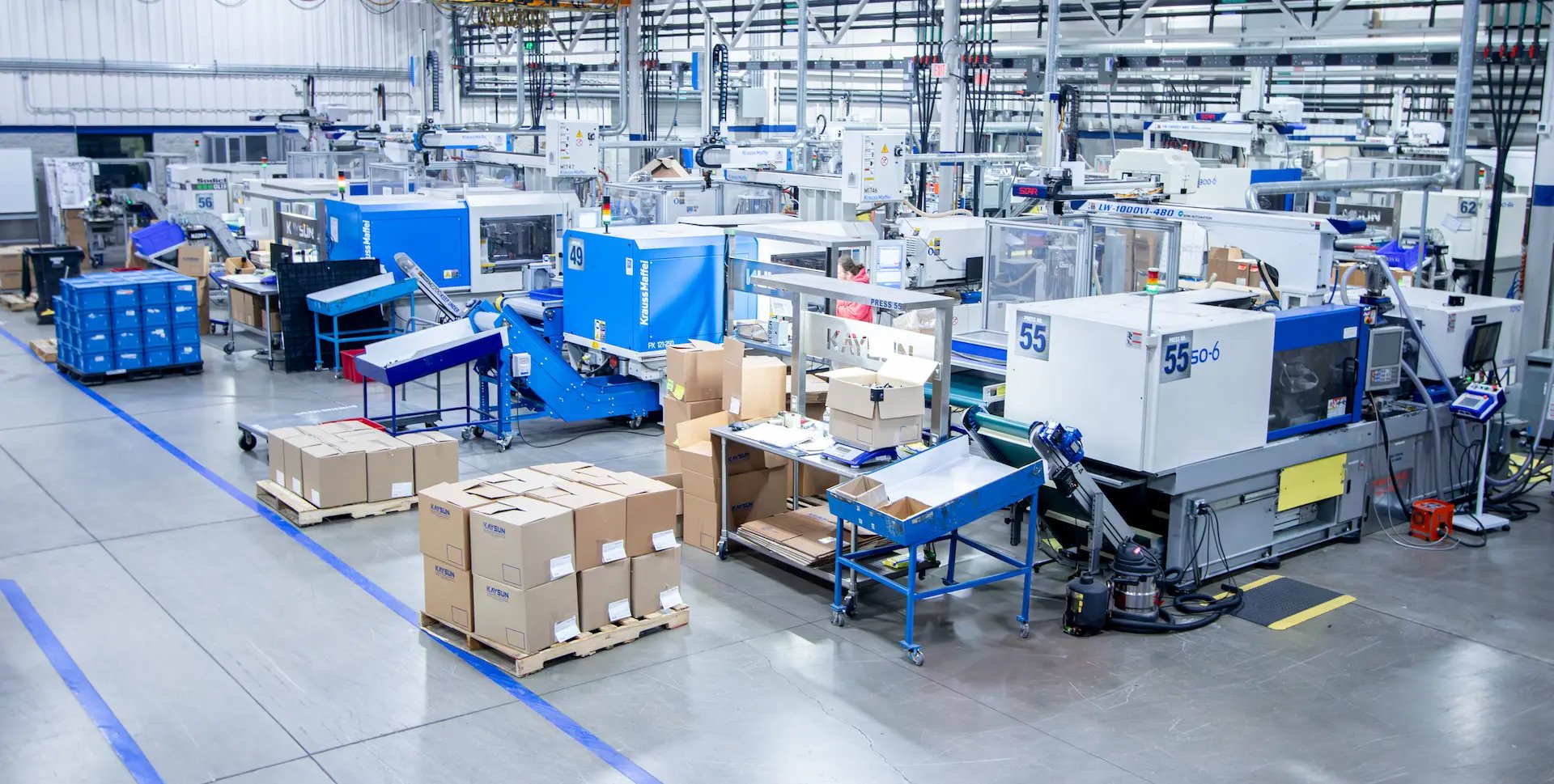
Tight Tolerance Molding: Critical for Quality & Performance Improve Manufacturability And Quality While Reducing Costs
Tolerances as tight as +/- .001 inches are required for many high-performance, complex plastic parts and products. Learn more about how injection molding achieves these remarkable tolerances in our guide, How to Achieve Tight Tolerances in Custom Plastic Injection Molding. In it you'll learn how:
- Tight tolerance molding reduces or eliminates secondary operations, like machining
- Tight tolerance molding is essential for controlling shrink and warp, and how mold filling analysis can predict these
- Thermal expansion rates in plastics can be controlled using fillers
- Tool design, tool material and cavitation all impact tolerance