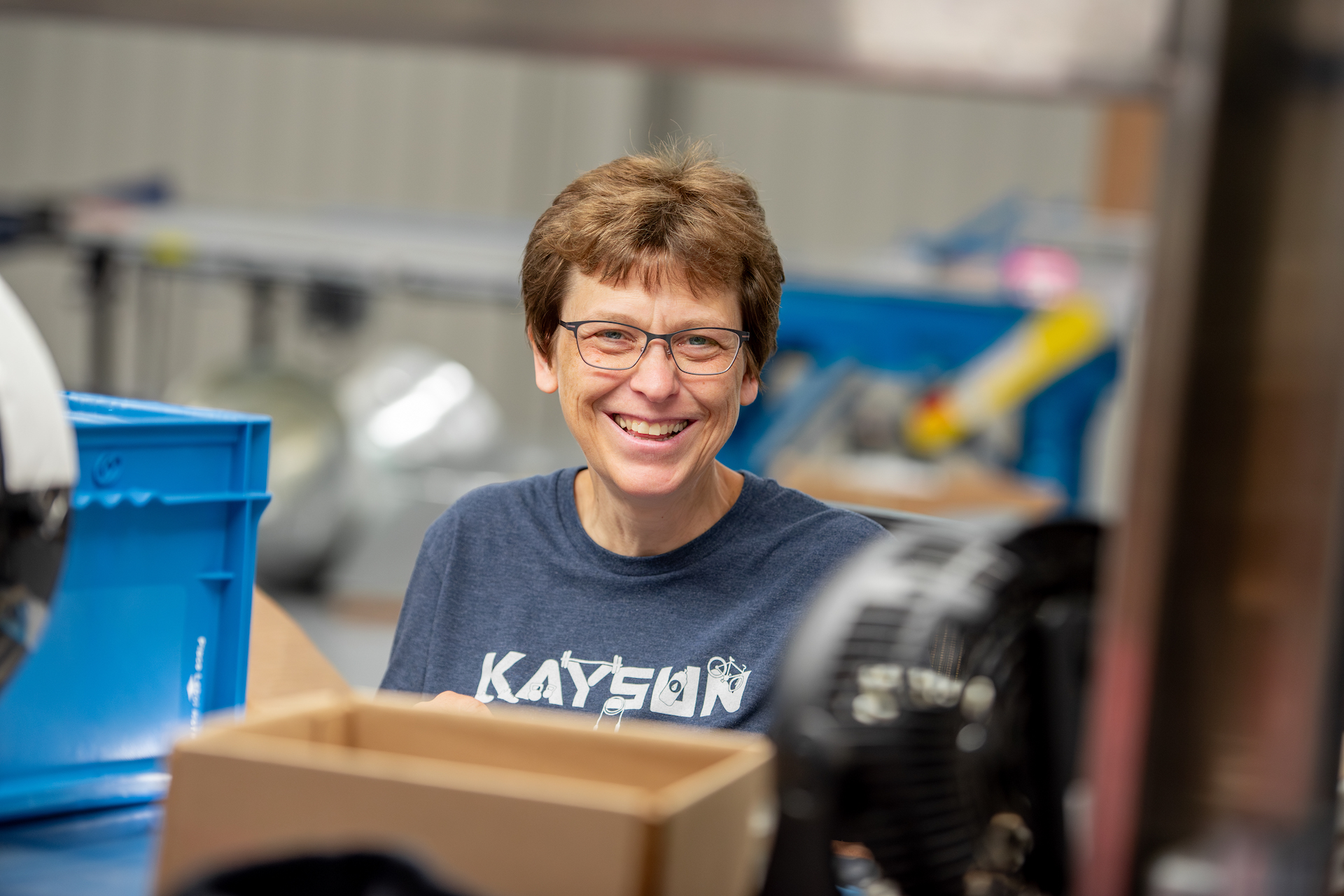
Is Kaysun a Fit FOR YOUR COMPANY?
Quickly assess how Kaysun aligns with your needs
Custom injection molding is often integral to the performance and reliability of complex applications. Knowing with certainty that the injection molder you choose aligns with your needs before you engage in a program is good business. Engaging in the right partnership from the start saves time and money, and helps prevent mismatches.
That’s why we created the “Are We a Fit?” assessment. You’ll know at a glance if you fit our best customer profile, and what a successful partnership looks like.
- Are well-established, with a minimum annual revenue of $100 million
- Operate within one of these select industries:
- Industrial
- Medical/Healthcare
- Consumer Products
- Automotive
- Military/Public Defense
- Energy
- Oil & Natural Gas
- Engineering
- Quality
- On-Time Delivery (OTD)
- New Product Development
- An active program or part design in development
- Part design includes highly engineered complex geometries and tolerances
- Part use-case requires highly engineered material and/or process
- Annual projected injection molding program volume minimum of 50,000 units
- Part size does not include micro molding
- Part material is exclusively thermoplastic; no thermoset or rubber molding
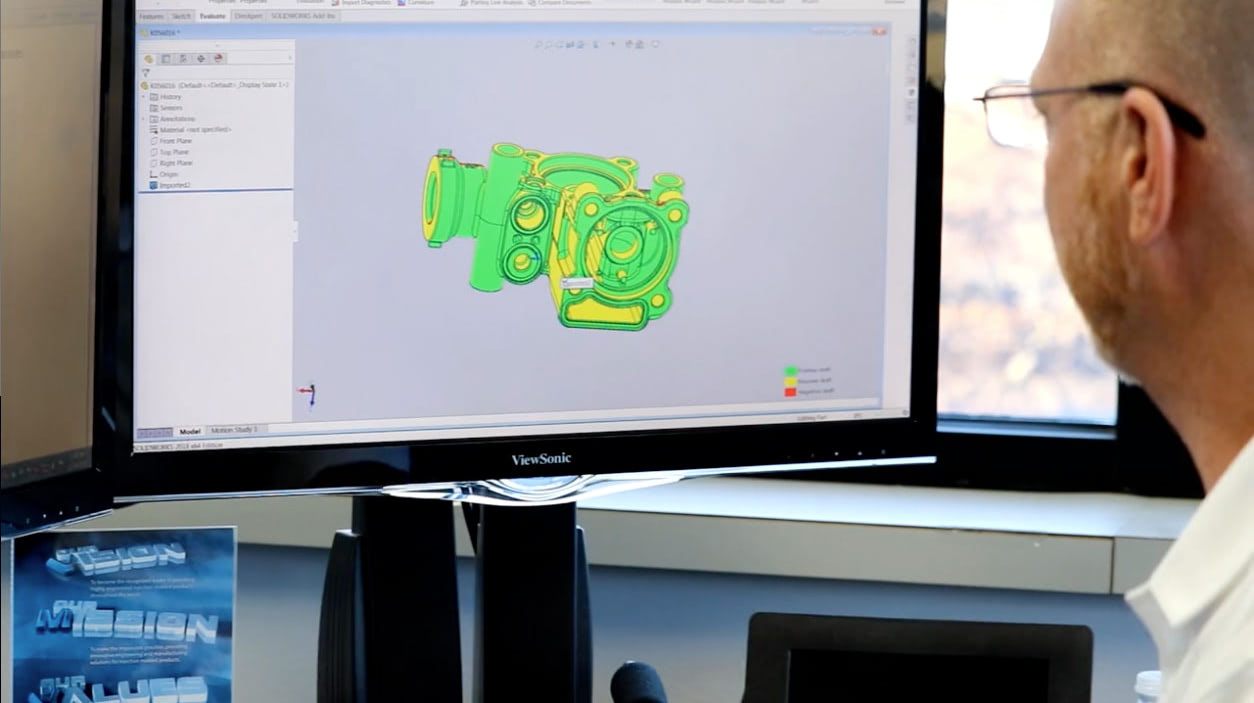
What does a partnership with Kaysun look like?
Kaysun believes in the power of teamwork. Our company is founded on it, and our customer relationships are strengthened by cross-functionality and collaboration at every touchpoint, including:
- Part and tooling design recommendations, gleaned through upfront Design for Manufacturability (DfM) analysis
- Material selection
- Forecasting
- Timelines
- Engineering
- New Product Development/R&D
- Quality Assurance (Look inside the Kaysun Quality Lab)
- Purchasing/Sourcing
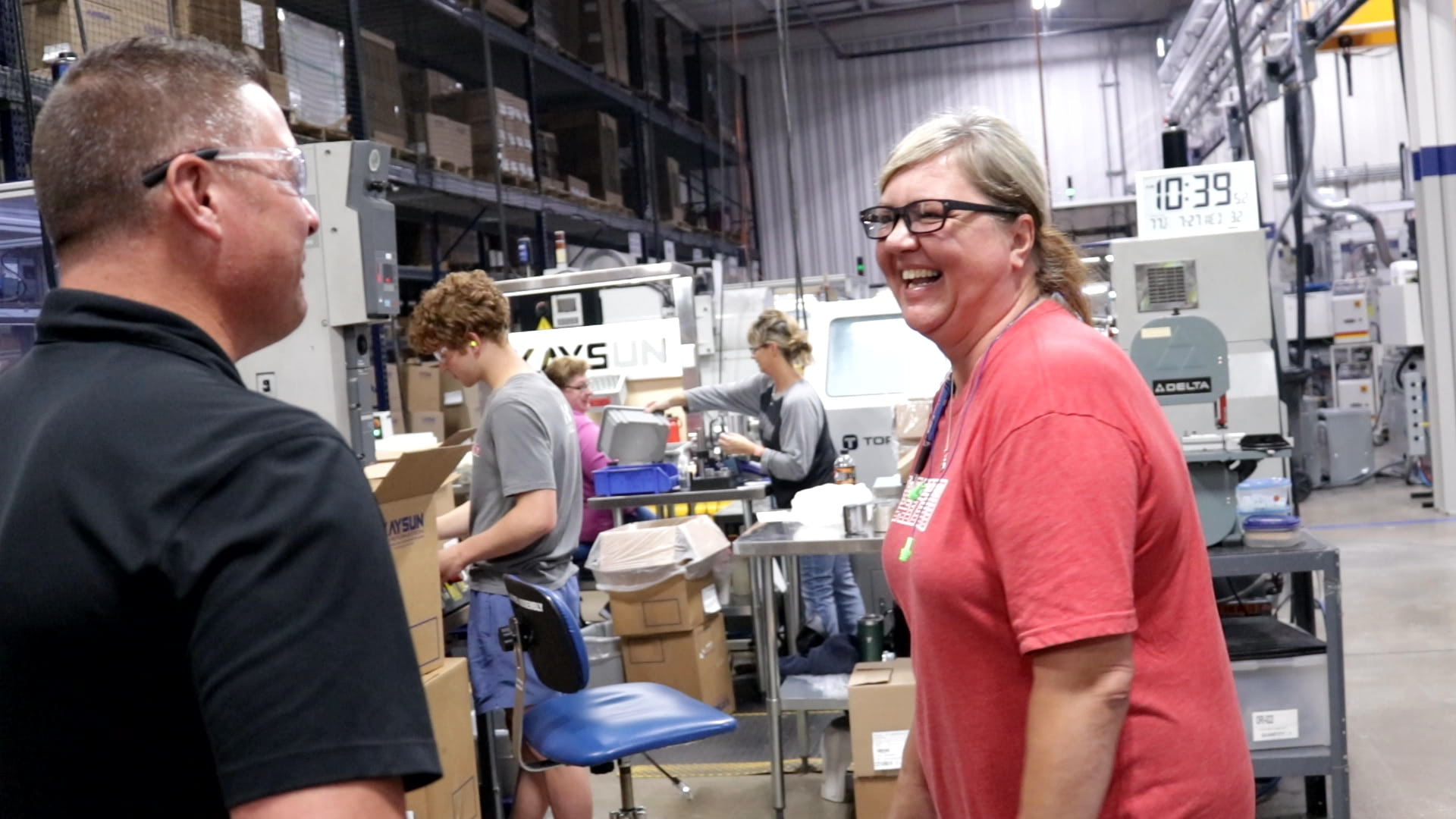
Kaysun is strategic about how we work with you throughout every phase of a program. Optimizing time and resources supports decision making, goal setting, and successful injection molding outcomes.
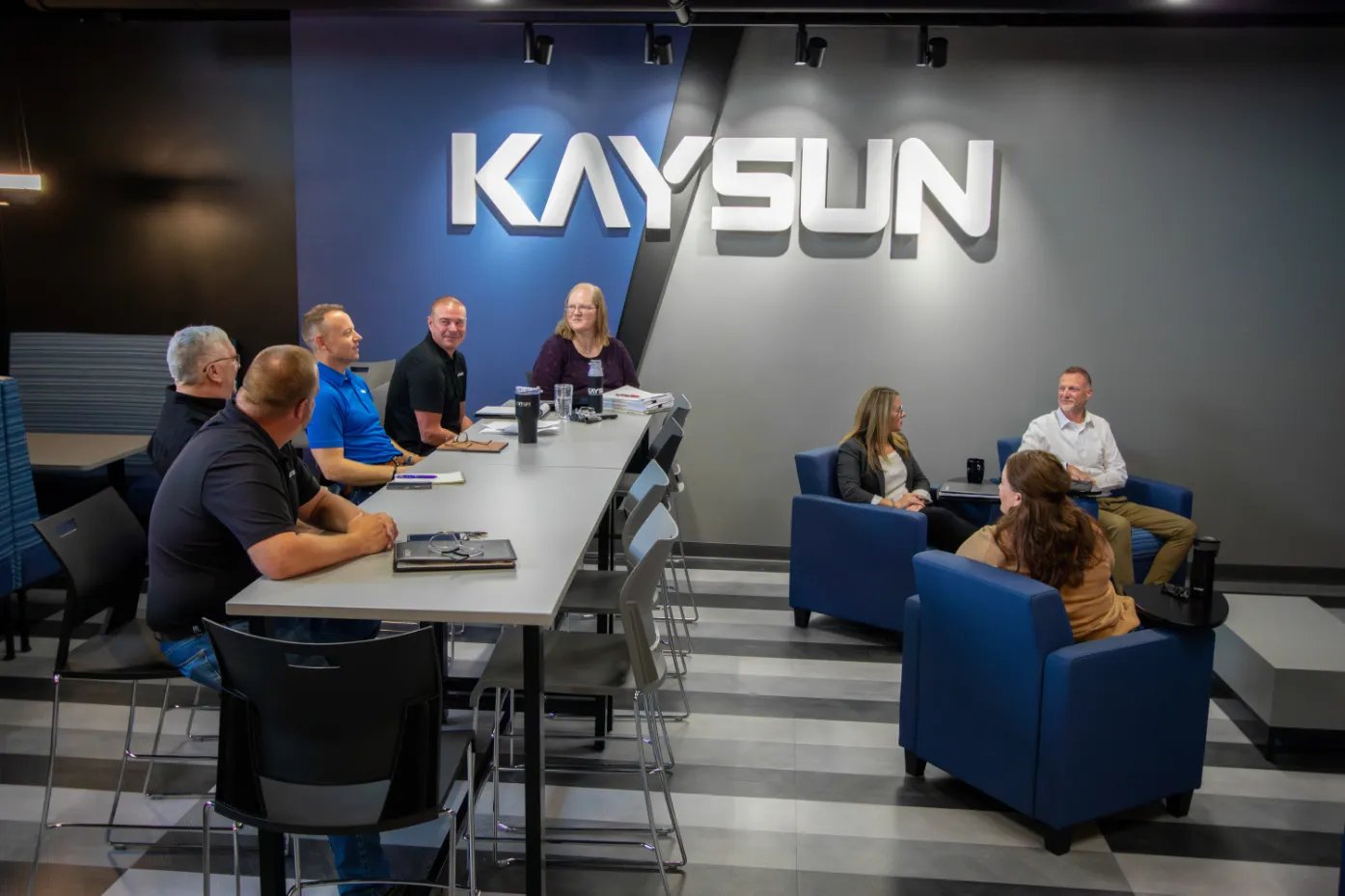
Does your company fit our ideal customer profile?
Complete the form to request a free consultation with our plastic engineering experts.