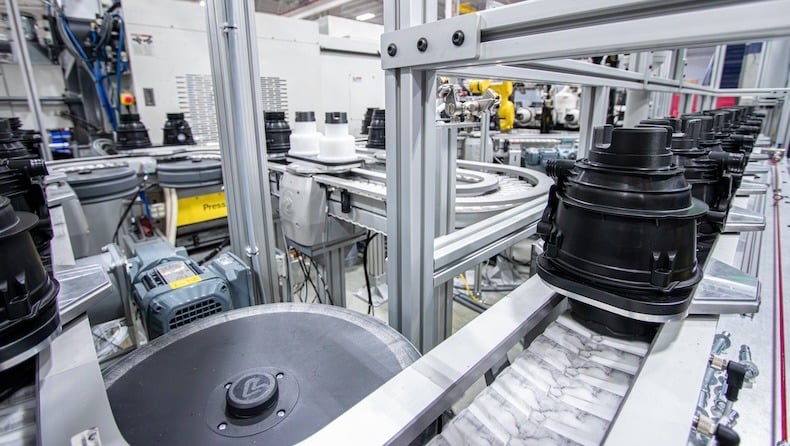
Kaysun Integrates AI on the Production Floor with RJG CoPilot
Industry 4.0 has made manufacturing more dynamic than ever before. Merging IoT, AI…
READ MORE
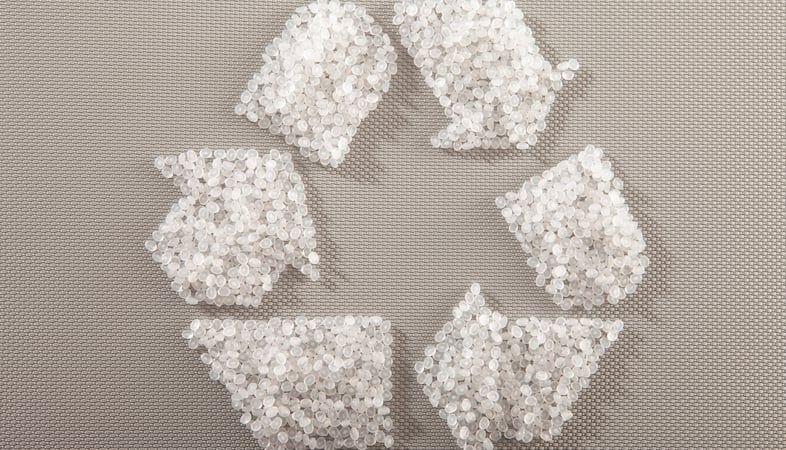
How Kaysun’s Culture of Sustainability Benefits OEMs and The Planet
Injection-molded parts and products are staples for OEMs in industries ranging fro…
READ MORE
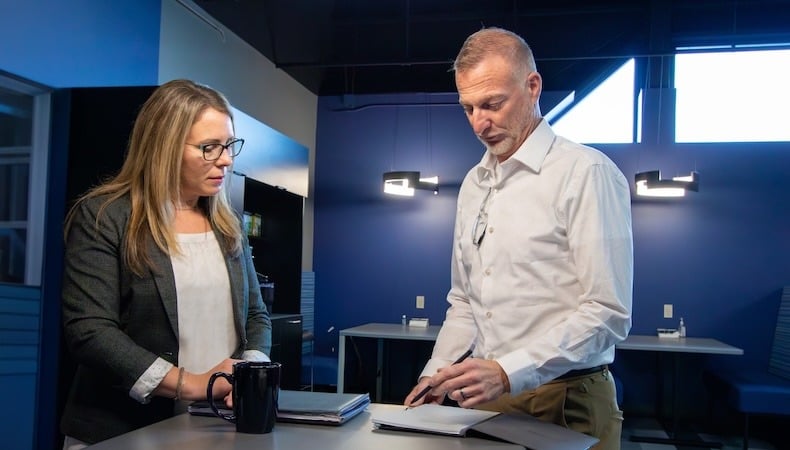
12 Common Injection Molding Questions — Answered!
Injection molding is a versatile and precise process, making it ideal for OEMs tha…
READ MORE