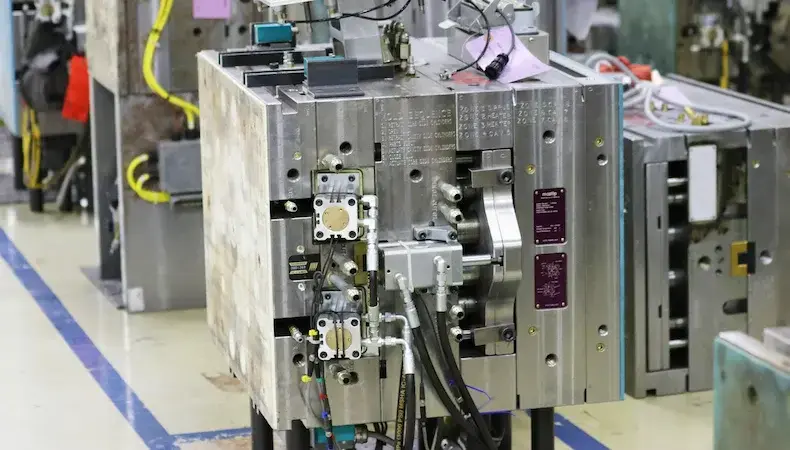
the interrelationship of tooling complexity and tight tolerances
Tooling design, materials, and cavitation all impact tolerance. In general, the more simple the process, the more likely it is to achieve and maintain tight tolerances.
Conversely, complex parts can put tight tolerances at risk since there are more variables to consider, such as the number of cavities in the mold or the need to precisely heat or cool the tools. For example, if tooling is not designed for consistent cooling, shrink rates will vary and tight tolerances will be harder to achieve. Mold cooling and part cooling are also critical for determining surface finish.
Logically, it follows that sophisticated injection-molded components require sophisticated tooling. Added features such as undercuts and threads are common. In the case of complex geometries, injection molding tooling could require the addition of rotating mechanical racks/gears, rotational hydraulic motors, hydraulic cylinders, floating plates, or multi-form slides.
sensors, benchmarking, and process repeatability
Directly correlated to scientific molding is the use of strategically placed transducers in multi-cavity and hot manifold tools to monitor and control the process in real time. Sensors can also be placed on the surface of the tool as a cooling lines or unit failure back-up. Upper and lower limits can be set on these sensors to monitor the cooling rate and the cavity pressure profile.
Establishing a production-capable process with in-tool sensors is also important for benchmarking. Having verified data to reference when making tooling material, process, or molding machine changes is essential for accurate monitoring, documentation, set-up, and future production repeatability.
tooling materials selection
A critical but sometimes overlooked injection molding tooling design consideration is proper tooling materials selection. The choice impacts several aspects of tool longevity:
- The proper steel grade and hardness properly balances wear and toughness, so tooling components that run together don’t wear out prematurely.
- Steel hardness can also introduce steel brittleness. Harder steel is not a good choice for tooling components subject to side-loading or impact, because if it flexes it will crack.
- Harder steel is required for molding glass-filled material, which can prematurely wear down tooling, including runner systems and gates.
ENGINEERING CONSIDERATIONS
Details matter in plastic injection tooling. Engineers play pivotal roles in ensuring an optimized production process, reduced costs, and unparalleled product quality.
Among chief responsibilities for tooling engineers is:
- Placement of waterlines to maximize cooling and minimize warping.
- Calculation of gate/runner sizing specifications for proper filling and minimal cycle times.
- Determination of the best shut-off methods for tooling durability over the life of the program.
Likewise, design engineers are accountable for several key tooling decisions. Principle among them is determining gate types and locations in order to:
- Achieve optimum flow, fill pressure, cooling time, and dimensions/tolerance.
- Assure proper part performance.
- Prevent part defects and flawed aesthetics (e.g., flow marks, shrinkage, warping).
Part art and part science, plastic injection tooling is all done to guide customers toward an optimized production process, reduced costs, and unparalleled product quality. Learn more about the process of scientifically qualifying a tool by downloading our infographic.