Surface finish for plastic parts can vary a great deal, depending on the physical and chemical properties of the polymer blend as well as the parameters of the injection molding process.
A custom injection molder works with the customer to determine how important the injection molding surface finish is to the final product's appearance and/or performance. For example, does the product need to be eye-catching or simply functional? Depending on the answer, the material selected and the desired finish will determine the settings for the injection molding process and any required secondary finishing operations.
SURFACE FINISH CATEGORIES
Surface finishes on injection molding tools are standardized according to the Plastics Industry Association (formerly known as the Society of Plastics Industry or SPI). The process used to achieve the finish determines the following grades:
- Grade A - Diamond Buffing: Diamond buffing paste has a very fine grain, so finishes are generally very glossy and product surfaces remain flat. Grade A finishes are considered the highest standard.
- Grade B - Sandpaper: This semi-gloss finish is applied using sanding grit and is ideal for hiding visible machining marks. The sandpaper grit number provides surface finish control — 600 for the finest finish, 400 for mid-range, and 320 for the most textured finish.
- Grade C - Grit Stone: Grit sanding stones generally follow the grit number and finish textures as sandpaper. However, grit stones cut fairly aggressively, which creates a rougher texture compared to B grades.
- Grade D - Pressure Blasting: Pressure blasting plastic surfaces with abrasives — typically sand or glass beads — results in non-directional patterns and dull or flat finishes.
Within each grade there are different levels of surface finish, which determines the degree of plastic surface texture. Generally, levels are sequentially numbered within the grades, with 1 being the least amount of texture and higher numbers correlating with more texture. For example, a sandpapered plastic surface finish categorized as a "B1" is semi-gloss and lightly textured; a "B3" is still semi-gloss but has more visual and tactile texture.
Injection molding finishing is an added cost — the higher the grade and finish level, the higher the bottom line. Since it can be a considerable investment, it's important to have an experienced custom injection molder weigh in on the appropriate injection molding surface finish and the most cost-effective tool classification.
Aesthetics vs. Functionality
There are functional tradeoffs to be considered. For example, the coefficient of friction and resistance to wear can be affected by the surface finish; if these characteristics are important to product performance, the design team needs to select a material and process that will create a compatible finish. Experienced injection molders have a vast body of scientific data on material chemistry, behavior, and processing conditions to cross-reference for accurate determination of surface finish based on process parameters.
It is critical to determine surface finish during the design stage because it will impact the types of material, tooling, and processing decisions that can be considered. The texture on the tool steel will limit the part surface finish. Sometimes a rougher texture can be used to hide other surface imperfections, such as sink. Injection molding surface finish can also affect the draft required on the part — without appropriate draft, the surface finish could be destroyed during ejection.
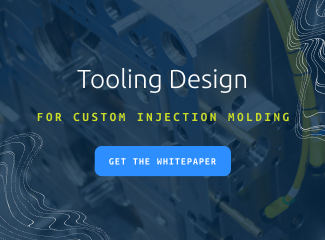
Material Selection Considerations
Two key surface characteristics — gloss and roughness — can be impacted by the material selected, additives, and different injection molding parameters such as fill rate, pressure, and temperature. Material type is especially important — for example, higher melt temperatures for products made from reinforced crystalline resins increase gloss and reduce roughness, creating a smoother surface. If reinforced amorphous resins are being injection-molded, however, a higher mold temperature will increase gloss and reduce roughness.
Another important consideration for injection molding surface finish is additive compounds that are mixed into the resin. This is where knowledge of material science really comes into play — for example, fiberglass content results in a lower gloss. Other additives like carbon black or mica can reduce surface roughness — these are additives to avoid (or find substitutes for) if a certain surface roughness must be maintained for product function or appearance. Adding particulate fillers may increase surface roughness. Engineers can mix and match the right combination of resins and additives to produce specific surface qualities.
Injection Speed & Temperature
Then there’s speed. Faster injection speeds, combined with higher melt or mold temperatures, will further enhance the gloss and smoothness of the surface. In fact, a faster injection speed always improves gloss and smoothness, regardless of the other production parameters that have been determined. For any reinforced composite, the fast injection speed combined with high melt and tool temperatures will always provide the glossiest and smoothest part (although a slow injection speed, combined with cooler tool and melt temperatures, may meet other product specifications, they will typically result in a poor surface texture). Quick filling of the tool cavity can help minimize fiber orientation, making the weld line less visible and boosting the aesthetic quality of the product.
These are just some of the methods for controlling surface finish during the injection molding process. Be sure to consult with your injection molder in the earliest design stages to fully determine surface finish needs and other project parameters as detailed in Critical-Use Plastic Parts: Key Design and Injection Molding Considerations. Click the button below to access your copy of this valuable guide now!
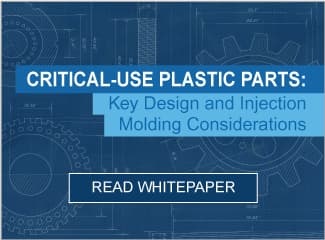